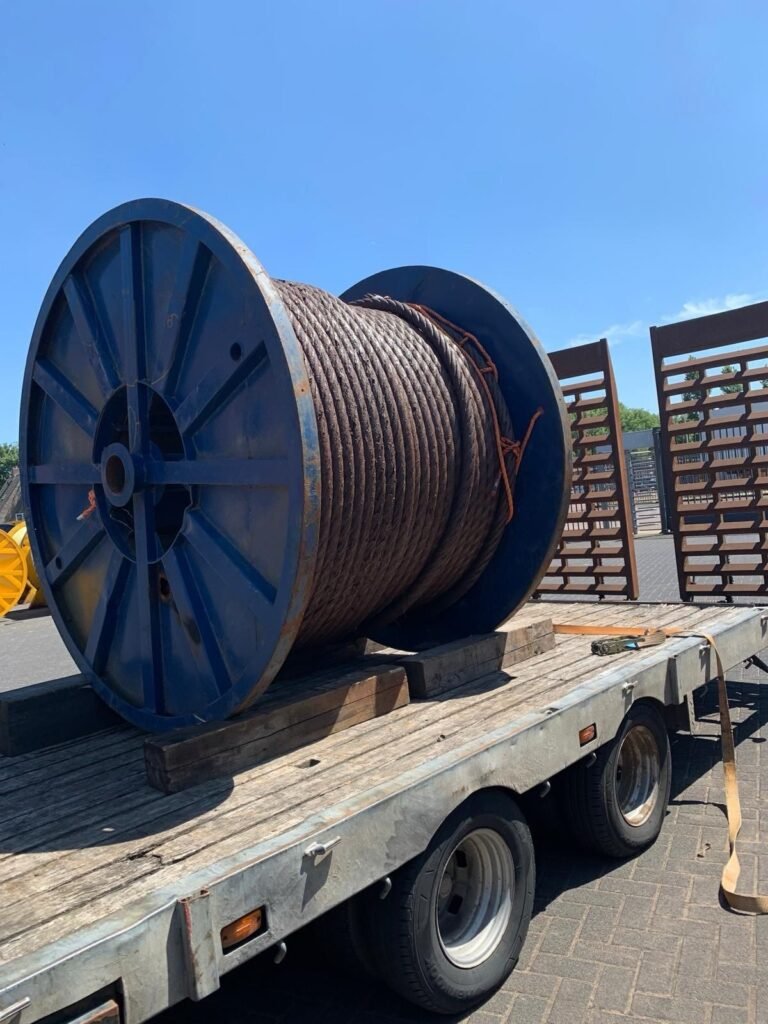
Is your current rope giving up when you need it most? Facing unexpected breaks on critical jobs? Don’t let weak ropes put your project at risk.
Yes, the strength of a rope significantly depends on its diameter. A greater diameter generally means a stronger rope, as it contains more material to bear the load.
Let me tell you, I’ve seen countless jobs where the right rope made all the difference. Choosing the wrong one, even by a millimeter, can lead to disaster. Stick with me, and I’ll explain why this matters for your work.
Does a thicker rope mean higher breaking load?
Choosing the right rope means understanding how size affects strength. It’s not just about looks. Do you know how rope thickness impacts its breaking load?
Yes, a thicker rope usually has a higher breaking load. This is because a larger diameter provides more material cross-section, allowing it to withstand greater force before breaking.
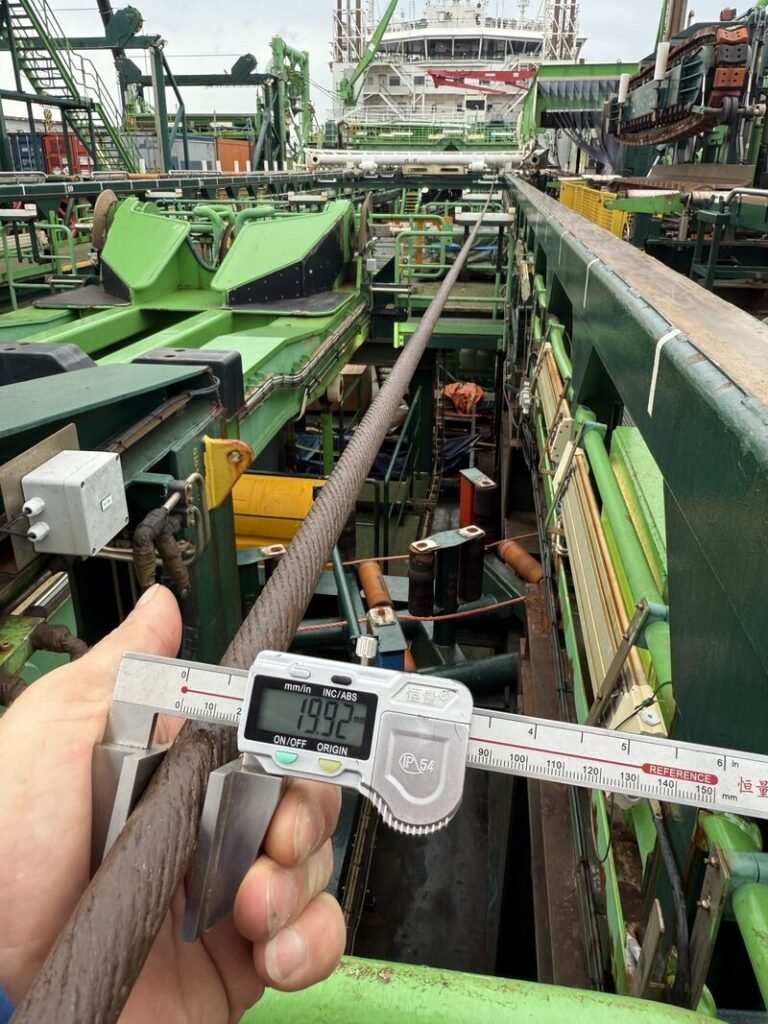
When we talk about the breaking load of a rope, we’re discussing the maximum force it can withstand before failing. For us, this is a critical number. Think about a crane lifting a heavy load. If the rope isn’t strong enough, it fails. We’ve seen this happen when the wrong rope is used.
Why does more material equal more strength?
Imagine two ropes made from the same material. One is thin like a pencil, the other thick like your arm.
- More Fibers: A thicker rope has more individual fibers or wires within its structure. Each fiber adds to the overall strength.
- Distributed Stress: When force is applied, the stress is spread out over a larger area. This means no single point takes too much strain.
- Reduced Concentration: A larger cross-section means fewer weak points are likely to be heavily loaded.
Rope Type | Diameter (mm) | Typical Breaking Load (kN) |
---|---|---|
Standard Steel | 6 | 25 |
Standard Steel | 10 | 65 |
Standard Steel | 20 | 250 |
These numbers are general. Real-world values depend on material and construction.
Are there exceptions to this rule?
While diameter is key, it’s not the only factor. You can’t just pick the thickest rope and call it a day.
- Material Quality: A high-quality steel wire rope with a smaller diameter can be stronger than a low-quality, larger-diameter synthetic rope. We focus on high-quality materials, like EN12385-4 compliant wire, to ensure our ropes perform.
- Construction Type: How the rope is twisted or laid can affect its strength. A specialized assembly might make a thinner rope stronger.
- Core Type: For wire ropes, the core material, like a steel core or a fiber core, impacts strength. A plastic impregnated core can add durability.
- Galvanization: Galvanized wire rope resists corrosion, which maintains strength over time. Corrosion can weaken a rope, regardless of its original diameter.
Factor | Impact on Strength | Example |
---|---|---|
Material Quality | High-grade materials lead to higher strength per diameter. | Imported steel vs. recycled scrap |
Construction | Specific lays or braids can optimize strength. | 6×19 vs. 6×36 construction |
Core Type | Steel cores offer more strength than fiber cores. | IWRC (Independent Wire Rope Core) vs. Fiber Core |
Surface Treatment | Galvanized ropes maintain strength longer. | Bare wire rope vs. galvanized wire rope |
Understanding these details helps us provide the exact rope your projects need.
Does wire rope construction type affect strength more than diameter?
It’s common to focus on size, but how a rope is built is also vital. Does the way a wire rope is constructed impact its strength more than its diameter?
No, wire rope construction type does not affect strength more than diameter. Both are crucial factors. Diameter provides the fundamental material mass, while construction optimizes how that material bears load and enhances specific properties like flexibility or abrasion resistance.
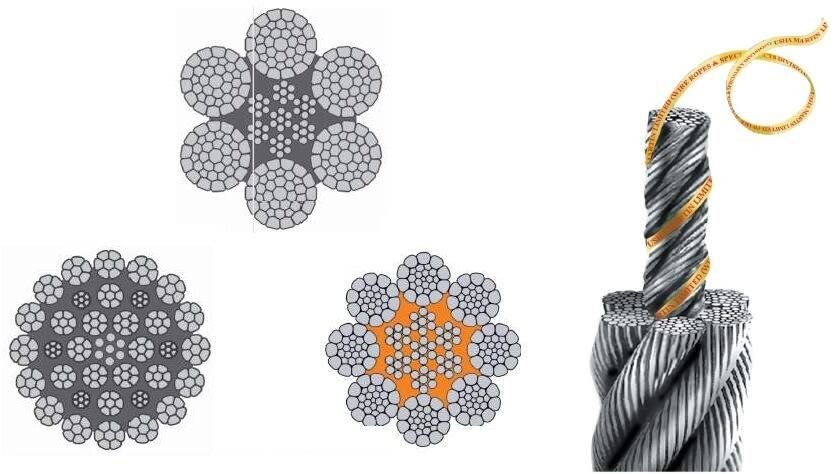
When we talk about ‘construction type,’ we mean things like the number of strands, the number of wires in each strand, and how they are laid together. This design choice influences how the rope behaves under stress, how flexible it is, and its resistance to fatigue. For example, a 6×36 construction is more flexible than a 6×19.
What are common wire rope constructions?
Different jobs need different ropes. Here are some common constructions we deal with:
- 6×19 Class: This class includes various constructions like 6x19S (Seale), 6x25FW (Filler Wire), and 6x26WS (Warrington Seale). These are known for a good balance of flexibility and abrasion resistance. They are widely used for general purposes.
- 6×36 Class: This class, like 6x36WS and 6x41WS, offers greater flexibility than the 6×19 class. It’s often used in applications requiring frequent bending over sheaves, such as crane wire rope.
- 19×7 and 35×7 (Rotation Resistant): These ropes are designed to resist rotation under load. This is important for single-part lines where load spinning is a concern, like on mobile cranes.
- Compacted Ropes: These ropes have strands that are drawn through a die. This compacts the steel, increasing the metallic cross-section. The result is a rope with a higher breaking load for its diameter, and better abrasion resistance. We provide these for high-performance needs.
Construction Type | Primary Benefit | Typical Application | Relative Flexibility |
---|---|---|---|
6×19 Seale (S) | Abrasion resistance | Winch lines, general hoisting | Medium |
6×36 Warrington Seale | Flexibility | Crane ropes, elevator wire rope | High |
19×7 Rotation Resistant | Non-rotating | Single-part crane lines | High |
Compacted | High breaking strength | Heavy lifting, demanding applications | Medium to High |
Each construction solves a specific problem. Knowing them helps us recommend the right product.
How does proper rope selection impact project safety and longevity?
Choosing the right rope, factoring in both diameter and construction, is about more than just strength. It’s about safety and long-term performance.
- Preventing Accidents: A rope that is too small or the wrong construction for the load can fail catastrophically. This puts lives and equipment at risk. Our ropes can come with BV, CE, RMRS, DNV, and ABS certificates. This gives buyers peace of mind.
- Extending Service Life: The right rope for the job lasts longer. It resists wear, fatigue, and kinking better. This means less downtime and fewer replacements, saving money in the long run. We know our products are used in tough environments, like mining wire rope applications.
- Optimizing Performance: A rope with the correct flexibility for sheaves, for example, will operate more smoothly and efficiently. This improves productivity. Think about an elevator wire rope; smooth operation is key.
- Compliance: Many industries have standards, like EN12385-4. Using compliant ropes ensures you meet these safety requirements. This is critical for export to countries like Singapore, Australia, or Russia.
We understand these concerns. We’ve built our factory with 4 production lines to meet high quality and tensile strength needs. Our goal is to provide solutions that work safely, day in and day out.
What is the best way to choose the right diameter for specialized applications?
You’ve learned that diameter is vital, and construction matters. But how do you put this into practice for specific jobs? What is the best way to choose the right diameter for specialized applications?
The best way to choose the right diameter for specialized applications is to consult industry standards, product specifications, and application-specific engineering data, always factoring in the required working load limit and safety margins.
When I talk to clients, especially those with demanding needs like marine wire rope or specialized assemblies, it’s never a one-size-fits-all answer. We have to dive deep into the specific details of their operations.
What specifications should I check when choosing rope diameter?
When you’re looking at ropes, there are several key specifications to consider beyond just the visible thickness.
- Working Load Limit (WLL): This is the maximum load a rope should ever carry in normal use. It’s often a fraction of the breaking load, typically 1/5 or 1/6, to ensure a good safety margin. Always respect the WLL.
- Minimum Breaking Force (MBF): This is the guaranteed minimum load at which a new rope will break. This is an important number for comparing ropes. Our products boast high breaking load capabilities.
- Material Grade: Is it standard steel, high-tensile steel, or stainless steel wire rope? Each has different strength characteristics for the same diameter. Stainless steel is often for corrosion resistance.
- Certification: Does the rope come with certifications like BV, CE, RMRS, DNV, or ABS? These prove the rope meets certain standards and has been tested. This is especially important for marine or offshore applications.
Specification | Description | Importance |
---|---|---|
Working Load Limit | Maximum safe load for daily use | Prevents overloading and ensures safety |
Minimum Breaking Force | Guaranteed minimum breaking strength | Direct measure of strength, for design calculation |
Material Grade | Type of steel or fiber used | Dictates inherent strength and durability |
Certification | Third-party verification of quality and standards | Ensures compliance and reliability |
Checking these thoroughly helps avoid costly mistakes.
How do I account for environmental factors and extreme conditions?
Ropes don’t always operate in perfect conditions. Real-world environments, especially for mining or marine use, can be harsh. You must factor these in when choosing a diameter.
- Corrosion: In salty air, water, or chemical environments, standard steel can corrode quickly, weakening the rope. Galvanized wire rope or stainless steel wire rope is essential here. Plastic impregnated options also help.
- Temperature Extremes: Very high or very low temperatures can affect the strength and flexibility of rope materials.
- Abrasions: If the rope will rub against rough surfaces, a thicker, more abrasion-resistant construction might be needed. This is common in mining where contact with rocks is possible.
- Fatigue: Repeated bending and unbending, like on a crane, causes fatigue. A more flexible construction (often with a larger diameter for the same strength) can extend life.
For example, when dealing with clients for piling tools, we know the ropes will face immense stress and potentially harsh ground conditions. We need to account for these variables when advising on diameter and type. We export to countries with diverse climates like Russia and Saudi Arabia, so knowing environmental impacts is essential.
How can I ensure the ropes I buy are genuinely high quality?
After all this talk about diameter and construction, you need to be sure the rope you get is actually what’s advertised. How can you ensure the ropes you buy are genuinely high quality?
To ensure ropes are genuinely high quality, verify their certifications (like BV, CE, RMRS, DNV, ABS), request material test reports, ensure compliance with standards like EN12385-4, and choose a manufacturer with a proven track record and transparent production.
When I first started sourcing product, realizing the difference between advertised quality and actual quality was a huge lesson. Our factory in China specializes in high-quality wire ropes. We want to be transparent with you.
What quality certifications should I look for?
Certifications are your best friend when buying wire ropes. They speak volumes about a manufacturer’s commitment to quality.
- BV (Bureau Veritas): A global leader in testing, inspection, and certification. Strong for marine applications.
- CE (Conformité Européenne): Indicates conformity with health, safety, and environmental protection standards for products sold within the European Economic Area. Key for European markets.
- RMRS (Russian Maritime Register of Shipping): Important for ships and marine structures in Russia and surrounding areas.
- DNV (Det Norske Veritas): A leading classification society for the maritime industry, focusing on safety and sustainability.
- ABS (American Bureau of Shipping): Another major classification society, primarily for marine and offshore assets.
We can provide these certificates if our clients need them. This is proof our ropes meet rigorous international standards. A reputable supplier will have these ready.
Why is compliance with standards like EN12385-4 important?
Compliance with specific industry standards, like EN12385-4, is not just a formality. It’s a guarantee of a certain baseline quality and performance.
- Safety Assurance: Standards set minimum requirements for material, manufacturing process, and performance. This helps ensure the rope is safe for its intended use.
- Interchangeability: If a rope meets a standard, you can be reasonably sure it will perform similarly to another rope meeting the same standard, even from a different manufacturer.
- Legal Compliance: In many countries, using compliant equipment is a legal requirement, especially in industries like construction, mining, or marine.
- Reliability: Ropes made to a standard are more predictable in their performance. This reduces unexpected failures.
EN12385-4 specifically covers steel wire ropes for general lifting applications. It dictates things like tensile strength, minimum breaking force, and construction types. We build our ropes to meet these demands.
What should I look for in a reputable supplier?
Choosing the right supplier is as important as choosing the right rope. Here’s what I recommend you consider:
- Experience and Track Record: How long have they been in business? What kind of clients do they serve? We have been exporting to Singapore, Indonesia, Vietnam, Saudi Arabia, UAE, Russia, Australia, Canada, and other countries for years.
- Manufacturing Capability: Do they have their own factory? How many production lines? This indicates control over quality. We have 4 production lines.
- Transparency: Are they open about their production process, testing, and certifications? Do they offer factory visits or audit reports?
- Customization: Can they provide customized requests, like custom logos or specialized assemblies? This shows flexibility and expertise.
- Customer Service and Technical Support: Can they answer your technical questions? Do they offer support for product selection? We pride ourselves on proactive client development.
We believe in building long-term relationships. That means not just selling a product, but providing confidence in its quality.
Conclusion
Yes, a rope’s strength clearly depends on its diameter. But remember, construction type, material quality, and certifications are also critical. Choosing the right rope means looking at the whole picture for safety and success.