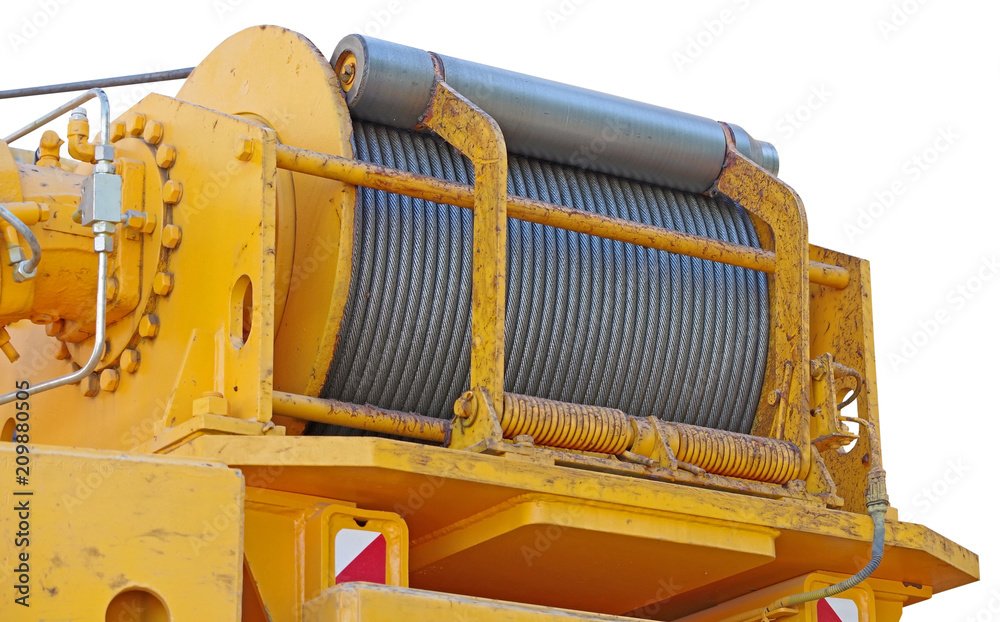
Is your crane wire rope failing too soon? Are you worried about costly replacements? Learn simple steps to extend its life and save money.
Proper care and maintenance greatly increase crane wire rope lifespan. Regular inspection, correct lubrication, and avoiding overload are key.
I remember a time when one of our clients faced constant crane downtime. Their ropes failed too often. It was a wake-up call for me. We then helped them implement precise strategies.
What is the best way to inspect crane wire ropes?
Regular inspection is crucial for crane wire rope safety and longevity. It helps identify issues early. This prevents unexpected failures.
The best way to inspect crane wire ropes involves visual checks for wear, damage, and corrosion. Feel for broken wires. Look for kinks or deformities.
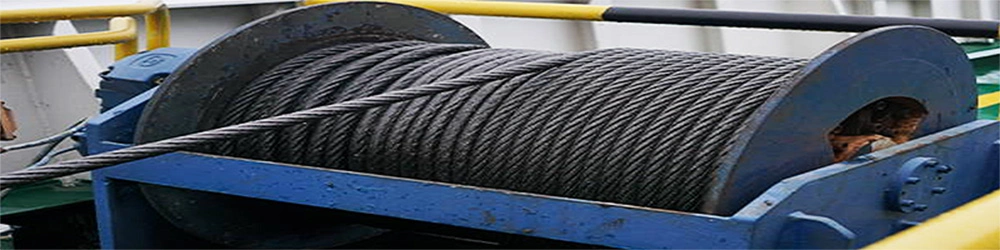
When checking your wire ropes, pay close attention to signs of degradation. This helps you act before problems become serious.
How often should I inspect my wire rope?
You should inspect your wire rope daily before it goes into service. A thorough inspection is needed weekly or monthly depending on use. Expert inspections are generally required annually.
What are key things to look for during an inspection?
- Broken Wires: Look for individual wires that are broken or frayed. These can poke out and cause more damage.
- Corrosion: Rust and pitting indicate corrosion. This weakens the rope.
- Wear: Check for flattened areas or reduced diameter. This shows wear.
- Kinks and Bends: Deformations like kinks or sudden bends severely compromise strength. They are often signs of improper handling.
- Lubrication: See if the rope looks dry. Proper lubrication keeps it healthy.
- End Fittings: Inspect the connections to the crane. Make sure they are secure and not damaged.
Regular inspection prevents small issues from growing into big, dangerous problems. Our team at Aulone always emphasizes this to clients. We provide high-quality ropes that meet EN12385-4. This makes them more durable. We also offer BV & CE, RMRS, DNV, ABS certificates for quality assurance.
How does proper lubrication extend wire rope life?
Lubrication is essential for wire rope longevity. It reduces friction. It also prevents corrosion.
Proper lubrication extends wire rope life by reducing internal and external friction. It also protects against rust and wear. This keeps the rope flexible.
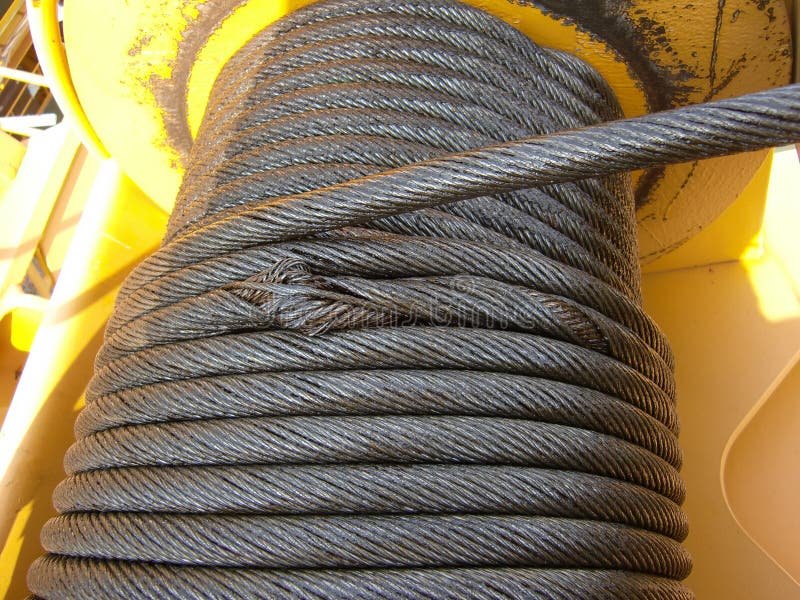
Many different things impact how long a wire rope lasts. Lubrication is one of the most important. It helps the rope work smoothly under stress.
Why is friction a problem for wire ropes?
Friction causes heat. It also causes wear. When wires rub against each other, they get weaker. Lubricant creates a film. This film prevents direct contact between wires. This reduces friction.
How does lubrication protect against corrosion?
Wire ropes are often used in harsh environments. These include marine or mining settings. Salt, moisture, and chemicals can cause rust. Rust weakens the steel. Lubricant forms a barrier. This barrier keeps harmful elements away from the metal. Some lubricants also have rust inhibitors.
What type of lubricant should I use?
The type of lubricant depends on the rope and its use.
- Penetrating lubricants get inside the rope. They lubricate the core and inner strands.
- Coating lubricants cover the outside. They protect against external wear and corrosion.
- Choose lubricants compatible with your rope material. For example, some ropes are plastic impregnated. We offer this feature with our ropes. This needs a compatible lubricant.
How often should I lubricate my wire rope?
Lubrication frequency depends on the rope’s use. It also depends on the environment. Heavy use and harsh conditions need more frequent application. A visual check for dry spots guides this decision. Always follow the manufacturer’s recommendations.
Investing in good lubrication saves money. It makes ropes last longer. It also reduces breakages. This improves safety.
What role does proper usage play in extending wire rope life?
Using the wire rope correctly is almost as important as maintenance. It prevents damage from wrong operation. This extends its operational lifespan.
Proper usage extends wire rope life by preventing overload, sudden shocks, and incorrect reeving. It means operating within safe working limits.
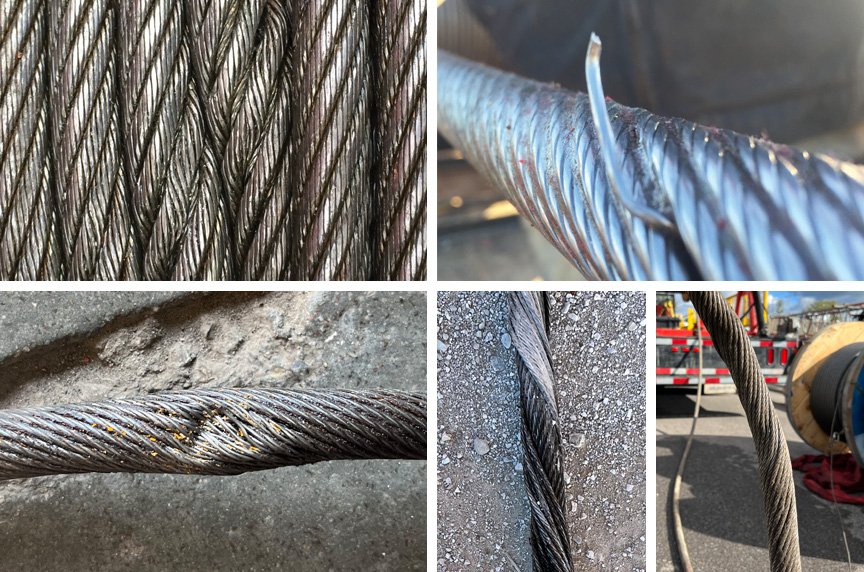
I have seen countless ropes fail because of wrong usage. My experience with clients, like those in mining, shows me this. A small mistake can lead to big problems.
How do I prevent overloading?
- Know the Load: Always know the weight of what you are lifting.
- Check the Capacity: Never exceed the crane’s or rope’s rated capacity. This is usually marked on the crane or in its manual.
- Use Load Indicators: Many modern cranes have load indicators. Use them.
- Avoid Shock Loads: Do not drop loads suddenly. Lower them smoothly. A sudden drop puts huge stress on the rope.
What is correct reeving?
Reeving is how the rope goes through the sheaves and drums. Wrong reeving can cause wear and damage.
- Avoid Crossover: Make sure the rope spools neatly onto the drum. Avoid ropes crossing over each other.
- Correct Sheave Alignment: Sheaves must be aligned. Misaligned sheaves cause rubbing and wear.
- Proper Fleet Angle: The fleet angle is the angle at which the rope approaches the drum. It should be small. A large angle causes rubbing.
Why are smooth movements important?
Sudden starts and stops put stress on the wire rope. Smooth movements distribute the load evenly. This reduces fatigue on the rope. This helps the rope last longer.
At Aulone, we make high-tensile strength wire ropes. They have high breaking loads. But even the best rope needs proper use to deliver its full life. We can customize logos too. This helps with branding for our buyers and distributors.
Why are environmental factors important for wire rope durability?
Environmental factors significantly affect wire rope durability. Conditions like moisture, temperature, and chemicals can speed up degradation. Understanding these factors helps in choosing and maintaining the right rope.
Environmental factors like moisture, extreme temperatures, and corrosive chemicals can degrade wire ropes. Protecting ropes from these elements is crucial for durability.
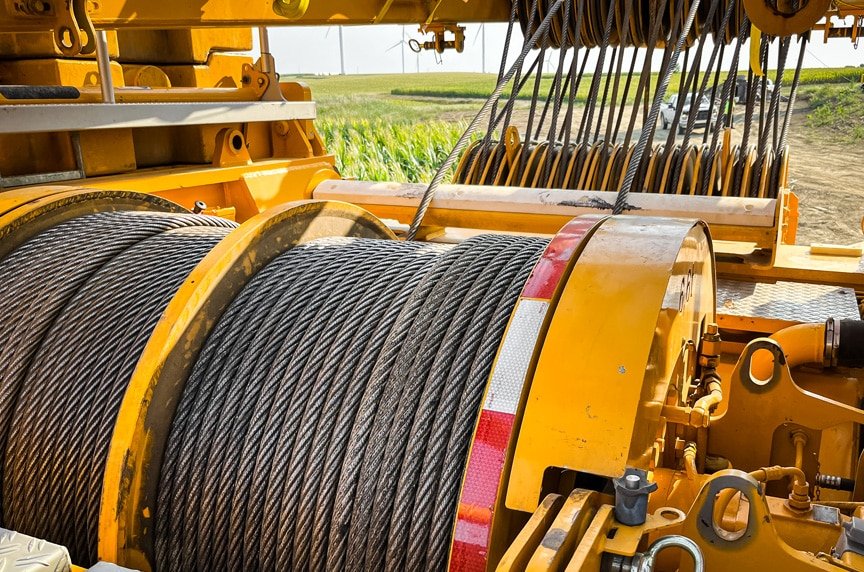
The environment where a wire rope operates is critical. A rope used near the sea, for example, faces different challenges than one used in a dry warehouse.
How does moisture affect wire ropes?
Moisture leads to rust and corrosion. Rain, humidity, or immersion in water can cause this. Corroded ropes lose strength. They become unsafe. Our galvanized wire ropes provide better protection against rust. This is a good option for wet environments.
What about extreme temperatures?
- High Temperatures: Excessive heat can affect the steel’s properties. It can also dry out lubricants. This leads to faster wear.
- Low Temperatures: Very low temperatures can make the steel brittle. It can make the rope more prone to breaking under stress. This also makes the rope stiff. This can affect its flexibility.
How do chemicals impact rope life?
Many industrial settings expose ropes to chemicals acids, alkalis, or solvents. These chemicals can corrode the steel. They can also damage the lubricant or fiber core. Special coatings or rope materials, like stainless steel wire rope, are needed for such conditions. We offer specialized assemblies and synthetic ropes too. These are great for tough chemical environments.
What can I do to protect ropes from the environment?
- Choose the Right Rope: Select ropes designed for the specific environment. For marine use, we offer marine wire rope. This is made to resist saltwater.
- Apply Proper Lubrication: Use lubricants that also offer environmental protection. Some are designed to shed water.
- Storage: Store ropes properly when not in use. Keep them dry and clean. Protect them from extreme temperatures.
- Regular Cleaning: Clean ropes to remove dirt and abrasive particles. This prevents them from grinding into the rope’s strands.
Understanding the operational environment is key to extending rope life. Our 4 production lines allow us to make specific ropes for different needs. Our ropes are also high quality, high tensile strength, and have high breaking load. This makes them good for many uses.
Conclusion
Extending crane wire rope life is about good habits. Inspecting, lubricating, using it right, and protecting it from the environment all help.