Does your crane wire rope wear out too fast? Are you losing money because of downtime? Many businesses face these problems.
You can increase crane wire rope life by choosing the ideal rope construction, inspecting it often, lubricating it regularly, and avoiding misuse.
I remember once, working with a large client who often spoke about their challenges with rope longevity. They used various types of crane ropes. That experience really made me focus on how we can help ropes last longer, starting with the right choice the first time.
What causes crane wire rope to fail?
When you work with heavy lifting, understanding why ropes fail is key. Many factors play a part. Recognizing these signs helps you act quickly.
Crane wire ropes primarily fail due to wear, fatigue, corrosion, crushing, bending, and improper operational use or installation procedures.
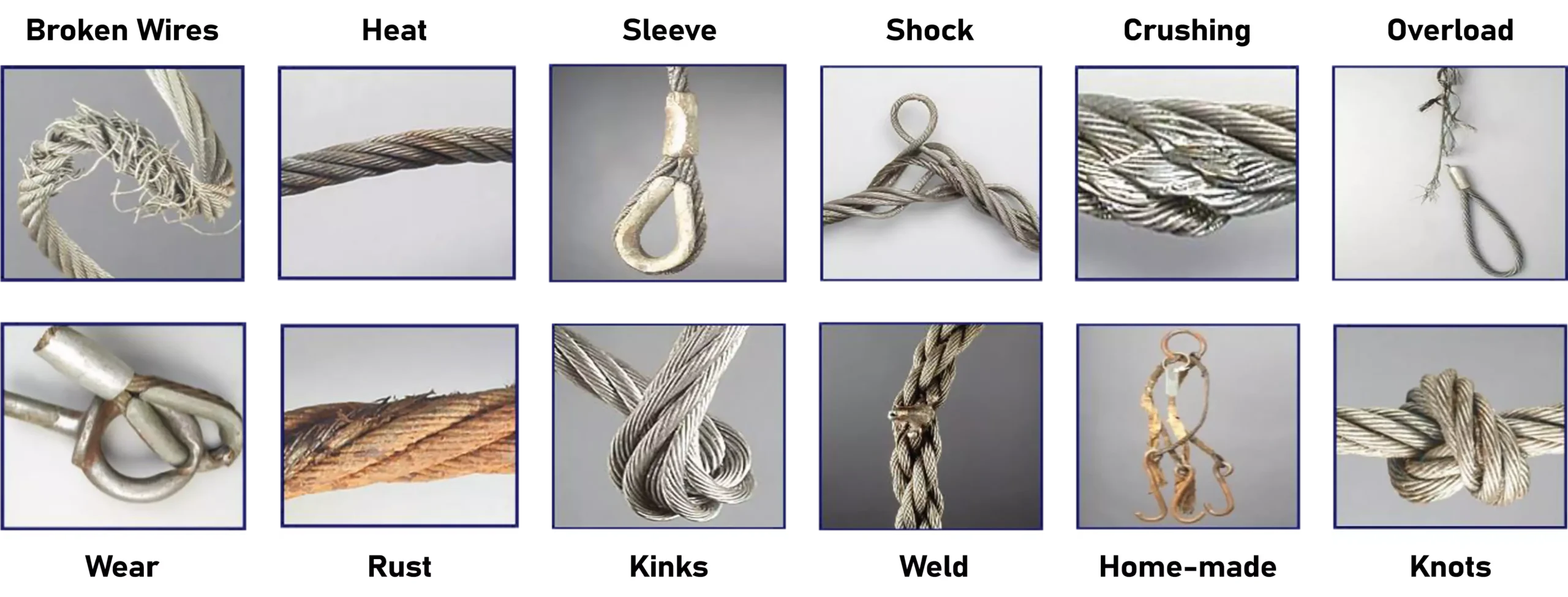
Let’s dive deeper into some common failure modes. Knowing these helps you prevent them. Understanding each failure type allows for targeted prevention.
Wear
Wear is a significant issue. It happens when the rope rubs against sheaves, drums, or other parts of the crane. This removes metal from the outer wires. This reduces the rope’s diameter and overall strength.
Type of Wear | What it Looks Like | Impact on Rope | Prevention Tip |
---|---|---|---|
Abrasive Wear | Outer wires appear flattened or shiny | Reduces rope strength and flexibility | Use correct sheave and drum groove dimensions; proper material selection |
Internal Wear | Not visible from outside; wires rub each other | Hidden damage, leads to sudden failure | Ensure adequate lubrication penetrates to the core; avoid severe bending |
Contact Wear | Occurs at points where rope contacts obstacles | Localized damage, often shows as indentations | Keep rope path clear; use guide rollers when needed |
Fatigue
Fatigue is a sneaky problem. It develops from repeated bending and unbending of the rope over sheaves and drums. This causes tiny, microscopic cracks to form within the individual wires. Over time, these cracks grow larger. Eventually, wires break. This type of failure is hard to predict without careful inspection. It often occurs without noticeable external signs until it’s too late.
Factor | Effect on Fatigue | Mitigation |
---|---|---|
Bend Radius | Smaller bend radii increase wire stress, accelerating fatigue | Use sheaves and drums with larger diameters; ensure proper D/d ratio |
Load Cycles | More cycles of loading and unloading lead to faster fatigue accumulation | Optimize lifting operations to reduce unnecessary cycles; avoid shock loading |
Vibration | Adds dynamic stress to wires, making them more prone to fatigue failure | Ensure crane mechanics are smooth; minimize sudden movements |
Reverse Bends | When rope bends in opposite directions over successive sheaves | Significantly increases fatigue compared to uni-directional bending |
Corrosion
Corrosion is the constant enemy of metal. It weakens the wires and strands by eating away at the steel. This happens when the rope is exposed to moisture, chemicals, saltwater, or other corrosive elements. Corrosion can be especially damaging internally where it is not visible. It reduces the metallic area of wires. This impacts the rope’s breaking strength. It also increases friction between wires.
Type of Corrosion | Environment | Appearance | Impact |
---|---|---|---|
General Rusting | Humid or wet air | Reddish-brown powder or flakes | Reduces strength, increases friction |
Pitting Corrosion | Localized areas, often from standing water | Small, deep holes or pits | Concentrates stress, leads to localized failure |
Stress Corrosion | Corrosive environment plus tensile stress | Cracks appear along wire grain boundaries | Can lead to sudden brittle fractures |
Galvanic Corrosion | Two dissimilar metals in contact with electrolyte | Accelerated corrosion of less noble metal | Avoid contact with dissimilar metals |
Crushing and Deformation
Sometimes, the rope gets flattened or distorted. This primarily happens when the rope winds improperly on the drum. Overlapping layers, excessive pressure, or improper fleet angle can cause this. Crushing also happens if the rope is not spooled with enough tension. This changes the rope’s internal structure. It makes it less flexible and weaker. It can also occur if the rope is run over sharp edges or crushed by external forces.
Improper Use or Installation
This is a very common cause of failure. If you install the rope incorrectly, or use it for tasks it’s not made for, it will fail fast. Examples include using undersized ropes. Also, shock loading, dragging the rope on the ground, or failing to follow proper reeving procedures can cause severe damage. Installation errors, such as inducing twists or kinks, permanently damage the rope. They severely reduce its strength.
How do you select the right wire rope for your crane?
Choosing the right wire rope is the first step to making it last. It’s not just about strength. It involves matching the rope’s characteristics to your crane’s specific needs and operating conditions.
You select the right wire rope by carefully considering the exact crane type, the operating environment, required strength, necessary flexibility, and specific resistance needs for wear and corrosion.
This choice greatly impacts the rope’s lifespan. Let me explain. We have extensive experience helping clients make these critical decisions.
Rope Construction
Wire ropes come in many different constructions. Each is designed for specific performance characteristics. Choosing the right construction is critical for both performance and longevity.
Construction Type | Key Features | Best For | What We Offer |
---|---|---|---|
19×7 | Rotation resistant; less torque generation | Single-part lines; operations with risk of uncontrolled spinning | Our 19×7 ropes offer stable lifting, minimizing load rotation which is crucial for precise placement. They are ideal for applications where the load is free to rotate. |
35xK7 | Highly rotation resistant; very flexible; compact | Mobile cranes, tower cranes, sensitive lifts with high heights | Our 35xK7 ropes provide superior rotation resistance and flexibility, making them excellent for long lifts and multi-part reeving systems where twist accumulation is a concern. Their compacted strands increase abrasion resistance. |
8xK26WS-IWRC | High breaking load; good abrasion resistance due to comp. strands; flexible | High-performance industrial cranes; heavy-duty lifting | With compacted strands and an independent wire rope core (IWRC), our 8xK26WS ropes offer an outstanding balance of strength, fatigue resistance, and durability. They are built for rigorous demands. |
6xK36WS-IWRC | Very high breaking load; excellent abrasion resistance from comp. strands | Main hoist ropes for large cranes; demanding industrial applications | Our 6xK36WS-IWRC ropes are designed for extreme loads and harsh conditions. The compacted outer strands provide maximum surface area for wear while maintaining high breaking strength and fatigue resistance. |
6x36WS-IWRC | Balanced strength and flexibility; good fatigue resistance | General purpose crane applications; overhead cranes | Our 6x36WS-IWRC is a versatile and robust choice. It provides dependable performance across a broad range of lifting tasks, offering good resistance to bending fatigue and abrasion. |
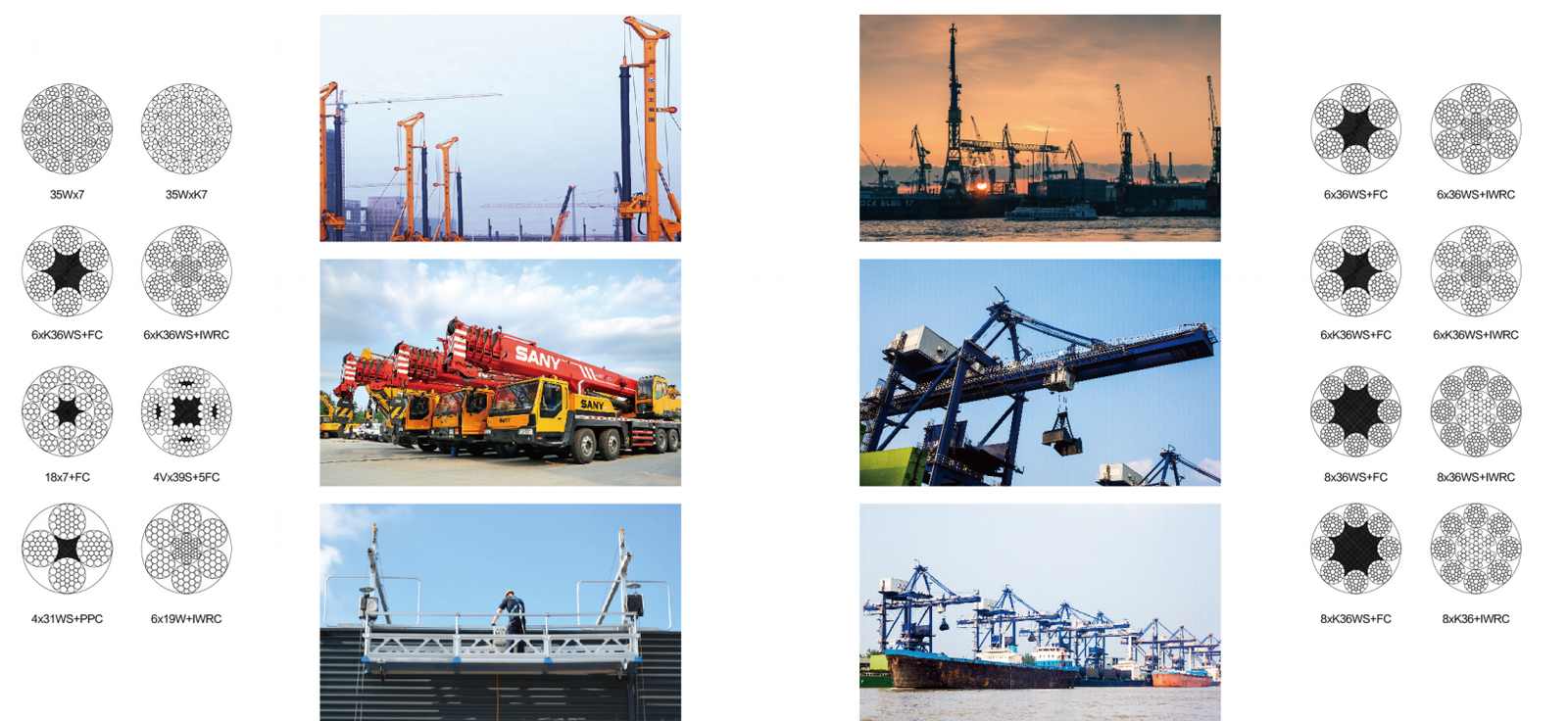
Material Type
The material matters a lot. We offer several options to meet your needs. We ensure our materials meet strict quality standards for performance.
Material | Properties | Best Suited For |
---|---|---|
Carbon Steel | High strength, cost-effective, durable | Standard lifting, demanding industrial use |
Galvanized Steel | Zinc coating for corrosion resistance | Outdoors, humid environments, marine applications |
Stainless Steel | Excellent corrosion resistance, aesthetic | Food industry, clean rooms, highly corrosive environments |
Plastic Impregnated | Enhanced corrosion and abrasion resistance | Harsh environments, aggressive industrial areas |
Strength Requirements
You must match the rope’s strength to your crane’s needs. This is critical for safety and performance. We always focus on providing ropes with high breaking loads. This ensures a healthy safety factor. It also gives you peace of mind during operations. Under-specifying strength leads to early failure. Over-specifying can lead to unnecessary cost.
Flexibility Needs
Some cranes need more flexible ropes. This depends on the size of the drums and sheaves. A more flexible rope handles bends better. This reduces internal wire fatigue. For instance, ropes with independent wire rope cores (IWRC) and multiple strands (like 19×7 or 35xK7) offer greater flexibility. This makes them suitable for cranes with small drum and sheave diameters.
Environmental Factors
Think about where the crane operates. Is it offshore, exposed to saltwater? In a mine with dust and chemicals? In a very cold place? These factors significantly affect rope choice. For example, galvanized or plastic impregnated ropes perform better in corrosive environments. For extreme temperatures, special lubricants and materials might be needed. This is why we focus on providing options like plastic impregnated and galvanized ropes. They stand up against harsh conditions.
What is the best way to inspect crane wire ropes?
Regular inspection is crucial. It helps you catch problems early. This saves money and prevents accidents. A robust inspection program is the backbone of wire rope longevity.
The best way to inspect crane wire ropes is through systematic daily visual checks, frequent detailed inspections performed by trained personnel, and periodic expert examinations.
A good inspection program not only extends rope life but also ensures the highest level of safety on your worksite.
Daily Visual Checks
Your operators should do a quick check every day. They should look for obvious damage before each shift or heavy lift.
What to Look For (Daily) | Sign of Problem | Action |
---|---|---|
Broken wires | Any visibly broken wires, especially bird-caging | Tag for closer review, potential replacement |
Kinks or permanent bends | Any unnatural, permanent bends or deformations | Stop use immediately, assess damage. Rope is likely compromised. |
Corrosion signs | Red dust, pitting, discoloration on wires | Note location, report for detailed check. Indicates lubrication issue. |
Proper winding on drum | Gaps between wraps, crossovers, crushing | Re-spool correctly if possible, or report for adjustment. Prevents accelerated wear. |
Lubrication presence | Rope appears dry, rusty, or stiff | Report for re-lubrication. Prevents internal friction and corrosion. |
Frequent Detailed Inspections
A designated, trained person should do these inspections. It should happen weekly or monthly, depending on how much you use the crane and the operating environment. This involves cleaning the rope to see all wires clearly. You need to measure diameter changes along the rope’s length. Look closely for internal damage signs. An experienced inspector can feel for broken wires inside the strands. We can provide guidance on what to look for based on EN12385-4 standards. This includes examining critical areas like end terminations and points that pass over sheaves frequently.
Periodic Expert Examinations
Every few months, or as dictated by regulations and usage, a certified third-party expert should conduct a thorough inspection. They use specialized tools, like non-destructive testing (NDT) equipment (e.g., magnetic rope testing), to detect damage deep inside the rope’s core that is invisible to the eye. They can meticulously check for certifications like BV, CE, RMRS, DNV, ABS, which we can also provide for our ropes. These examinations are crucial for identifying hidden deterioration that could lead to catastrophic failure.
Documentation
Keep comprehensive records of all inspections. This helps you track wear patterns over time. It helps predict when a rope might need replacing, moving from reactive maintenance to predictive maintenance. Good records also serve as proof of compliance for safety audits. Each entry should include date, inspector’s name, observations, and any actions taken.
How does lubrication help extend wire rope life?
Lubrication is critically important for wire rope health. It’s an investment that pays off significantly by prolonging your rope’s lifespan and ensuring safer operation. Many overlook its importance.
Lubrication significantly extends wire rope life by effectively reducing friction between individual wires, actively preventing corrosion within the rope structure, and consistently maintaining the rope’s essential flexibility.
Think of it like oil for your car engine. Without proper and consistent lubrication, internal components would grind, corrode, and fail rapidly.
Reducing Friction
When the rope bends and flexes, individual wires and strands move and rub against each other. Lubricant creates a protective film between these components. This film reduces metal-to-metal contact. Less friction means less abrasive wear on the wires. It also means less heat buildup. This directly translates to increased fatigue life. Effective lubrication ensures that all wires can slide past each other smoothly during operation.
Benefit of Lubrication | How it Helps | Impact on Rope Life |
---|---|---|
Reduces internal friction | Prevents individual wires from grinding against each other as rope bends | Significantly extends the rope’s overall fatigue life by reducing stress concentration |
Reduces external friction | Minimizes wear on the rope surface when in contact with sheaves and drums | Prolongs the abrasion resistance of the outer wires, maintaining full cross-section |
Dissipates heat | Lubricant can help carry away heat generated by friction | Prevents thermal degradation of the rope’s internal structure and lubricant itself |
Preventing Corrosion
Wire ropes are almost always made of steel. Steel is prone to rusting and corrosion when exposed to moisture, chemicals, saltwater, and other atmospheric elements. Lubricant coats the wires. It fills gaps between strands. This creates a protective barrier. This barrier prevents corrosive agents from reaching the bare steel. This is especially vital for marine wire ropes or those used in harsh, outdoor environments. Plastic impregnated ropes help delay the onset of corrosion by sealing the core. But external lubrication is still needed for the outer strands.
Maintaining Flexibility
A well-lubricated rope remains flexible. This is important for smooth operation over sheave and drum systems. Flexibility allows the rope to conform to the curvature of the sheave and drum grooves without undue stress on individual wires. A dry, stiff rope will experience much higher localized stresses. This accelerates fatigue and leads to premature wire breakage. Proper lubrication ensures that the rope’s core remains pliable. This allows the rope to distribute loads evenly across all strands and wires.
Application Methods
Applying lubricant correctly matters as much as choosing the right one. The goal is to ensure the lubricant penetrates to the rope’s core.
Method | Description | When to Use |
---|---|---|
Hand Application (Brush/Rag) | Simple, manual method, applying lubricant to the surface | Regular top-ups, small sections, where visual inspection is critical. Limited core penetration. |
Drip System | Continuous or intermittent dripping of lubricant onto a moving rope | For long ropes in continuous operation, ensures more consistent coverage. Requires setup. |
Pressure Lubrication (Pressure Sprayers, Bath/Flow Systems) | Forces lubricant into the rope under pressure, or runs rope through a bath | Provides deep penetration to the rope’s core. Best for thorough re-lubrication, less frequent but highly effective. |
Lubricating Sheaves | Using sheaves with built-in lubrication systems | Ideal for continuously lubricating the rope as it passes over frequently used sheaves. |
Always use a lubricant specifically designed for wire ropes. It should penetrate well, adhere to the wires, and not be sticky or attract excessive dirt and abrasives. Different operating environments (e.g., hot, cold, wet) require different lubricant properties.
Does proper storage affect wire rope lifespan?
Yes, how you store your wire rope matters a lot. Poor storage can damage a new rope even before it is installed and put into service. This can significantly shorten its lifespan and compromise its safety.
Proper storage directly affects wire rope lifespan by actively preventing corrosion, avoiding kinking, and mitigating various forms of material degradation before the rope is ever put into use.
I’ve seen brand new ropes ruined by incorrect storage. This represents a significant waste of resources, time, and potential safety risks. Preventing this is simple with good practices.
Preventing Corrosion
Moisture is the primary enemy during storage. Always store ropes in a dry, covered indoor area. Keep them elevated off the ground, ideally on sturdy racks or pallets. This prevents direct contact with damp concrete or other moisture sources. Ensure good air circulation. If storing outdoors, even temporarily, use waterproof covers that allow ventilation to prevent condensation. Also, ensure the rope itself is well-lubricated before long-term storage.
Avoiding Kinks and Bends
New ropes come spooled on reels or coiled. It is crucial to keep them in this original configuration until the moment of installation. Any improper unrolling or handling can induce permanent kinks or sharp bends. A kinked rope is scientifically proven to lose a significant portion of its strength (often 40-50% or more). This damage is non-reversible. It necessitates immediate replacement for safety. Never simply uncoil a rope by pulling it off the side of the coil; it must be rolled out.
Storage Best Practice | Why it Matters | Outcome |
---|---|---|
Store in dry, low-humidity environment | Prevents the formation of rust and pitting corrosion on wire surfaces | Preserves the rope’s original strength and prevents premature failure |
Elevated storage (on racks/pallets) | Prevents moisture absorption from floor, protects from spills | Protects bottom layers of rope from unseen damage, ensures uniform condition |
Store in original reel/coil | Maintains rope’s natural lay and prevents undesirable twisting or kinking | Ensures easy, safe, and proper unreeling/uncoiling, retaining full strength |
Protect from direct sunlight/UV | Prevents degradation of any plastic components (e.g., plastic impregnated ropes) | Maintains material integrity for specialized ropes, extends overall lifespan |
Avoid heavy impacts or crushing loads | Prevents physical deformation or crushing of inner strands/wires | Maintains roundness and structural integrity, crucial for smooth operation |
Protecting from Other Damage
Store ropes away from potential hazards. These include chemicals, extreme heat sources, open flames, and areas with heavy vehicle or foot traffic where they might be crushed or struck. A clean, organized storage area is best. Keep ropes covered if possibility of dust, dirt, or debris settling on them, especially if they are to be stored for extended periods. Dirt can become an abrasive when the rope is put into service.
Temperature Control
While not always feasible, avoiding extreme temperature fluctuations in the storage area is beneficial. Rapid changes can lead to condensation inside packaging. Also, very high temperatures can degrade certain types of lubricants or plastic components in specialized ropes. A stable, moderate ambient temperature is ideal for long-term storage of wire ropes.
Conclusion
Making your crane wire ropes last longer saves you money and keeps your operations safe. By choosing the right construction, inspecting often, lubricating regularly, and storing correctly, you ensure maximum lifespan for your ropes.