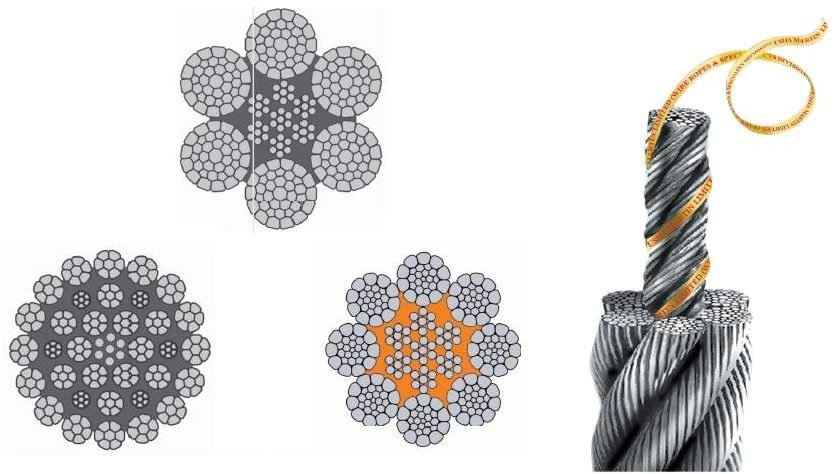
Have you ever wondered what makes a seemingly ordinary wire rope capable of bearing incredible weight? A weak wire rope can lead to disaster. Understanding these factors is crucial for safety.
The strength of a wire rope is influenced by several core factors, including its material, construction, manufacturing process, core type, and post-treatment. These elements together determine its load capacity and durability.
My name is Jessica Cheng. I have worked in the wire rope industry for a long time. I have seen many ropes. Some ropes are very strong. Some ropes are weak. This difference is not by chance. There is a lot of design and manufacturing knowledge behind it.
[Table of contents]
How Do Wire Rope Materials Affect Its Strength?
The material of a wire rope is the foundation of its strength. Different materials have different strengths. Choosing the right material is essential.
A wire rope’s strength primarily depends on the steel wire material used. High-carbon steel is commonly used for high-strength wire ropes. Alloy steel can offer additional performance.
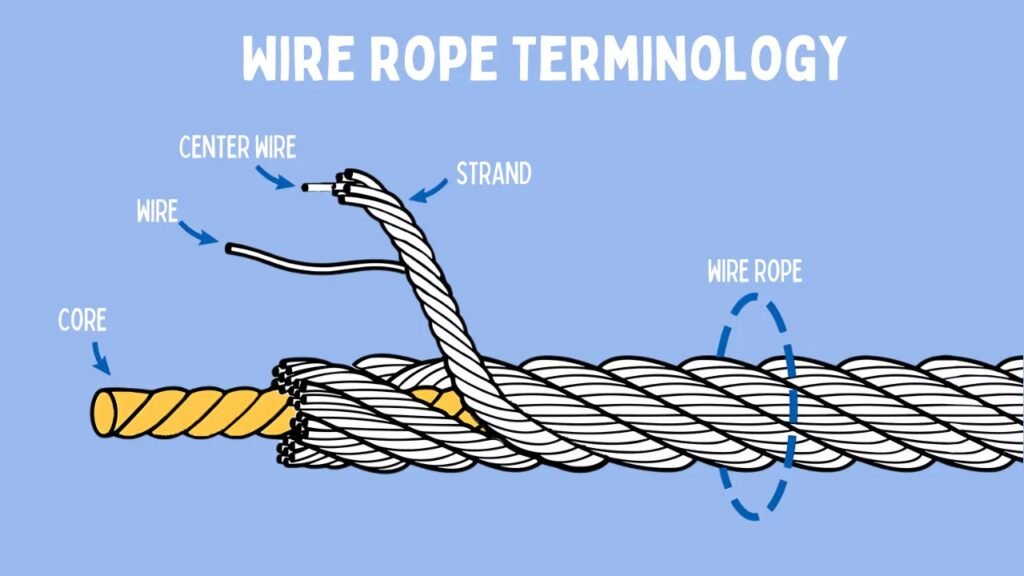
When producing wire rope, we need to consider various materials. It is not a simple choice.
Carbon Steel vs. Alloy Steel Choices
- Carbon Steel: This is a common choice. It is cost-effective. It also has high strength. However, carbon steel may rust in some harsh environments. For example, marine environments. We supply this rope to customers in Singapore and Vietnam. They like this rope very much.
- Alloy Steel: This material contains added elements. For example, chromium and nickel. This increases strength. It also increases corrosion resistance. For Maksim in Russia, we sometimes recommend this rope. This is because they have very high-quality requirements.
Material Characteristics
- Tensile Strength: This is the material’s ability to resist tension. High tensile strength means the material is very tough.
- Ductility: This is the material’s ability to stretch before breaking. Good ductility means the rope will not break suddenly. It will deform. This gives us a warning.
- Corrosion Resistance: This is important if the rope works in a wet environment. Stainless steel wire rope is the best choice for corrosion resistance. We supply this rope to marine customers.
How Does Wire Rope Construction Affect Its Strength?
The construction of a wire rope is like the framework of a house. It determines the overall power of the rope. Every steel wire is important.
Wire rope strength largely depends on its number of strands, the number of wires per strand, and their arrangement. Spiral and parallel lay are two common constructions. These constructions affect the rope’s flexibility and resistance to crushing.
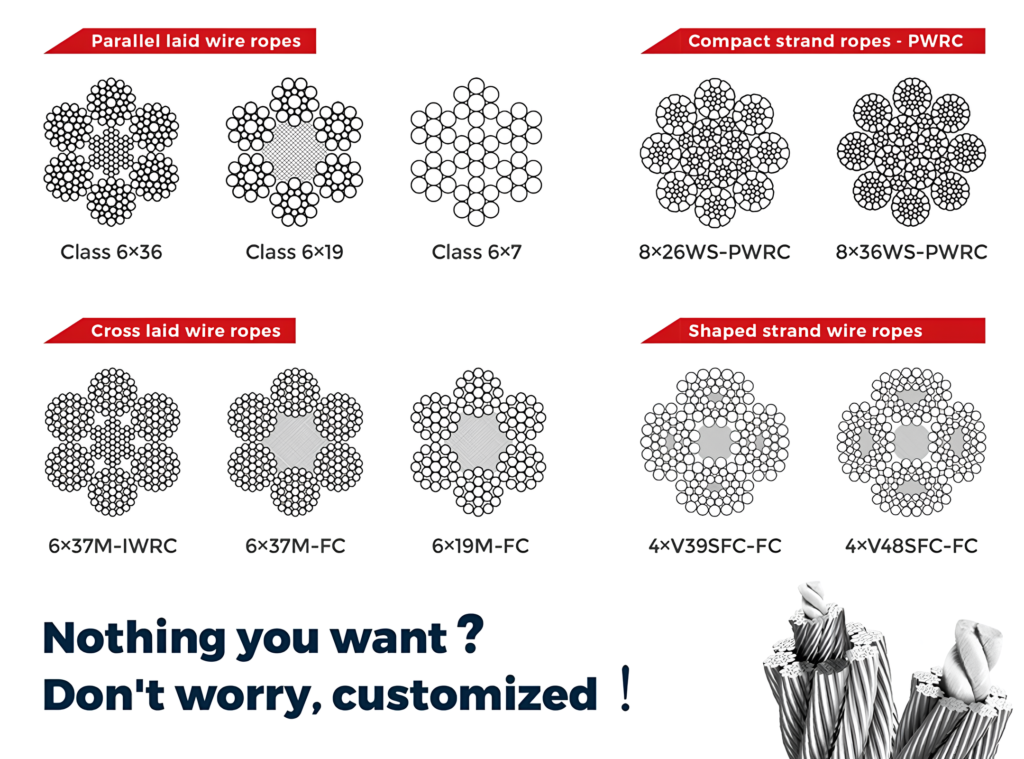
The construction of a wire rope is very complex. It is not simply twisting wires together.
Types of Strands
- Regular Lay: The wires in the strand run in the opposite direction to the lay of the strand itself. This construction is very stable. It is suitable for many uses.
- Lang Lay: The wires in the strand run in the same direction as the lay of the strand itself. This construction is more wear-resistant. It is more flexible. However, it is easier to unravel. It requires more careful installation.
- Sealed Strand: Wires are tightly packed in layers. This forms a smooth surface. This rope is very dense. It has high strength. It is also more wear-resistant.
Core Selection
- Fiber Core: For example, natural or synthetic fibers. It provides flexibility. It can store lubricant. However, its strength is not as high as a steel core.
- Steel Core: Usually an independent wire rope. It provides higher strength. It is also more resistant to crushing. For crane and mining applications, a steel core is more common. For example, we supply this rope to customers in Australia and Canada.
Impact of Construction on Strength
- Rotation Resistance: Some constructions can reduce the rope’s rotation under load. This is important for lifting applications.
- Lateral Stability: Good construction maintains the rope’s shape. This is true even under heavy loads.
How Do Wire Rope Manufacturing Process and Post-Treatment Affect Its Strength?
This is not simple assembly. Every step in the manufacturing process is important. Correct treatment can significantly improve wire rope performance.
Wire rope strength is also influenced by the manufacturing process. For example, the laying method and tension control. In addition, post-treatments like lubrication, galvanization, or plastic coating can enhance its durability and corrosion resistance.
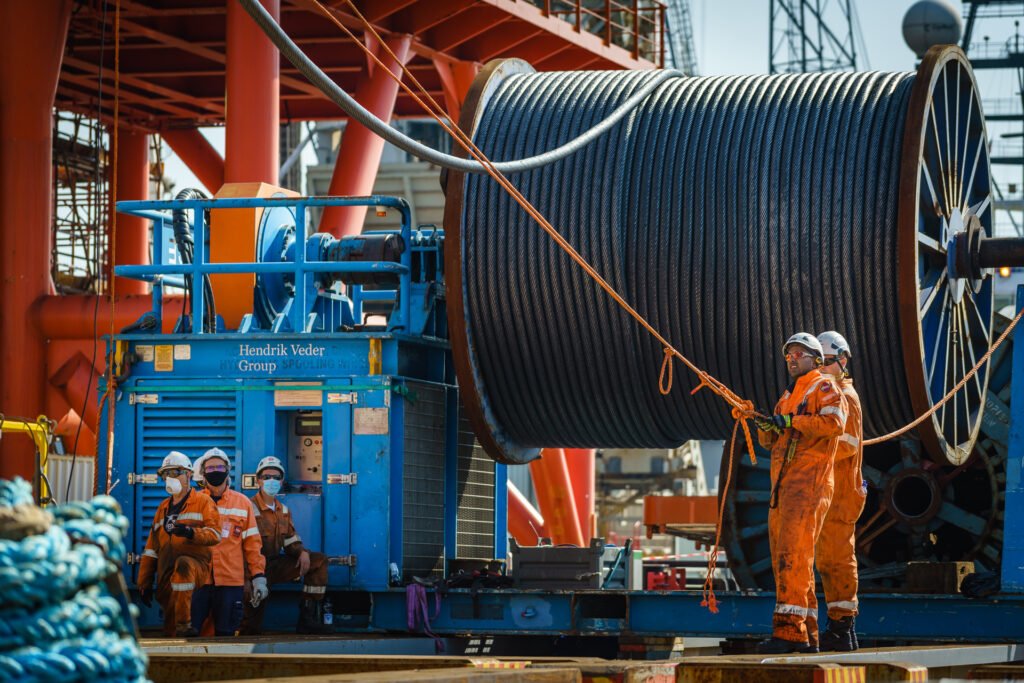
Our factory has 4 production lines. This allows us to control every step of manufacturing well.
Manufacturing Process
- Wire Drawing: This ensures each wire’s diameter is uniform. It also ensures its strength meets standards.
- Stranding and Laying: Wires are twisted into strands. Then strands are twisted into rope. Tension control during this process is key. If tension is uneven, the rope’s strength will be compromised. Our ropes fully comply with EN12385-4 standards.
- Pre-stretching: The rope is pre-stretched before leaving the factory. This can eliminate internal stresses. This increases the rope’s stability. It also improves its breaking load.
Post-Treatment
- Lubrication: The rope is lubricated. This reduces internal friction. It also prevents corrosion. The choice of lubricant is important.
- Galvanization: A layer of zinc is coated on the wire surface. This significantly improves corrosion resistance. We supply this rope to customers in the Middle East. This is because the climate there is humid.
- Plastic Coating: A layer of plastic is applied to the outside of the rope. It protects the rope from external damage. It also prevents moisture from entering.
- Heat Treatment: Some ropes undergo heat treatment. This can increase their strength. It also increases their toughness.
How Do Wire Rope Maintenance and Usage Conditions Affect Its Strength?
Even the best wire rope needs proper maintenance. The use environment also directly affects its lifespan.
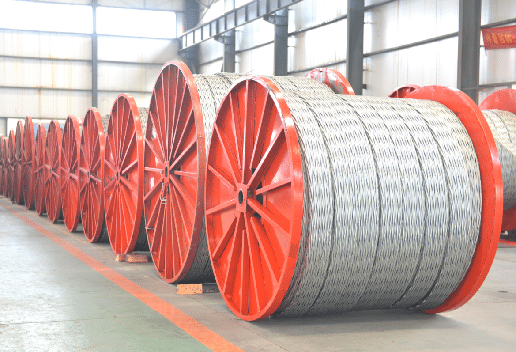
The lifespan of a wire rope does not only depend on manufacturing quality. It also depends on how the user handles it.
Regular Inspection
- Wear: Check the rope surface for wear.
- Broken Wires: Check for any broken steel wires.
- Corrosion: Check for rust.
- Deformation: Check if the rope is twisted or flattened.
If Maksim’s team can inspect regularly, they can manage their inventory well.
Lubrication
- Maintain Lubrication: Lubrication reduces internal friction. It also prevents corrosion.
Environmental Impact on Usage
- Temperature: Extreme temperatures can affect rope performance.
- Chemicals: Exposure to corrosive chemicals can damage the rope.
- Shock Loads: Sudden impacts can exceed the rope’s limits. This is true even if it has a high breaking load.
Conclusion
Wire rope strength is a complex topic. It is determined by its material, construction, manufacturing process, post-treatment, and maintenance.