Answer:
6: Refers to the number of strands in the wire rope.
36: Refers to the number of wires in each strand.
IWRC: Stands for Independent Wire Rope Core, meaning the core of the rope is made of a bundle of wires, which provides greater strength and flexibility compared to a fiber core.
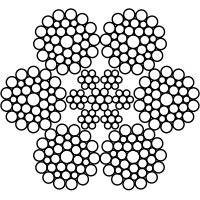
This article will continue the discussion on 6X36WS-IWRC steel wire rope from the following aspects.
Outline
6X36WS-IWRC Advantage
A 6-strand steel wire rope with a metal core, designed with a Warrington-Seale construction for enhanced flexibility and a high number of wires.
This wire rope is ideal for lifting applications, including overhead cranes, container cranes, gantry cranes, auto cranes, and excavators.
It is manufactured in compliance with the EN 12385-4 standard.
What is the difference between 6x19 and 6x36 wire rope?
The main difference between 6×19 and 6×36 wire rope lies in their construction, which affects their flexibility, strength, and durability:
-
Construction:
- 6×19: This rope consists of 6 strands, each containing 19 wires. It is a simpler construction and is more commonly used for general-purpose applications.
- 6×36: This rope also consists of 6 strands, but each strand contains 36 wires. It has a higher number of wires per strand, which makes it more flexible and capable of withstanding more wear and tear.
-
Flexibility:
- 6×19: Less flexible compared to 6×36. This construction is more rigid, which means it’s better suited for applications where less bending and flexing are required.
- 6×36: More flexible and can handle repetitive bending better, making it ideal for applications like cranes and hoists, where the rope needs to move around sheaves or pulleys frequently.
-
Strength and Durability:
- 6×19: Generally, it has a lower breaking strength than 6×36 due to fewer wires in each strand.
- 6×36: Offers higher strength and better resistance to wear, but may not be as strong in high-load applications where rigidity is required.
-
Usage:
- 6×19: Often used in lifting or rigging applications where flexibility isn’t a major concern, and strength needs are moderate.
- 6×36: Suitable for more dynamic applications, such as cranes, where the rope will undergo frequent bending, or for applications requiring higher durability.
So, 6×36 provides better flexibility and wear resistance, while 6×19 is stiffer and may be better for static, high-load applications.
What is 6x19 wire rope used for?
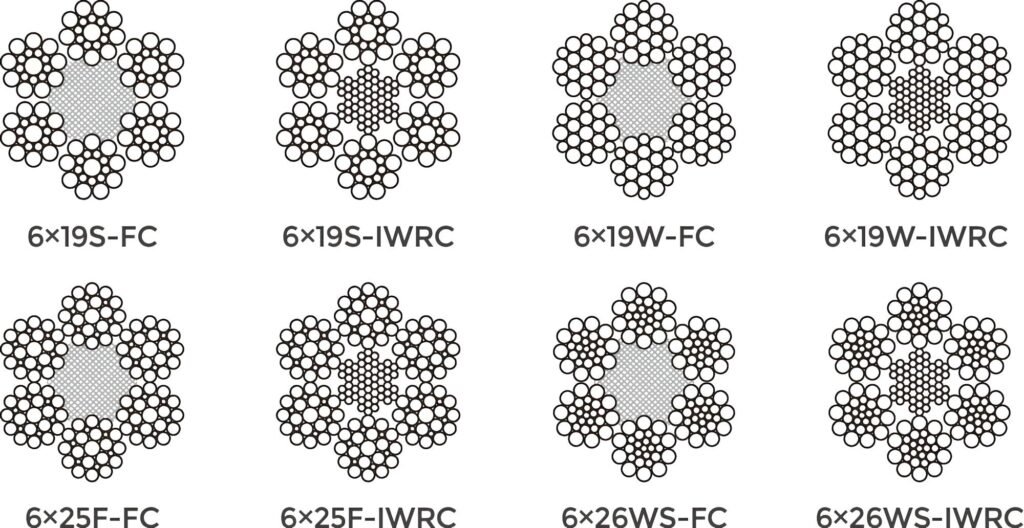
6×19 wire rope is commonly used in applications where moderate flexibility and strength are required, and where the rope won’t undergo frequent bending or high abrasion. Here are some typical uses:
-
Lifting and Rigging:
- 6×19 wire rope is often used in lifting and rigging systems for general purposes, such as in construction cranes or hoists, where the load isn’t subject to constant bending.
-
Towing and Hauling:
- Due to its moderate strength and durability, 6×19 rope is suitable for towing applications, including marine and industrial towing.
-
Winch Lines:
- It’s commonly used in winches for various vehicles, including trucks, off-road vehicles, and marine winches, where high breaking strength is required but the rope doesn’t need to be overly flexible.
-
Elevators:
- 6×19 ropes are often used in elevator systems because they provide a good balance of strength, wear resistance, and cost-effectiveness.
-
Suspension and Support Systems:
- It can also be found in suspension lines for structures or other general support systems where the rope is relatively static and not subjected to continuous bending.
-
Mining and Oil Rigs:
- 6×19 wire rope is used in the mining industry for lifting and moving heavy loads, and in oil rigs for hoisting or pulling equipment in and out of wells.
-
Fishing Lines:
- In fishing or industrial applications like dredging, 6×19 ropes can be used for pulling nets or equipment from the water.
The general use of 6×19 wire rope tends to focus on applications where moderate flexibility is beneficial but extreme bending or abrasion resistance isn’t critical.
What is iwrc wire rope?
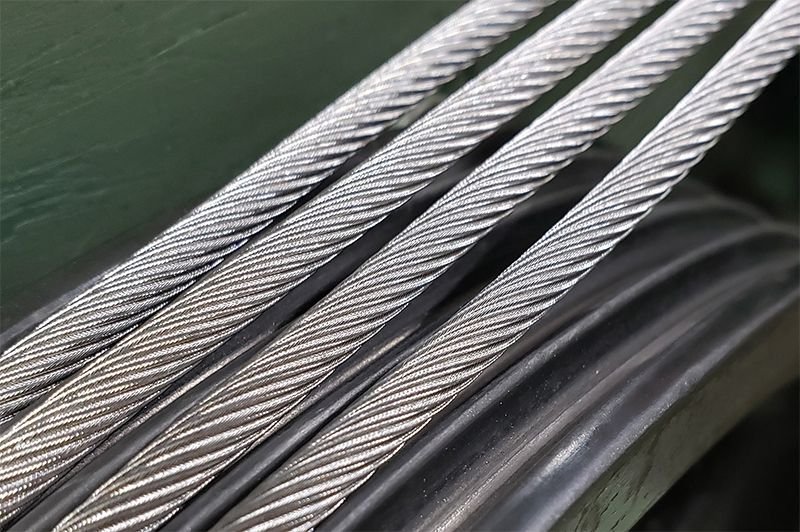
IWRC stands for Independent Wire Rope Core. IWRC wire rope is a type of steel cable composed of multiple strands of wire twisted together, with a core made of another wire rope. This design provides greater strength, durability, and resistance to crushing compared to wire ropes with a fiber core.
The independent wire rope core acts as a support structure, enhancing the overall performance of the rope, particularly in applications that require high tensile strength and resistance to deformation. IWRC wire ropes are commonly used in heavy-duty applications such as crane hoists, mining, construction, and offshore drilling.
The main advantages of IWRC wire rope include:
- Higher tensile strength: The steel core provides additional strength, allowing the rope to support heavier loads.
- Better resistance to crushing: The rigid core helps maintain the rope’s shape under pressure, reducing the risk of damage from compression.
- Improved resistance to wear and abrasion: The steel core and outer strands are more resistant to wear and tear, resulting in a longer service life.
- Enhanced resistance to heat: Steel cores are less susceptible to heat damage than fiber cores, making IWRC wire ropes suitable for use in high-temperature environments.
However, IWRC wire ropes can be less flexible than those with a fiber core, which may make them less suitable for applications requiring greater flexibility.
What is the difference between 6X36 and 6X37 wire rope?
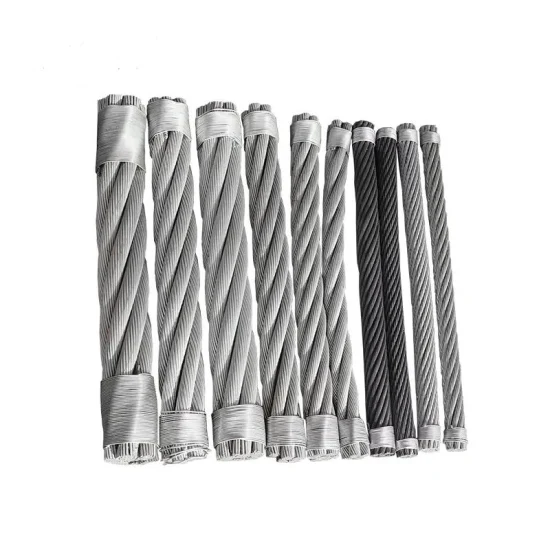
The difference between 6×36 and 6×37 wire ropes lies primarily in their construction, performance characteristics, and applications. Both are common types of wire ropes, but they are designed for different use cases based on their structural makeup. Here’s a detailed comparison:
1. Construction
6×36 Wire Rope:
Structure: 6 strands with 36 wires per strand.
Wire Arrangement: The wires in each strand are typically arranged in a more complex pattern, such as a combination of different wire sizes (e.g., a larger core wire surrounded by smaller outer wires).
Flexibility: Moderately flexible due to the higher number of wires per strand.
6×37 Wire Rope:
Structure: 6 strands with 37 wires per strand.
Wire Arrangement: The wires are usually arranged in a more uniform pattern, often with a central core wire and multiple layers of smaller wires around it.
Flexibility: More flexible than 6×36 due to the higher wire count and finer wire diameter.
2. Performance Characteristics
Property | 6×36 Wire Rope | 6×37 Wire Rope |
---|---|---|
Strength | High tensile strength, suitable for heavy loads. | Slightly lower tensile strength compared to 6×36, but still strong. |
Flexibility | Moderate flexibility, good for general-purpose use. | Higher flexibility, ideal for applications requiring frequent bending. |
Fatigue Resistance | Good fatigue resistance due to its construction. | Excellent fatigue resistance, better suited for dynamic loads. |
Abrasion Resistance | Good abrasion resistance, suitable for rough environments. | Slightly lower abrasion resistance due to finer wires. |
Crush Resistance | Better crush resistance due to thicker wires. | Less crush-resistant due to finer wires. |
3. Applications
6×36 Wire Rope:
Commonly used in general-purpose lifting, cranes, and hoisting equipment.
Suitable for mining, construction, and industrial applications where a balance of strength and flexibility is needed.
Often used in static or low-flex applications where abrasion resistance is important.
6×37 Wire Rope:
Ideal for dynamic applications requiring high flexibility, such as crane boom hoists, towing lines, and elevator cables.
Frequently used in marine environments, theater rigging, and aerial tramways where frequent bending and fatigue resistance are critical.
Better suited for smooth sheaves and drums due to its finer wire construction.
4. Key Differences Summary
Aspect | 6×36 | 6×37 |
---|---|---|
Wires per Strand | 36 wires | 37 wires |
Flexibility | Moderate | High |
Fatigue Resistance | Good | Excellent |
Abrasion Resistance | Better | Slightly lower |
Crush Resistance | Better | Lower |
Typical Use | Heavy lifting, static loads | Dynamic loads, frequent bending |
5. Choosing Between 6×36 and 6×37
Choose 6×36 if:
You need a balance of strength and abrasion resistance.
The application involves heavy loads and rough environments.
The rope will experience minimal bending or dynamic movement.
Choose 6×37 if:
High flexibility and fatigue resistance are critical.
The application involves frequent bending or dynamic loads.
The rope will run over smooth sheaves or drums.