35WXK7
High performance steel wire rope from Aulone for Floating Crane
High Performance Steel Wire Ropes For Floating Crane
Lifting ever-heavier loads brings constant challenges for floating cranes, whether in harbors or offshore. Safety remains the top priority for crane operators during every lift. Aulone’s high-performance steel wire ropes, featuring plastic-impregnated steel cores, ensure maximum efficiency and safety throughout their lifespan. Our ropes are used worldwide to lift heavy loads on ships, available in both galvanized and bright finishes to meet various customer needs.
Aulone offers rotation-resistant ropes as well as specialized 6- and 8-strand steel wire ropes, ideal for all types of heavy-lift cranes. These hoist ropes deliver exceptionally high breaking strength and outstanding wear resistance, thanks to compacted outer strands. With our compaction technology, we guarantee consistent diameters with minimal variation along the entire rope length, ensuring smooth, safe crane operations and reducing total ownership costs.
Tailored Floating Crane Wire Ropes to Suit Your Needs!
Are you looking for high-quality wire ropes for your floating crane? We offer customized wire rope solutions designed to meet your specific requirements, ensuring optimal performance and safety for your lifting operations.
Available Sizes: Ranging from 8mm up to 50mm.
Tensile Strength: 1770, 1960, 2160mpa.
Specifications on Offer: EN12385-4, GB8918, YB/T5359 and specific customer requirements.
Surface Treatments: Options including hot galvanized, ungalvanized, and stainless steel.
Special technology: Including multi-strand ropes, plastic impregnated, compacted, galvanized.
Structure: 35WX7, 35WXK7, 24WXK7, 15XK7, 8XK26,8XK26WS-EPIWRC,6XK36WS, 6XK26, etc
Lay types: RHLL, RHRL, LHLL, LHOL
Certifications: All our ropes come with BV and CE certifications, providing you with the assurance of quality and compliance with international standards.
To discuss your specific needs and get a quote for tailored floating crane wire ropes, reach out to our team of specialists at info@wireropes.net. Let us help you elevate your construction projects with our premium wire rope solutions!
Hoist Ropes
High-Performance Hoist Ropes for Floating Cranes
Heavy lift applications bring new demands to floating cranes, especially as they tackle increasingly heavy loads on a daily basis. Whether deployed in ports or offshore, safety remains the highest priority for crane operators during each lift. Aulone’s high-performance steel wire ropes, designed with advanced materials and construction, help customers achieve both maximum safety and efficiency throughout the product’s entire service life.
Our hoist ropes are engineered specifically for heavy lift cranes used on ships worldwide. Constructed with a highly durable steel core and available in both galvanized and bright finishes, our ropes are designed to meet the varied requirements of our clients across the globe.
In addition to rotation-resistant options, Aulone provides specialized 6 and 8-strand steel wire ropes that are optimized for heavy lift operations. These ropes deliver not only exceptionally high breaking strength but also superior wear resistance, thanks to the compacted outer strands. Our advanced compaction technology ensures consistent diameters with minimal variations along the entire rope length, offering smooth and reliable crane operation while reducing total cost of ownership.
Let Aulone’s high-performance wire ropes support your lifting needs with the strength, reliability, and safety you can trust.
Auxiliary hoist ropes
The lifting of increasingly heavy loads in heavy lift applications introduces new challenges for floating cranes, day after day. Whether these cranes are operating in harbors or on offshore projects, ensuring safety during lifting operations remains the top priority for crane operators. Equipped with a plastic-impregnated steel core, Aulone’s high-performance steel wire ropes enable customers to achieve maximum efficiency and safety throughout the entire lifespan of the ropes. Our ropes have been successfully used to lift heavy loads on ships worldwide. Based on customer requirements, these ropes are available in both galvanized and bright finishes.
Boom hoist and grab ropes
When lifting heavy loads on floating cranes, safety is crucial and thus one of the biggest challenges for ship crane operators. Whether in ports or offshore areas, Teufelberger-Redaelli’s high performance steel wire ropes help you achieve maximum efficiency. In addition to their perfected construction manufactured in tested and tried production processes, the plastic impregnated PLASTFILL® steel core is key in achieving the necessary high performance for a variety of technical parameters. This is one of the key factors which ensures the exceptional lifetime of these ropes.
Your Ultimate Guide to Acquiring Floating Crane Wire Rope
Acquiring the right wire rope for a floating crane is critical to ensure safety, efficiency, and longevity. Floating cranes are used in demanding environments, including ports, offshore installations, and heavy-lift marine operations. This guide provides everything you need to know about selecting, evaluating, and acquiring the best wire rope for your specific application.
Table of contents
Chapt 1
What are the key components of a floating crane wire rope?
A floating crane wire rope is composed of several key components, each designed to contribute to the rope’s strength, durability, flexibility, and suitability for marine environments. Here’s a breakdown of its main components:

1. Wires:
- Definition: Thin strands of steel that form the individual building blocks of the rope.
- Material: Typically high-carbon steel, often galvanized or stainless steel for corrosion resistance.
- Purpose: Provide tensile strength and resistance to wear.
2. Strands:
- Definition: Groups of wires twisted together to form a strand.
- Construction: Strands can have different patterns such as Warrington, Seale, or filler wire construction, which balance strength, flexibility, and wear resistance.
- Purpose: Provide the rope’s overall shape and flexibility.
3. Core:
- The core is the central part of the wire rope and provides support to the strands. It can be of various types:
- Independent Wire Rope Core (IWRC): A separate wire rope core, offering higher strength and resistance to crushing.
- Fiber Core (FC): Made of synthetic or natural fibers, providing flexibility and cushioning but less strength.
- Plastic-Impregnated Core (EPIWRC): A core embedded in plastic for additional protection against corrosion and wear.
4. Lubrication:
- Definition: Special lubricants applied during the manufacturing process.
- Purpose: Reduce friction between wires and strands, protect against internal corrosion, and enhance the rope’s lifespan.
5. Galvanized Coating (Optional):
- Definition: A zinc coating applied to individual wires to resist corrosion.
- Purpose: Protects against saltwater exposure, a critical feature for marine environments.
6. Plastic Coating (Optional):
- Definition: A plastic layer covering the entire rope or impregnating the strands.
- Purpose: Enhances corrosion resistance, minimizes wear, and provides an additional barrier against environmental damage.
7. Lay of the Rope:
- Definition: The direction and pattern in which strands are twisted.
- Right-Hand Lay: Strands twisted in a right-hand direction.
- Left-Hand Lay: Strands twisted in a left-hand direction.
- Lang’s Lay or Regular Lay: Dictates how strands and wires interact for flexibility or wear resistance.
- Purpose: Influences the rope’s performance, flexibility, and rotation resistance.
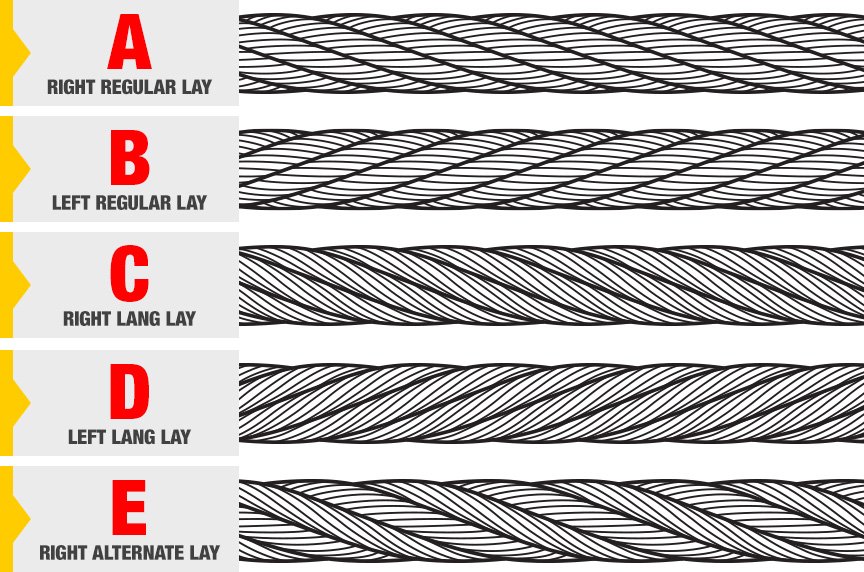
8. End Terminations (Attachments):
- Definition: Fittings or ends of the wire rope, such as swaged sockets, thimbles, or ferrules.
- Purpose: Provide a secure attachment to the crane or load and ensure safe load handling.
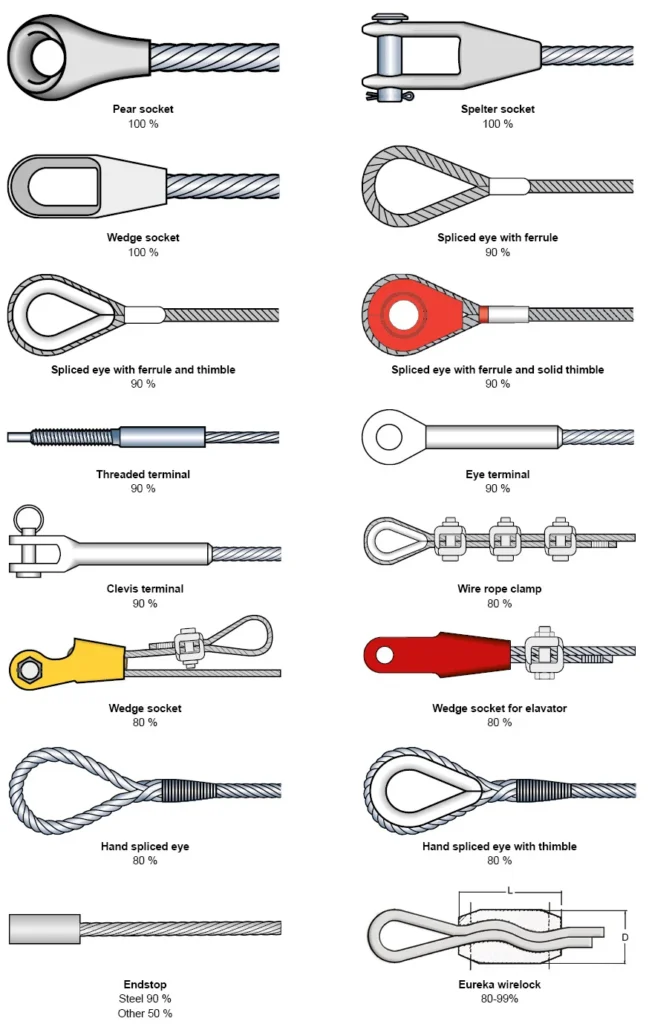
Additional Considerations:
- Breaking Load Capacity: Ensures the rope can handle the maximum intended load with safety margins.
- Rotational Stability: Non-rotating ropes like 35WXK7 or similar configurations are often used to prevent twisting during lifting operations.
These components work together to create a wire rope that is strong, durable, and suited to the demanding conditions encountered in floating crane applications.
Chapt 2
What factors can affect the lifespan of a wire rope on a floating crane?
The lifespan of a wire rope on a floating crane is influenced by numerous factors that range from operational conditions to maintenance practices. Proper management of these factors can significantly extend the rope’s service life, ensuring safety and cost-efficiency. Below are the critical factors affecting the lifespan of wire ropes in floating crane applications:
1. Operational Factors
1.1 Load Characteristics
- Static Loads: Consistent loads are less damaging compared to fluctuating or dynamic loads.
- Shock Loads: Sudden application of high forces can cause internal wire damage and reduce fatigue resistance.
- Overloading: Regularly exceeding the rope’s safe working load (SWL) drastically shortens its lifespan.
1.2 Bending Over Sheaves and Drums
- Sheave Diameter: Insufficient sheave diameters cause excessive bending, leading to fatigue.
- A diameter-to-rope ratio (D/d) of at least 20:1 is recommended for most ropes.
- Drum Alignment: Misaligned drums cause uneven stress and premature wear.
- Fleet Angle: Excessive fleet angles (more than 1.5°) lead to uneven winding and rope damage.
1.3 Tension Variability
- Constant tension changes, as in lifting and lowering operations, induce fatigue.
- Unequal tension distribution across strands may cause localized failures.
1.4 Rotational Forces
- High torsional forces in non-rotating ropes, if improperly handled, can lead to internal damage.
1.5 Environmental Conditions
- Saltwater Exposure: Marine environments accelerate corrosion unless the rope is well-lubricated or galvanized.
- UV Radiation: Prolonged sunlight exposure can degrade synthetic cores or coatings.
- Temperature Extremes: Extremely high or low temperatures can reduce the rope’s flexibility and performance.
2. Rope Construction Factors
2.1 Material Properties
- Higher tensile steel wires provide greater strength but may be less resistant to fatigue.
- Galvanized or plastic-coated wires resist corrosion better than uncoated options.
2.2 Core Type
- IWRC (Independent Wire Rope Core): Superior resistance to crushing and fatigue.
- Fiber Core (FC): More flexible but less durable under heavy loads and marine conditions.
- Plastic-Impregnated Core (EPIWRC): Offers the highest resistance to corrosion and internal wear.
2.3 Rope Lay
- Regular Lay: Better resistance to crushing and abrasion.
- Lang’s Lay: Offers better flexibility but is more prone to twisting.
2.4 Lubrication
- Factory-applied lubrication prevents internal friction but wears off over time.
- The type and amount of lubricant affect resistance to corrosion and heat.
3. Maintenance Practices
3.1 Inspection
- Inadequate or irregular inspections lead to undetected damage, such as broken wires, corrosion, or core failure.
- Magnetic flux or other non-destructive tests can reveal hidden issues.
3.2 Re-Lubrication
- Failure to reapply marine-grade lubricants accelerates internal wear and corrosion.
3.3 Cleaning
- Salt and debris can accumulate on the rope, acting as abrasives. Regular cleaning is essential.
3.4 End Termination Maintenance
- Neglecting sockets or ferrules can lead to uneven load distribution and stress concentration.
4. Handling and Installation Factors
4.1 Proper Installation
- Improper winding on drums or incorrect tension during installation can induce kinks and crush damage.
4.2 Storage
- Ropes stored in wet or poorly ventilated environments are more prone to rust and corrosion.
- Avoid exposing ropes to direct sunlight or extreme temperatures during storage.
4.3 Usage Practices
- Dragging the rope over sharp edges or rough surfaces causes abrasion.
- Frequent use without allowing the rope to “rest” increases wear.
5. Design and Equipment Compatibility
5.1 Compatibility with Crane
- Rope specifications must match the crane’s load and operational requirements.
- Using ropes with improper diameters or strength ratings leads to premature failure.
5.2 Sheave and Drum Conditions
- Worn or damaged sheaves/drums can cause localized abrasion and crushing.
- Grooves must be appropriately sized for the rope diameter.
5.3 Fleet Angle Management
- Mismanaged fleet angles lead to uneven spooling and stress concentrations.
6. Environmental Protection Measures
6.1 Corrosion Resistance
- Regular exposure to saltwater necessitates the use of galvanized or plastic-coated ropes.
- Environmental coatings and marine-grade lubricants are critical.
6.2 UV and Weather Protection
- For synthetic components, UV-resistant coatings prolong the rope’s life.
7. Operator Training and Handling
7.1 Skilled Operation
- Sudden jerks or rapid lowering can induce shock loads, weakening the rope.
- Operators should be trained to avoid bad practices like side pulling or improper load balancing.
7.2 Monitoring
- Continuous load monitoring can prevent accidental overloading.
8. Failure to Replace Worn Ropes
Using a rope past its recommended replacement criteria is highly unsafe and accelerates damage to other components of the crane system.
Key Indicators of Wire Rope Wear
- Broken wires exceeding 10% of total wires in any strand.
- Corrosion, rust, or pitting.
- Core failure or wire rope deformation (flattening, kinking, or birdcaging).
- Reduced diameter beyond acceptable tolerances.
- Excessive elongation or stretch.
Conclusion
To maximize the lifespan of wire ropes on floating cranes, it is essential to select the appropriate rope construction, maintain proper operational practices, and follow a stringent inspection and maintenance schedule. Each factor—whether related to the environment, design, handling, or maintenance—plays a critical role in ensuring the wire rope’s longevity and performance. Regular training and adherence to best practices can prevent premature wear, ensuring safety and operational efficiency.
Chapt 3
How do I choose the right wire rope for a specific floating crane application?
Choosing the right wire rope for a specific floating crane application is crucial to ensure safety, efficiency, and durability. The selection process involves assessing the operational requirements, environmental conditions, and the crane’s specifications. Below is a comprehensive guide to help you make an informed decision:
1. Understand the Application Requirements
1.1 Load Capacity
- Safe Working Load (SWL): Determine the maximum weight the rope needs to lift, including any dynamic forces.
- Breaking Load: Select a rope with a minimum breaking load that is at least 5–10 times the maximum load to ensure a sufficient safety margin.
1.2 Operating Conditions
- Frequency of Use: Consider the expected load cycles. Ropes subjected to frequent use should have high fatigue resistance.
- Shock Loads: For operations with sudden loading (e.g., wave-induced crane movements), choose a rope designed to handle shock forces.
1.3 Crane Configuration
- Type of Crane: Floating cranes may use different ropes for hoisting, luffing, or guy lines. Each application may require distinct properties.
- Rope Path: Consider the fleet angle, drum spooling patterns, and number of sheaves to ensure compatibility.
2. Assess Environmental Factors
2.1 Corrosion Resistance
- Marine Environment: Saltwater exposure necessitates galvanized or plastic-coated ropes to prevent rust.
- Humidity and Temperature: High-humidity areas or extreme temperature ranges require ropes with additional protective coatings or specific materials.
2.2 Abrasion Resistance
- Operations involving frequent contact with sheaves, drums, or other surfaces require abrasion-resistant rope constructions like 8-strand or plastic-coated ropes.
3. Evaluate Wire Rope Specifications
3.1 Construction
- Multi-Strand Ropes:
35×7 Non-Rotating: Ideal for hoisting operations requiring rotational stability.
- Core Type:
- IWRC (Independent Wire Rope Core): High strength, crush resistance, and stability.
- Fiber Core (FC): Increased flexibility but less durable in heavy-duty applications.
- Plastic-Impregnated Core (EPIWRC): Enhanced corrosion resistance and longevity.
3.2 Diameter
- Ensure the rope’s diameter matches the sheave and drum grooves to avoid uneven wear or crushing.
3.3 Rope Lay
- Lang’s Lay: Offers superior abrasion resistance and higher strength for lifting applications.
- Regular Lay: Preferred for applications where rotation resistance is critical.
3.4 Tensile Strength
- High-tensile wire ropes, such as those made of 1960mpa, 2160mpa.
4. Determine Performance Criteria
4.1 Fatigue Resistance
- Applications with frequent bending over sheaves require ropes with high fatigue resistance. Opt for configurations like 6x36WS or similar.
4.2 Rotation Resistance
- For lifting operations, especially at great heights, non-rotating ropes such as 35×7 are crucial to prevent twisting under load.
4.3 Crushing Resistance
- In applications with high pressure on the drum or sheaves, use wire ropes with robust cores, such as IWRC or EPIWRC.
4.4 Lubrication
- Pre-lubricated ropes reduce internal friction and corrosion. Marine-grade lubricants are essential for floating crane applications.
5. Check Compatibility with Equipment
5.1 Sheaves and Drums
- Diameter-to-Rope Ratio (D/d): Ensure the sheaves and drum diameters comply with the rope’s specifications (typically D/d ≥ 20).
- Groove Profile: The groove should match the rope diameter for even stress distribution.
5.2 End Fittings
- Select appropriate terminations like swaged sockets, thimbles, or ferrules based on the crane’s design.
6. Perform a Cost-Benefit Analysis
While high-performance wire ropes may have a higher upfront cost, they can reduce long-term maintenance costs and downtime. Consider the total cost of ownership rather than the initial expense.
7. Seek Expert Advice
Consult with manufacturers or suppliers to select the most appropriate wire rope. Provide detailed information about:
- Crane type and operational requirements.
- Environmental conditions (e.g., salinity, temperature).
- Load specifications and operational cycles.
8. Maintenance and Monitoring
Selecting the right wire rope is only the beginning. Regular inspection, cleaning, lubrication, and tension adjustments are essential to ensure long-term performance.
By carefully considering these factors, you can choose a wire rope that meets the operational demands of your floating crane, minimizes downtime, and enhances safety. If you need additional guidance, feel free to ask for tailored recommendation
Chapt 4
What coating or finish should the rope have?
The coating or finish your wire rope should have depends on the operating environment and application requirements. Here’s a breakdown of the most common options and their suitability:
1. Uncoated (Bright) Steel Wire Rope
- Best for: Dry environments with minimal exposure to moisture or corrosive elements.
- Advantages: Higher tensile strength compared to coated ropes of the same diameter; typically less expensive.
- Limitations: Prone to rust and corrosion, especially in marine or humid conditions.
2. Galvanized Steel Wire Rope
- Best for: Environments with moderate exposure to moisture or corrosive elements, such as light marine settings or industrial use.
- Advantages: A protective zinc coating resists rust and extends the lifespan of the rope in corrosive conditions.
- Limitations: Slightly lower tensile strength compared to uncoated ropes; the zinc coating can wear down over time.
3. Stainless Steel Wire Rope
- Best for: High-corrosion environments, such as marine applications, floating cranes, and offshore operations.
- Advantages: Excellent corrosion resistance; requires minimal maintenance; long-lasting in harsh conditions.
- Limitations: More expensive than galvanized or uncoated ropes; slightly lower tensile strength.
4. Plastic-Coated Wire Rope
- Best for: Applications where the rope needs added protection from wear and abrasion or to prevent contact damage.
- Advantages: A plastic (e.g., PVC or nylon) layer protects the rope strands, reduces wear, and adds flexibility.
- Limitations: Not suitable for heavy-duty applications where strength is a priority; the coating can degrade under UV exposure or extreme temperatures.
Recommended Coating for Floating Crane Wire Rope
- Primary Choice: Galvanized Wire Rope for its balance of corrosion resistance and cost-effectiveness.
- Secondary Choice: Stainless Steel Wire Rope if the crane operates in highly corrosive environments, such as saltwater exposure or offshore operations.
Tip for Buyers:
Ask about additional protective measures like special lubricants to further reduce internal friction and corrosion, especially for marine environments.
Chapt 5
What's Min breaking force?
The Minimum Breaking Force (MBF) of a wire rope is the maximum load the rope can bear before failure. It is a crucial parameter for ensuring safety and reliability in various applications, including lifting, towing, and structural support.
1. What is MBF?
- Definition: The force required to break a wire rope under tension, measured in kilonewtons (kN) or metric tons (MT).
- Importance:
- Determines the maximum safe load the rope can handle.
- Prevents overload and ensures operational safety.
- A critical factor in compliance with industry standards.
2. Factors Influencing MBF
Rope Grade:
- Higher grades (e.g., 1960 MPa, 2160 MPa) have higher tensile strength, resulting in greater MBF.
Rope Diameter:
- Larger diameters provide higher MBF due to more material bearing the load.
Construction:
- Compact or multi-strand ropes often have a higher MBF than standard constructions of the same diameter.
Core Type:
- IWRC (Independent Wire Rope Core): Offers higher MBF compared to FC (Fiber Core) ropes.
Coating:
- Galvanized or plastic-coated ropes may have slightly different MBFs due to added material layers.
3. Calculating Working Load from MBF
The Working Load Limit (WLL) is derived from the MBF using a safety factor:
- WLL = MBF ÷ Safety Factor
Safety Factor Guidelines:
- Lifting Applications: 5:1 to 7:1 (e.g., cranes, elevators).
- Static Applications: 3:1 to 5:1 (e.g., structural cables).
- Dynamic Applications: Higher safety factors may be needed due to sudden loads or impacts.
4. Ensuring Proper MBF Selection
Understand Load Requirements:
- Determine the maximum expected load and select a rope with an MBF that accommodates the load plus the safety margin.
Consult Rope Specifications:
- Always check the manufacturer’s datasheet for precise MBF values for the specific rope grade and construction.
Inspect Regularly:
- Ropes under constant use may experience wear, reducing MBF over time. Regular inspections and maintenance are critical.
5. Conclusion
The MBF is a key specification for choosing the right wire rope. Always ensure the MBF exceeds the operational load when factoring in safety margins. Understanding MBF and its relation to rope grade, diameter, and construction ensures safe and efficient operations.
For detailed MBF values and recommendations, consult your wire rope supplier or technical manual.
Chapt 6
What environmental factors should I consider?
When selecting a wire rope for a floating crane, it’s critical to evaluate the environmental factors that can impact the rope’s performance, lifespan, and safety. Here are the key factors to consider:
1. Corrosion Risks
- Marine Environment: Exposure to saltwater is highly corrosive and can significantly shorten the lifespan of the rope. Look for galvanized or stainless steel wire ropes with additional corrosion resistance.
- Humidity and Moisture: Constant exposure to damp conditions, even if not directly in saltwater, can lead to rust and degradation.
2. Temperature Extremes
- Cold Temperatures: Low temperatures can make some wire ropes brittle and reduce flexibility. Opt for ropes designed for cold-weather performance.
- High Temperatures: Excessive heat can weaken the steel or degrade protective coatings and lubricants. Ensure the rope is rated for the crane’s operating temperature range.
3. Abrasion and Wear
- Contact Surfaces: Frequent contact with sheaves, drums, or rough surfaces can wear down the wire rope. Consider ropes with abrasion-resistant coatings or durable outer strands.
- Handling Conditions: Repeated bending and unspooling can lead to fatigue, especially in rough environments.
4. UV Exposure
- Sunlight Exposure: Prolonged exposure to ultraviolet (UV) light can degrade plastic coatings on some ropes. If using plastic-coated wire, ensure it’s UV-resistant.
5. Chemical Exposure
- Industrial Chemicals: In environments where chemicals like oil, solvents, or acidic substances are present, the rope’s material and coating must resist degradation.
- Saltwater Spray: Even indirect saltwater exposure can cause corrosion over time.
6. Load and Shock Conditions
- Dynamic Loads: Floating cranes often face sudden or fluctuating loads due to waves and wind. Choose a rope that can handle dynamic stresses without fatigue.
- Shock Loads: Environmental factors, such as wind gusts or unexpected movements, can cause sharp increases in tension. A strong, durable rope with proper elasticity is essential.
7. Environmental Debris
- Sand, Mud, or Marine Growth: If the rope will encounter debris, such as sand or marine organisms, this can cause internal wear or reduce the rope’s performance. Lubricated ropes with sealed designs can help mitigate this.
8. Wind and Wave Action
- Offshore Conditions: Waves and wind add unique stress to floating cranes. A rotation-resistant or stabilized rope may be necessary to prevent twisting or kinking.
Best Practices:
- Choose a wire rope with a protective coating (e.g., galvanized or stainless steel) to resist corrosion.
- Use lubrication to minimize wear from internal friction and exposure to environmental elements.
- Conduct regular inspections and maintenance to identify early signs of wear or corrosion.
By considering these factors, you can ensure that the wire rope is well-suited for your crane’s operating conditions and achieves optimal performance and longevity.
Chapt 7
What specifications or parameters should I provide to obtain an accurate quotation?
To get an accurate quote for Floating Crane wire rope, you need to provide the following detailed parameters to the supplier:
1. Basic Specifications
- Diameter:
The specific diameter of the wire rope (e.g., 28mm, 36mm). Specify in mm or inches. - Length:
The total required length of the rope (e.g., 1000m). Specify in meters or feet. - Construction:
Specify the construction type, such as 35WXK7, 8XK26WS-IWRC, etc., as it affects flexibility and strength. - Tensile Strength:
The rope’s strength rating (e.g., 1770 N/mm², 1960 N/mm²,2160 N/mm²). - Min breaking force:
The maximum load a wire rope can handle before breaking, measured in kilonewtons (kN) or metric tons (MT).
Purpose: Ensures the rope can safely carry loads without risk of failure.
2. Coating and Surface Treatment
- Coating Type:
- Bright (Uncoated)
- Galvanized
- Stainless Steel
- Plastic-Coated
- Corrosion Resistance:
Specify if it will be used in a marine environment or if additional anti-corrosion treatment is needed.
3. Standards:
Specify the required compliance standards, such as EN 12385, GB8918 etc
4. Certifications:
Request additional certifications if needed, such as BV, Lloyd’s Register, or CE marking.
5. Quantity and Delivery Requirements
- Quantity:
Total amount needed (e.g., the number of ropes or total weight in tons). - Delivery Time:
Specify the timeframe when the rope is needed. - Delivery Location:
Mention the delivery port or location (e.g., FOB or CIF terms).
6. Special Requirements
- Lubrication:
Indicate if pre-lubrication is required and the preferred type of lubricant. - Accessories:
Specify if additional fittings like sockets, thimbles, or end connections are needed.
By providing these details, Aulone can calculate costs and offer you an accurate and comprehensive quote. This saves time and ensures you procure the most suitable wire rope for your floating crane.
Want to buy wire rope & sling?
We’re happy to assist you in finding the ideal rope for your application
86-15573139663
86-15363044363