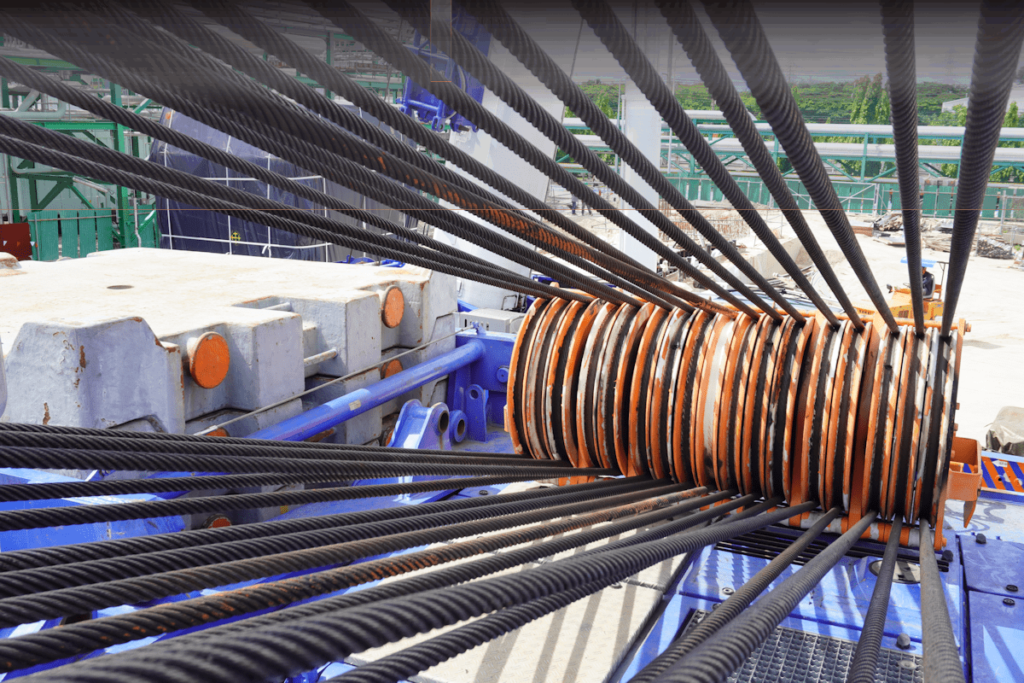
Problem: Is your crane wire rope failing too soon? Agitate: Frequent replacements cost you time and money. Solve: Let me show you how to make your ropes last longer.
Regular inspection and proper maintenance are key to extending the life of your crane wire rope. This includes lubrication, proper spooling, and avoiding overloading. Following these simple steps will significantly improve rope longevity.
I have worked with wire ropes for many years. Through my experience at Aulone, I have learned the best ways to care for these critical components. Let me share some valuable tips with you.
How Do I Properly Inspect My Crane Wire Rope?
Inspecting your crane wire rope is crucial. You need to look for specific signs of wear. This helps you catch problems early.
Proper inspection involves checking for broken wires, corrosion, deformation, and proper lubrication. You should conduct daily visual checks and more thorough inspections regularly.
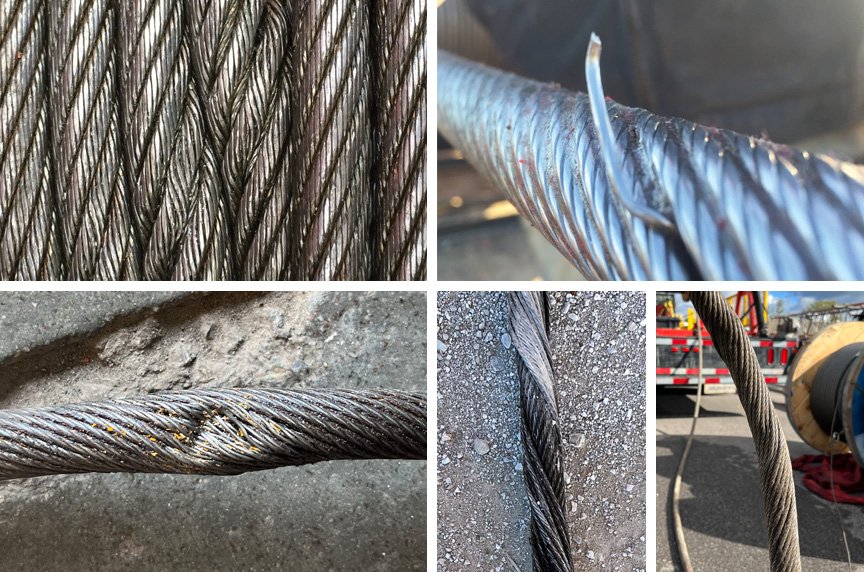
Dive Deeper: What to Look For During Inspection
When I inspect a crane wire rope, I look at several key areas. Each area tells me something about the rope’s health.
Broken Wires: The First Sign of Trouble
One of the most common issues I see is broken wires. These are easy to spot.
- When to replace: If you find a certain number of broken wires over a specific length, it’s time for replacement. For example, 6 randomly distributed broken wires in one lay length (six times the rope diameter) often signal replacement is needed.
- Where to check: Pay extra attention near end connections, over sheaves, and around drum areas. These are high-stress points.
- Why it matters: Broken wires reduce the rope’s overall strength. This makes it unsafe.
Corrosion: A Silent Killer
Corrosion can weaken a wire rope from the inside out. You might not always see it on the surface.
- What it looks like: Reddish-brown dust is a common sign. Pitting on the steel surface shows severe corrosion.
- How it happens: Moisture and chemicals cause corrosion. Ensure your ropes are stored and used in dry conditions if possible.
- Why it matters: Corrosion reduces metal area. This lowers the rope’s breaking strength.
Deformation: Changes in Shape
Any change in the rope’s shape is a red flag. This includes kinking, crushing, or birdcaging.
- Kinking: A permanent bend in the rope. This usually happens from improper handling. Once kinked, the rope is permanently damaged.
- Crushing: Flattening of the rope. This occurs from heavy loads or improper drum winding.
- Birdcaging: The strands open up and separate. This is caused by sudden release of load or torsion.
- Why it matters: Deformations compromise the rope structure. This severely reduces its strength and safety.
Lubrication: The Lifeblood of Your Rope
A well-lubricated rope lasts longer. Lubrication reduces friction and prevents corrosion.
- What to check: The rope should feel slightly greasy. It should not look dry or rusty.
- How often: Check often. Lubricate as needed based on operating conditions and manufacturer recommendations.
- Why it matters: Proper lubrication ensures the internal wires move freely. This prevents wear and corrosion.
What is the Best Way to Lubricate a Crane Wire Rope?
Lubrication is vital for crane wire rope longevity. It reduces friction and protects against rust. Applying lubricant correctly makes a big difference.
The best way to lubricate a crane wire rope is by applying a compatible lubricant evenly along its entire length. This can be done manually or with automated systems, ensuring saturation into the core.
Dive Deeper: Types of Lubricants and Application Methods
Choosing the right lubricant and applying it properly are both important.
Choosing the Right Lubricant
Not all lubricants are the same. You need one designed for wire ropes.
- Penetration: The lubricant must penetrate the rope’s core. This is where internal friction and corrosion often start. I prefer lubricants that are thin enough to get inside but thick enough to stay.
- Adhesion: It should stick to the rope surface. This prevents it from being flung off during operation.
- Corrosion Protection: A good lubricant also acts as a barrier against moisture and corrosive elements. At Aulone, we offer plastic impregnated and galvanized wire ropes. These have extra protection.
- Compatibility: Ensure the lubricant is compatible with the rope material. Ask your rope supplier for recommendations.
Application Methods
There are a few ways to apply lubricant. Each has its pros and cons.
- Manual Application: This involves brushing or wiping the lubricant onto the rope. It is labor-intensive. However, it allows for close inspection during the process. This method is good for smaller ropes or localized lubrication.
- Drip Application: A slow drip of lubricant onto the rope as it passes. This is more consistent than manual methods. It requires a system to catch excess lubricant.
- Pressure Lubrication: This is the most effective method. It uses pressure to force lubricant into the rope’s core. This ensures complete penetration. It is often done with specialized equipment. This is ideal for large ropes or regular maintenance programs.
- Bath/Spray Application: Dipping the rope in a lubricant bath or spraying it. This can be effective. It needs careful control to avoid over-lubrication.
Lubrication Schedule Example
Here is a simple table for a lubrication schedule. This is just an example. Your actual schedule may vary.
Condition | Frequency | Method Recommended | Notes |
---|---|---|---|
Normal, dry environment | Every 3-6 months | Manual/Drip | Check appearance often. |
Humid, dusty environment | Monthly | Drip/Pressure | Dust can absorb lubricant. |
Corrosive environment (e.g., marine) | Weekly/Bi-weekly | Pressure | Critical for marine wire ropes. |
High Usage/Heavy Loads | Monthly/Bi-weekly | Pressure | Increased internal friction. |
Why is Proper Spooling on the Drum Important?
Proper spooling means winding the wire rope neatly on the drum. It seems simple. But it has a huge impact on rope life.
Proper spooling prevents crushing, kinking, and uneven wear of the wire rope. It ensures the rope maintains its structural integrity and distributes tension evenly across its length.
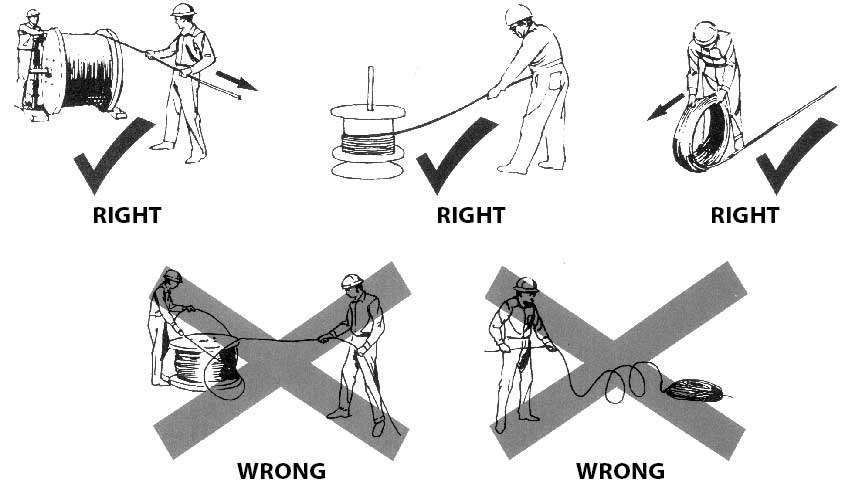
Dive Deeper: Consequences of Poor Spooling
Poor spooling can cause several problems. These problems reduce rope life significantly.
Crushing and Distortion
When the rope is not spooled evenly, layers can cross over each other. This creates pinch points.
- Result: The lower layers get crushed by the upper ones. This distorts the rope’s shape.
- Impact: Crushing weakens the rope. It can lead to internal wire breaks.
Kinking and Birdcaging
Improper winding can introduce twists. This can lead to kinks or birdcaging.
- Kinking: A permanent bend. Once a rope kinks, its strength is severely reduced. It must be replaced. This often happens if the rope is slack and then suddenly loaded.
- Birdcaging: Strands separate. This happens due to sudden load release or uneven tension.
- Impact: Both kinking and birdcaging are signs of severe damage. They make the rope unsafe.
Uneven Wear and Stress Concentration
Poor spooling also leads to uneven wear. Some parts of the rope will wear out faster.
- Problem: If the rope piles up on one side of the drum, that section experiences more stress.
- Result: You get localized wear. This means one small part of your rope fails, even if the rest is fine. This leads to premature replacement of the entire rope.
- Impact: Reduces the overall useful life of the rope.
Achieving Good Spooling
Here are a few tips for proper spooling:
- Maintain Tension: Always maintain slight tension on the rope during winding. This ensures tight wraps.
- Guide System: Use a proper rope guide or fleet angle. This helps the rope lay evenly.
- Drum Grooves: If your drum has grooves, make sure the rope fits correctly. This helps guide the wraps.
- Avoid Shock Loading: Sudden starts or stops can cause poor spooling. Operate smoothly.
Conclusion
Extending the life of your crane wire rope is not hard. Regular inspection, proper lubrication, and careful spooling are the keys. Doing this saves money and keeps your operations safe.