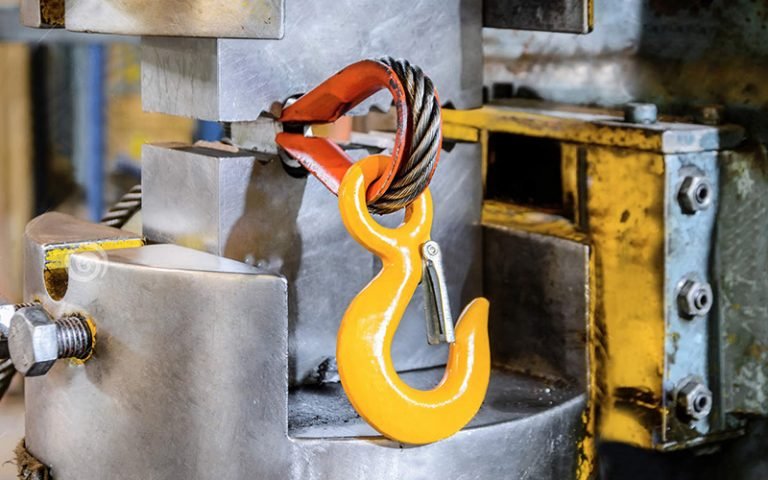
Does your wire rope break easily? Are you tired of unexpected failures? Get the right wire rope and boost your project success.
Choosing the right wire rope involves assessing load, environment, and application to ensure safety and efficiency in your operations.
I remember a time when a new client, who had worked with top German brands, came to me with a problem. They needed something reliable, fast. They were fed up with the uncertainty they faced.
What Factors Impact Wire Rope Performance and Durability?
Understanding wire rope performance is key. It affects how long your rope lasts. It also impacts how safe your operations are.
Many factors influence wire rope’s performance and durability, including material, construction, lubrication, and environmental conditions.
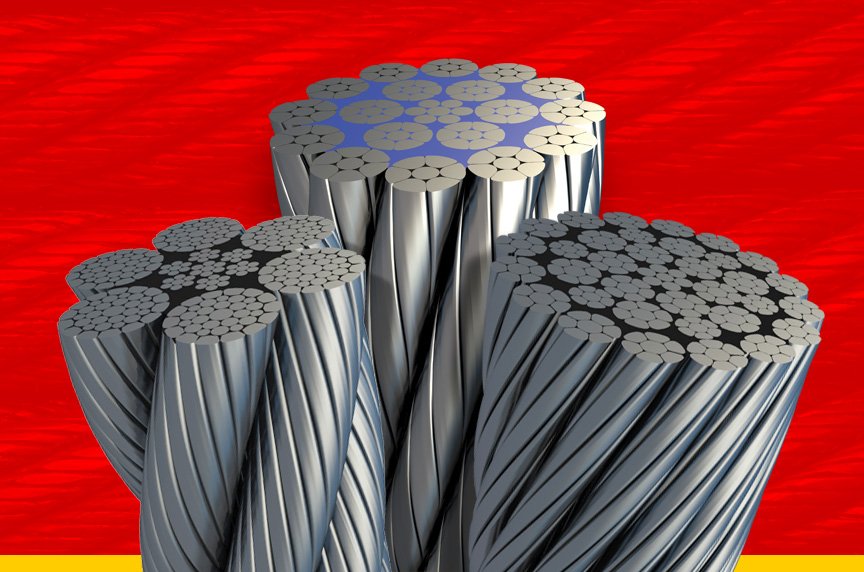
When we talk about wire rope performance, we look at many details. For example, a quality wire rope handles stress better. It resists wear and tear. This means fewer breakdowns. It also saves you money. We ensure our ropes meet high standards. They are built to last even in tough conditions.
Dive Deeper: Key Factors in Wire Rope Performance
1. Material Composition
The material used is vital. For example, carbon steel is strong. Stainless steel resists corrosion. Each material has its strengths. We use certified materials. This ensures high tensile strength. It also guarantees high breaking load.
Material Type | Key Feature | Best Use Case |
---|---|---|
Galvanized Steel | Corrosion resistance | Marine, outdoor applications |
Stainless Steel | High corrosion resistance, aesthetics | Food processing, architectural |
High Carbon Steel | High strength, durability | Cranes, mining, heavy lifting |
2. Rope Construction
How the rope is built matters. It affects flexibility and strength. Different constructions suit different tasks. We offer various constructions. This includes different strand patterns. We also offer different core types. Our ropes often comply with EN12385-4. This ensures top quality.
- Construction Types:
- 6×19: Good balance of flexibility and wear resistance.
- 6×36: More flexible, better for fatigue.
- 18×7: Non-rotating, good for single-part lines.
3. Lubrication
Lubrication protects the rope. It reduces friction. It prevents rust. Proper lubrication extends life. We use tested lubricants. This keeps our ropes running smoothly. Plastic impregnation is also available for some products. It offers extra protection.
4. Environmental Conditions
Where the rope is used impacts it. Saltwater causes rust. Extreme temperatures can weaken it. We consider these factors. Our ropes are built for tough environments. This includes marine and mining uses. We can provide specific certifications like DNV or ABS for marine applications.
How Can Customization Enhance Wire Rope Utility?
Customization makes wire ropes fit your needs. It increases efficiency. It also improves safety for specific jobs.
Customizing wire ropes through length, diameter, and special assemblies optimizes them for unique operational requirements and applications.
Often, standard ropes don’t perfectly fit. That’s why customization is important. We can adjust many features. This includes length and end fittings. It makes the rope ideal for your machine. This also means safer work.
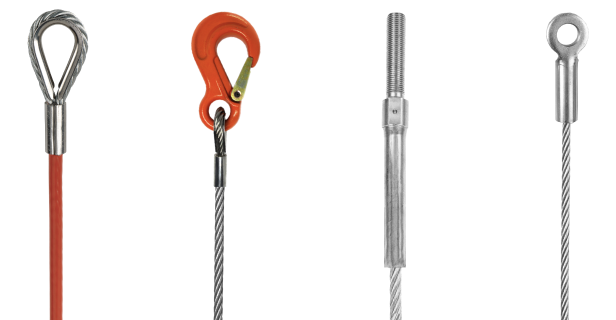
When I talk to clients like those in Australia, they often have very specific needs. They face unique challenges. Standard solutions do not always work. That is where our ability to customize comes in. We can tailor our products. This ensures they meet exact requirements. We can add a custom logo if needed. This adds a personal touch. It also reinforces your brand.
Dive Deeper: The Power of Customization
1. Tailored Dimensions
You might need a specific length. Or a precise diameter. We produce ropes to your exact size. This minimizes waste. It also maximizes performance. Our factory has four production lines. This allows for quick and accurate customization.
Dimension Type | Customization Option | Benefit |
---|---|---|
Length | Specific cutting to meters/feet | Prevents excess, precise fit |
Diameter | Varying sizes from common to specialized | Matching specific sheaves and drums |
Construction | Different lay types and number of strands | Optimizing flexibility or strength |
2. Specialized End Assemblies
Sometimes, the end of the rope needs a special fitting. This could be a thimble or a socket. We make custom assemblies. They fit your lifting gear perfectly. This ensures a strong connection. It also ensures a safe one. We offer specialized assemblies for various applications, from piling tools to cranes.
3. Surface Finish Customization
Do you need extra protection? We offer galvanized finishes. This prevents rust. It is great for outdoor use. Plastic impregnation is another option. It protects the core. This extends the rope’s life. These options provide enhanced durability in harsh conditions.
4. Certifications for Specific Industries
Different industries have different rules. For example, marine needs specific certificates. We provide BV & CE, RMRS, DNV, and ABS certificates. This shows our ropes meet global standards. It also ensures compliance for export.
Why is Quality Control Crucial for Wire Rope Users?
Quality control is critical. It guarantees safety. It also ensures product reliability. Poor quality ropes can lead to accidents.
Rigorous quality control in wire rope manufacturing ensures high tensile strength, breaking load, and compliance, preventing failures and enhancing safety.
When I talk about quality, I mean more than just words. It is about trust. It is about safety. Every rope we make goes through strict checks. Our commitment to quality protects your operations. It also protects your people.
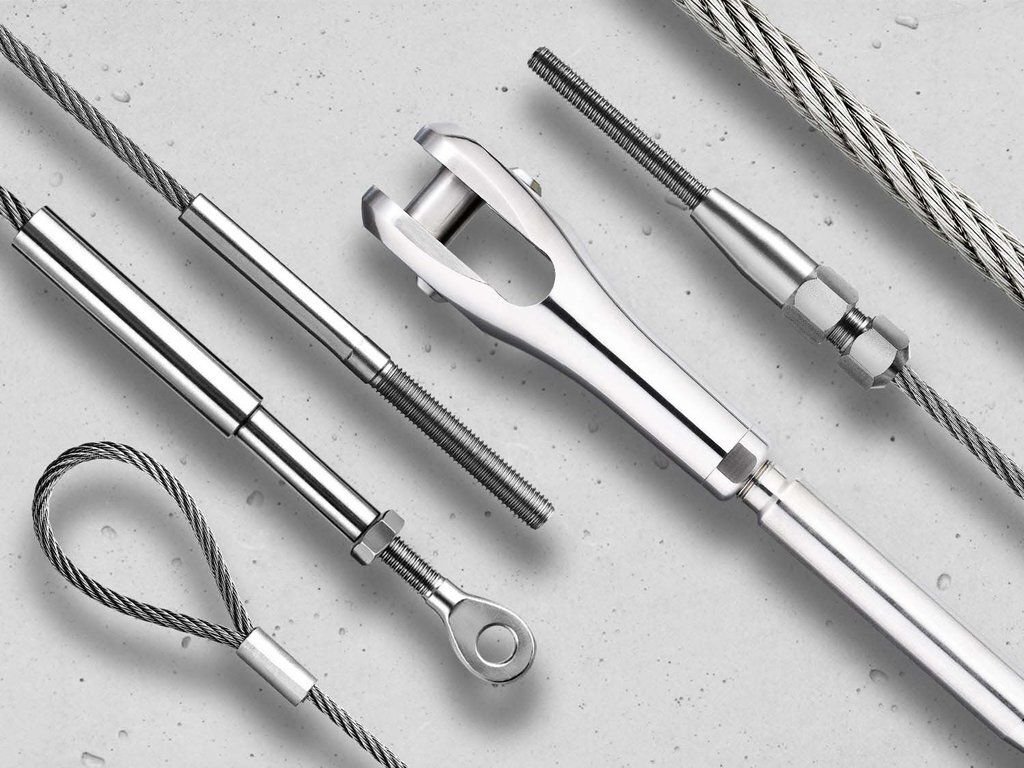
One of my clients emphasized strict quality control. He wanted proof. He had experienced issues before. For us, quality is not an option. It is a fundamental part of our process. We strive for excellence. This is from raw material to finished product. We ensure every rope meets high standards. We offer many certifications. This confirms our quality guarantee.
Dive Deeper: The Pillars of Quality Control
1. Material Sourcing and Testing
We start with raw materials. They are tested for purity and strength. This ensures a strong foundation. We only use high-grade steel. This prevents early failures. It also ensures consistent performance.
Test Type | Purpose | Standard |
---|---|---|
Tensile Test | Measures ultimate strength | ASTM, ISO |
Chemical Analysis | Verifies material composition | API, ASTM |
Hardness Test | Checks material resistance to indentation | Rockwell, Brinell |
2. In-Process Inspections
During production, we check every step. Our machines are precise. Our staff are well-trained. This finds any defects early. It ensures uniform quality. This includes monitoring drawing, stranding, and closing processes.
3. Final Product Testing
Before shipping, every rope is tested. We check breaking load. We verify dimensions. This ensures our ropes perform as promised. We provide test certificates. These are tangible proofs of quality.
4. Compliance and Certifications
We follow international standards. This includes EN12385-4. We also offer specific certificates. These include CE, RMRS, DNV, and ABS. These attest to our ropes’ global acceptance. They also confirm their suitability for critical applications.
What Are the Benefits of Partnering with a Direct Manufacturer?
Partnering with a direct manufacturer offers many benefits. You get better prices. You also get customized solutions.
Working with a direct manufacturer like us provides competitive pricing, direct communication, and tailored products, eliminating middlemen and improving efficiency.
When you buy from a factory, you get a direct line. No extra costs. No communication issues. This streamlines your purchasing. It also builds a stronger partnership.
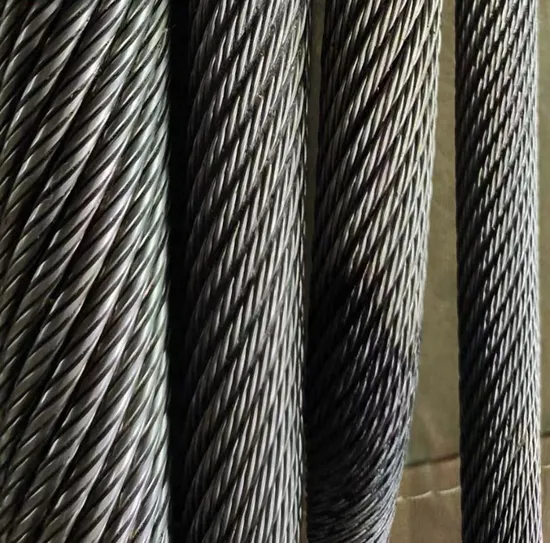
My factory has four production lines. We export to many countries. This includes Singapore, Indonesia, and Saudi Arabia. Our direct model works well. It allows us to be flexible. It also allows us to be responsive. A client once told me how much they valued direct contact. They got faster answers. They also got better service. This is what we offer.
Dive Deeper: Advantages of Direct Manufacturing Partnership
1. Cost Efficiency
Buying direct cuts out intermediaries. This means lower prices for you. There are no reseller markups. This helps your budget. It also increases your profit margins.
Purchasing Method | Cost Structure | Typical Savings |
---|---|---|
Distributor/Agent | Product Cost + Agent Fee + Margin | – |
Direct Manufacturer | Product Cost Only | 10-20% (estimated) |
2. Direct Communication and Support
You talk directly to the source. This means faster updates. You get accurate information. Any issues are resolved quickly. Our team is responsive. We are available by email or through our official website.
3. Customization Capabilities
As a manufacturer, we can customize. We can fulfill unique product requests. This includes specific lengths or materials. Our direct interaction ensures your exact needs are met. This is a huge advantage over distributors.
4. Quality Assurance and Transparency
We control the quality process. From start to finish. You get full transparency. We share our testing results. We provide all necessary certificates. This gives you peace of mind. You know exactly what you are getting.
5. Long-Term Partnership Potential
Direct relationships build trust. We aim for long-term partnerships. We understand your needs. We grow with your business. This is more than just a sale. It is a collaboration.
Conclusion
Choosing the right wire rope impacts safety and success. Focus on quality, customization, and direct suppliers. It ensures project efficiency and reliability.