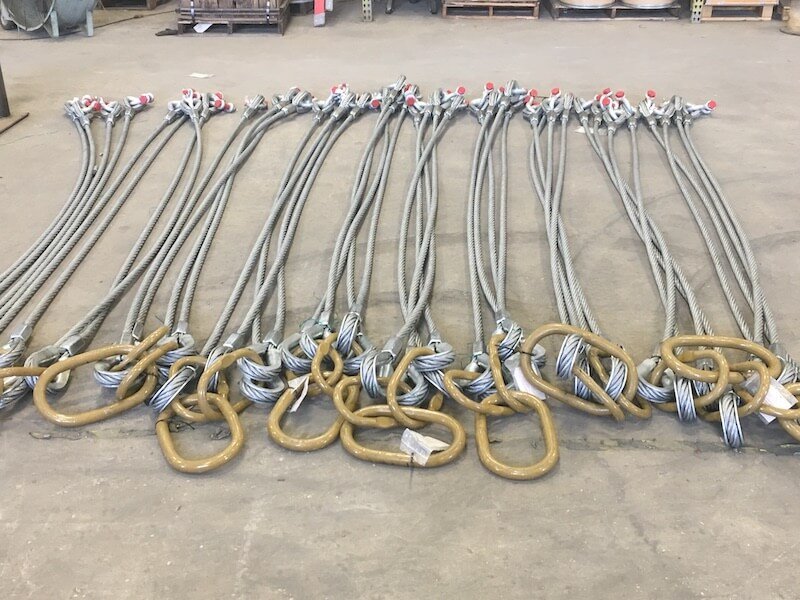
Is your team struggling with safe sling operations? Unsafe practices cause problems. They lead to accidents and unexpected costs. This affects your business directly.
Ensuring safe sling use requires proper training, regular equipment inspection, and strict adherence to established lifting procedures for every task.
I’ve seen firsthand how crucial this is. I recently worked with a client from Australia. He values strict quality control. He understands the importance of safety. It’s not just about products. It’s about safe operations too.
What Are the Key Steps for Safe Sling Inspection?
Pre-use inspection is essential. It prevents failures. How do you check your slings properly?
Key steps for safe sling inspection include checking for cuts, abrasions, kinks, heat damage, and structural integrity before every lift operation.
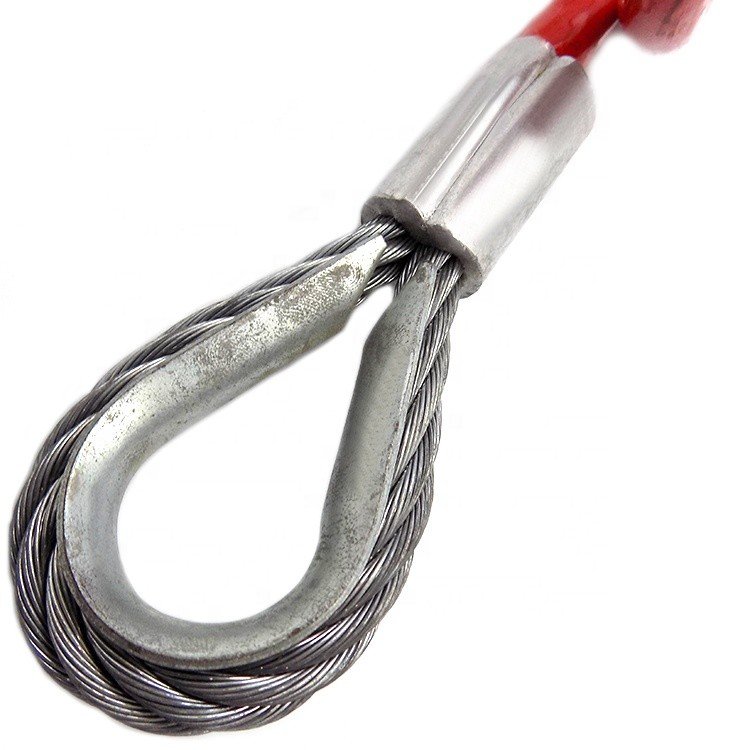
When inspecting slings, it’s not just a quick glance. It’s a detailed check. You need to look for specific signs of wear or damage. This makes sure the sling is safe for use. My factory at Aulone produces high-quality wire ropes. We focus on high tensile strength and high breaking load. This means our products are strong. But even the best products need careful inspection.
Visual Inspection Points:
Damage Type | What to Look For | Why It Matters |
---|---|---|
Cuts/Nicks | Any visible breaks in fibers or wires | Reduces strength, can lead to sudden failure |
Abrasions | Frayed areas, worn surfaces | Weakens material, increases risk of breakage |
Kinks/Distortions | Bends or twists that deform the rope’s shape | Permanently damages internal structure |
Heat Damage | Discoloration, charring, stiffness | Compromises material integrity |
Corrosion | Rust (for wire ropes), chemical degradation | Weakens material, especially in steel ropes |
You also need to check the hardware. This includes hooks, shackles, and thimbles. They must be free of cracks, deformation, or excessive wear. Any sign of damage means the sling is unsafe. It must be tagged and removed from service immediately. We can provide BV & CE, RMRS, DNV, ABS certificates for our wire ropes. This ensures our products meet high safety standards. But how you use them matters just as much.
How Does Proper Sling Selection Impact Safety?
Choosing the right sling is vital. The wrong sling can fail. This puts lives and property at risk. How do you pick the correct sling?
Proper sling selection impacts safety by ensuring the lifting capacity matches the load, the material suits the environment, and the sling type is appropriate for the lift configuration.
Selecting the right sling is not a guessing game. It requires knowledge of the load. It also requires understanding the environment. Consider the weight of the load first. Each sling has a Working Load Limit (WLL). Never exceed it. My factory produces specialized wire ropes for different uses. This includes crane wire rope, elevator wire rope, and mining wire rope. Each type is designed for specific applications.
Factors in Sling Selection:
Factor | Consideration | Example Application |
---|---|---|
Load Weight | Always match or exceed WLL | Lifting a 10-ton beam needs a sling >10T WLL |
Load Shape | Will it damage the sling? | Sharp edges require edge protection |
Environment | Temperature, chemicals, abrasives | Stainless steel for corrosive environments |
Lift Type | Choked hitch, basket hitch, vertical hitch | Each hitch affects the sling’s capacity |
Material | Steel, synthetic, chain | Synthetic for delicate surfaces |
For example, galvanized wire rope is excellent for marine use. It resists corrosion. Synthetic rope is lighter. It is good for delicate items. Choosing correctly prevents overstressing. It prevents premature wear. It ensures the sling performs as expected. This aligns with our commitment to high-quality and reliable products.
Why is Crew Training Essential for Sling Safety?
Even with suitable equipment, mistakes happen. Lack of training is a major cause. How important is training for safety?
Crew training is essential for sling safety because it teaches proper rigging techniques, hazard identification, communication protocols, and emergency procedures, significantly reducing accident risks.
Training is not a one-time event. It’s an ongoing process. Riggers and operators must understand the basics. They need to know advanced techniques too. Comprehensive training covers many areas. It starts with inspecting slings. It moves to knowing load capacities. It also includes proper attachment methods.
Key Training Modules:
Module | Learning Objectives | Importance |
---|---|---|
Sling Inspection | Identify damaged slings, remove from service | Prevents equipment failure |
Load Calculation | Determine load weight, calculate tension | Ensures sling is not overloaded |
Rigging Techniques | Proper hitching, balancing loads | Prevents load slippage or dropping |
Communication | Hand signals, radio protocols | Avoids miscommunication during lifts |
Emergency Procedures | Actions for mechanical failure or accidents | Minimizes injury and damage |
Continuous training also includes refreshers. It introduces new industry practices. It ensures everyone is up-to-date. This proactive approach saves lives. It also protects assets. It helps companies like mine build trust. We ensure our wire ropes comply with EN12385-4. Our quality is certified. User training ensures that quality translates to safe operations. My factory has four production lines. We export to many countries. This includes Singapore, Indonesia, Vietnam, and Saudi Arabia. Safe operation is a global need.
What Role Does Regular Maintenance Play in Sling Longevity and Safety?
Slings wear out over time. Heavy use causes damage. Ignoring maintenance shortens life. It also creates hazards. How does maintenance affect safety?
Regular maintenance plays a crucial role in sling longevity and safety by identifying wear and tear early, preventing catastrophic failures, and extending the service life of valuable lifting equipment.
Maintaining slings goes beyond daily checks. It involves scheduled, detailed inspections. It includes proper storage. It also means timely repairs by qualified professionals. For instance, galvanized wire rope from Aulone has enhanced corrosion resistance. But even coated ropes need care. They need to be kept clean and dry. They must be stored away from corrosive chemicals.
Maintenance Best Practices:
Practice | Description | Benefit |
---|---|---|
Scheduled Inspections | Periodic thorough checks by trained personnel | Detects hidden damage, ensures compliance |
Proper Storage | Store in dry, clean, covered areas, off the ground | Prevents corrosion and environmental damage |
Cleaning | Remove dirt, grease, and debris regularly | Allows for better inspection, prevents wear |
Lubrication | For wire ropes, apply appropriate lubricants | Reduces friction, prevents internal corrosion |
Repair/Replacement | Promptly repair minor damage or replace condemned slings | Maintains safety, avoids costly failures |
For wire ropes, proper lubrication is especially important. It reduces friction between strands. This prevents internal wear. It also protects against rust. We offer plastic impregnated wire ropes. These have improved internal lubrication. This adds to their durability. Ultimately, a well-maintained sling is a safe sling. It ensures smooth operations. It supports a culture of safety.
Conclusion
Ensuring safe sling use protects people and property. This involves regular checks, proper item selection, employee training, and consistent upkeep.