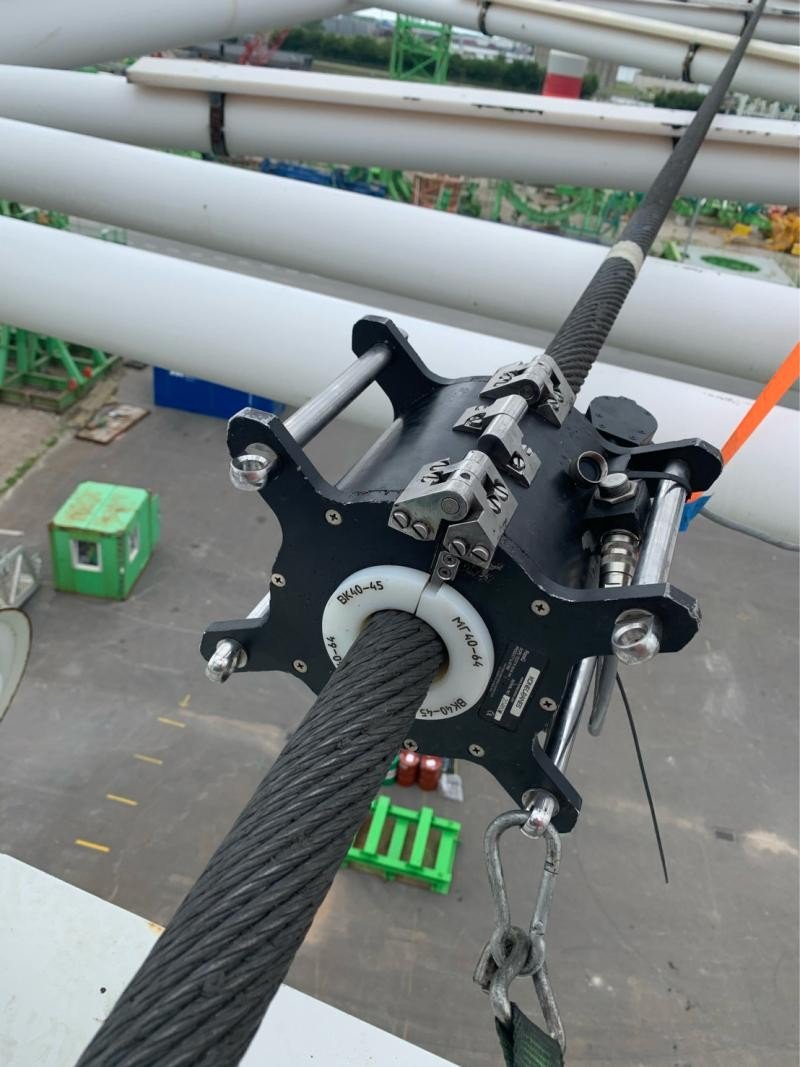
Are you worried about rope failures? Do you need a rope that won’t let you down? Weak ropes can cause big problems and safety risks.
The strongest ropes, especially those made from high-strength steel or advanced synthetics, can hold hundreds of tons of weight, far exceeding everyday needs.
Let me tell you, I’ve seen a lot of ropes in my time. From massive cranes to deep mines, the right rope makes all the difference. It’s not just about lifting; it’s about trust and safety.
What Materials Make the Strongest Ropes?
Choosing the right material is key for rope strength. Different materials offer different benefits. Understanding these is important for your projects.
The strongest ropes are often made from high-carbon steel wire, aramid fibers like Kevlar, or ultra-high molecular weight polyethylene (UHMWPE) like Dyneema.
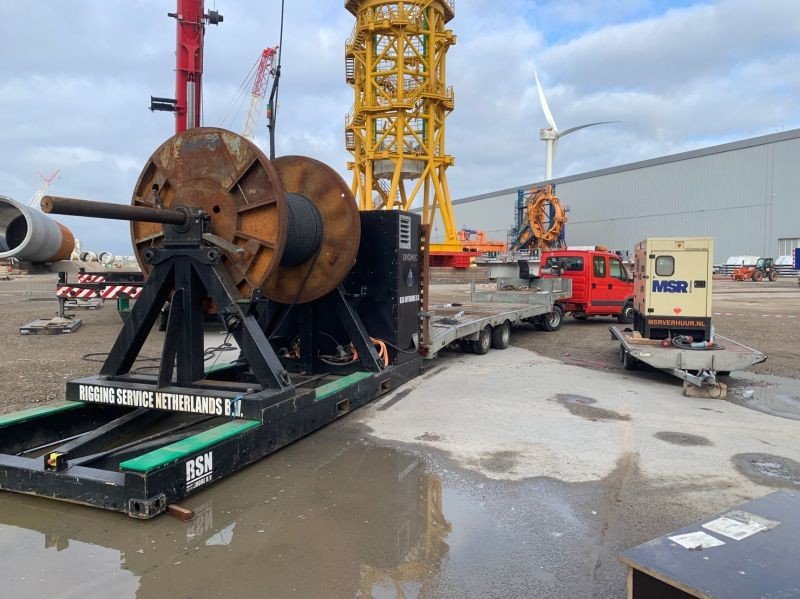
Dive Deeper: The Science Behind Rope Strength
Materials science plays a big role in rope strength. We look at things like tensile strength and ductility. For example, steel wire ropes are made from many thin wires. These wires are twisted together. This twisting makes the rope strong and flexible.
Different types of steel are used. High-carbon steel is very strong. It can handle heavy loads. Synthetic materials are also amazing. Aramid fibers, like Kevlar, are known for being very light but super strong. UHMWPE fibers, like Dyneema, float on water. But they are stronger than steel on a weight-for-weight basis.
Let’s look at a simple comparison of common rope materials:
Material Type | Typical Breaking Load (Approximate per unit area) | Key Benefits | Common Uses |
---|---|---|---|
High-Carbon Steel | Very High (e.g., 1770 N/mm²) | Extreme strength, durable | Cranes, bridges, mining |
UHMWPE (Dyneema) | Extremely High (e.g., 2000 N/mm² or more) | Lightweight, floats, low stretch | Marine, extreme sports, rigging |
Aramid (Kevlar) | Very High (e.g., 1500 N/mm²) | High strength-to-weight, heat res | Military, protective gear, specialized |
Polyester | Moderate (e.g., 600 N/mm²) | Good abrasion resistance, low cost | General purpose, docking, hauling |
Nylon | Moderate (e.g., 550 N/mm²) | Strong, good stretch, shock absorb | Tow lines, climbing, anchor lines |
We often combine these materials. For example, some steel ropes have a plastic core. This can protect the wires. It also increases strength. For galvanized wire rope, we add a zinc coating. This coating protects against rust. This makes the rope last longer, especially in wet places.
How Do Different Rope Constructions Affect Strength?
Rope construction is about how the wires or fibers are put together. This greatly impacts the rope’s total strength. It also affects its flexibility and wear resistance.
The construction, such as the number of strands, lays, and core type, fundamentally changes how a rope distributes load and resists breakage, thus affecting its ultimate strength.
Dive Deeper: Understanding Rope Anatomy
Think about a puzzle. Each piece fits together. Ropes are similar. They have different parts that work together. A wire rope typically has a core. Then it has strands wrapped around the core. Each strand is made of many individual wires.
The way these strands are twisted matters. We talk about “lay” direction. Regular lay means wires are twisted in one direction. Strands are twisted in the opposite direction. This makes a balanced rope. Lang lay means wires and strands are twisted in the same direction. This makes the rope more flexible. It also gives it better wear resistance. But it can be harder to handle.
Here’s a look at common wire rope constructions:
Construction Type | Description | Key Strength Impact | Typical Application |
---|---|---|---|
6×19 Class (e.g., 6×19, 6×36) | 6 strands, 19 or 36 wires per strand | Good balance of strength and flexibility | General industry, crane |
6×7 Class (e.g., 6×7) | 6 strands, 7 wires per strand | Stiff, good for abrasion, lower flexibility | Hoist lines, well drilling |
8×19 Class (e.g., 8×19, 8×36) | 8 strands, 19 or 36 wires per strand | More flexible than 6-strand, good for fatigue | Crane, elevator ropes |
19×7 (Non-rotating) | 19 strands, 7 wires per strand, counter-laid | High strength, resists rotation | Single-part line applications |
For marine wire rope, we often use specific designs. These designs resist saltwater corrosion. For elevator wire rope, we prioritize smooth operation. We also need very high safety factors. Mining wire rope needs to be extremely strong. It also needs to resist abrasion. This is because of underground conditions.
Why Are Certifications and Quality Control So Important for Rope Strength?
Certifications and strict quality control are not just paperwork. They are vital for safety and performance. They ensure a rope meets specific strength standards.
Certifications like EN12385-4 and third-party checks (BV, CE, RMRS, DNV, ABS) confirm a rope’s strength and reliability, validating its ability to hold intended loads safely.
Dive Deeper: Ensuring Trust and Safety
We believe in quality. Our factory has four production lines. We export to many countries. These include Singapore, Indonesia, and Australia. Every country has its own safety standards. This is why certifications are so important.
For example, EN12385-4 is a standard for steel wire ropes. It defines requirements for material, manufacturing, and testing. When a rope is certified, it means it has passed these tests. This gives customers confidence. They know the rope will perform as expected.
Here are some important certifications and what they mean:
Certification Abbreviation | Full Name / Issuing Body | Key Focus | Relevance to Rope Strength |
---|---|---|---|
EN12385-4 | European Standard for Steel Wire Ropes | General requirements for wire ropes | Defines minimum breaking force and safety factors |
BV | Bureau Veritas | Classification of ships, industrial asset cert | Verifies material quality and load-bearing capacity |
CE | Conformité Européenne | European Economic Area safety standard | Product meets EU health, safety, environmental req |
RMRS | Russian Maritime Register of Shipping | Certification for ships, marine equipment | Confirms suitability for maritime operations, strength |
DNV | DNV GL (Det Norske Veritas Germanischer Lloyd) | Global quality assurance and risk management | Audits manufacturing processes, product performance |
ABS | American Bureau of Shipping | Marine and offshore classification society | Ensures marine ropes meet specific safety and performance standards |
We offer BV, CE, RMRS, DNV, and ABS certificates. This is if a client needs them. We also offer customizable logos. This helps our clients brand their products. Our focus is on high quality. We ensure high tensile strength and high breaking load for all our products. We also provide options like plastic impregnation and galvanizing. This enhances durability and strength.
Conclusion
The strongest ropes blend advanced materials and precise construction. They are backed by strict quality checks. This ensures they can hold immense weight safely.