Piling Rigs Wire Rope
High Performance Steel Wire Ropes For Piling Rigs
Piling rigs should feature exceptionally flexible leader kinematics, allowing for very high radii and inclinations in all directions. This capability ensures highly efficient piling, thereby enhancing the competitive position of operating companies. Choosing the right high-performance steel wire rope is crucial for the cost-effectiveness of these machines.
The flexibility of the leader kinematics is a game-changer for piling rigs, as it not only improves efficiency but also reduces operational costs by allowing precise control over the piling process.
Aulone high-performance steel wire ropes meet the stringent requirements for hoist ropes and auxiliary hoist ropes, such as high rotation resistance, extreme wear resistance, and high resistance to external operational influences like shock loads. These qualities are essential for maintaining performance and reliability in demanding conditions.
In the field of hoist and auxiliary hoist ropes, Aulone offers highly compacted, rotation-resistant high-performance steel wire ropes with extremely high minimum breaking loads, robustness, and flexibility. These ropes are successfully used in piling equipment, ensuring durability and efficiency. Additionally, our delivery program includes tested rope end terminations, such as button sockets for commercially available pouch sockets, solid thimbles, as well as tests and acceptance certificates. This comprehensive approach ensures that our products not only meet but exceed industry standards.
Tailored Piling Rigs Wire Ropes to Suit Your Needs!
Elevate your piling operations with Aulone’s tailored wire ropes, designed to meet the specific needs of your equipment and enhance your operational efficiency.
Available Sizes: Ranging from 8mm up to 50mm.
Tensile Strength: 1770, 1960, 2160mpa.
Specifications on Offer: EN12385-4, GB8918, YB/T5359 and specific customer requirements.
Surface Treatments: Options including hot galvanized, ungalvanized.
Special technology: Including multi-strand ropes, plastic impregnated, compacted, galvanized.
Structure:35WXK7, 15XK7, 35WXK7-EP, 24WXK7, etc.
Lay types: RHLL, LHLL
Certifications: All our ropes come with BV and CE certifications, providing you with the assurance of quality and compliance with international standards.
Hoist Ropes
Aulone offers a range of high-performance steel wire ropes designed specifically for hoist and auxiliary hoist applications in piling rigs. Our ropes are engineered to provide:
High Rotation Resistance: Prevents twisting and ensures stability during operations.
Extreme Wear Resistance: Ensures long service life, even in the toughest conditions.
High Breaking Load: Provides the strength needed to handle heavy loads safely.
Robustness and Flexibility: Combines durability with the flexibility required for efficient operation.
Customization and Certification:
Aulone provides tailored solutions to meet the specific needs of your piling equipment. Our ropes come with:
Tested Rope End Terminations: Options include button sockets for commercially available pouch sockets and solid thimbles.
Comprehensive Testing and Acceptance Certificates: Ensuring compliance with industry standards and customer requirements.
Benefits of Using Aulone Hoist Ropes:
Enhanced Efficiency: High-quality ropes reduce downtime and maintenance costs.
Increased Safety: Robust and reliable ropes minimize the risk of accidents and failures.
Cost-Effectiveness: Durable and long-lasting ropes contribute to lower operational costs.
Why Choose Aulone?
Proven Quality: Our ropes are rigorously tested to ensure they meet and exceed industry standards.
Complete Solutions: From end terminations to certification, we provide a comprehensive package for your hoisting needs.
Expertise and Innovation: We leverage advanced technology and expertise to deliver superior performance and reliability.
35WXK7 & 35WXK7-EP Compacted Wire Rope
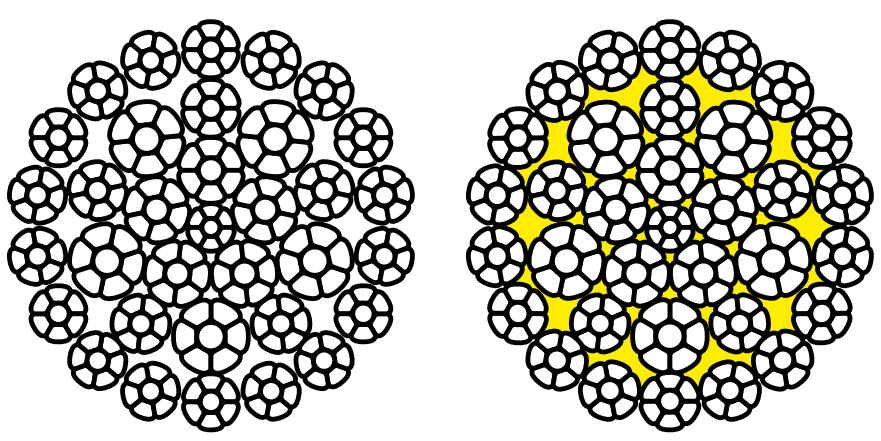
- 35WXK7 is a high performance compacted low rotational rope that combines varying multistrand rope designs to achieve excellent rotation resistance in high lift operations.
Multistrand Non-rotating Wire Ropes with Compacted Outer Strands, EN 12385-4
35WXK7 Advantage
- High tensile strength
- High abrasion resistance
- High fatigue failure resistance
- Expanded contact with bearing surface area
- Less wear of sheaves and capstans
35WXK7-EP Advantage
- High polymer filled and sealed steel reinforced plastic layer within the lubricating oil to make it longer.
- Resistance to outer strands of wire rope to squeeze;
- Non-rotation Recommended for high lifting operations
- High strength
- Reduced rope sheave wear
- Accurate diameter,recommended for multi-layer coiling
- Suitable for single part and multi-part reeving Long service life
Diameter | Approx. weight (kg/100m) | Tensile strength (MPa) | ||
(mm) | 1770 | 1960 | 2160 | |
Minimum breaking load (kN) | ||||
8 | 33 | 51 | 56 | 62 |
9 | 41 | 65 | 71 | 79 |
10 | 51 | 80 | 88 | 97 |
11 | 62 | 96 | 107 | 118 |
12 | 73 | 115 | 127 | 140 |
13 | 86 | 135 | 149 | 164 |
14 | 100 | 156 | 173 | 191 |
15 | 115 | 179 | 198 | 219 |
16 | 131 | 204 | 226 | 249 |
17 | 147 | 230 | 255 | 281 |
18 | 165 | 258 | 286 | 315 |
19 | 184 | 288 | 318 | 351 |
20 | 204 | 319 | 353 | 389 |
21 | 225 | 351 | 389 | 429 |
22 | 247 | 386 | 427 | 470 |
23 | 270 | 421 | 467 | 514 |
24 | 294 | 459 | 508 | 560 |
25 | 319 | 498 | 551 | 608 |
26 | 345 | 538 | 596 | 657 |
27 | 372 | 581 | 643 | 709 |
28 | 400 | 624 | 691 | 762 |
29 | 429 | 670 | 742 | 817 |
30 | 459 | 717 | 794 | 875 |
31 | 490 | 765 | 848 | 934 |
32 | 522 | 816 | 903 | 995 |
35 | 625 | 976 | 1080 | 1191 |
36 | 661 | 1032 | 1143 | 1260 |
39 | 776 | 1211 | 1342 | 1478 |
40 | 816 | 1274 | 1411 | 1555 |
Auxiliary Hoist Ropes
Aulone offers a range of high-performance steel wire ropes specifically designed for auxiliary hoist applications in piling rigs. Our ropes are engineered to provide:
High Rotation Resistance: Prevents twisting and ensures stability during operations.
Extreme Wear Resistance: Ensures long service life, even in the toughest conditions.
High Breaking Load: Provides the strength needed to handle heavy loads safely.
Robustness and Flexibility: Combines durability with the flexibility required for efficient operation.
Customization and Certification:
Aulone provides tailored solutions to meet the specific needs of your piling equipment. Our ropes come with:
Tested Rope End Terminations: Options include button sockets for commercially available pouch sockets and solid thimbles.
Comprehensive Testing and Acceptance Certificates: Ensuring compliance with industry standards and customer requirements.
Benefits of Using Aulone Auxiliary Hoist Ropes:
Enhanced Efficiency: High-quality ropes reduce downtime and maintenance costs.
Increased Safety: Robust and reliable ropes minimize the risk of accidents and failures.
Cost-Effectiveness: Durable and long-lasting ropes contribute to lower operational costs.
35WXK7 & 35WXK7-EP Compacted Wire Rope
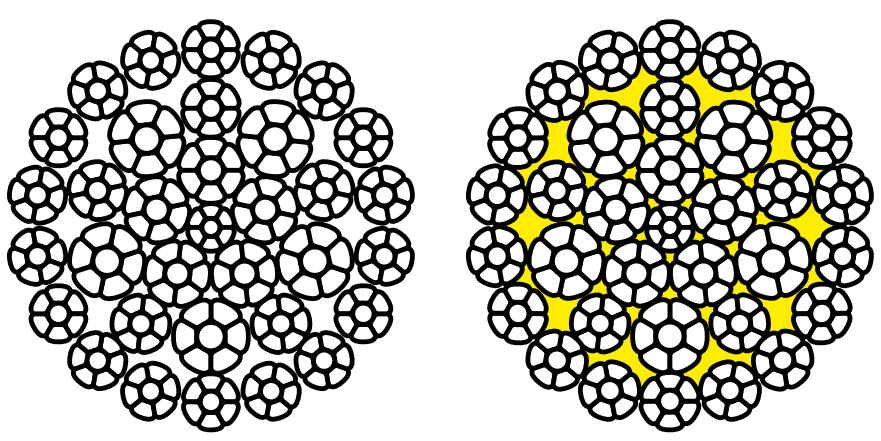
- 35WXK7 is a high performance compacted low rotational rope that combines varying multistrand rope designs to achieve excellent rotation resistance in high lift operations.
Multistrand Non-rotating Wire Ropes with Compacted Outer Strands, EN 12385-4
35WXK7 Advantage
- High tensile strength
- High abrasion resistance
- High fatigue failure resistance
- Expanded contact with bearing surface area
- Less wear of sheaves and capstans
35WXK7-EP Advantage
- High polymer filled and sealed steel reinforced plastic layer within the lubricating oil to make it longer.
- Resistance to outer strands of wire rope to squeeze;
- Non-rotation Recommended for high lifting operations
- High strength
- Reduced rope sheave wear
- Accurate diameter,recommended for multi-layer coiling
- Suitable for single part and multi-part reeving Long service life
Diameter | Approx. weight (kg/100m) | Tensile strength (MPa) | ||
(mm) | 1770 | 1960 | 2160 | |
Minimum breaking load (kN) | ||||
8 | 33 | 51 | 56 | 62 |
9 | 41 | 65 | 71 | 79 |
10 | 51 | 80 | 88 | 97 |
11 | 62 | 96 | 107 | 118 |
12 | 73 | 115 | 127 | 140 |
13 | 86 | 135 | 149 | 164 |
14 | 100 | 156 | 173 | 191 |
15 | 115 | 179 | 198 | 219 |
16 | 131 | 204 | 226 | 249 |
17 | 147 | 230 | 255 | 281 |
18 | 165 | 258 | 286 | 315 |
19 | 184 | 288 | 318 | 351 |
20 | 204 | 319 | 353 | 389 |
21 | 225 | 351 | 389 | 429 |
22 | 247 | 386 | 427 | 470 |
23 | 270 | 421 | 467 | 514 |
24 | 294 | 459 | 508 | 560 |
25 | 319 | 498 | 551 | 608 |
26 | 345 | 538 | 596 | 657 |
27 | 372 | 581 | 643 | 709 |
28 | 400 | 624 | 691 | 762 |
29 | 429 | 670 | 742 | 817 |
30 | 459 | 717 | 794 | 875 |
31 | 490 | 765 | 848 | 934 |
32 | 522 | 816 | 903 | 995 |
35 | 625 | 976 | 1080 | 1191 |
36 | 661 | 1032 | 1143 | 1260 |
39 | 776 | 1211 | 1342 | 1478 |
40 | 816 | 1274 | 1411 | 1555 |
Your Ultimate Guide to Acquiring Piling Rigs Wire Rope
When it comes to piling rigs, the selection of wire rope is critical. The right wire rope ensures efficient operation, safety, and the longevity of your equipment. Here’s your comprehensive guide to understanding and acquiring the right wire rope for piling rigs.
Table of contents
Chapt 1
Understanding Piling Rigs Wire Rope Requirements
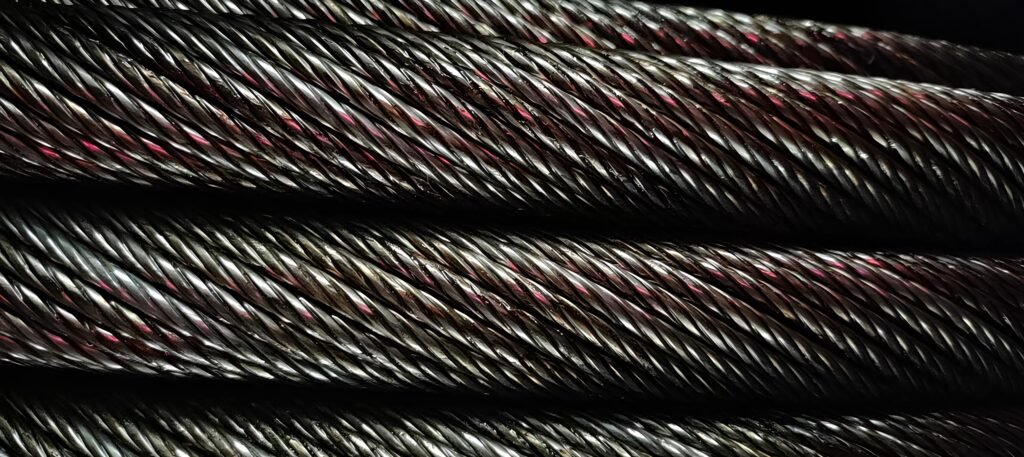
Selecting the correct wire rope for piling rigs is essential for both the safety and efficiency of your operations. Piling rigs are powerful machines used in construction to drive piles deep into the ground, and they demand wire ropes that can handle heavy loads and harsh working conditions. Understanding the specific requirements for wire rope in these applications ensures better performance and longer service life.
1. Load Capacity
The primary function of the wire rope in piling rigs is to handle immense loads, whether it’s for lifting, pulling, or supporting the rig itself. The wire rope must have a high breaking strength to withstand the maximum load applied during the rig’s operations.
- Safety Factor: It’s crucial to apply a safety factor, typically ranging from 5:1 to 10:1, to account for dynamic forces, shock loads, and potential overloads.
- Breaking Load: The minimum breaking load of the wire rope must exceed the maximum load expected in the piling rig operation.
2. Fatigue Resistance
Piling rigs expose wire ropes to repetitive bending and flexing, which can cause fatigue over time. To ensure long service life, wire ropes used in piling rigs must have high fatigue resistance.
- Bending Fatigue: Occurs when wire ropes are constantly bent over sheaves or drums. The wire rope’s design, such as its construction and strand pattern, can influence fatigue resistance.
- Material Quality: High-quality steel wire ropes with finer strands typically offer better fatigue resistance.
3. Abrasion Resistance
Wire ropes used in piling rigs are exposed to friction from contact with the drum, sheaves, and potentially the ground. Abrasion resistance is vital to prevent premature wear.
- Outer Wire Thickness: Ropes with thicker outer wires or specialized coatings can better resist abrasion. This is critical when the rope repeatedly comes into contact with abrasive surfaces.
- Galvanized Coating: Adding a protective galvanized coating can extend the life of the wire rope in corrosive or abrasive environments.
4. Tensile Strength and Durability
For piling rig applications, the wire rope must be strong enough to withstand high tensile forces without stretching or deforming under load. High-tensile steel is commonly used for its superior strength and durability.
- Tensile Strength: This is the maximum stress the rope can take before breaking. The wire rope for piling rigs should have a high tensile strength to handle the operational stresses of the machine.
- Wire Rope Construction: Wire ropes with multi-strand configurations (e.g., 6XK36WS-IWRC) are commonly used for their excellent balance of tensile strength, flexibility, and durability.
5. Rotational Stability
For hoisting operations in piling rigs, non-rotating wire ropes are often recommended. These ropes are engineered to minimize rotation under load, preventing twisting or kinking during operation.
- Non-Rotating Wire Rope (35WXK7): This configuration is ideal for hoist ropes on piling rigs as it prevents unwanted spinning or twisting, which could affect the rig’s performance.
- Stability under Load: Ensures the rope remains steady even during heavy lifting, reducing the risk of accidents or equipment damage.
6. Flexibility
Wire ropes for piling rigs need a balance of strength and flexibility. A flexible rope is easier to handle, can smoothly run over pulleys, and reduces the likelihood of damage during use.
- Strand Composition: Flexible wire ropes usually feature a higher number of smaller wires in each strand, allowing them to bend more easily around sheaves and drums without compromising strength.
7. Corrosion Resistance
Piling rigs often operate in environments where exposure to water, mud, and other corrosive materials is common. Wire ropes need to be protected against corrosion to maintain their structural integrity and prolong their service life.
- Galvanized Ropes: These are coated with zinc to resist rust and corrosion, making them suitable for outdoor construction projects, especially in marine or wet conditions.
- Plastic-Coated Ropes: Ropes like 8XK26WS-EPIWRC, 35WXK7-EPWSC offer additional protection with plastic coatings, making them even more resistant to corrosion and abrasion.
8. Certification and Standards
Wire ropes used in piling rigs should meet internationally recognized safety and quality standards to ensure they perform reliably under harsh conditions.
- EN 12385: European standard specifying safety requirements for steel wire ropes used in lifting and construction.
Conclusion
The right wire rope for piling rigs must meet stringent requirements for load capacity, fatigue resistance, abrasion resistance, tensile strength, and flexibility. By selecting ropes with the correct specifications and certifications, you ensure the safe and efficient operation of your piling rig. A careful understanding of these factors will help in making an informed choice and extending the lifespan of your wire rope.
For assistance in acquiring certified wire ropes for your piling rigs, Aulone offer customizable solutions that meet the most rigorous industry standards.
Chapt 2
How Do You Control The Quality Of Piling Rig Wire Rope?
At Aulone, ensuring the highest quality of our wire ropes for piling rigs is our top priority. Our rigorous quality control process spans every stage of production, from raw material selection to final testing. Here’s how we maintain exceptional standards in the manufacture of piling rig wire ropes.
1. Raw Material Selection and Inspection
We start by selecting only the finest high-carbon steel for our wire ropes. This ensures that the ropes have the necessary strength and durability for heavy-duty applications like piling rigs.
- Chemical Composition Analysis: We perform a thorough analysis of the steel’s chemical composition to ensure it has the right balance of carbon, manganese, and other essential elements. This guarantees optimal performance in terms of strength and flexibility.
- Surface Defect Inspection: We inspect raw steel using ultrasonic testing and visual inspection to detect any surface imperfections like cracks or rust. This step ensures the raw material meets our high standards before moving forward in the production process.
2. Precision in Wire Rope Construction and Stranding
Our wire ropes are built to handle extreme loads and harsh conditions. We pay close attention to the details during the construction phase.
- Consistent Diameter Control: We use precision laser measurements to monitor the diameter of individual wires throughout the manufacturing process. Maintaining uniform diameter is key to ensuring even load distribution across the rope.
- Tension Control: During the stranding process, we carefully control tension to prevent kinks or uneven winding. This helps maintain the structural integrity of the rope and ensures long-term performance.
- Sampling and Testing: Regular sampling and testing of strands during production help us catch any issues early and ensure the rope construction meets our rigorous quality benchmarks.
3. Tensile Strength and Breaking Load Testing
At Aulone, we understand that the tensile strength of wire ropes is critical for safe and efficient piling rig operations.
- Tensile Strength Testing: We conduct tensile strength tests on every batch of wire ropes to verify that they meet or exceed the required load-bearing capacity. Our ropes are tested to ensure they can withstand the high tension needed for piling rigs without failure.
- Breaking Load Verification: Each wire rope is tested to determine its breaking load, ensuring it meets the stringent safety factors needed for heavy construction applications.
4. Fatigue Resistance Testing
Piling rigs put wire ropes through repetitive flexing and high-stress conditions. We ensure our ropes are built to last through extensive fatigue testing.
- Bend Fatigue Testing: We conduct bend fatigue tests where our wire ropes are bent over sheaves multiple times under load. This simulates real-world usage and allows us to gauge how well the rope resists fatigue over time.
- Dynamic Load Testing: Our ropes undergo dynamic load testing to replicate the repeated lifting and lowering actions of piling rigs. This helps ensure the ropes can handle fluctuating loads without degrading in performance.
5. Abrasion and Wear Resistance Testing
Wire ropes used in piling rigs face constant friction and wear. At Aulone, we take extra steps to ensure our ropes are built to resist abrasion.
- Abrasion Testing: We simulate abrasive conditions by running the wire rope over rough surfaces to measure wear resistance. Our ropes are designed with thicker outer wires or protective coatings to minimize abrasion.
- Surface Inspection: After testing, we conduct a detailed visual and microscopic inspection to check for any signs of surface wear, broken wires, or other damage.
6. Non-Destructive Testing (NDT)
We use advanced non-destructive testing methods to detect internal defects in our wire ropes, ensuring safety and reliability.
- Magnetic Rope Testing (MRT): Our ropes undergo magnetic rope testing to identify any internal broken wires or corrosion that may not be visible on the surface.
- Ultrasonic Testing (UT): We also use ultrasonic testing to detect cracks or voids within the rope that could compromise its performance.
7. Corrosion Resistance Testing
Given that wire ropes often operate in harsh, outdoor environments, corrosion resistance is essential. At Aulone, we take several steps to protect our ropes against rust and corrosion.
- Galvanization Testing: For galvanized ropes, we test the thickness and uniformity of the zinc coating to ensure proper corrosion resistance, especially in marine or damp environments.
- Salt Spray Test: We subject our ropes to accelerated corrosion testing using a salt spray chamber. This ensures that the ropes can withstand exposure to moisture and chemicals without corroding prematurely.
- Plastic Coating Integrity Testing: For plastic-coated ropes, we verify the coating’s thickness, flexibility, and adhesion to make sure it can protect the wire from harsh environmental conditions.
8. Flexibility and Rotation Testing
For applications like piling rigs, flexibility and rotation resistance are key. We ensure that our wire ropes are easy to handle while maintaining their structural integrity.
- Flexibility Test: Our ropes are bent over pulleys to assess their flexibility, ensuring they can move smoothly without developing kinks or cracks.
- Rotation Testing: Non-rotating wire ropes like our 35WXK7 are tested under load to verify they won’t twist or rotate, which is essential for safety and performance in lifting applications.
9. Ongoing Inspections and Maintenance
Quality control doesn’t end when the wire rope leaves our facility. We recommend regular inspections and proper maintenance to extend the lifespan of your wire ropes.
- Routine Visual Inspections: Regular inspections for wear, corrosion, and damage help identify issues early, reducing the risk of rope failure.
- Lubrication: Proper lubrication minimizes internal friction between the strands, which helps extend the life of the wire rope.
- Replacement Guidelines: We provide clear guidelines for wire rope replacement based on signs of wear, breaking strength reduction, and accumulated usage cycles.
Conclusion
At Aulone, we control the quality of our piling rig wire ropes with precision and care. From raw material selection to rigorous testing processes, we ensure that our ropes meet the highest standards of safety, durability, and performance. Our commitment to quality helps us deliver wire ropes that you can rely on for even the most demanding applications.
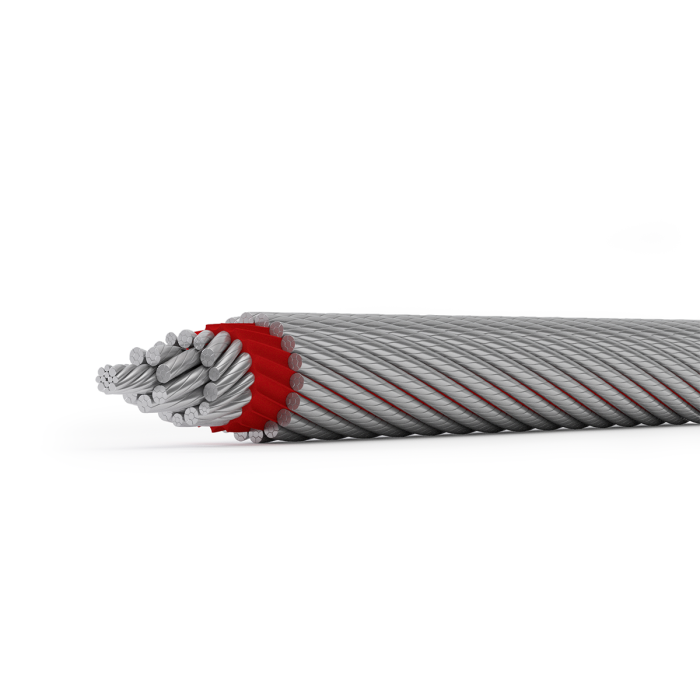
Chapt 3
Why Choose Aulone‘s Piling Rigs Wire Rope?
When it comes to wire ropes for piling rigs, Aulone is the trusted name you can rely on. Our ropes are designed to withstand the toughest conditions, ensuring safety, performance, and durability. Here are the key reasons why choosing Aulone for your piling rig wire ropes is the best decision:
Unmatched Quality and Precision Manufacturing
At Aulone, quality comes first. We use only premium high-carbon steel and follow stringent manufacturing processes to produce wire ropes that exceed industry standards. Our ropes are crafted with precision, ensuring high load-bearing capacity, superior fatigue resistance, and maximum durability.
- High Strength: Our ropes are engineered to handle the extreme loads of piling rigs without compromising on safety.
- Tight Tolerances: We control the diameter and tension during manufacturing to guarantee uniform performance and reduce the risk of failure.
Rigorous Testing for Superior Performance
We put our wire ropes through a series of rigorous tests to ensure they meet the demands of heavy-duty piling rigs. From tensile strength testing to fatigue resistance, each rope is tested to perform reliably under high stress.
- Tensile Strength and Breaking Load Testing: Every rope is tested to ensure it can handle the toughest loads with a high safety margin.
- Fatigue and Abrasion Resistance: Our ropes are designed to withstand repeated bending and harsh abrasion, giving them a longer lifespan in demanding environments.
Customizable Solutions for Specific Needs
At Aulone, we understand that every project has unique requirements. That’s why we offer customizable wire ropes designed specifically for piling rigs, ensuring they meet your exact operational needs.
- Non-Rotating Ropes: For applications that require stability and minimal twisting, we offer non-rotating wire ropes like 35WXK7.
- Plastic-Coated Ropes: For enhanced corrosion resistance, our plastic-coated ropes provide additional protection, ideal for wet or corrosive environments.
Advanced Corrosion Protection for Longevity
Piling rigs often operate in harsh environments where corrosion can compromise the integrity of the wire rope. At Aulone, we take extra measures to ensure our ropes are built to last, even in the most challenging conditions.
- Galvanized and Plastic-Coated Options: We offer both galvanized and plastic-coated ropes that provide excellent corrosion resistance in marine or damp conditions.
- Proven Corrosion Resistance: Our ropes undergo extensive corrosion testing, including salt spray tests, to ensure they perform reliably in corrosive environments.
Commitment to Safety and Reliability
Safety is our top priority. We know that equipment failure can lead to costly downtime or dangerous situations, especially in piling rig operations. That’s why we emphasize rigorous quality control and testing to deliver wire ropes you can trust.
- Non-Destructive Testing: We use advanced magnetic rope testing (MRT) and ultrasonic testing (UT) to detect any internal defects that could compromise safety.
- Reliable Performance: Our ropes are designed to handle extreme stress, ensuring they perform safely and reliably in the field.
Expert Support and Service
At Aulone, we go beyond just supplying wire ropes. Our team of experts is here to help you select the right rope for your specific piling rig application. We offer ongoing support and advice to ensure you get the most out of your investment.
- Technical Expertise: Our team has years of experience in wire rope manufacturing and can provide expert guidance on choosing the right product for your needs.
- Customer Service: We pride ourselves on delivering excellent customer service, ensuring you receive prompt support before, during, and after your purchase.
Proven Track Record in the Industry
Aulone has built a solid reputation for supplying high-quality wire ropes to a wide range of industries, including construction, marine, and heavy lifting. Our ropes are trusted by industry leaders around the world for their durability and performance.
- Trusted by Major Companies: We’ve supplied wire ropes for large-scale construction projects and piling operations, earning the trust of our clients through consistent quality and reliability.
- Long-Term Reliability: Our ropes are built to last, giving you the peace of mind that your equipment will operate safely and efficiently for years to come.
Conclusion
Choosing Aulone means choosing superior quality, reliability, and performance. Our wire ropes for piling rigs are designed to meet the toughest challenges, withstanding heavy loads, abrasive conditions, and harsh environments. Whether you need non-rotating ropes for stability or corrosion-resistant ropes for long-term durability, we have the right solution for your piling rig needs.
Contact us today to learn more about our customizable options and how we can help improve the safety and performance of your operations.
Chapt 4
What are the signs that a wire rope needs to be replaced?
Wire ropes used in piling rigs or other heavy-duty applications experience constant stress and wear. Regular inspection is crucial to prevent equipment failure, accidents, or costly downtime. Below are the key signs that indicate a wire rope needs to be replaced:
1. Broken Wires
One of the most common and obvious signs of wear is the presence of broken wires. Broken wires can compromise the strength and integrity of the wire rope.
- Number of Broken Wires: According to industry standards like ISO 4309, if more than 10% of the wires in any rope section are broken, the rope should be replaced.
- Concentration of Breaks: If broken wires are concentrated in a short length of the rope (typically one rope lay length), it suggests localized damage, and the rope may be unsafe to use.
- Location of Breaks: Breaks near the rope’s terminations or at points where the rope repeatedly bends over sheaves are especially dangerous.
2. Abrasion and Wear
Abrasion occurs when the rope runs over rough surfaces or through pulleys, wearing down the outer wires.
- Outer Wire Flattening: If the outer wires have become visibly flattened or worn down, it reduces the rope’s diameter and strength. Excessive wear can lead to broken strands or internal damage.
- Loss of Diameter: Significant reduction in the rope’s overall diameter (more than 10% of the original size) is a clear sign that it needs to be replaced. This may be caused by wear, corrosion, or core failure.
3. Corrosion
Corrosion is a serious issue that weakens the wire rope over time, especially in harsh environments such as marine or industrial applications.
- Rust and Discoloration: Visible rust or discoloration on the surface of the rope can indicate deeper corrosion inside the rope, especially if the rope is not adequately protected or lubricated.
- Pitting: Corrosion can cause pitting on the surface of the wires, which reduces their load-bearing capacity and increases the risk of wire breaks.
- Internal Corrosion: Even if the outer wires appear intact, corrosion can occur internally, especially in ropes that aren’t adequately lubricated. This can be detected through magnetic or ultrasonic testing.
4. Kinks and Deformations
Kinks, twists, or bends in the wire rope indicate improper handling or overloading and can severely reduce the rope’s strength.
- Kinks: Kinks occur when the rope is improperly loaded or wound, causing permanent deformation in the wire strands. Kinks disrupt the alignment of the strands, leading to uneven stress distribution and premature failure.
- Crushing: Crushing happens when the rope is subjected to excessive pressure, flattening or distorting the rope. This can happen when the rope is improperly spooled on the drum or forced through sheaves that are too small.
- Birdcaging: A birdcage occurs when the rope’s strands separate and bulge outward, often due to sudden shock loading or twisting. Birdcaging weakens the rope and is a clear sign that it should be replaced.
5. Core Failure
The core of a wire rope plays a critical role in maintaining its structural integrity. Core failure can be difficult to detect but is a major reason for rope replacement.
- Wire Rope Core Protrusion: If the core is protruding from the rope or has become damaged, the entire rope is compromised and should be replaced immediately.
- Loose or Swollen Rope: A loose, swollen, or distorted rope can indicate internal core failure. In ropes with fiber cores, excessive swelling may indicate core degradation, while in steel-core ropes, it may suggest internal wire failure or misalignment.
6. Reduction in Flexibility
A wire rope that has become stiff or less flexible than usual may be experiencing internal damage or core failure.
- Stiffness: Over time, wire ropes can lose their flexibility due to internal wear, core damage, or corrosion. A reduction in flexibility can make the rope harder to handle and more prone to breakage.
- Visible Wear at Bending Points: Ropes that are used frequently over sheaves or in applications requiring bending can suffer from excessive wear at the bending points, causing them to become less flexible and more susceptible to breakage.
7. Heat Damage
Wire ropes exposed to excessive heat, whether from environmental conditions or contact with hot surfaces, can suffer damage that significantly weakens their strength.
- Discoloration: Heat can cause the rope’s surface to discolor, typically turning blue or black. This is a sign that the rope’s strength has been compromised, and it should be replaced.
- Brittleness: Heat exposure can make the rope’s wires brittle, increasing the likelihood of breaks under normal load conditions.
8. Incorrect or Insufficient Lubrication
Proper lubrication is essential to prevent internal friction and wear. If the rope appears dry, it may lead to premature wear and internal corrosion.
- Dry or Rusted Surface: A rope that appears dry or rusted is likely not receiving adequate lubrication, which can cause the wires to grind against each other internally, accelerating wear and reducing the rope’s lifespan.
- Internal Friction: If you notice that the wire rope is becoming unusually hot during operation, it could indicate increased internal friction due to lack of lubrication.
Conclusion
Wire ropes are critical components in piling rigs and other heavy machinery, and their integrity directly affects safety and operational efficiency. Regular inspection and monitoring of these key signs—broken wires, abrasion, corrosion, deformations, core failure, and more—are essential to ensure timely replacement. At Aulone, we always recommend proactive maintenance and using high-quality, properly inspected wire ropes to avoid accidents and minimize downtime. If you notice any of these signs, it’s time to replace your wire rope to maintain the safety and efficiency of your operations.
Chapt 5
What is bird-caging in wire ropes, and how can you prevent it?
Bird-caging is a common and potentially dangerous deformation in wire ropes that occurs when the individual strands of the rope separate and bulge outward, resembling the shape of a birdcage. This type of damage usually results from improper handling, overloading, or sudden shock loading, which causes the internal structure of the rope to become misaligned. Bird-caging significantly weakens the wire rope and can lead to failure, making it critical to detect and address it early.
Causes of Bird-Caging
Shock Loading: When the rope is subjected to sudden or excessive forces, such as dropping a load or applying a jerking force, the internal strands can shift, leading to bird-caging.
Overloading: If the wire rope is used to lift or support loads beyond its rated capacity, the internal wires may be forced out of alignment, causing the strands to separate and form a birdcage.
Incorrect Tensioning: Uneven tension in the rope, either during installation or operation, can cause localized stress, leading to deformation and bird-caging.
Improper Handling: Mishandling the rope during installation or transportation, such as pulling the rope off a stationary reel or dragging it along rough surfaces, can cause internal damage that leads to bird-caging.
Improper Spooling or Winding: Incorrect spooling of the wire rope onto the drum with uneven tension or poor alignment can cause uneven stress, contributing to bird-caging.
How to Prevent Bird-Caging in Wire Ropes
Preventing bird-caging is critical to maintaining the safety and longevity of wire ropes. Here are the key measures to avoid this type of damage:
1. Use Proper Tension and Load Control
Avoid Overloading: Ensure that the wire rope is used within its rated load capacity, including an appropriate safety factor. Overloading increases the risk of bird-caging by overstressing the rope.
Gradual Load Application: Apply loads gradually rather than subjecting the rope to sudden or shock loading. Abrupt force application can cause the internal strands to shift and lead to bird-caging.
Monitor Tension: When installing or using the rope, maintain even tension to avoid localized stresses. Use tension control devices during installation to ensure smooth and uniform tension distribution.
2. Correct Handling and Installation
Use Proper Reeling Techniques: Always reel the wire rope off the spool in a controlled manner. Avoid pulling the rope off a stationary reel, which can twist and deform the strands. Use a rotating reel or spooler to unwind the rope smoothly.
Avoid Sharp Bends: Handle the rope carefully during transportation and installation to prevent kinks or sharp bends. Ensure that the rope is never bent around radii smaller than the minimum recommended for its diameter.
Use Appropriate Sheave Sizes: Ensure the sheaves and pulleys in your system are correctly sized for the diameter of the wire rope. Sheaves that are too small can induce bending stress, increasing the likelihood of bird-caging.
3. Proper Spooling and Winding
Correct Winding Direction: Wind the rope onto the drum in the correct direction according to the rope’s lay (right-hand or left-hand lay). Incorrect winding can cause twisting and internal misalignment, leading to bird-caging.
Even Tension During Spooling: Ensure that the rope is spooled evenly on the drum with consistent tension. Uneven winding can cause layers to overlap or uneven pressure points, which may lead to bird-caging.
Avoid Cross-Layering: If winding the rope in multiple layers on the drum, make sure the layers are uniform and tightly packed. Cross-layering can create pressure points that deform the internal structure.
4. Routine Inspection and Maintenance
Regular Visual Inspections: Regularly inspect the wire rope for signs of wear, deformation, and bird-caging. Early detection allows you to replace the rope before it poses a significant safety risk.
Check for Uneven Wear: Uneven wear or tension can cause localized stress, leading to bird-caging. Regularly inspect the rope for signs of abnormal wear, especially in areas where the rope runs over sheaves or around drums.
Proper Lubrication: Ensure the rope is adequately lubricated to reduce internal friction. Lack of lubrication can lead to uneven stress distribution, which increases the likelihood of bird-caging.
5. Avoid Shock Loads
Smooth Operation: In operations like lifting or lowering heavy loads, avoid jerky movements or sudden impacts. These forces can shift the strands inside the wire rope and lead to bird-caging.
Use Appropriate Lifting Techniques: When lifting loads, use controlled and steady movements to prevent sudden tension spikes in the rope. Gentle loading and unloading extend the life of the wire rope and reduce the risk of internal damage.
6. Train Personnel on Proper Rope Handling
Educate Operators: Train all operators and personnel on the correct handling, installation, and usage of wire ropes. Proper handling techniques can significantly reduce the risk of bird-caging and other damage.
Best Practices: Ensure all team members understand the importance of load limits, tension control, and smooth operation to maintain the integrity of the wire rope.
Conclusion
Bird-caging in wire ropes is a serious form of damage that compromises the rope’s strength and safety. By following best practices in handling, installation, tension control, and routine inspection, you can prevent bird-caging and extend the lifespan of your wire rope. At Aulone, we emphasize the importance of using high-quality wire ropes and following correct installation and usage procedures to prevent this type of damage and ensure safe, reliable operations.
Chapt 6
How do you perform a proper wire rope lubrication, and why is it necessary?
Proper lubrication of wire ropes is essential for maximizing the lifespan, safety, and performance of the rope in demanding applications such as piling rigs, cranes, and other industrial equipment. Lubrication minimizes friction between the individual strands and wires, protects against corrosion, and helps the rope perform optimally under load.
Here’s how to perform proper wire rope lubrication and why it’s a necessary part of maintenance.
Why Is Wire Rope Lubrication Necessary?
Wire ropes experience significant wear and tear due to internal friction between strands, bending over sheaves, and exposure to harsh environmental conditions. Lubrication plays a crucial role in addressing these issues:
- Reduces Friction: Lubrication minimizes friction between the strands and wires as they move against each other during operation, particularly when the rope bends or flexes. This reduces wear and extends the rope’s service life.
- Prevents Corrosion: Wire ropes are often exposed to moisture, chemicals, and other corrosive elements, which can lead to rust and weaken the rope. Lubricants provide a protective barrier that prevents corrosion, especially for ropes used in outdoor or marine environments.
- Maintains Flexibility: Proper lubrication helps keep the rope flexible, allowing it to bend and move smoothly over sheaves, pulleys, and drums without developing internal wear or damage.
- Reduces Internal Wear: Without lubrication, internal strands can rub against each other, leading to fatigue, internal abrasion, and ultimately rope failure. Lubrication reduces the internal friction, preventing these issues.
- Extends Lifespan: By reducing friction, preventing corrosion, and minimizing internal wear, lubrication significantly extends the operational life of wire ropes.
How to Properly Lubricate a Wire Rope
To properly lubricate a wire rope, follow these essential steps to ensure the lubricant reaches both the surface and the internal core of the rope:
1. Select the Right Lubricant
Choosing the correct lubricant for your wire rope depends on the environment and operating conditions.
- Penetrating Lubricants: These lubricants are thin and designed to penetrate the outer strands of the wire rope and reach the core. They are ideal for reducing internal friction but may require more frequent application.
- Coating Lubricants: These lubricants form a thicker, protective layer on the surface of the rope to protect against external corrosion. They are often used in combination with penetrating lubricants.
- Environment-Specific Lubricants: For ropes operating in marine or corrosive environments, choose lubricants with corrosion inhibitors. In high-heat applications, select lubricants that maintain their effectiveness at elevated temperatures.
2. Inspect and Clean the Wire Rope
Before applying lubricant, inspect the wire rope to ensure there is no visible damage, corrosion, or dirt buildup that could interfere with the lubrication process.
- Clean the Rope: Use a wire brush, compressed air, or specialized cleaning solutions to remove dirt, debris, old lubricant, and any signs of rust. This allows the new lubricant to penetrate more effectively and ensures proper adhesion.
3. Choose the Lubrication Method
There are several methods to lubricate wire ropes, depending on the size of the rope, the amount of use, and the type of lubricant you are applying. The most common methods include:
- Manual Application (Brush or Spray):
- Brush Application: A brush can be used to manually apply the lubricant to the surface of the rope. This is effective for smaller ropes or when applying thick, coating lubricants.
- Spray Application: Using a spray applicator or aerosol can allows for even coverage and is effective for penetrating lubricants. It can be applied along the length of the rope during its movement.
- Drip or Soaking Method: For larger ropes or those requiring deep lubrication, you can drip or soak the rope in a lubricant tank. This allows the lubricant to penetrate deeply into the core of the rope.
- Pressure Lubricators: Specialized equipment like pressure lubrication systems are highly effective for large industrial ropes. These systems force lubricant into the core of the rope under pressure, ensuring thorough lubrication inside and out.
4. Ensure Proper Lubricant Penetration
It’s critical to ensure the lubricant penetrates both the outer surface and the internal strands of the wire rope. The most important areas to lubricate include:
- Between Strands: The lubricant should penetrate between the individual strands to reduce friction and wear during operation.
- Core: Lubrication should also reach the core of the wire rope, which is particularly susceptible to internal friction and corrosion.
- Bend Areas: Pay special attention to the areas where the rope bends over sheaves or pulleys. These points experience the most wear and are most likely to require frequent lubrication.
5. Apply Lubricant Evenly Along the Entire Length
Ensure that the lubricant is applied evenly along the entire length of the rope, including the terminations and the sections that pass through sheaves and pulleys. Move the rope during the process to allow the lubricant to coat all sides and penetrate deep into the strands.
6. Monitor the Lubrication Process
After applying the lubricant, continue to monitor the wire rope for signs of dryness, excessive wear, or corrosion. In high-use or harsh environments, reapply lubrication at regular intervals based on the rope’s usage and environmental exposure.
- Visual Inspection: Look for areas where the rope may be dry, discolored, or showing signs of rust or wear.
- Touch Test: Run your hand (with a glove) along the rope to feel if the rope is adequately lubricated and smooth.
- Lubrication Schedule: Set a regular lubrication schedule based on the operating environment (e.g., weekly or monthly), and adhere to it to maintain proper rope health.
7. Record Maintenance and Lubrication Intervals
Keep a detailed log of when the rope was cleaned and lubricated, the type of lubricant used, and any signs of wear noticed during inspections. This helps track the rope’s condition and ensures that lubrication is applied at appropriate intervals.
Additional Tips for Effective Wire Rope Lubrication
- Avoid Over-Lubrication: Excessive lubrication can cause the rope to become slippery, which may interfere with proper gripping in winches or pulleys. It can also attract dirt and debris, which can cause further wear.
- Reapply After Cleaning: Whenever the rope is cleaned, especially after exposure to water, dirt, or chemicals, reapply lubrication to restore the protective layer.
- Use Compatible Lubricants: Make sure the lubricant is compatible with the rope’s material and any existing coating or galvanization.
Conclusion
Proper lubrication of wire ropes is critical to ensuring their longevity, safety, and performance, especially in demanding environments like piling rigs or cranes. By selecting the right lubricant, applying it thoroughly and evenly, and adhering to a regular lubrication schedule, you can significantly reduce friction, prevent corrosion, and extend the life of your wire rope.
At Aulone, we emphasize the importance of regular maintenance and proper lubrication to keep your wire ropes functioning safely and efficiently in the most challenging conditions.
Common Questions
Frequently Asked Questions
The cost of our Aulone wire ropes varies depending on the specifications and quantity you require. Could you please provide more details so we can give you an accurate quotation?
Regarding warranties and after-sales services, rest assured, we offer comprehensive support. Our products come with a warranty, and we provide after-sales service to ensure your satisfaction. We are committed to maintaining the quality of our products and assisting you throughout the entire process.
80m is acceptable.
It's based on order size and customization requirements. Generally speaking, it is 30 days,However, we strive to fulfill orders as quickly as possible while maintaining our quality standards. For specific timelines, please reach out directly to our sales team.
Please provide wire rope structure, diameter, lay types, galvanized or ungalvanized, tensile strength, min breaking force, length of a roll, termination condition.
Want to buy wire rope & sling?
We’re happy to assist you in finding the ideal rope for your application
86-15573139663
86-15363044363