Compacted Strand Wire Rope
Are you in search of highly durable wire ropes products tailored for demanding industries such as mining, transportation, and construction?
High-Performance Wire Ropes and Sling Solutions
Welcome to Aulone, where our commitment to quality and customer satisfaction drives every product we offer. Our wire ropes and sling solutions are designed to deliver unparalleled strength, flexibility, and reliability, making them ideal for critical applications in diverse industries.
Explore our extensive range of product forms, including customized wire ropes, slings, shackles, and hooks, all tailored to meet the specific needs of your projects. Our solutions are particularly suited for applications requiring high load-bearing capacity and corrosion resistance, ensuring optimal performance under tough conditions.
At Aulone, we are dedicated to providing products that represent the highest standards of quality and safety. Our wire ropes and socket are your partners in lifting and construction tasks, designed to ensure success and excellence in your operations.
Mian Structure
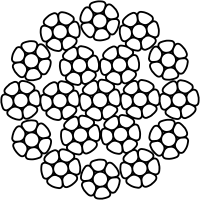
Abrasion resistance performance
High breaking force
Fatigue resistant performance
Suitable for high-lifting working.
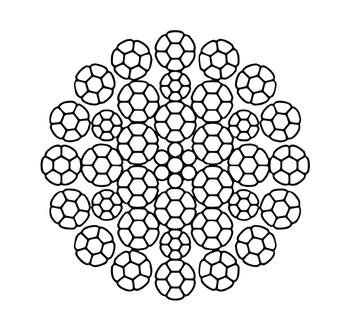
High tensile strength
High abrasion resistance
High fatigue failure resistance
Less wear of sheaves and capstans
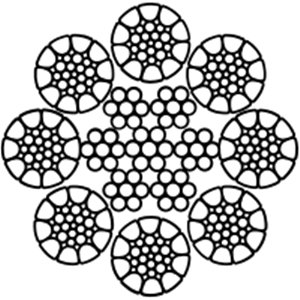
Abrasion resistance performance.
High breaking force
Outstanding bending fatigue performance
Very stable rope construction
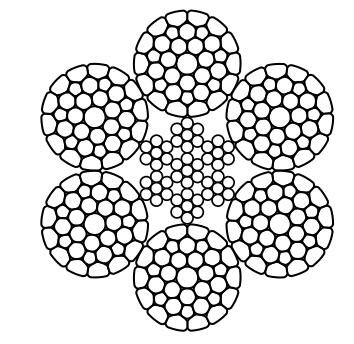
Abrasion resistance performance.
High breaking force.
Fatigue resistant performance
Improved support of outer strands in service.
Improved ton-mile performance
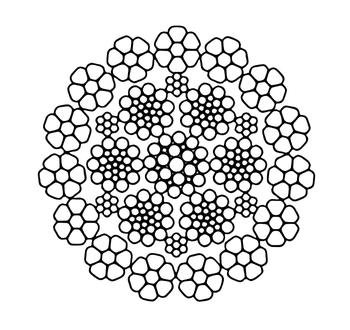
Abrasion resistance performance
High breaking force
Fatigue resistant performance
Suitable for high-lifting working
High performance rotation resistant
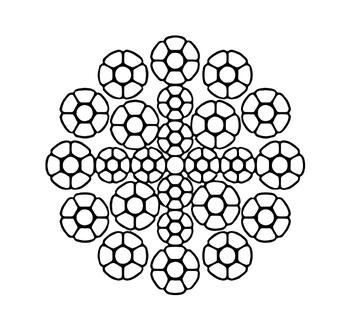
Abrasion resistance performance
High breaking force
Fatigue resistant performance
Suitable for high-lifting working
High performance rotation resistant
Your Ultimate Guide to Acquiring Compacted Strand Wire Rope
When looking to acquire compacted strand wire rope, there are several factors to consider to ensure you get a product that meets your specific needs and standards. Here’s a comprehensive guide to help you navigate the selection process:
Table of contents
Chapt 1
What is Compacted Strand Wire Rope

Compacted wire rope is a type of wire rope that undergoes a specialized manufacturing process to compress or compact the individual strands and wires within the rope. This compaction reduces the diameter of the rope while maintaining its strength and load-bearing capacity. The compaction process typically involves passing the strands through a series of rollers that compress and reshape them.
The key characteristic of compacted wire rope is its denser structure compared to traditional wire rope. This denser structure offers several advantages, including increased strength, improved abrasion resistance, reduced internal friction, and enhanced fatigue performance.
Compacted wire rope is commonly used in heavy-duty lifting and hoisting applications where strength, durability, and reliability are crucial. Industries such as construction, mining, offshore oil and gas, and crane operations often rely on compacted wire rope for their demanding lifting requirements.
Chapt 2
Advantege of Compacted Strand Wire Rope
Compacted wire rope offers several advantages over traditional wire rope, making it a preferred choice for heavy-duty and high-stress applications. Here are the key benefits:
- Increased Load Capacity: Due to the denser and more compact structure of the strands, compacted wire rope has a higher breaking strength than standard wire rope of the same diameter. This allows it to handle heavier loads, which is especially beneficial in applications like crane operations, mining, and offshore rigging.
- Enhanced Durability: The smooth exterior of the compacted strands reduces wear and tear on the rope as well as on the sheaves and drums it operates over. This reduces the frequency of rope replacement and maintenance, which can lead to significant cost savings over time.
- Improved Abrasion Resistance: The compacted structure provides a larger contact surface area and fewer gaps between wires, which makes the rope more resistant to external abrasions and cuts. This is crucial in environments where the rope may come into contact with rough surfaces or edges.
- Reduced Internal Friction: The closer contact between wires within the strands decreases internal friction, which helps in reducing the internal heat generated during operation. Lower internal friction also contributes to the overall longevity of the rope.
- Less Stretch and Better Flexibility: Compacted wire rope exhibits less stretch under load compared to standard rope, which provides more precise control in lifting operations. Despite the compaction, these ropes maintain excellent flexibility, which is critical for efficient handling and operation.
Superior Fatigue Resistance: The compaction process increases the fatigue resistance of the rope, making it more suitable for applications involving repetitive loading cycles. This feature is particularly important in mechanical systems where the rope must endure many cycles of tension and relaxation.
- Better Stability: The compact structure minimizes the risk of birdcaging or kinking, common issues in standard ropes under heavy loads or improper handling. This stability is crucial for ensuring safety and reliability in critical lifting operations.
- Reduced Diameter for Same Strength: For applications with space or weight constraints, compacted wire ropes can provide the same strength as thicker, non-compacted ropes, but in a slimmer profile. This can be advantageous when retrofitting equipment or designing new systems where space is limited.
Overall, the benefits of compacted wire rope make it an excellent choice for various industrial applications requiring robust performance and reliability.
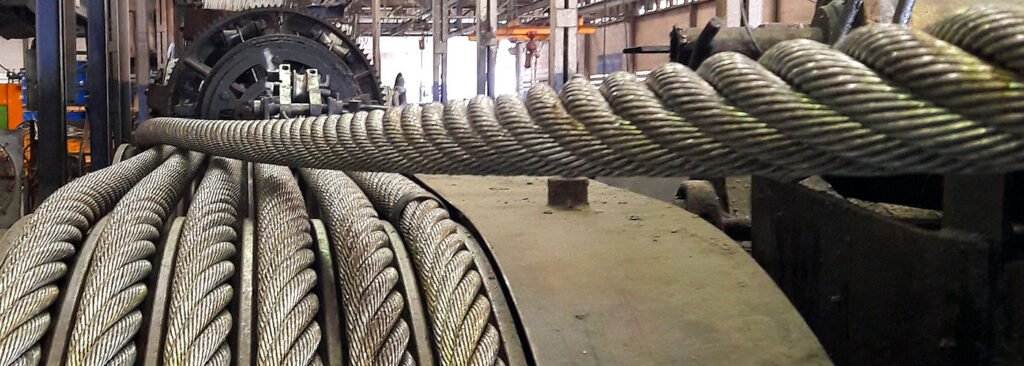
Chapt 3
Compacted Wire Rope Production Procedure
Compacted wire rope is produced through a series of meticulous processes that enhance its strength, flexibility, and wear resistance compared to standard wire ropes. Here’s a general overview of the compacted wire rope production procedure:
Material Selection: The process begins with the selection of high-quality steel wire, which is the primary material used in the manufacturing of wire ropes. The steel wire must meet specific composition and tensile strength standards.
Wire Drawing: The selected steel wires are drawn through a series of dies to reduce their diameter and increase their tensile strength. This is done gradually to avoid any damage to the wire.
Stranding: After drawing, the wires are stranded together. This involves twisting multiple wires into helical strands. In compacted rope, these strands are often pre-formed to a specific shape that fits more closely together.
Compacting: This critical step involves passing the strands through a compaction die or roller, which compresses and deforms the wires and strands into a more compact and denser configuration. This reduces the internal voids and increases the contact area among the wires, which enhances the load-bearing capacity and resistance to wear and bending fatigue.
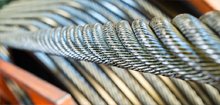
Closing: The compacted strands are then closed into a rope around a core, which could be fiber or another set of metal strands. The core supports the strands and distributes the load evenly across the rope. The closing process is critical and must ensure that the rope maintains its compact structure without any distortion.
Heat Treatment: After closing, the wire rope might undergo a heat treatment process to relieve stresses induced during drawing, stranding, and compacting. This process improves the flexibility and fatigue resistance of the rope
Lubrication: The rope is then lubricated to reduce friction between the wires and strands during use, which helps in increasing the rope’s lifespan and performance
Inspection and Testing: The final step involves thorough inspection and testing for diameter, tensile strength, flexibility, and other critical parameters to ensure the rope meets all required specifications and standards.
Coiling and Packaging: Once approved, the rope is coiled and packaged for shipping to customers.
Each of these steps is crucial in ensuring that the compacted wire rope delivers superior performance and durability. The specifics of the process can vary based on the rope application and the manufacturer’s technology and standards.
Chapt 4
Application of Compacted Wire Rope
Compacted strand wire rope is widely used across various industries due to its enhanced strength, flexibility, and resistance to abrasion compared to standard wire rope. Here are some of its key applications:
Crane Industry
Compacted wire rope is often used in crane cables because it provides higher breaking strength and improved resistance to rotation and bending fatigue, which is essential for lifting heavy loads safely.
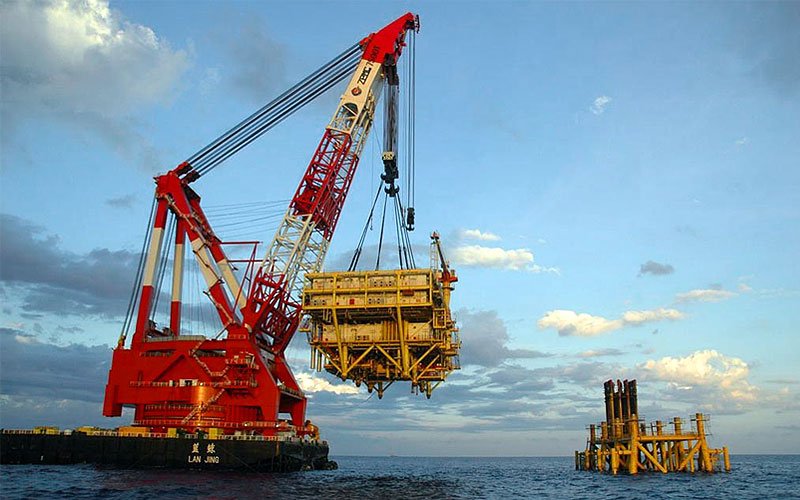
Oil and Gas Drilling
In offshore oil rigs and marine applications, rotation-resistant wire rope is used for lifting heavy loads such as equipment, containers, and personnel. It helps maintain stability and control during lifting operations, even in harsh sea conditions.
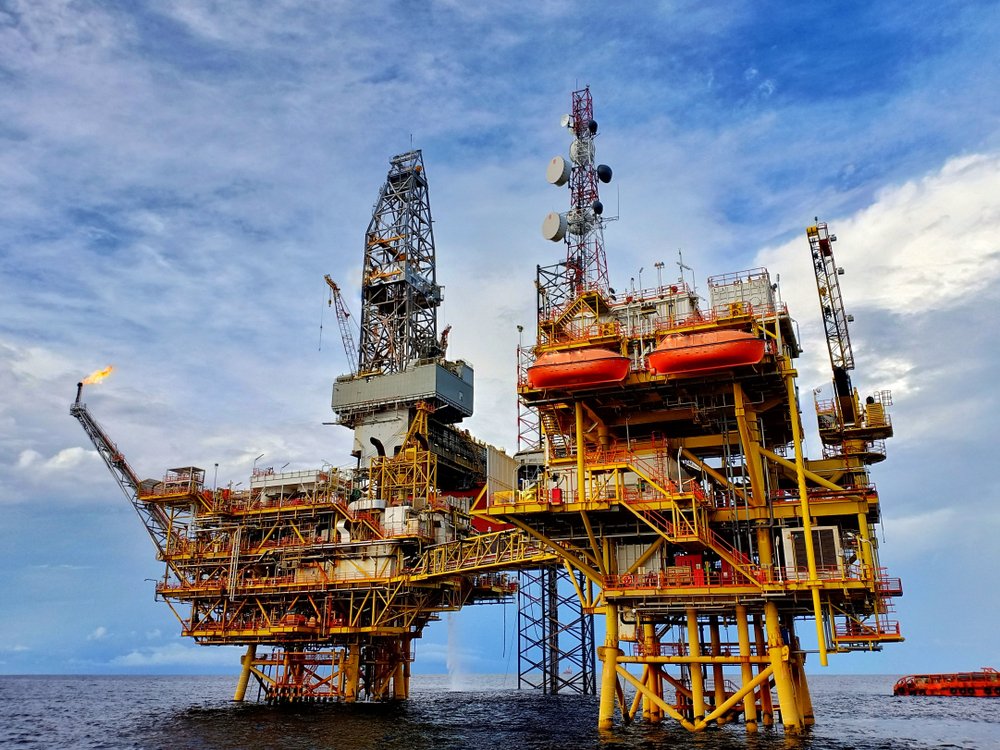
Marine Applications
Compacted strand wire rope is ideal for maritime environments, particularly in mooring lines, towing lines, and anchor lines, due to its high strength and reduced stretch, which ensure better handling and durability under adverse conditions.
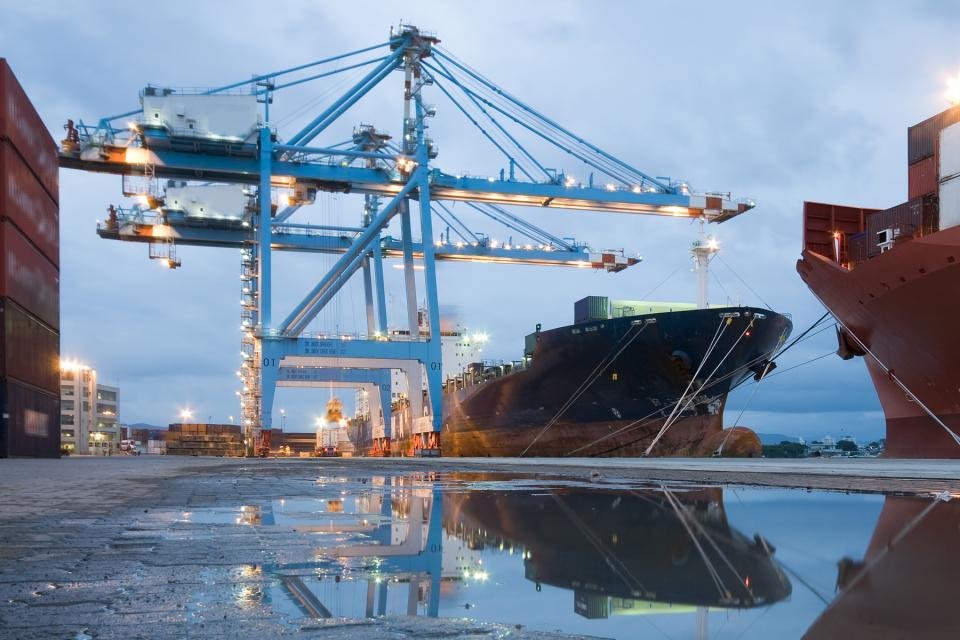
Mining
In mining operations, compacted wire rope is used in hoist and drag lines. It offers high resistance to abrasion and fatigue, which is essential for the continuous lifting and dragging of heavy materials.
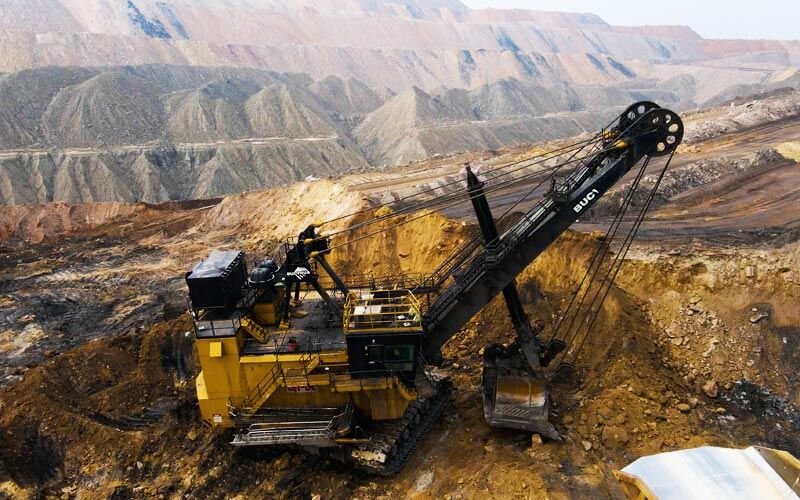
These applications benefit from the compacted wire rope’s enhanced properties, such as increased load-bearing capacity, improved flexibility, reduced internal friction, and superior resistance to fatigue and environmental damage.
Chapt 5
How Do You Properly Select And Use Compacted Wire Rope?
Compacted strand wire rope, also known as compacted wire rope or swaged rope, is designed to provide greater strength, durability, and resistance to crushing and abrasion compared to standard wire rope. Here’s a guide on properly selecting and using compacted strand wire rope:
Understand Your Requirements: Determine the specific requirements of your application, including load capacity, operating conditions (such as temperature, exposure to chemicals, etc.), and environmental factors (such as moisture, abrasion, etc.). This will help you select the appropriate construction and material for your compacted wire rope.
Choose the Right Construction: Compacted wire ropes are available in various constructions, including standard, rotation-resistant, and non-rotating constructions. Select the construction that best suits your application requirements. For example, rotation-resistant ropes are suitable for applications where minimizing twisting is important, such as crane operations.
Consider the Core: Compacted wire ropes may have either a fiber core (FC) or a steel core (IWRC). Steel core ropes provide greater strength and resistance to crushing, making them suitable for heavy-duty applications. Fiber core ropes are more flexible and lighter but may not be as strong as steel core ropes.
Select the Correct Diameter and Length: Choose the appropriate diameter and length of the compacted wire rope based on your load requirements and the dimensions of your equipment or machinery.
Inspect Regularly: Before each use, inspect the compacted wire rope for any signs of wear, damage, or deformation. Look for broken wires, corrosion, and flattened sections, as these can indicate potential failure points. Replace any damaged or worn ropes immediately to prevent accidents.
Proper Installation: Follow the manufacturer’s guidelines for proper installation of the compacted wire rope. Ensure that it is correctly seated and secured to the equipment or machinery, and that it is properly tensioned according to the recommended specifications.
Use Proper Accessories: Use appropriate fittings, such as thimbles, clips, or sockets, to terminate and secure the ends of the compacted wire rope. Make sure these accessories are properly installed and tightened to prevent slippage or failure.
Follow Operating Procedures: Adhere to all recommended operating procedures and safety guidelines when using compacted wire rope. Avoid overloading the rope beyond its rated capacity, and operate equipment or machinery smoothly to minimize stress on the rope.
Regular Maintenance: Perform regular maintenance, including cleaning and lubricating the compacted wire rope, to prolong its lifespan and ensure optimal performance. Remove any dirt, debris, or corrosive substances that could cause premature wear or damage.
Training and Certification: Ensure that personnel involved in handling and using compacted wire rope are properly trained and certified in safe rigging practices. Provide ongoing training to keep them updated on best practices and safety procedures.
By following these guidelines, you can properly select and use compacted strand wire rope to ensure safe and efficient operations in various industrial applications.
Chapt 5
Quality Assurance For Compacted Wire Rope
Quality assurance (QA) for compacted wire rope is crucial to ensure its reliability, safety, and longevity, especially when used in critical applications such as lifting, construction, and maritime operations. Here’s a detailed look at the key aspects of quality assurance for compacted wire rope:
Specification Compliance: The company would ensure all wire rope meets specific industry standards such as EN12385-4, or GB8918 other relevant certifications depending on the geographic region and application. Compliance includes adherence to specifications regarding dimensions, material composition, and mechanical properties.
Raw Material Quality Control: All steel wire used in the production would undergo rigorous testing for tensile strength, chemical composition, and other properties. This ensures the raw materials used are of high quality and suitable for the demanding applications of compacted wire rope.
Production Monitoring: The compacting process would be closely monitored to ensure the wire rope is manufactured to precise specifications. This includes the consistency of the compaction, which affects the rope’s flexibility, strength, and fatigue resistance.
Advanced Testing Procedures: Aulone would likely use advanced testing methods including:
Tensile Testing: To verify that the rope can withstand the forces it is rated for without breaking.
Fatigue Testing: To determine how the rope withstands repeated loading and unloading cycles.
Rotational Resistance Testing: Important for applications where the wire rope should not untwist under load.
Corrosion Testing: Especially for ropes used in marine or chemically aggressive environments.
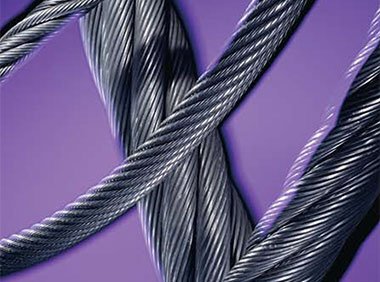
End-to-End Traceability: Implementing traceability from the raw material stage through to the final product. This would include batch numbers, production dates, and testing records to ensure every piece of wire rope can be traced back to its source materials and production conditions.
Visual Inspection: Regular visual inspections during production to identify any potential defects such as irregularities in compaction, surface imperfections, and inconsistencies in lubrication or coating.
Employee Expertise: Continuous training for staff involved in the production and quality assurance processes to ensure they are up-to-date with the latest technologies and standards.
Customer Feedback Integration: Systematic collection and analysis of customer feedback to identify areas for improvement and ensure that the product meets the real-world demands of its applications.
Continuous Improvement: Leveraging findings from quality tests, customer feedback, and internal audits to continually improve the manufacturing process and product quality.
Documentation and Certification: Providing detailed documentation and certification with each shipment, certifying that the wire rope meets all relevant standards and specifications.
By adopting such comprehensive quality assurance measures, a company like Aulone can maintain high standards for their compacted wire rope, ensuring reliability, safety, and customer satisfaction. If Aulone is indeed a specific company or product, it might be helpful to consult directly with them for more detailed and precise information on their QA processes.
Get the catalogue
Leave a request and we will send you the catalogue with Aulone steel wire ropes by e-mail
86-15573139663
86-15363044363