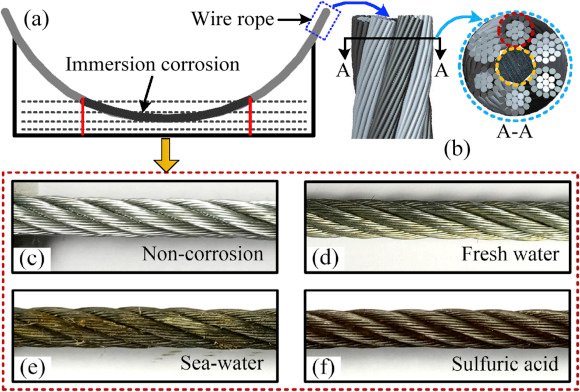
Is your wire rope showing signs of rust? This problem can lead to serious safety issues. Learning about corrosion is important for extending the life of your wire rope.
Wire rope corrosion happens when metal reacts with its environment. This reaction weakens the rope over time. Proper prevention methods can stop this damage.
I once had a client, a procurement manager, who faced sudden rust problems. He thought he bought the best ropes. But something was wrong. This made me think deeply about how wire ropes get damaged.
What Environmental Factors Cause Wire Rope Corrosion?
The environment plays a big role in wire rope corrosion. Many things around us can harm wire ropes. Understanding them helps us protect our ropes better.
Environmental factors like moisture, salt, and chemicals are main causes of wire rope corrosion. These elements speed up the breakdown of metal.
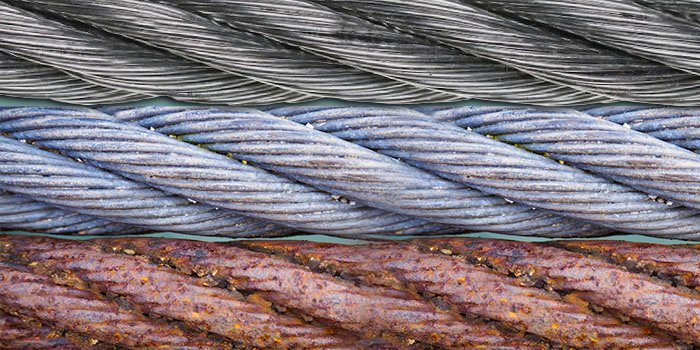
When we talk about the environment, it’s not just rain. It’s much more.
Dive Deeper: Understanding Environmental Corrosives
- Moisture and Humidity: Water is a common enemy. High humidity means more water vapor in the air. This water sticks to the metal surface. It allows oxygen to react with the iron in the steel. This forms rust. Even small amounts of moisture can start this process.
- How it works: Water acts as an electrolyte. It helps ions move. This speeds up the corrosion process.
- Example: Ropes used in coastal areas or near rivers face high humidity. They rust faster.
- Salt Exposure: Salt is very corrosive. It speeds up the corrosion process. This is why marine environments are so harsh. Saltwater contains chloride ions. These ions break down the protective oxide layer on steel.
- Marine environments: Ships, offshore platforms, and port cranes use wire ropes. These ropes are always exposed to saltwater. This makes them highly prone to corrosion.
- Road salt: Even road salt used for de-icing can cause problems. If wire ropes are used near roads, this salt can splash onto them.
- Chemicals and Acids: Many industries use chemicals. These chemicals can be very acidic or alkaline. If wire ropes come into contact with them, they corrode quickly.
- Industrial settings: Factories might have fumes or spills containing corrosive chemicals. Mining operations also expose ropes to harsh ground chemicals.
- Types of chemicals: Sulfuric acid, hydrochloric acid, and even strong cleaning agents can harm wire ropes. It’s important to know what chemicals are present in the work area.
- Temperature Variations: Extreme temperature changes can also make corrosion worse. When temperatures go up and down quickly, condensation can form. This brings moisture to the rope surface.
- Thermal cycling: This process involves heating and cooling. It can create tiny cracks in the metal. These cracks become entry points for corrosive elements.
- High temperatures: Some chemical reactions speed up at higher temperatures. This means corrosion can happen faster when it’s hot.
Environmental Factor | Impact on Wire Rope | Common Locations |
---|---|---|
Moisture & Humidity | Rust formation | Coasts, Humid Climates |
Salt Exposure | Rapid corrosion | Marine, Coastal, Roads (winter) |
Chemicals & Acids | Metal degradation | Industrial, Mining |
Temperature Changes | Condensation, Cracks | Any outdoor environment with daily temp shifts |
How Does Poor Storage and Handling Affect Wire Rope Longevity?
Even when a wire rope is not in use, it can still be damaged. How we store and handle it makes a big difference. Improper care can shorten its life.
Poor storage and rough handling directly lead to early wire rope corrosion. Storing ropes in damp places or dropping them causes damage.
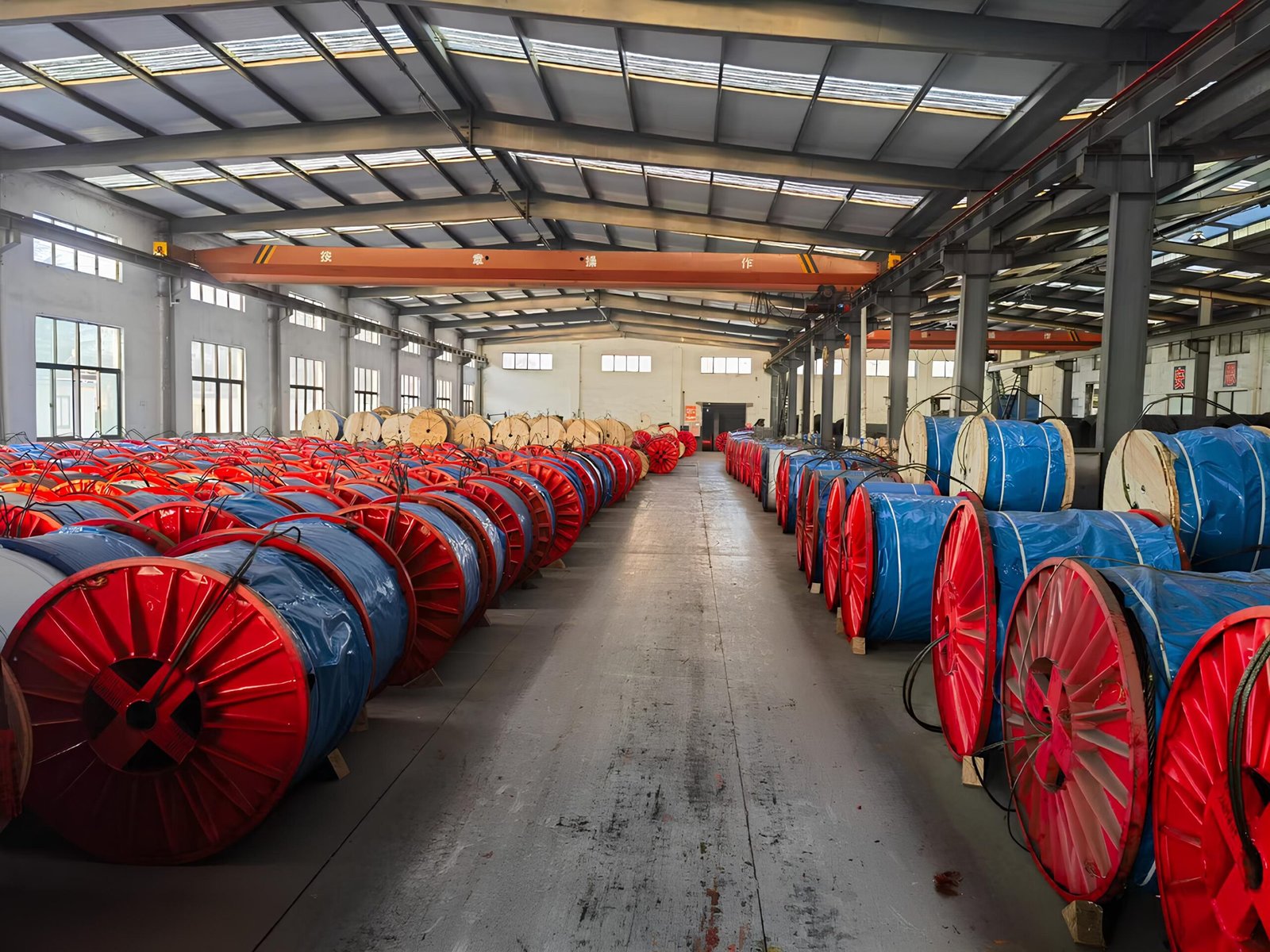
I always tell my clients, “A good wire rope needs good care.” It begins even before it’s used.
Dive Deeper: Storage and Handling Best Practices
- Damp or Wet Storage Areas: Storing wire ropes in places with high moisture or direct water can start corrosion quickly. Water on the rope allows rust to form.
- Warehouses: Even warehouses can be humid. If not climate-controlled, they can cause problems.
- Outdoor storage: Storing ropes outside directly exposes them to rain, snow, and dew. This is a very bad idea.
- Lack of Proper Lubrication During Storage: Lubrication is key. It forms a barrier against moisture and air. If a wire rope is stored without enough lubricant, it becomes vulnerable.
- Manufacturer’s lube: Ropes usually come pre-lubricated. But this protection can wear off over time.
- Re-lubrication: For long-term storage, ropes should be re-lubricated periodically. This renews the protective layer.
- Physical Damage from Rough Handling: Dropping or dragging wire ropes can cause nicks and cuts. These small damages expose the inner wires. Once exposed, they are easier targets for corrosion.
- Impact damage: When a heavy object hits the rope, it can bruise the wires. This weakens the rope and breaks surface protection.
- Abrasion: Dragging ropes over rough surfaces scratches them. This removes the outer layer of wires. It also removes any protective coatings.
Bad Practice | Consequence | Prevention Strategy |
---|---|---|
Damp Storage | Rust, pitting | Store in dry, controlled environment |
No Lubrication | Inner wire corrosion | Re-lubricate regularly |
Rough Handling | Nicks, exposed wires | Use proper lifting gear, avoid dragging |
Why Does Improper Maintenance Lead to Wire Rope Failure?
Maintenance is not just about fixing things when they break. It is about preventing problems. If we do not maintain wire ropes correctly, they will fail sooner.
Improper maintenance, like rare inspections or missed lubrication, directly causes wire rope failure. Neglecting these steps allows corrosion and wear to worsen.
Regular checks are like health check-ups for your wire ropes. Skipping them is risky.
Dive Deeper: The Impact of Neglected Maintenance
- Infrequent or No Inspections: You cannot fix what you do not see. Regular inspections help catch early signs of corrosion or wear. If you do not inspect, small problems become big ones.
- Visual checks: Look for rust, broken wires, or changes in shape.
- Professional inspections: A trained eye can spot issues others miss. My factory technicians are trained to spot even the smallest signs of weakening.
- Lack of Re-lubrication During Use: Wire ropes need new lubrication often. During use, the old lubricant gets squeezed out or washed away. Without it, wires rub against each other. They also get exposed to corrosion.
- Internal wear: Lack of lube inside the rope causes wires to wear down from friction.
- External protection: Lubricant on the outside protects against moisture and chemicals.
- Using Incompatible Lubricants: Not all lubricants are the same. Using the wrong type can be worse than using none. Some lubricants might not stick well. Others might react negatively with the rope material or environment.
- Specification adherence: Always use lubricants recommended by the rope manufacturer.
- Testing: If unsure, test a small section or consult experts. Always make sure the lubricant is compliant with standards.
What Are the Best Practices to Prevent Wire Rope Corrosion?
Preventing corrosion is easier than fixing it. There are clear steps we can take. These steps help keep ropes strong and safe for a long time.
To prevent wire rope corrosion, you must choose the right rope, lubricate it well, store it correctly, and inspect it often. These steps protect the rope from damage.
My customer, an Australian buyer, always stresses quality. He asks for ropes compliant with EN12385-4. High-quality ropes are the first step to preventing failure.
Dive Deeper: Implementing Corrosion Prevention Strategies
- Proper Wire Rope Selection: The type of wire rope matters. For harsh environments, use ropes with better corrosion resistance.
- Galvanized wire rope: This type has a zinc coating. Zinc protects the steel from rust. It is good for many outdoor or wet uses. We offer galvanized ropes.
- Stainless steel wire rope: This is best for very corrosive places, like marine or chemical settings. Stainless steel contains chromium, which forms a protective layer. We produce stainless steel wire ropes.
- Plastic Impregnated ropes: Some ropes have plastic inside. This seals the core. It stops moisture from getting in. This greatly reduces internal corrosion. We offer these.
- Specialized Assemblies: Sometimes, the way the rope is put together matters. Special designs can offer better protection.
- Effective Lubrication Practices: Lubrication is the most important step. It keeps moisture out and reduces friction.
- Regular application: Apply lubricant frequently based on usage and environment.
- Proper type: Use a high-quality wire rope lubricant that penetrates to the core. It should be viscous enough to stick but fluid enough to seep in.
- Application methods: Brushing, spraying, or pressure lubrication can be used. Pressure lubrication is best for getting oil into the core.
- Correct Storage Conditions: How you store your wire rope affects its life.
- Dry environment: Store ropes in a cool, dry place. Avoid direct sunlight and extreme temperatures.
- Elevated storage: Never store ropes directly on the ground. Use reels or pallets to keep them off the floor.
- Covering: If storing outdoors, cover them with waterproof but breathable material. This prevents moisture buildup.
- Routine Inspection and Maintenance: Regular checks find problems early.
- Visual inspections: Daily or weekly checks for obvious damage like rust spots or broken wires.
- Detailed inspections: Monthly or quarterly, depending on use, inspect more closely for internal damage.
- Record keeping: Keep records of all inspections and maintenance actions. This helps track the rope’s condition over time.
- Certifications: Always look for ropes with relevant certifications. We can provide BV & CE, RMRS, DNV, and ABS certificates. This proves the rope meets high-quality standards.
Prevention Method | Key Action | Benefit |
---|---|---|
Selection | Choose galvanized or stainless steel | Higher inherent corrosion resistance |
Lubrication | Apply proper lube regularly | Forms barrier, reduces friction, prevents internal rust |
Storage | Store dry, off ground | Protects from environmental moisture |
Inspection | Regular checks | Early detection of damage, timely action |
Conclusion
Wire rope corrosion is a serious threat. But you can fight it. Choose the right rope, lube it often, store it dry, and inspect it regularly. These steps save you money and keep your operations safe.