Elevator Industry
8X19S-GSF Polymer core elevator wire ropes
Aulone Advanced manufacturing techniques allow for the creation of wire ropes with varying materials, constructions, and coatings, ensuring compatibility with diverse elevator designs and operational demands. Whether it’s high-rise skyscrapers, industrial facilities, or residential buildings, tailored wire ropes can be engineered to meet the unique needs of each application.
From robust steel cores for heavy-duty lifting to specialized coatings for corrosion resistance, the versatility of tailored wire ropes enables customization for any elevator system. Additionally, advancements in design and materials contribute to extended service life, reduced maintenance costs, and enhanced safety standards.
By partnering with experienced wire rope manufacturers and leveraging cutting-edge technologies, elevator companies can offer reliable and efficient vertical transportation solutions tailored to the specific requirements of their clients. This approach not only enhances overall performance but also ensures compliance with industry regulations and standards, fostering trust and confidence among building owners and occupants alike.
Low-rise traction rope
Mid-rise traction rope
High-rise traction rope
Governor rope
Compensating rope
Door closing rope
Tailored Elevator Wire Ropes to Suit Your Needs!
Customized elevator wire ropes can significantly enhance safety, durability, and efficiency in vertical transportation systems. By tailoring wire ropes to specific requirements, factors such as load capacity, speed, environmental conditions, and building architecture can be optimized for peak performance.
Available Sizes: Ranging from 6.3-22MM
Tensile Strength: 1370,1570, 1770,1870, 1960mpa.
Specifications on Offer: EN12385 and specific customer requirements.
Surface Treatments: Options including hot galvanized, ungalvanized.
Structure: 8x19S-NFC,8x19S-FC (GSF),8x25F-NFC,6x25F-NFC / SFC, 6x19W-WSC ,8x19W-IWRC , 8x19S-IWRC etc
Lay types: RHLL, RHRL, LHLL, LHOL
Certifications: All our ropes come with BV and CE certifications, providing you with the assurance of quality and compliance with international standards.
Your Ultimate Guide to Acquiring Compacted Strand Wire Rope
Acquiring the right elevator wire rope is crucial for the safety and efficiency of your elevator system. This guide will help you navigate the key factors and considerations involved in making an informed purchase.
Table of contents
Chapt 1
What are elevator wire ropes made of?

Elevator wire ropes are typically made of high-strength steel, specifically carbon steel, stainless steel, or galvanized steel. Each type of steel offers different properties suited to various elevator applications:
Carbon Steel:
- Description: Carbon steel wire ropes are the most common type used in elevator applications.
- Properties: They offer high tensile strength and good resistance to wear and abrasion. Carbon steel wire ropes are cost-effective and suitable for most elevator systems.
Stainless Steel:
- Description: Stainless steel wire ropes are corrosion-resistant and suitable for elevators operating in corrosive environments or exposed to moisture.
- Properties: They offer excellent resistance to rust and corrosion, making them ideal for outdoor elevators, coastal regions, or industrial settings where exposure to moisture or chemicals is common. Stainless steel wire ropes are also highly durable and have a longer service life compared to carbon steel ropes.
Galvanized Steel:
- Description: Galvanized steel wire ropes are coated with a layer of zinc to enhance corrosion resistance.
- Properties: They offer improved protection against rust and corrosion, making them suitable for elevators operating in outdoor or humid environments. Galvanized steel wire ropes are more durable than untreated carbon steel ropes and are often chosen for elevators exposed to moisture or corrosive elements.
The choice of wire rope material depends on factors such as the environment in which the elevator operates, the load capacity, and the desired service life. Carbon steel wire ropes are suitable for most elevator applications, while stainless steel and galvanized steel wire ropes offer enhanced corrosion resistance for specific environmental conditions.
Chapt 2
How are elevator wire ropes constructed?
Elevator wire ropes are constructed using a specific arrangement of steel wires twisted together to form strands, which are then twisted together to create the final rope. Here’s an overview of the construction process:
Individual Wires:
Elevator wire ropes are typically made of multiple individual steel wires. These wires are drawn from steel rods through a series of dies to achieve the desired diameter and mechanical properties.
Strand Formation:
The individual wires are grouped together and twisted around a central core to form strands. The number of wires in each strand and the direction of twist (right-hand or left-hand lay) can vary depending on the desired characteristics of the rope.
Core Selection:
The strands may be wrapped around a core, which can be made of fiber (fiber core), independent wire rope (IWRC), or wire strand (WSC). The core provides additional stability and support to the rope structure.
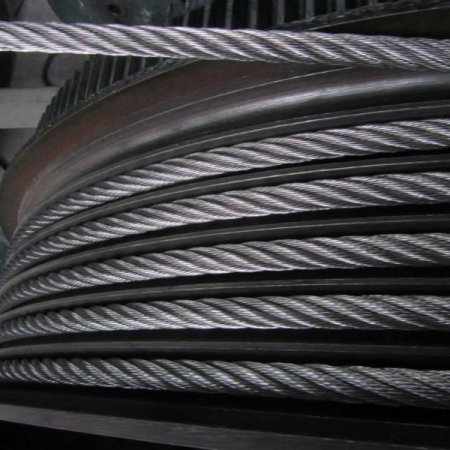
Stranding Process:
The twisted strands are then combined and twisted together in the opposite direction to form the final wire rope. This twisting process helps distribute the load evenly across the strands and enhances the strength and flexibility of the rope.
Finishing:
After the stranding process, the wire rope may undergo additional treatments or coatings to improve its performance and durability. This could include galvanizing to provide corrosion resistance or lubrication to reduce friction and wear.
Inspection and Testing:
Once the wire rope is manufactured, it undergoes rigorous inspection and testing to ensure it meets the required specifications and standards for strength, flexibility, and safety. This may include visual inspections, dimensional checks, and mechanical testing.
Overall, the construction of elevator wire ropes involves precise engineering and manufacturing processes to create a durable and reliable product capable of safely lifting and supporting elevator cars and their passengers.
Chapt 3
What factors affect the lifespan of elevator wire ropes?
The lifespan of elevator wire ropes can be influenced by various factors, including:
Material Quality: The quality of the steel used in the wire rope significantly impacts its lifespan. High-quality materials, such as carbon steel, stainless steel, or galvanized steel, are more resistant to wear, corrosion, and fatigue, resulting in longer lifespans.
Load Capacity: Elevator wire ropes are designed to withstand specific load capacities. Exceeding these capacities can lead to premature wear and fatigue, reducing the rope’s lifespan. Properly matching the rope’s load capacity to the elevator’s requirements is essential for maximizing its lifespan.
Frequency of Use: Elevators that are heavily used or subjected to frequent starts and stops may experience accelerated wear and fatigue on the wire ropes. The more cycles the rope undergoes, the shorter its lifespan is likely to be.
Maintenance Practices: Regular maintenance, including lubrication, tension adjustments, and visual inspections, can help identify and address issues that could shorten the wire rope’s lifespan. Neglecting maintenance can lead to accelerated wear and deterioration.
Environmental Conditions: Elevator wire ropes operating in harsh environments, such as high humidity, extreme temperatures, or exposure to corrosive substances, may experience accelerated corrosion and degradation. Proper protection measures, such as galvanizing or stainless steel construction, can help mitigate these effects and extend the rope’s lifespan.
Proper Installation: Incorrect installation, including improper tensioning or termination, can lead to premature wear and fatigue on the wire rope. Ensuring proper installation by trained professionals following manufacturer guidelines is essential for maximizing the rope’s lifespan.
Sheave and Drum Condition: The condition of the sheaves and drums over which the wire rope travels can impact its lifespan. Worn or misaligned sheaves can cause increased friction and wear on the rope, leading to reduced lifespan. Regular inspection and maintenance of sheaves and drums are necessary to minimize these effects.
By considering and addressing these factors, elevator owners and maintenance personnel can help maximize the lifespan of elevator wire ropes, ensuring safe and reliable operation over an extended period.
Chapt 4
What are the common types of wire rope deterioration?
Wire rope deterioration in elevator systems can occur due to various factors. Recognizing the common types of deterioration is essential for timely maintenance and ensuring safety. Here are the common types:
Wear and Abrasion:
External Wear: Caused by friction between the rope and sheaves or other surfaces. This leads to flattening or reduction in the rope’s diameter.Internal Wear: Occurs between the strands and wires within the rope, often due to inadequate lubrication.
Corrosion:
- Surface Corrosion: Visible rust or pitting on the rope’s surface, often due to exposure to moisture or corrosive environments.
- Internal Corrosion: Occurs within the rope, particularly in humid or corrosive environments, leading to weakened internal wires.
Fatigue:
- Bending Fatigue: Results from the rope repeatedly bending over sheaves and drums, causing cracks and breaks in individual wires.
- Torsional Fatigue: Occurs from twisting and untwisting movements, especially in non-rotation-resistant ropes.
Broken Wires:
- Fatigue Breaks: Appear as small breaks due to repeated bending.
- Shock Loads: Sudden impact loads can cause immediate wire breaks.
- Abrasion Breaks: Result from continuous wear and friction.
Deformation:
- Kinking: Caused by improper handling or sudden release of tension, leading to permanent bends in the rope.
- Crushing: Results from ropes being squeezed or pressed, often seen in multilayer winding systems on drums.
Core Failures:
- Fiber Core Deterioration: Fiber cores can rot or break down, reducing support for the outer strands.
- Steel Core Damage: Steel cores can suffer from fatigue and corrosion, impacting the overall strength of the rope.
Birdcaging:
- Description: The outer strands become loose and form a cage-like appearance around the core, usually due to sudden release of tension or overloading.
- Impact: Severely reduces the rope’s strength and requires immediate attention.
Corroded or Damaged End Fittings:
- Description: Corrosion or damage at the rope’s termination points, such as sockets or clips.
- Impact: Can lead to slippage or failure at the connection points.
Reductions in Rope Diameter:
- Description: General reduction in diameter due to wear, corrosion, or internal damage.
- Impact: Indicates overall weakening of the rope structure.
Monitoring and Maintenance
Regular inspections and proper maintenance practices are crucial to identify these types of deterioration early. Using lubricants, ensuring proper tension, avoiding overloading, and following manufacturer guidelines for installation and maintenance can help extend the lifespan of elevator wire ropes and ensure safe operation.
Conclusion
Understanding these common types of wire rope deterioration enables timely detection and intervention, ensuring the safety and reliability of elevator systems. Regular maintenance and inspections are key to mitigating these issues and extending the lifespan of the wire ropes.
Chapt 5
What are the best practices for maintaining elevator wire ropes?
Maintaining elevator wire ropes is crucial for ensuring safe and reliable operation. Here are some best practices for maintaining elevator wire ropes:
Regular Inspection: Schedule routine visual inspections of the wire ropes to check for signs of wear, corrosion, broken wires, or any other damage. Inspections should be conducted by trained personnel according to manufacturer recommendations and industry standards.
Lubrication: Proper lubrication helps reduce friction, wear, and corrosion, extending the lifespan of the wire ropes. Use a suitable lubricant recommended by the manufacturer and apply it according to the specified intervals and methods.
Tensioning: Maintain proper tension in the wire ropes to prevent slack or excessive stress. Follow the manufacturer’s guidelines for adjusting tension and ensure that the ropes are correctly installed and aligned with the elevator system.
Environmental Protection: Protect wire ropes from exposure to moisture, chemicals, extreme temperatures, and other environmental factors that can accelerate corrosion and deterioration. Use appropriate covers, seals, or coatings to shield the ropes from harmful elements.
Cleaning: Keep the wire ropes clean and free from debris, dirt, or contaminants that can cause abrasion or damage. Use gentle cleaning methods and avoid abrasive materials or harsh chemicals that could degrade the rope’s surface.
Replacement of Worn Ropes: Monitor the condition of the wire ropes regularly and replace them when they reach the end of their service life or show significant signs of wear and tear. Follow the manufacturer’s recommendations for rope replacement intervals and procedures.
Proper Storage: Store spare wire ropes in a clean, dry, and well-ventilated area to prevent rusting or contamination. Avoid storing ropes near sources of moisture, heat, or chemicals that could degrade their quality.
Training and Awareness: Provide training to elevator maintenance personnel on proper wire rope handling, inspection techniques, and safety precautions. Encourage awareness of potential hazards associated with wire rope maintenance and operation.
By following these best practices, you can ensure the optimal performance, longevity, and safety of elevator wire ropes in your facility. Regular maintenance and attention to detail are key to preventing accidents and minimizing downtime associated with wire rope issues.
Chapt 6
How do you inspect elevator wire ropes for safety?
Inspecting elevator wire ropes for safety is a crucial part of elevator maintenance to ensure the reliable operation of the elevator and the safety of passengers. Here’s a general outline of how elevator wire ropes are inspected for safety:
Visual Inspection:
Begin with a visual inspection of the wire ropes. Look for any signs of wear, corrosion, fraying, or broken strands. Inspect the entire length of the wire ropes, including areas where they pass over pulleys and around sheaves.
Check for any abnormalities such as kinks, birdcaging (where strands splay out), or crushing.
Lubrication:
Check the lubrication of the wire ropes. Proper lubrication helps to reduce friction and wear between the wire strands, extending the life of the wire ropes.
Ensure that the lubricant is evenly distributed along the length of the wire ropes.
Tension Inspection:
Measure the tension of the wire ropes using a tension gauge or dynamometer. Proper tension is critical for the safe operation of the elevator.
Refer to the elevator manufacturer’s specifications for the recommended tension levels for the specific type of wire rope used in the elevator.
Non-Destructive Testing (NDT):
Utilize non-destructive testing methods such as magnetic particle inspection (MPI) or ultrasonic testing (UT) to detect internal defects or cracks in the wire ropes.
NDT techniques can identify issues that may not be visible during visual inspections alone, providing a more thorough assessment of the wire rope’s condition.
Documentation and Record-Keeping:
Maintain detailed records of all inspections, including dates, findings, and any maintenance or repair work performed on the wire ropes.
Keep track of the service life of the wire ropes and schedule replacements as necessary based on their condition and usage.
Professional Inspection:
In addition to regular inspections performed by maintenance personnel, schedule periodic inspections by qualified elevator technicians or third-party inspection agencies.
These professionals have specialized knowledge and equipment to conduct thorough inspections and identify any potential safety hazards or maintenance issues.
Compliance with Regulations:
Ensure that all inspections and maintenance activities comply with relevant safety regulations, codes, and standards governing elevator operation and maintenance.
Regular and thorough inspections are essential for identifying potential safety hazards and maintaining the reliability and safety of elevator wire ropes. Any signs of wear, damage, or deterioration should be addressed promptly to prevent accidents and ensure the continued safe operation of the elevator.
Get the catalogue
Leave a request and we will send you the catalogue with Aulone steel wire ropes by e-mail
86-15573139663
86-15363044363