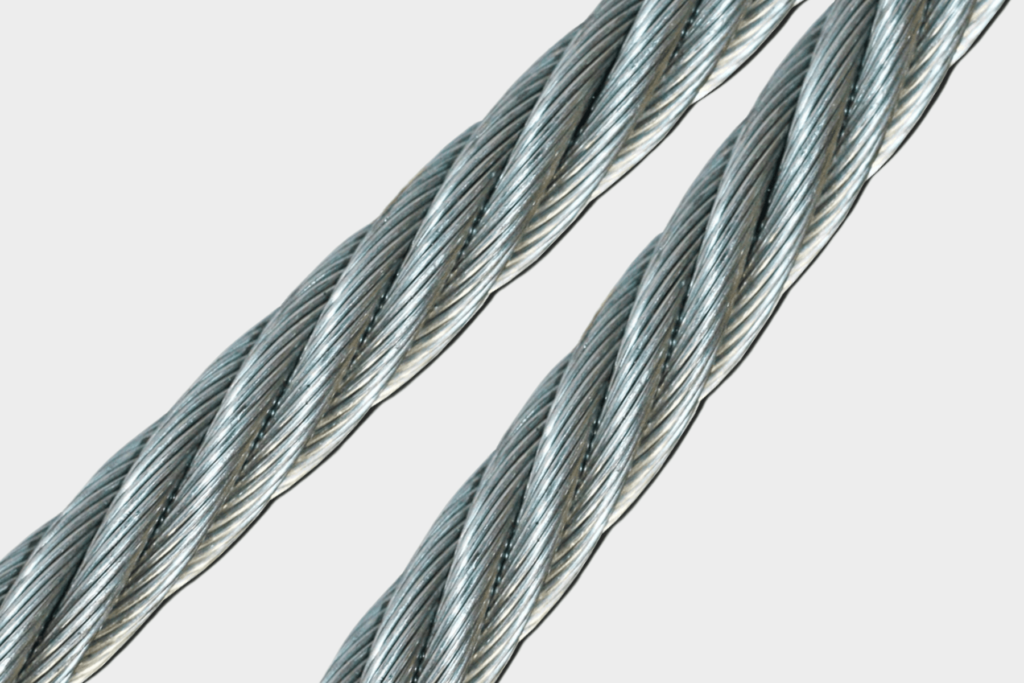
Does your wire rope corrode quickly? Are you constantly replacing it? This can be very frustrating. It also costs a lot of money.
Corrosion-resistant stainless steel wire rope resists rust. It works well in harsh places. This keeps your operations moving smoothly for longer.
Let me tell you about a time I saw a customer struggle with this. Their standard ropes failed fast. They needed a better solution.
What Makes Stainless Steel Wire Rope Resist Corrosion?
When you work with wire ropes, you know quality matters. But what truly makes stainless steel special for resisting corrosion? Let’s explore this.
Stainless steel wire rope resists corrosion because it has elements like chromium. This forms a protective layer on the surface. This layer prevents rust and damage.
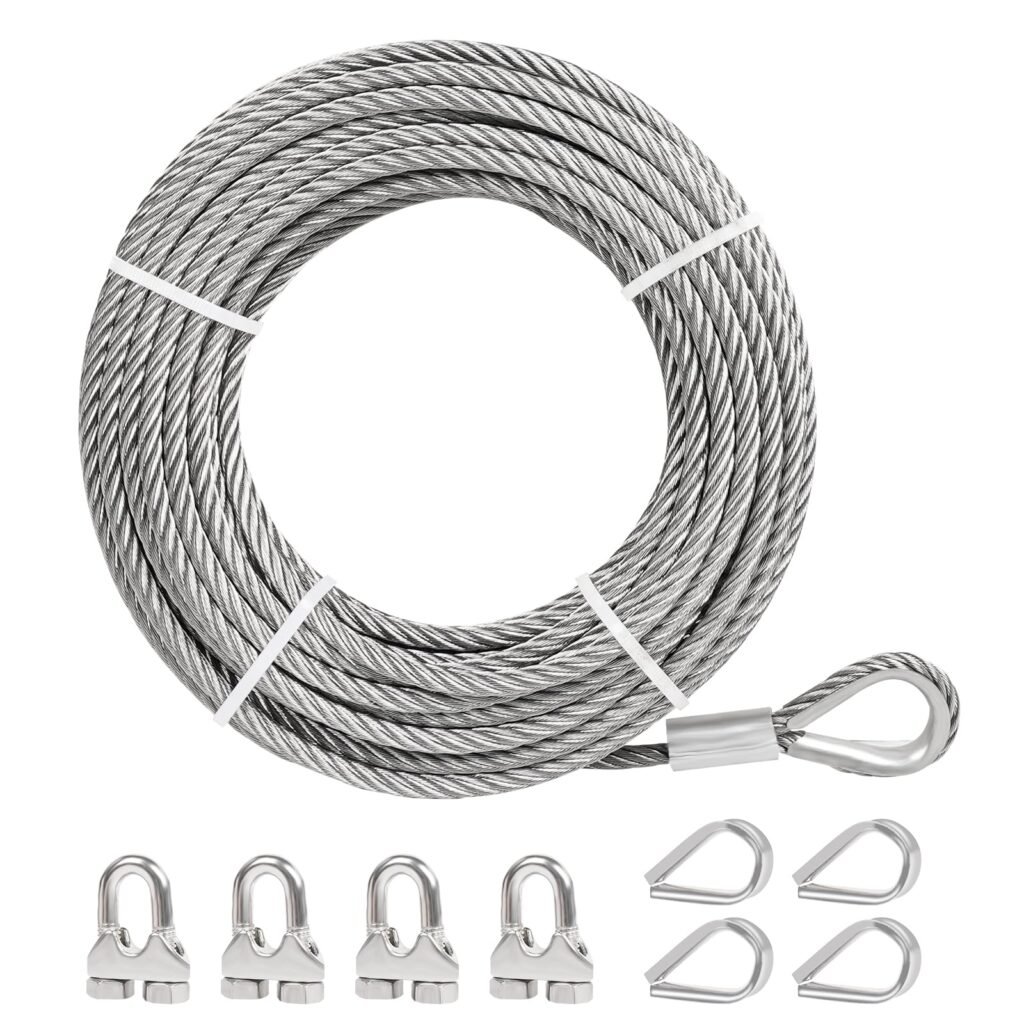
How Does the Protective Layer Work?
Understanding how stainless steel fights corrosion helps you make better choices. It’s not magic. It’s science.
When chromium in the steel meets oxygen, it forms something special. It creates a thin, invisible layer on the steel surface. We call this the passive layer. This layer protects the metal underneath.
Why is this Passive Layer Important?
- Self-healing: If the surface gets a scratch, the passive layer can repair itself. It just needs more oxygen. This makes it very durable.
- Barrier effect: It stops harmful substances from reaching the steel. This prevents rust from starting.
- Different grades: Not all stainless steels are the same. Different grades have different amounts of chromium and other elements. This changes their corrosion resistance.
Stainless Steel Grade | Main Elements | Common Uses | Corrosion Resistance |
---|---|---|---|
304 | Cr, Ni | General | Good |
316 | Cr, Ni, Mo | Marine | Better |
316L | Cr, Ni, Mo | Welding | Best |
This table shows why selecting the right grade for your use is crucial. For example, in marine settings, 316 or 316L is usually the best choice. This is because they contain molybdenum, which helps against salt water.
Where Are Corrosion-Resistant Ropes Most Useful?
Working in tough environments needs tough equipment. Standard wire ropes just won’t cut it. They rust too fast.
Corrosion-resistant ropes are most useful in saltwater, chemical plants, and high-humidity areas. They are also good in places with extreme temperatures or pollution.
Dive Deeper: Real-World Applications
Let’s think about places where ropes really suffer. Imagine a crane on a ship. It’s always wet and salty. Or a factory dealing with harsh chemicals. These places demand special ropes.
- Marine and offshore: This is perhaps the most obvious. Saltwater is very corrosive. Stainless steel ropes are essential here. They are used on ships, oil rigs, and docks. My company, Aulone, provides marine wire ropes that excel in these conditions. They have high breaking load and comply with EN12385-4.
- Chemical processing plants: These places have corrosive fumes or liquids. Wire ropes here must resist chemical attack. Stainless steel prevents rapid degradation.
- Food and beverage industry: Here, cleanliness is paramount. Stainless steel is easy to clean and does not corrode. This prevents contamination.
- Mining: While often a very dusty environment, some mining operations involve acidic water or corrosive elements. My company also offers specialized mining wire rope and is even helping some users in Russia.
- Architectural applications: Ropes are sometimes used for aesthetic purposes in buildings. Here, they need to look good for a long time. Stainless steel keeps its appearance.
One of our clients was a Russian company. They shifted from German suppliers due to global changes. They needed high quality. They also needed ropes fast. We helped them with strong, reliable ropes. These ropes resisted corrosion. They met strict quality control. This shows how crucial the right material is.
What Are the Benefits of Using These Ropes?
Choosing corrosion-resistant ropes offers many benefits beyond just preventing rust.
- Longer lifespan: You replace ropes less often. This saves time and money.
- Reduced downtime: Fewer replacements mean your machines run more. This boosts productivity.
- Improved safety: Ropes that do not corrode are stronger and more reliable. This reduces the risk of accidents.
- Lower maintenance costs: Less rust means less need for cleaning or protective coatings.
Can All Stainless Steel Ropes Handle Tough Conditions?
It’s common to think all stainless steel is the same. But that’s not true. Just saying “stainless” isn’t enough.
No, not all stainless steel ropes can handle tough conditions equally. The grade and specific manufacturing process determine its true corrosion resistance and strength for harsh environments.
Understanding Grades and Manufacturing
When I talk to clients, I always emphasize this point. Just like not all cars are the same, not all stainless steel ropes are identical.
Different Grades, Different Strengths
As mentioned before, grades like 304, 316, and 316L have different properties.
- 304 Stainless Steel: This is the most common type. It offers good corrosion resistance for general uses. But it might not be enough for very aggressive environments like strong acids or constant saltwater exposure.
- 316/316L Stainless Steel: These grades contain molybdenum. This element greatly improves resistance to chlorides. This makes them ideal for marine or chemical applications. The “L” in 316L means “low carbon.” This is better for welding. It also helps prevent corrosion near welds.
Manufacturing Process Matters
Beyond the material, how the rope is made also affects its performance.
- Plastic impregnation: Some wire ropes have plastic inside. This fills the spaces between strands. It can increase fatigue life. It also keeps corrosive elements out. My company offers plastic impregnated ropes.
- Galvanization: While not stainless steel, galvanized wire rope (carbon steel with a zinc coating) offers good corrosion protection in certain environments. It’s a different solution, but sometimes relevant for cost reasons. We also provide this option.
- Quality control: A well-made rope, with consistent strand lay and proper lubrication, will perform better. Even if it’s stainless, poor manufacturing can lead to early failure. At Aulone, our factory has four production lines. We focus on high quality. We also meet standards like EN12385-4. We can provide BV & CE, RMRS, DNV, ABS certificates for our clients too.
When our Russian client needed ropes, not only did they seek specific certifications, but they also had very strict quality control. They relied on me to ensure the ropes would withstand their operational demands, which often included harsh weather.
This rigorous attention to detail, from the raw material to the final product, is what separates basic stainless steel rope from truly corrosion-resistant, high-performance wire rope.
Conclusion
Choosing the right wire rope is critical. Corrosion-resistant stainless steel ropes last longer. They also perform better in tough places. Invest in quality for safety and efficiency.