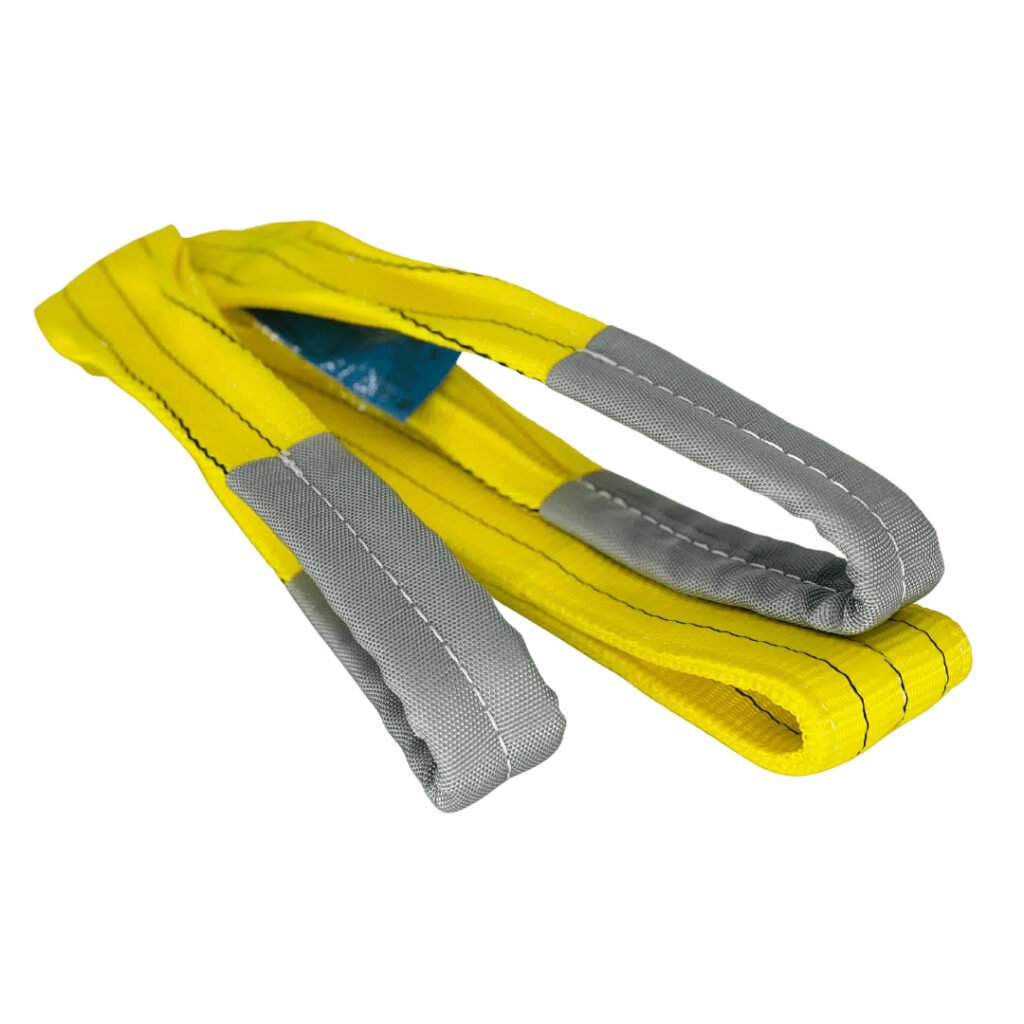
Are you tired of heavy lifting being a nightmare? Do you fear damage during transport? Webbing slings could be your simple, strong solution.
Webbing slings are flat, flexible lifting devices made from synthetic fibers. They lift and move loads safely and efficiently across many industries.
Let me tell you about my friend, Andri. He used to struggle with heavy loads. But then he found a better way. I helped him discover the power of proper lifting tools.
What materials are webbing slings made from?
Are you curious about what makes these slings so strong? It all comes down to the materials.
Webbing slings are typically made from polyester, nylon, or sometimes polypropylene. Each material has unique strengths for different lifting needs.
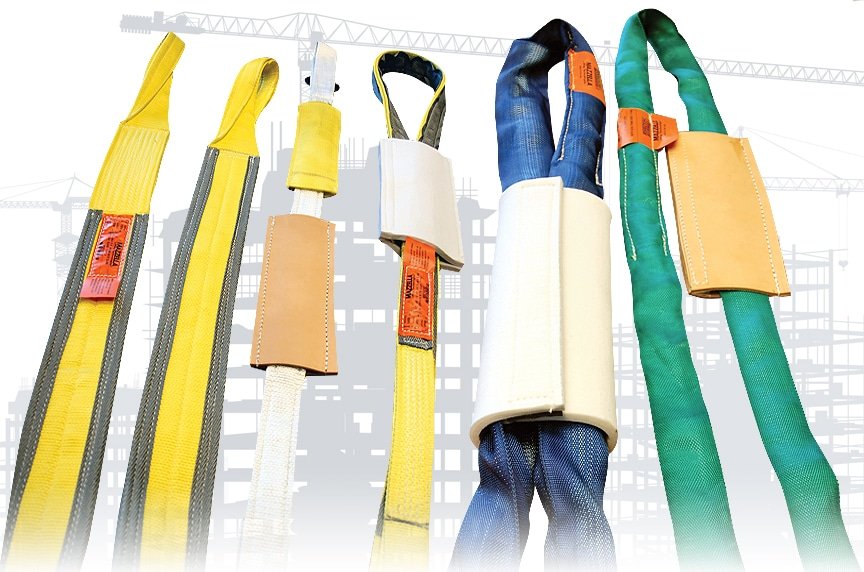
Dive Deeper: When choosing a webbing sling, the material is key. Polyester is popular for its high strength-to-weight ratio and low stretch. It handles chemicals well, except for strong alkalis. Nylon offers good elasticity and abrasion resistance. However, it can lose strength when wet. Polypropylene is lighter and floats on water, making it suitable for marine environments. It resists certain chemicals that polyester and nylon do not. Understanding these differences helps ensure safe and effective use.
Material Properties
Material | Key Feature | Chemical Resistance | Water Absorption | Elongation |
---|---|---|---|---|
Polyester | High Strength | Resistant to most acids, not strong alkalis | Low | Low |
Nylon | Good Elasticity | Resistant to alkalis, not strong acids | High | Moderate |
Polypropylene | Lightweight, Floats | Resistant to most acids and alkalis | Very Low | High |
What are the common types of webbing slings?
Do you need a sling but don’t know which type? There are several options available.
Common types include flat woven slings, endless slings, and round slings. Each type offers specific advantages for different lifting applications.
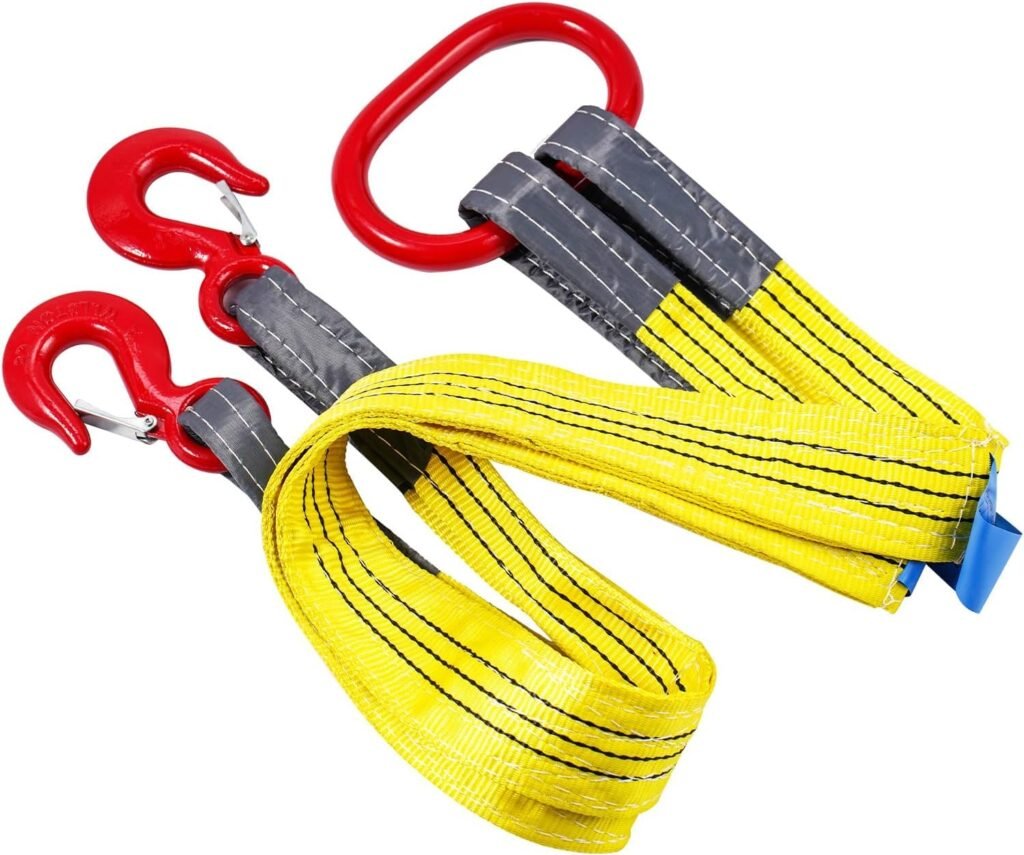
Dive Deeper: Flat woven slings are versatile. They have stitched eyes or loops on each end. This makes them easy to attach to hooks. Endless slings are continuous loops of webbing. They are often used for choking or basket hitches. This allows for even wear and extended life. Round slings consist of a continuous bundle of polyester fibers protected by a woven cover. They are very flexible and can conform to odd shapes. This reduces damage to loads. Choosing the correct type is vital for safety and efficiency.
Sling Types and Uses
Sling Type | Description | Typical Use | Advantages |
---|---|---|---|
Flat Woven Sling | Flat web with reinforced eyes at ends | General purpose lifting, choker or basket hitches | Versatile, easy to attach |
Endless Sling | Continuous loop of webbing | Choking, basket, or vertical hitches | Even wear, longer life |
Round Sling | Continuous bundle of fibers in a protective cover | Lifting delicate loads, odd shapes, heavy loads | Flexible, won’t damage load, high capacity |
What are the advantages of using webbing slings?
Are you wondering why so many industries choose webbing slings? Their benefits are clear.
Webbing slings offer several advantages. They are lightweight, flexible, and non-marring. They also provide high strength and are less likely to damage delicate loads.
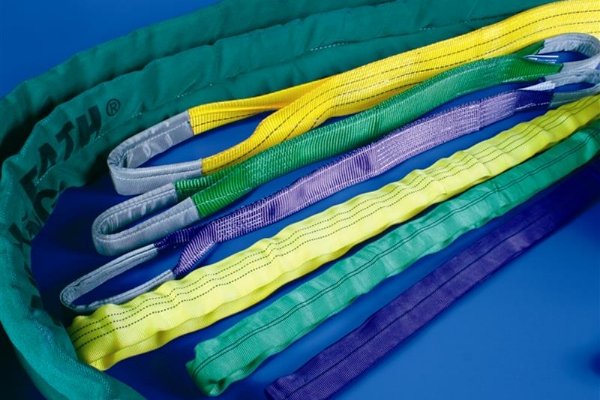
Dive Deeper: The lightweight nature of webbing slings makes them easy to handle. This reduces operator fatigue. Their flexibility allows them to conform to irregular shapes. This provides a secure grip. Unlike chains or wire ropes, they are less likely to scratch or dent finished surfaces. This is a critical factor when handling painted or polished items. Webbing slings are also safer. They show signs of wear more readily than other lifting gear. This allows for timely replacement. This helps prevent accidents.
Advantages Breakdown
Advantage | Benefit | Impact on Operation |
---|---|---|
Lightweight | Easy to carry, set up, and store | Reduces worker strain, improves efficiency |
Flexible | Conforms to load shape, distributes weight evenly | Secure grip, less load shifting |
Non-marring | Won’t scratch or damage delicate surfaces | Protects valuable goods, reduces repair costs |
Visible Wear | Signs of damage (cuts, tears) are easy to spot | Improves safety, enables timely replacement |
Cost-effective | Generally less expensive than metal alternatives | Reduces initial investment, lowers operational costs |
What are the proper ways to maintain webbing slings?
Do you want your webbing slings to last? Proper care is essential.
Maintaining webbing slings involves regular inspection, proper cleaning, and correct storage. This ensures their longevity and safe operation.
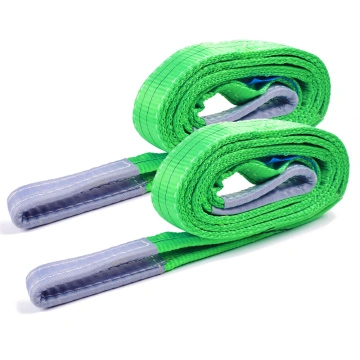
Dive Deeper: Inspections should happen before each use. Look for cuts, abrasions, snags, or chemical damage. Check for heat damage or melted fibers. Any visible damage means the sling should be removed from service. Cleaning slings involves using mild soap and water. Then, allow them to air dry completely. Never use harsh chemicals or strong detergents. Store slings in a cool, dry place away from direct sunlight and sharp edges. Proper maintenance extends the life of the sling. It also prevents dangerous failures.
Maintenance Checklist
Action | Frequency | Details |
---|---|---|
Visual Check | Before each use | Look for cuts, tears, abrasions, snags, chemical exposure, heat damage. |
Thorough Inspection | Annually or more frequently | Detailed check by a qualified person for hidden damage, stitching integrity. |
Cleaning | As needed | Mild soap and water, air dry completely. Avoid harsh chemicals. |
Storage | Always | Store in a cool, dry, dark place on racks. Avoid direct sunlight and sharp edges. |
Record Keeping | After inspection/repair | Document inspection dates, findings, and any repairs or retirements. |
Conclusion
Webbing slings are vital for safe lifting. They are strong, flexible, and protect loads. Regular care keeps them working well.