Rotary Drilling Rig Wire Rope
High performance steel wire rope from Aulone for tower cranes.
High Performance Steel Wire Ropes For Rotary Drilling Rigs
Rotary drilling rigs are essential for various applications in deep foundation engineering. The hoist ropes and/or auxiliary hoist ropes are critical components of rotary drilling rigs, and Aulone experts understand the significant responsibility they bear. The high-performance steel wire ropes developed by Aulone specifically for rotary drilling rigs have the necessary characteristics such as high rotational resistance, exceptional wear resistance, and the ability to withstand external impacts. These features make rotary drilling rigs on-site more cost-effective, easier to maintain, and safer to operate.
The Aulone high-performance steel wire ropes used as hoist ropes and auxiliary hoist ropes are fully compacted and feature a plastic insert steel core. This design ensures that they are both robust and flexible, capable of bearing extremely high loads. These characteristics significantly contribute to extending the service life of the ropes, thereby enhancing the overall lifespan and operational efficiency of the rotary drilling rigs.
Moreover, Aulone provides comprehensive rope solutions with tested rope end terminations, such as button sockets suitable for commercially available pouch sockets, solid thimbles, and associated test and acceptance certificates. These tested terminations ensure secure and reliable connections, further enhancing the performance and safety of the wire ropes in demanding drilling environments.
By focusing on these advanced features and rigorous testing standards, Aulone’s high-performance steel wire ropes offer unparalleled reliability and durability, supporting the most challenging deep foundation projects and ensuring optimal performance of rotary drilling rigs.
Tailored Rotary Drilling Rigs Wire Ropes to Suit Your Needs!
Rotary drilling rigs are indispensable for a variety of applications in deep foundation engineering. Aulone understands the critical role that lifting ropes and auxiliary lifting ropes play in these operations, which is why our experts are dedicated to delivering top-tier wire rope solutions
Available Sizes: Ranging from 8mm up to 50mm.
Tensile Strength: 1770, 1960, 2160mpa.
Specifications on Offer: EN12385-4, GB8918, YB/T5359 and specific customer requirements.
Surface Treatments: Options including hot galvanized, ungalvanized, and stainless steel.
Special technology: Including multi-strand ropes, plastic impregnated, compacted, galvanized.
Structure:35WXK7, 15XK7,24WXK7, 8XK26WS-IWRC, 8XK26WS-EPIWRC, 6X36, 6XK36WS-IWRC etc.
Lay types: RHLL, RHRL, LHLL, LHOL
Certifications: All our ropes come with BV and CE certifications, providing you with the assurance of quality and compliance with international standards.
Hoist Ropes
Rotary drilling rigs are vital in deep foundation engineering, demanding reliable and robust hoist ropes to ensure smooth and efficient operations. At Aulone, we specialize in providing high-performance steel wire ropes designed to meet the rigorous demands of rotary drilling rigs.
Why Choose Aulone’s High-Performance Hoist Ropes?
- High Rotational Resistance: Our hoist ropes are engineered to minimize rotation under load, ensuring precise and stable lifting operations. This feature is critical for maintaining the alignment and integrity of the drilling rig components during operation.
- Exceptional Durability: Crafted to endure the harsh conditions of drilling environments, our ropes offer outstanding resistance to abrasion, wear, and external impacts. This durability translates to longer service intervals and reduced downtime.
- Flexibility and Strength: Featuring a fully compacted design and a plasticized steel core, Aulone ropes provide an optimal combination of flexibility and strength. This allows the ropes to handle heavy loads with ease while maintaining the necessary flexibility for complex rigging setups.
- Corrosion Resistance: Galvanized or specially coated to protect against rust and corrosion, extending the lifespan of the ropes even in challenging environments such as offshore drilling and humid conditions.
35WXK7 & 35WXK7-EP Compacted Wire Rope
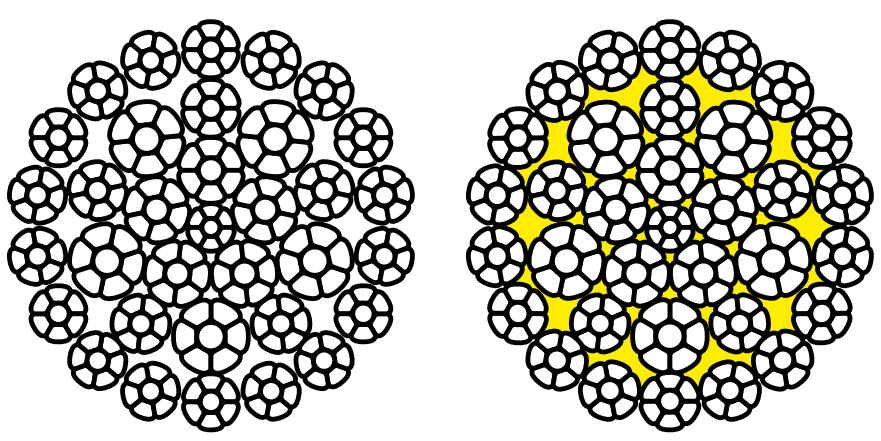
- 35WXK7 is a high performance compacted low rotational rope that combines varying multistrand rope designs to achieve excellent rotation resistance in high lift operations.
Multistrand Non-rotating Wire Ropes with Compacted Outer Strands, EN 12385-4
35WXK7 Advantage
- High tensile strength
- High abrasion resistance
- High fatigue failure resistance
- Expanded contact with bearing surface area
- Less wear of sheaves and capstans
35WXK7-EP Advantage
- High polymer filled and sealed steel reinforced plastic layer within the lubricating oil to make it longer.
- Resistance to outer strands of wire rope to squeeze;
- Non-rotation Recommended for high lifting operations
- High strength
- Reduced rope sheave wear
- Accurate diameter,recommended for multi-layer coiling
- Suitable for single part and multi-part reeving Long service life
Diameter | Approx. weight (kg/100m) | Tensile strength (MPa) | ||
(mm) | 1770 | 1960 | 2160 | |
Minimum breaking load (kN) | ||||
8 | 33 | 51 | 56 | 62 |
9 | 41 | 65 | 71 | 79 |
10 | 51 | 80 | 88 | 97 |
11 | 62 | 96 | 107 | 118 |
12 | 73 | 115 | 127 | 140 |
13 | 86 | 135 | 149 | 164 |
14 | 100 | 156 | 173 | 191 |
15 | 115 | 179 | 198 | 219 |
16 | 131 | 204 | 226 | 249 |
17 | 147 | 230 | 255 | 281 |
18 | 165 | 258 | 286 | 315 |
19 | 184 | 288 | 318 | 351 |
20 | 204 | 319 | 353 | 389 |
21 | 225 | 351 | 389 | 429 |
22 | 247 | 386 | 427 | 470 |
23 | 270 | 421 | 467 | 514 |
24 | 294 | 459 | 508 | 560 |
25 | 319 | 498 | 551 | 608 |
26 | 345 | 538 | 596 | 657 |
27 | 372 | 581 | 643 | 709 |
28 | 400 | 624 | 691 | 762 |
29 | 429 | 670 | 742 | 817 |
30 | 459 | 717 | 794 | 875 |
31 | 490 | 765 | 848 | 934 |
32 | 522 | 816 | 903 | 995 |
35 | 625 | 976 | 1080 | 1191 |
36 | 661 | 1032 | 1143 | 1260 |
39 | 776 | 1211 | 1342 | 1478 |
40 | 816 | 1274 | 1411 | 1555 |
Auxiliary Hoist Ropes
Auxiliary hoist ropes are essential components in rotary drilling rigs, providing additional lifting capacity and support for various operations. Aulone specializes in delivering high-performance steel wire ropes tailored to meet the stringent requirements of auxiliary hoist applications.
Comprehensive Rope Solutions
In addition to high-performance auxiliary hoist ropes, Aulone provides a range of tested rope end terminations to ensure secure and reliable connections:
- Button Sockets: Ideal for use with commercially available wedge sockets, providing secure and robust connections. Button sockets ensure that the rope can be easily attached and detached without compromising safety.
- Solid Thimbles: Designed for heavy-duty applications, offering enhanced durability and strength. Solid thimbles help to distribute the load evenly, reducing wear on the rope.
- Test and Acceptance Certificates: Each rope comes with comprehensive testing documentation, verifying that it meets the highest standards of safety and performance. This includes load tests, fatigue tests, and corrosion resistance tests.
35WXK7 & 35WXK7-EP Compacted Wire Rope
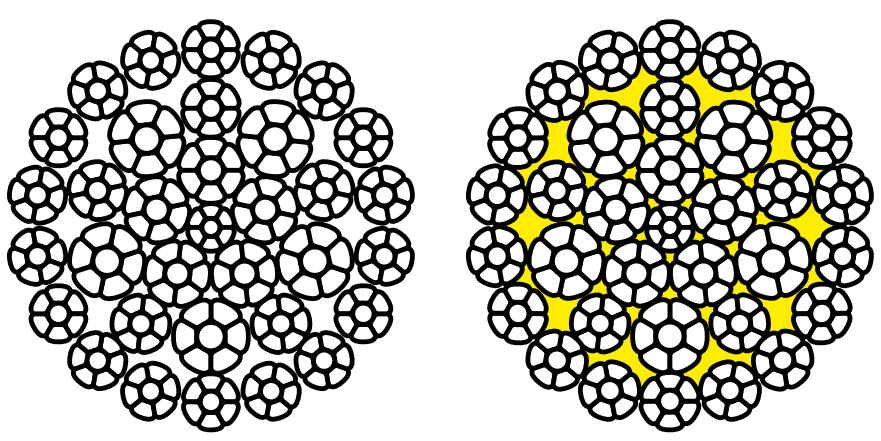
- 35WXK7 is a high performance compacted low rotational rope that combines varying multistrand rope designs to achieve excellent rotation resistance in high lift operations.
Multistrand Non-rotating Wire Ropes with Compacted Outer Strands, EN 12385-4
35WXK7 Advantage
- High tensile strength
- High abrasion resistance
- High fatigue failure resistance
- Expanded contact with bearing surface area
- Less wear of sheaves and capstans
35WXK7-EP Advantage
- High polymer filled and sealed steel reinforced plastic layer within the lubricating oil to make it longer.
- Resistance to outer strands of wire rope to squeeze;
- Non-rotation Recommended for high lifting operations
- High strength
- Reduced rope sheave wear
- Accurate diameter,recommended for multi-layer coiling
- Suitable for single part and multi-part reeving Long service life
Diameter | Approx. weight (kg/100m) | Tensile strength (MPa) | ||
(mm) | 1770 | 1960 | 2160 | |
Minimum breaking load (kN) | ||||
8 | 33 | 51 | 56 | 62 |
9 | 41 | 65 | 71 | 79 |
10 | 51 | 80 | 88 | 97 |
11 | 62 | 96 | 107 | 118 |
12 | 73 | 115 | 127 | 140 |
13 | 86 | 135 | 149 | 164 |
14 | 100 | 156 | 173 | 191 |
15 | 115 | 179 | 198 | 219 |
16 | 131 | 204 | 226 | 249 |
17 | 147 | 230 | 255 | 281 |
18 | 165 | 258 | 286 | 315 |
19 | 184 | 288 | 318 | 351 |
20 | 204 | 319 | 353 | 389 |
21 | 225 | 351 | 389 | 429 |
22 | 247 | 386 | 427 | 470 |
23 | 270 | 421 | 467 | 514 |
24 | 294 | 459 | 508 | 560 |
25 | 319 | 498 | 551 | 608 |
26 | 345 | 538 | 596 | 657 |
27 | 372 | 581 | 643 | 709 |
28 | 400 | 624 | 691 | 762 |
29 | 429 | 670 | 742 | 817 |
30 | 459 | 717 | 794 | 875 |
31 | 490 | 765 | 848 | 934 |
32 | 522 | 816 | 903 | 995 |
35 | 625 | 976 | 1080 | 1191 |
36 | 661 | 1032 | 1143 | 1260 |
39 | 776 | 1211 | 1342 | 1478 |
40 | 816 | 1274 | 1411 | 1555 |
Crowd Ropes
Rotary drilling rigs have a variety of applications in specialized deep foundation engineering. High cost-effectiveness, reliable quality, easy maintenance, high safety standards, and long service life are specific requirements for rotary drilling rigs. The crowd ropes used must also meet these high demands, and Aulone is ready to meet this challenge with its high-performance steel wire ropes. From selecting development and production techniques to the practical use by the customer, Aulone’s expert team focuses on a single goal: to find the best economical and technical rope solutions for installation on rotary drilling rigs.
Aulone’s heavy-duty steel crowd ropes offer exceptional wear resistance and extreme impact load capacity, as well as the ability to withstand severe external impacts that could damage the wire ropes. Aulone provides a wide range of non-rotating high-performance steel wire ropes for use as compression ropes in rotary drilling rigs.
Advantages of 6-Strand and 8-Strand Compacted Wire Ropes
6-Strand Compacted Wire Ropes:
- High Load Capacity: Capable of handling significant loads, making them ideal for heavy lifting tasks.
- Flexibility: Offers a good balance between strength and flexibility, suitable for applications where moderate bending and flexibility are required.
- Wear Resistance: Enhanced surface contact due to compacting increases wear resistance, extending the rope’s service life.
8-Strand Compacted Wire Ropes:
- Greater Flexibility: Higher strand count provides greater flexibility, ideal for applications requiring frequent bending and flexing.
- High Load Capacity: Despite their flexibility, they maintain a high load-bearing capacity, suitable for demanding tasks.
- Smooth Surface: The compacted strands result in a smoother surface, reducing internal friction and wear, thereby enhancing durability.
Both 6-strand and 8-strand compacted wire ropes have been successfully used in various machines, providing the necessary balance of strength, flexibility, and durability for challenging drilling environments.
Customization and Testing
Customization with tested rope end terminations (such as button sockets for commercially available wedge sockets), along with test and acceptance certificates, are all part of our comprehensive solutions. Aulone is dedicated to providing each customer with efficient, reliable, and economical rope solutions to ensure the optimal performance and safety of rotary drilling rigs.
6XK36WS-IWRC & 6XK36WS-EPIWRC
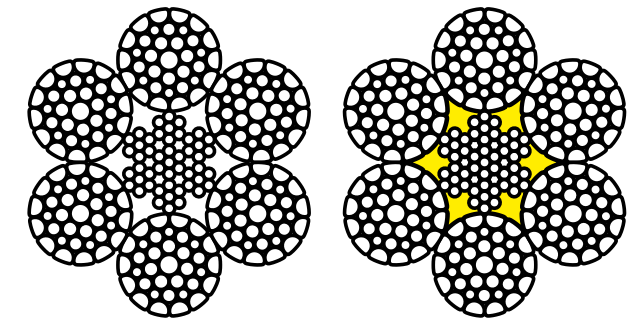
Rope type:6×K19, 6×K36
Rope Construction :6×K19S, 6×K26WS, 6×K31WS, 6×K36WS, 6×K41WSIn accordance with the EN 12385-4 standard.
Different constructions depending on the diameter.
Grade:1770mpa,1960mpa,2160mpa
Lay: sZ,zS,zZ,sS
Application: They can be used as Variable amplitude rope on mobile crane, vessel crane and grab bucket crane. And can be used as hoisting rope on container crane, floating crane, portal crane and steel factory crane etc… Also be applicable to multi-multiplying power system with smaller hoisting height, double coiling block system with matched left-hand and right-hand pairs using for deep hoisting height.
6XK36WS-IWRC Advantage
- Abrasion resistance performance.
- High breaking force.
- Fatigue resistant performance
- Improved support of outer strands in service.
- Improved ton-mile performance
6XK36WS-EPIWRC Advantage
- Abrasion resistance performance.
- High breaking force.
- Outstanding bending fatigue performance
- Improved support of outer strands in service
- Plastic inset
- Long service life
Diameter (mm) | Approx. weight (kg/100m) | Tensile strength (MPa) | ||||||||||||
1570 | 1670 | 1770 | 1870 | 1960 | 2160 | |||||||||
Minimum breaking load (kN) | ||||||||||||||
FC | WC | FC | WC | FC | WC | FC | WC | FC | WC | FC | WC | FC | WC | |
12 | 61.2 | 67.0 | 84.3 | 93.8 | 89.7 | 99.8 | 95.1 | 106 | 100 | 112 | 105 | 117 | 116 | 129 |
14 | 83.3 | 91 | 115 | 128 | 122 | 136 | 129 | 144 | 137 | 152 | 143 | 159 | 158 | 176 |
16 | 109 | 119 | 150 | 167 | 159 | 177 | 169 | 188 | 179 | 199 | 187 | 208 | 206 | 230 |
18 | 138 | 151 | 190 | 211 | 202 | 225 | 214 | 238 | 226 | 251 | 237 | 264 | 261 | 290 |
20 | 170 | 186 | 234 | 261 | 249 | 277 | 264 | 294 | 279 | 310 | 292 | 325 | 322 | 359 |
22 | 206 | 225 | 283 | 315 | 301 | 335 | 320 | 356 | 338 | 376 | 354 | 394 | 390 | 434 |
24 | 245 | 268 | 337 | 375 | 359 | 399 | 380 | 423 | 402 | 447 | 421 | 469 | 464 | 516 |
26 | 287 | 314 | 396 | 440 | 421 | 469 | 446 | 497 | 472 | 525 | 494 | 550 | 545 | 606 |
28 | 333 | 365 | 459 | 511 | 488 | 543 | 518 | 576 | 547 | 608 | 573 | 638 | 632 | 703 |
30 | 382 | 419 | 527 | 586 | 561 | 624 | 594 | 661 | 628 | 698 | 658 | 732 | 725 | 807 |
32 | 435 | 476 | 600 | 667 | 638 | 710 | 676 | 752 | 714 | 795 | 749 | 833 | 825 | 918 |
34 | 491 | 538 | 677 | 753 | 720 | 801 | 763 | 849 | 806 | 897 | 845 | 940 | 931 | 1040 |
36 | 551 | 603 | 759 | 844 | 807 | 898 | 856 | 952 | 904 | 1010 | 947 | 1050 | 1040 | 1160 |
38 | 614 | 671 | 846 | 941 | 899 | 1000 | 950 | 1060 | 1010 | 1120 | 1060 | 1170 | 1160 | 1290 |
40 | 680 | 744 | 937 | 1040 | 1000 | 1110 | 1060 | 1180 | 1120 | 1240 | 1170 | 1300 | 1290 | 1430 |
42 | 750 | 820 | 1030 | 1150 | 1100 | 1220 | 1160 | 1300 | 1230 | 1370 | 1290 | 1430 | 1420 | 1580 |
44 | 823 | 900 | 1130 | 1260 | 1210 | 1340 | 1280 | 1420 | 1350 | 1500 | 1420 | 1570 | 1560 | 1740 |
46 | 899 | 984 | 1240 | 1380 | 1320 | 1470 | 1400 | 1550 | 1480 | 1640 | 1550 | 1720 | 1700 | 1900 |
48 | 979 | 1070 | 1350 | 1500 | 1440 | 1600 | 1520 | 1690 | 1610 | 1790 | 1680 | 1870 | 1860 | 2070 |
50 | 1060 | 1160 | 1460 | 1630 | 1560 | 1730 | 1650 | 1840 | 1740 | 1940 | 1830 | 2030 | 2010 | 2240 |
52 | 1150 | 1260 | 1580 | 1760 | 1680 | 1870 | 1790 | 1990 | 1890 | 2100 | 1980 | 2200 | 2180 | 2420 |
54 | 1240 | 1360 | 1710 | 1900 | 1820 | 2020 | 1930 | 2140 | 2030 | 2260 | 2130 | 2370 | 2350 | 2610 |
56 | 1330 | 1460 | 1840 | 2040 | 1950 | 2170 | 2070 | 2300 | 2190 | 2430 | 2290 | 2550 | 2530 | 2810 |
58 | 1430 | 1560 | 1970 | 2190 | 2100 | 2330 | 2220 | 2470 | 2350 | 2610 | 2460 | 2740 | 2710 | 3020 |
60 | 1530 | 1670 | 2110 | 2350 | 2240 | 2490 | 2380 | 2640 | 2510 | 2790 | 2630 | 2930 | 2900 | 3230 |
8XK26WS-IWRC & 8XK26WS-EPIWRC
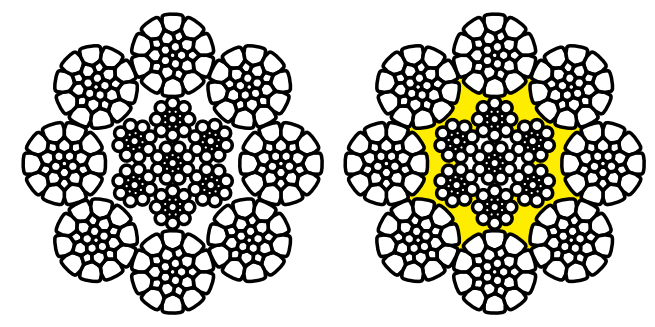
Extremely flexible rope types with up to 288 single wires (8×36) in the outer strands. Better fatigue performance and fatigue life expectancy than 6×19/6×36. Due to the larger number of outer wires these ropes tend to be more sensitive to mechanical damages.
All 8-strand constructions require proper sheave- and drum groove dimensions. Undersized and/or worn sheaves will immediately result in rope deformations, waviness, or high strands. These ropes require extra care during installation (no reverse bend spooling).
High performance compacted single layer constructed rope with 8 outer strands.
The compacted exterior wires make for a larger metal section, and increased resistance to abrasion and crushing.
Rope series :8×K19S, 8×K26WS, 8×K31WS, 8×K36WS, 8×K41WS
In accordance with the EN 12385-4 standard.
Different constructions depending on the diameter.
Core:IWRC, Independent Wire Rope Core
Grade:1770mpa,1960mpa,2160mpa
Lay: sZ,zS,zZ,sS
Application: They can be used as Variable amplitude rope on mobile crane, vessel crane and grab bucket crane. And can be used as hoisting rope on container crane, floating crane, portal crane and steel factory crane etc… Also be applicable to multi-multiplying power system with smaller hoisting height, double coiling block system with matched left-hand and right-hand pairs using for deep hoisting height.
8XK26WS-IWRC Advantage
- Abrasion resistance performance.
- High breaking force
- Outstanding bending fatigue performance
- Very stable rope construction
- improved support of outer strands in service
8XK26WS-EPIWRC Advantage
- High breaking force
- lexible eight strand construction
- High temperature lubricant
- Consistent performance
- Enhanced bend fatigue
- Superior crush resistance
- Accurate diameter tolerance
- Long life, reduced lifetime costs
- Reduced stretch
- Corrosion protected core
- Recommended for multi-layer coiling
Diameter | Approx. | Tensile strength (MPa) | ||||||||||||
1570 | 1670 | 1770 | 1870 | 1960 | 2160 | |||||||||
Minimum breaking load (kN) | ||||||||||||||
FC | WC | FC | WC | FC | WC | FC | WC | FC | WC | FC | WC | FC | WC | |
10 | 40.5 | 48.5 | 51.8 | 65.2 | 55.1 | 69.3 | 58.4 | 73.5 | 62 | 78 | 64.7 | 81.3 | 71.2 | 89.6 |
12 | 58.3 | 69.8 | 74.6 | 93.8 | 79.4 | 99.8 | 84.1 | 106 | 89 | 112 | 93.1 | 117 | 103 | 129 |
14 | 79.4 | 95.1 | 102 | 128 | 108 | 136 | 114 | 144 | 121 | 152 | 127 | 159 | 140 | 176 |
16 | 104 | 124 | 133 | 167 | 141 | 177 | 150 | 188 | 158 | 199 | 166 | 208 | 183 | 230 |
18 | 131 | 157 | 168 | 211 | 179 | 225 | 189 | 238 | 200 | 251 | 210 | 264 | 231 | 290 |
20 | 162 | 194 | 207 | 261 | 220 | 277 | 234 | 294 | 247 | 310 | 259 | 325 | 285 | 359 |
22 | 196 | 235 | 251 | 315 | 267 | 335 | 283 | 356 | 299 | 376 | 313 | 394 | 345 | 434 |
24 | 233 | 279 | 298 | 375 | 317 | 399 | 336 | 423 | 355 | 447 | 373 | 469 | 411 | 516 |
26 | 274 | 328 | 350 | 440 | 373 | 469 | 395 | 497 | 417 | 525 | 437 | 550 | 482 | 606 |
28 | 318 | 380 | 406 | 511 | 432 | 543 | 458 | 576 | 484 | 608 | 507 | 638 | 559 | 703 |
30 | 364 | 437 | 466 | 586 | 496 | 624 | 526 | 661 | 555 | 698 | 582 | 732 | 642 | 807 |
32 | 415 | 497 | 531 | 667 | 564 | 710 | 598 | 752 | 632 | 795 | 662 | 833 | 730 | 918 |
34 | 468 | 561 | 599 | 753 | 637 | 801 | 675 | 849 | 713 | 897 | 748 | 940 | 824 | 1040 |
36 | 525 | 629 | 671 | 844 | 714 | 898 | 757 | 952 | 800 | 1010 | 838 | 1050 | 924 | 1160 |
38 | 585 | 700 | 748 | 941 | 796 | 1000 | 843 | 1060 | 891 | 1120 | 934 | 1170 | 1030 | 1290 |
Your Ultimate Guide to Acquiring Rotary Drilling Rigs Wire Ropes
Rotary drilling rigs are essential for heavy-duty drilling operations in construction, mining, and oil industries. The efficiency and safety of these rigs depend significantly on the quality and durability of the wire ropes they use. Selecting the right wire rope for your rotary drilling rig can significantly impact operational productivity and safety. This guide will walk you through everything you need to know to make the right choice.
Table of contents
Chapt 1
Basic Structure and Classification of Wire Ropes
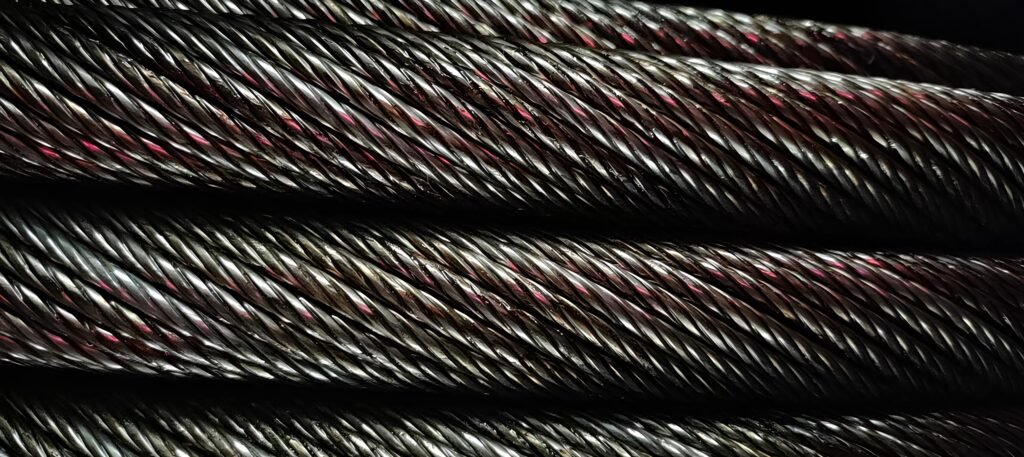
- Wire ropes are essential components in various industries, including construction, shipping, mining, and more, due to their strength, durability, and flexibility. Understanding the basic structure and classification of wire ropes is crucial for selecting the right type for specific applications.
Detailed Structure and Classification of Wire Ropes
Basic Structure of Wire Ropes
Wires:
Material: High-carbon steel, stainless steel, or other alloys.
Function: Provide strength and flexibility.
Strands:
Composition: Groups of wires twisted together.
Diameter: Varies depending on the number and size of wires.
Function: Contribute to the overall strength and flexibility.
Core:
Fiber Core (FC): Natural or synthetic fibers, flexible but less strong.
Independent Wire Rope Core (IWRC): Separate wire rope, offers maximum strength.
Wire Strand Core (WSC): Single wire strand, stronger than fiber core.
Classification of Wire Ropes
Construction
- Single Layer Rope: Simplest form with a single layer of strands.
- Seale Construction: Uniform wire diameter in each strand, providing a smooth outer surface.
- Warrington Construction: Alternating large and small wires in each strand, combining flexibility and strength.
- Filler Wire Construction: Smaller wires fill gaps between main wires, enhancing strength and flexibility.
Lay
- Regular Lay: Wires in strands twist in one direction, strands twist in the opposite direction.
- Lang Lay: Wires and strands twist in the same direction, offering greater resistance to wear and fatigue.
- Alternate Lay: Combination of regular and lang lay, balancing properties.
Application
- General Purpose: Versatile use in lifting, pulling, and securing loads.
- Elevator Ropes: High flexibility and smooth operation for elevators.
- Crane Ropes: High tensile strength and abrasion resistance for cranes.
- Mining Ropes: Durability and resistance to harsh conditions in mining.
- Marine Ropes: Corrosion resistance and durability for marine environments.
Key Specifications
Diameter
- Ranges from 1 mm to over 260 mm, depending on the application.
Length
- Typically supplied in coils or reels ranging from 100 meters to over 5,000 meters.
Tensile Strength
- Measured in megapascals (MPa), ranges from 1,500 MPa to over 2,200 MPa for high-performance ropes.
Minimum Breaking Force
- Dependent on diameter and construction.
Selecting the Right Wire Rope
Determine Load Requirements:
Calculate the maximum load the rope will need to handle.
Consider dynamic loading and potential shock loads.
Consider Environmental Factors:
Choose materials and construction that resist corrosion and abrasion if used in harsh environments.
- Evaluate Flexibility Needs:
Select a rope construction that offers the necessary balance between strength and flexibility.
- Verify Certification and Quality Control:
Ensure the wire rope meets relevant standards and certifications for safety and reliability.
Conclusion
Wire ropes come in various constructions, materials, and specifications to meet diverse application needs. By understanding their detailed structure, classification, and key specifications, you can make an informed decision to select the right wire rope for your requirements, ensuring safety, efficiency, and durability in your operations.
Chapt 2
How Do You Control The Quality Of Rotary Drilling Rig Wire Rope
Ensuring the high quality of rotary drilling rig wire rope is essential for safety and operational efficiency. Aulone employs a comprehensive quality control process, which includes the following steps:
Material Selection
- High-Grade Raw Materials:
- Sourcing: Raw materials are sourced from reputable suppliers known for producing high-quality steel.
- Certification: Each batch of raw materials comes with certificates of origin and compliance, verifying the necessary standards for chemical composition and mechanical properties.
Manufacturing Process Control
- Calibration and Maintenance: Regular calibration and maintenance of machinery ensure consistent performance and precision.
Process Monitoring:
Tension Control: Continuous monitoring of tension during wire drawing and stranding processes to ensure uniformity and strength.
Temperature Regulation: Controlling temperatures during heat treatment processes to achieve desired material properties
Speed Control: Maintaining optimal speeds during production to prevent stress and deformation in the wire ropes.
Inspection and Testing
Visual Inspection:
Surface Examination: Detailed visual inspection for surface irregularities, including cracks, abrasions, and other defects.
Dimensional Checks:
Measuring Instruments: Precision instruments such as micrometers and calipers are used to verify that dimensions meet specified tolerances.
Non-Destructive Testing (NDT):
Magnetic Particle Testing (MPT): Detects surface and slightly subsurface discontinuities using magnetic particles.
Ultrasonic Testing (UT): High-frequency sound waves detect internal flaws without damaging the rope.
Tensile Testing:
- Breaking Strength: Wire ropes are subjected to tensile tests to determine their ultimate tensile strength, ensuring they can handle maximum expected loads.
Fatigue Testing:
Load Cycles: Simulating operational conditions by repeatedly loading and unloading the wire ropes to test their fatigue resistance over time.
Corrosion Testing:
Environmental Simulation: Exposing wire ropes to simulated corrosive environments to ensure their resistance to rust and other forms of corrosion.
Coating and Lubrication
Galvanization:
Corrosion Resistance: Applying a zinc coating to protect against rust and corrosion, particularly in marine or humid environments.
Lubrication:
Friction Reduction: Applying appropriate lubricants to minimize friction and wear during operation.
Penetration Checks: Ensuring that the lubricant adequately penetrates between the wires and strands for optimal protection.
Quality Management System
ISO Certification:
Compliance: Adhering to ISO 9001 standards, providing a systematic approach to quality management, ensuring continuous improvement and consistency.
Documentation and Traceability:
Record Keeping: Maintaining detailed records for each production batch, including raw material certificates, manufacturing logs, and test results.
Batch Identification: Each batch of wire ropes is marked with a unique identifier for traceability and quality assurance.
Regular Audits:
Internal Audits: Conducting regular internal audits to assess compliance with quality standards and identify areas for improvement.
External Audits: Third-party audits to validate the effectiveness of the quality management system.
Skilled Workforce
Training:
Continuous Education: Regular training programs to keep employees updated on the latest manufacturing techniques and quality control practices.
Expert Supervision:
Experienced Supervisors: Supervisors with extensive experience oversee the production process, ensuring adherence to quality protocols and standards.
Customer Feedback and Continuous Improvement
- Customer Feedback:
- Feedback Mechanism: Implementing a robust feedback system to gather and analyze customer feedback on product performance and quality.
- Actionable Insights: Using customer insights to make informed decisions and improvements in the manufacturing process.
- Kaizen: Adopting Kaizen principles for continuous, incremental improvements in quality and efficiency.
Packaging and Delivery
Protective Packaging:
Damage Prevention: Using high-quality packaging materials to protect wire ropes from damage during transportation and storage.
Labeling: Clear labeling of packages with relevant information such as batch numbers, dimensions, and handling instructions.
Quality Checks Before Dispatch:
Final Inspection: Conducting a thorough inspection before dispatch to ensure all wire ropes meet the required quality standards.
Documentation: Providing detailed documentation, including quality certificates and test reports, with each shipment.
By implementing these comprehensive quality control measures, Aulone ensures that its rotary drilling rig wire ropes are of the highest quality, offering reliability, safety, and optimal performance in demanding drilling operations.
Chapt 3
Why Choose Aulone Rotary Drilling Rig Wire Rope?
Inspecting and maintaining tower cranes is crucial to ensure their safe and efficient operation. Here’s a general guideline for tower crane inspection and maintenance:
Superior Quality and Precision
Rigorous Quality Control: Each batch of wire rope undergoes strict quality control processes to meet and exceed industry standards, including non-destructive testing (NDT) and tensile testing.
Customization Options
- Tailored Solutions: Aulone offers customizable wire ropes to meet specific requirements of different rotary drilling rigs, considering load capacity, environmental conditions, and operational demands.
- Flexible Constructure: Aulone provides various configurations such as 35WXK7, 15XK7, 8XK26WS-IWRC, and 6XK36WS-IWRC etc to suit your exact needs.
High Strength and Durability
- Enhanced Strength: Using top-quality materials, Aulone wire ropes offer high breaking strength, essential for the heavy-duty demands of rotary drilling operations.
- Long-Lasting Performance: Designed for durability, Aulone wire ropes withstand the harsh conditions of drilling environments, reducing the frequency of replacements and maintenance costs.
Excellent Fatigue Resistance
- Advanced Design: The wire ropes are designed with optimal strand patterns such as 35WXK7, 15XK7, 8XK26WS-IWRC, and 6XK36WS-IWRC, providing superior fatigue resistance, crucial for the repetitive loading cycles in drilling operations.
- High-Quality Lubrication: Properly lubricated to minimize friction and wear, ensuring smooth operation and extended lifespan.
Corrosion and Abrasion Resistance
- Galvanized and Plastic coated Options: Aulone offers wire ropes with coatings to resist corrosion, ideal for operations in marine and other corrosive environments.
- Abrasion-Resistant Strands: Special strand patterns and treatments enhance resistance to abrasion, maintaining rope integrity under tough conditions.
Comprehensive Support and Service
- Expert Consultation: Aulone provides expert advice on selecting the right wire rope configuration for your specific drilling needs, ensuring optimal performance and safety.
- After-Sales Service: Dedicated support team to assist with installation, maintenance, and any issues that may arise, ensuring minimal downtime and maximum efficiency.
Competitive Pricing
- Cost-Effective Solutions: While maintaining high quality, Aulone offers competitive pricing, making it a cost-effective choice for businesses looking to maximize their investment.
- Flexible Payment Terms: With options like 30% advance payment and balance on the bill of lading, Aulone makes the purchasing process convenient and financially manageable.
Global Reach with Local Expertise
- International Standards: Aulone’s wire ropes meet international standards, making them suitable for global applications.
- Local Expertise: Understanding the specific needs of different regions, Aulone tailors its products to meet local regulations and operational conditions.
Detailed Quality Control Measures
Material Selection
- High-Grade Raw Materials: Sourced from reputable suppliers, each batch of raw materials is certified for chemical composition and mechanical properties.
- Material Certification: Verified for compliance with industry standards, ensuring the fundamental quality of the wire ropes.
Manufacturing Process Control
- Advanced Machinery: Utilization of German equipment (GPL037) for precise manufacturing.
- Process Monitoring: Continuous monitoring of tension, temperature, and speed to maintain consistent quality.
Inspection and Testing
- Visual Inspection: Thorough surface examination for defects.
- Dimensional Checks: Precision instruments verify dimensions meet specified tolerances.
- Non-Destructive Testing (NDT)
- Magnetic Particle Testing (MPT)
- Ultrasonic Testing
- Tensile Testing: Verifies breaking strength.
- Fatigue Testing: Simulates operational conditions to test fatigue resistance.
- Corrosion Testing: Ensures resistance to rust and corrosion.
Coating and Lubrication
- Galvanization: For corrosion resistance.
- Lubrication: Proper lubrication reduces friction and wear.
Quality Management System
- ISO Certification: Adhering to ISO 9001 standards.
- Documentation and Traceability: Detailed records and batch identification.
- Regular Audits: Internal and external audits to ensure compliance.
Skilled Workforce
- Training: Regular programs for updated manufacturing techniques.
- Expert Supervision: Experienced supervisors oversee production.
Customer Feedback and Continuous Improvement
- Feedback Mechanism: Robust system to gather and analyze feedback.
- Continuous Improvement Programs: Six Sigma and Kaizen methodologies.
Packaging and Delivery
- Protective Packaging: High-quality materials to prevent damage.
- Quality Checks Before Dispatch: Final inspections and detailed documentation.
Advantages of Specific Wire Rope Structures
35WXK7
- High Flexibility: Suitable for applications requiring frequent bending and handling.
- Fatigue Resistance: Excellent resistance to fatigue due to its flexible construction.
- Durability: Robust design that withstands heavy loads and harsh conditions.
15XK7
- Enhanced Strength: Ideal for high-load applications due to its robust construction.
- Abrasion Resistance: Superior resistance to abrasion, making it suitable for rough environments.
- Versatility: Can be used in a variety of drilling operations.
8XK26WS-IWRC
- Improved Core Stability: Independent Wire Rope Core (IWRC) provides additional strength and stability.
- Fatigue Resistance: Excellent resistance to repeated loading and unloading cycles.
- Corrosion Resistance: Suitable for environments with higher corrosion risks.
6XK36WS-IWRC
- High Strength: Offers high breaking strength, suitable for demanding drilling operations.
- Flexibility: Balances strength with flexibility, making it easy to handle.
- Longevity: Designed for long service life under heavy-duty conditions.
By implementing these comprehensive quality control measures and offering tailored wire rope configurations, Aulone ensures that its rotary drilling rig wire ropes are of the highest quality, providing reliability, safety, and optimal performance in demanding drilling operations.
Chapt 4
How Can We Extend The Lifespan Of Wire Rope?
Ensuring the longevity of rotary drilling rig wire ropes involves a combination of proper selection, regular maintenance, and correct handling practices. Here are detailed steps to extend the lifespan of these essential components:
Proper Selection
- Material and Coating: Choose wire ropes made from high-quality materials with appropriate coatings (e.g., galvanized or stainless steel) to resist corrosion.
- Configuration: Select the correct wire rope configuration (e.g., 35WXK7, 15XK7, 8XK26WS-IWRC, 6XK36WS-IWRC) based on the specific operational requirements and environmental conditions.
- Safety Factor: Ensure the wire rope has an adequate safety factor, typically 5:1 for critical applications, to handle the maximum expected loads.
Regular Inspection
- Visual Checks: Conduct daily visual inspections to identify signs of wear, corrosion, kinks, broken wires, and other surface irregularities.
- Dimensional Measurements: Regularly measure the diameter and length of the wire rope to detect any reduction in size that could indicate wear.
- Non-Destructive Testing: Perform NDT methods like Magnetic Particle Testing (MPT), Ultrasonic Testing (UT), and X-ray inspections to detect internal flaws.
Proper Lubrication
- Internal Lubrication: Apply internal lubricants to reduce friction between wires and strands, minimizing wear and tear.
- External Lubrication: Use external lubricants to protect the wire rope from environmental factors like moisture and dust.
- Regular Application: Lubricate the wire rope regularly, especially after cleaning or in harsh working conditions.
Cleaning and Maintenance
- Regular Cleaning: Clean the wire rope to remove dirt, debris, and old lubricant. Use appropriate cleaning agents that do not damage the rope material.
- Protective Coatings: Apply protective coatings to prevent rust and corrosion, especially in marine or humid environments.
- Tension Maintenance: Maintain the correct tension in the wire rope to prevent overloading or slack, which can cause excessive wear.
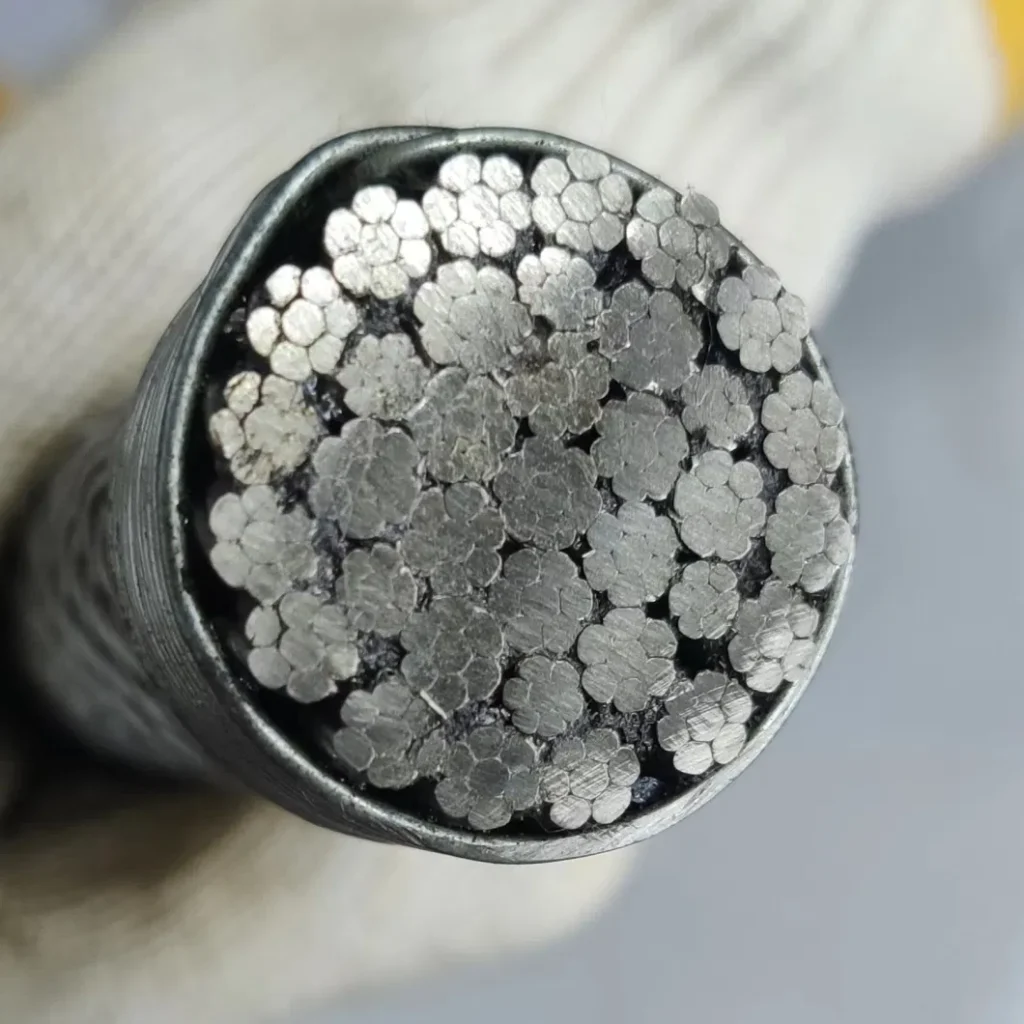
Correct Handling
- Avoid Kinks and Bends: Handle the wire rope carefully to avoid kinks and bends that can cause internal damage.
- Proper Coiling and Uncoiling: Coil and uncoil the wire rope correctly to prevent twists and damage. Use proper techniques and equipment designed for this purpose.
- Avoid Overloading: Ensure the wire rope is not overloaded beyond its capacity. Use load monitoring systems to track the applied loads.
Storage
- Dry and Clean Environment: Store wire ropes in a dry, clean, and well-ventilated area to prevent rust and corrosion.
- Proper Support: Store the wire ropes on reels or racks to prevent contact with the ground and potential contamination.
- Protection from Elements: Cover stored wire ropes to protect them from sunlight, moisture, and extreme temperatures.
Training and Education
- Operator Training: Train operators on proper handling, usage, and maintenance procedures for wire ropes.
- Safety Procedures: Educate staff on safety procedures related to wire rope operations to prevent accidents and damage.
Monitoring and Feedback
- Regular Monitoring: Implement regular monitoring of wire rope condition using sensors and load monitoring systems.
- Feedback Loop: Establish a feedback loop to gather information from operators and maintenance staff about wire rope performance and issues. Use this information to improve maintenance practices and selection criteria.
End Termination Care
- Proper End Terminations: Ensure that end terminations (e.g., sockets, thimbles, clamps) are secure and in good condition. Inspect them regularly for signs of wear or damage.
- Correct Splicing: Use appropriate techniques and tools for splicing to maintain the strength and integrity of the wire rope.
By following these best practices, you can significantly extend the lifespan of rotary drilling rig wire ropes, ensuring their reliability and performance in demanding conditions. Regular maintenance, proper handling, and continuous monitoring are key to preventing premature failure and maximizing the service life of these critical components.
Chapt 5
How Do You Correctly Install Rotary Drilling Rig Wire Rope?
Pre-Installation Preparation
Inspection of Wire Rope
Visual Inspection:
- Surface Examination: Inspect the wire rope for any visible signs of damage, such as kinks, broken wires, corrosion, or abrasions.
- Lubrication Check: Ensure the wire rope is properly lubricated. If the rope is dry, apply a suitable lubricant before installation.
Verification of Specifications:
- Length and Diameter: Confirm that the length and diameter of the wire rope match the specifications required for your drilling rig.
- Certificates and Documentation: Verify the manufacturer’s certificates and documentation for compliance with industry standards and your specific requirements.
Inspection of Equipment
Drums and Sheaves:
- Cleanliness: Ensure that all drums and sheaves are clean and free from debris, which could damage the wire rope.
- Groove Condition: Inspect the grooves of the drums and sheaves for wear and alignment. Worn or misaligned grooves can cause uneven wear on the wire rope.
- Size Matching: Confirm that the drum grooves and sheaves are the correct size for the wire rope to be installed.
Guides and Rollers:
- Alignment: Check that all guides and rollers are properly aligned to prevent the wire rope from rubbing against the sides, which can cause premature wear.
- Condition: Ensure that all guides and rollers are in good condition and rotate freely.
Installation Steps
Unreeling the Wire Rope
- Correct Unreeling:
- Turntables and Reel Stands: Use turntables or reel stands to facilitate smooth unreeling. The wire rope should be rolled off the reel in a straight line, avoiding any sharp bends or twists.
- Control of Movement: Ensure that the wire rope is controlled during unreeling to prevent it from whipping or flailing, which could cause damage or injury.
Threading the Wire Rope
Guiding the Rope:
- Smooth Passage: Carefully thread the wire rope through the system, ensuring it passes smoothly over sheaves and through any guides. Avoid any sharp bends that could damage the rope.
- Assistive Tools: Use assistive tools, such as a wire rope grip or a come-along, to guide the rope and maintain control.
Avoiding Twists and Kinks:
- Proper Handling: Handle the wire rope with care to avoid introducing twists and kinks, which can weaken the rope and reduce its lifespan.
- Use of Swivels: Consider using swivels to prevent the rope from twisting during installation.
Securing the Wire Rope Ends
- Proper Terminations:
- Correct Termination Methods: Use the appropriate termination methods, such as sockets, clamps, or splices, as specified for the application. Ensure that terminations are installed according to manufacturer’s recommendations.
- Verification: Double-check that the terminations are secure and correctly installed to prevent slippage.
Winding on the Drum
Initial Layer:
- Tight and Even Winding: Begin with an initial layer that is tightly and evenly wound onto the drum. This provides a solid foundation for subsequent layers.
- Tension Application: Apply the appropriate tension to the wire rope during winding to prevent slack and ensure even spooling.
Subsequent Layers:
- Smooth Crossover Points: Ensure that crossover points between layers are smooth to prevent the rope from digging into the lower layers.
- Consistent Tension: Maintain consistent tension throughout the winding process to avoid loose wraps and uneven layers.
Alignment
- Ensuring Proper Alignment:
- Drum and Sheave Alignment: Align the wire rope with the center of the drum and sheaves to prevent off-center loading and uneven wear.
- Adjustments: Make necessary adjustments to sheaves and guides to maintain proper alignment during operation.
Post-Installation Checks
Final Inspection
- Visual and Dimensional Checks:
- Surface Inspection: Conduct a final visual inspection to ensure the wire rope is properly installed, correctly threaded, and free of any twists or kinks.
- Dimensional Verification: Measure the diameter and length of the installed wire rope to confirm it meets the required specifications.
Tension Adjustment
- Gradual Load Application:
- Initial Load: Gradually apply the load to the wire rope, monitoring its performance and making adjustments as necessary to ensure even tension distribution.
- Observation: Observe the wire rope during initial operations to ensure it is performing correctly without any signs of distress or abnormal wear.
Documentation
- Recording Details:
- Installation Log: Document the installation process, including the date, wire rope specifications, and any observations or adjustments made.
- Maintenance Schedule: Establish a maintenance schedule based on the manufacturer’s recommendations and operational demands.
Safety Precautions
Use of Proper Equipment
Safety Gear:
- Personal Protective Equipment (PPE): Ensure that all personnel involved in the installation process wear appropriate safety gear, including gloves, safety glasses, helmets, and steel-toed boots.
Handling Tools:
- Correct Tools: Use proper tools and equipment designed for handling and installing wire ropes, such as wire rope grips, come-alongs, and turntables.
Training
- Qualified Personnel:
- Training Programs: Ensure that the installation is carried out by qualified personnel who are trained in the correct handling and installation of wire ropes.
- Safety Procedures: Train staff on safety procedures related to wire rope installation to prevent accidents and damage.
Safety Inspections
- Regular Safety Checks:
- Inspection Schedule: Conduct regular safety inspections to identify and mitigate potential hazards associated with wire rope operations.
- Emergency Procedures: Develop and implement emergency procedures for dealing with wire rope failures or other critical issues.
Best Practices for Extending Wire Rope Lifespan
Proper Storage:
- Dry and Clean Environment: Store wire ropes in a dry, clean, and well-ventilated area to prevent rust and corrosion.
- Support: Store the wire ropes on reels or racks to prevent contact with the ground and potential contamination.
Routine Maintenance:
- Regular Cleaning and Lubrication: Clean and lubricate the wire rope regularly to remove dirt and apply fresh lubricant.
- Tension and Alignment Checks: Regularly check and adjust the tension and alignment of the wire rope to ensure it operates within optimal parameters.
By following these detailed steps and precautions, you can ensure the correct installation and extend the lifespan of rotary drilling rig wire ropes, thereby maximizing their performance and reliability in demanding conditions.
Chapt 6
What Precautions Should Be Taken When Transporting Wire Ropes
Transporting wire ropes requires careful planning and handling to ensure they arrive at their destination in optimal condition. Here are detailed precautions that should be taken when transporting wire ropes:
Preparation Before Transport
1. Proper Coiling and Spooling
Correct Coiling: Ensure that wire ropes are coiled or spooled correctly on reels to prevent kinks and bends.
Secure Ends: Secure the ends of the wire rope to prevent them from unraveling during transport.
2.Inspection
Visual Check: Inspect the wire ropes for any visible damage before transport. Address any issues such as kinks, corrosion, or broken wires.
- Lubrication: Ensure that the wire ropes are properly lubricated to protect against rust and abrasion during transit.
3.Packaging
- Protective Covers: Use protective covers such as plastic sheaths, tarpaulins, or shrink wrap to shield the wire ropes from dirt, moisture, and physical damage.
- Cushioning Material: Place cushioning material between layers of coiled rope to prevent abrasion.
Loading Precautions
1.Use Proper Equipment
Lifting Tools: Use appropriate lifting tools such as slings, hooks, and cranes to handle wire ropes. Avoid using rough or sharp tools that can damage the ropes.
Forklift and Crane Safety: Ensure forklifts and cranes are in good working condition and operated by trained personnel.
2.Prevent Overloading
Weight Distribution: Distribute the weight evenly on the transport vehicle to prevent overloading on one side, which could damage the wire ropes.
- Avoid Exceeding Load Limits: Do not exceed the load limits of the transport vehicle or the lifting equipment.
3. Secure the Load
Tie-Downs: Use tie-downs, straps, or chains to secure the reels or coils to the transport vehicle. Ensure they are tight enough to prevent movement but not so tight that they damage the wire ropes.
Blocking and Bracing: Use blocks and braces to prevent the reels or coils from shifting during transport.
Transport Precautions
1.Weather Protection
Avoid Exposure: If possible, transport wire ropes in covered vehicles to protect them from rain, snow, and direct sunlight.
Tarpaulin Covers: Use tarpaulins or other covers to protect wire ropes on open transport vehicles.
2. Handling During Transit
Gentle Handling: Ensure that the transport vehicle handles the load gently, avoiding sudden stops, starts, or sharp turns that could shift the load.
Monitor the Load: Periodically check the load during transit to ensure it remains secure and has not shifted.
Unloading Precautions
1. Use Proper Equipment
Lifting Tools: Use appropriate lifting tools to unload wire ropes, ensuring they are handled carefully to prevent damage.
Avoid Dragging: Do not drag wire ropes off the transport vehicle as this can cause abrasion and damage.
2. Secure Area
- Clear Path: Ensure the unloading area is clear of obstacles and that there is enough space to safely maneuver the wire ropes.
Safety Zone: Establish a safety zone around the unloading area to keep unauthorized personnel clear.
3. Inspect After Unloading
Check for Damage: Inspect the wire ropes immediately after unloading for any signs of damage that may have occurred during transport.
- Reapply Lubricant: If necessary, reapply lubricant to the wire ropes if they have been exposed to the elements or if lubrication appears to have worn off.
Documentation and Tracking
1. Transport Records
Document Condition: Keep detailed records of the wire ropes’ condition before, during, and after transport, including any observations or incidents.
Tracking Information: Maintain tracking information for the transport vehicle to monitor the location and status of the shipment.
2. Compliance with Regulations
Transport Regulations: Ensure that the transport of wire ropes complies with all relevant transportation regulations and guidelines, including weight limits, securing methods, and safety standards.
By following these detailed precautions, you can ensure that wire ropes are transported safely and arrive at their destination in optimal condition, ready for use. Proper handling, secure packaging, and careful monitoring throughout the transport process are key to preventing damage and maintaining the integrity of the wire ropes.
Chapt 7
Discard Standards For Rotary Drilling Rig WireRopes
1. Number of Broken Wires
If there are more than 10% broken outer wires in one lay length, the rope should be discarded.
- For ropes used in critical applications, if there are more than 5% broken wires in one lay length, consider discarding.
2. Wear and Tear
Diameter Reduction:
- If the wire rope’s diameter has decreased by more than 7% of its original diameter due to wear, it should be discarded.
- Measure the diameter at several points along the rope’s length to ensure accuracy.
Outer Wire Wear:
- If the outer wires are worn down by more than one-third of their original diameter, the rope should be discarded.
- Look for signs of flattening or severe abrasion on the outer wires.
3. Corrosion
Surface Corrosion:
- If there is significant rust or corrosion on the surface that affects the integrity of the rope, it should be discarded.
- Regularly inspect for rust, especially in environments with high humidity or exposure to chemicals.
Internal Corrosion:
- If internal wires show rust or corrosion, indicating that the rope’s core is compromised, it should be discarded.
- Internal inspection might require cutting a sample section of the rope.
4. Deformation
Twisting and Kinking:
- Severe twisting, kinking, or other forms of deformation that cannot be corrected indicate that the rope should be discarded.
- Ensure the rope is not subject to sharp bends or heavy impacts during operation.
Imprints and Bends:
- Any significant imprints or local bends that affect the rope’s structural integrity should lead to discarding.
- Check for crushing or bending marks that indicate overloading or improper handling.
5. Structural Damage
Strand Breakage:
- If the strands of the wire rope are broken or separated, the rope should be discarded.
- Regularly inspect for broken strands and unraveling.
Core Damage:
- Damage or breakage of the rope’s core (such as IWRC – Independent Wire Rope Core) means the rope should be discarded.
- Inspect for core protrusion or any irregularities in the rope’s structure.
6. Abnormal Conditions
Heat Damage:
- Exposure to excessive heat can change the color of the wire or cause localized hardening; such ropes should be discarded.
- Avoid exposing the rope to high temperatures and monitor for any discoloration or hardness.
Operational Abnormalities:
- If the rope produces unusual noises, severe vibrations, or fails to operate normally, it should be inspected immediately and discarded if necessary.
- Any unexpected behavior during operation warrants a thorough check.
7. Other Standards
Service Time:
- Based on the wire rope’s service time and specific working environment, conduct regular inspections and discard ropes as needed.
- Implement a routine inspection schedule based on the rope’s usage frequency and environmental conditions.
Load Testing:
- If the wire rope fails to meet the required strength during load testing, it should be discarded.
- Perform periodic load tests to verify the rope’s load-bearing capacity.
By following these detailed discard standards, you can ensure the safety and efficiency of your rotary drilling rig operations. Regular inspections and maintenance are key to identifying when a wire rope needs to be replaced. If you have any further questions or need additional information, feel free to ask!
Chapt 8
Common Questions
Frequently Asked Questions
The cost of our Aulone wire ropes varies depending on the specifications and quantity you require. Could you please provide more details so we can give you an accurate quotation?
Regarding warranties and after-sales services, rest assured, we offer comprehensive support. Our products come with a warranty, and we provide after-sales service to ensure your satisfaction. We are committed to maintaining the quality of our products and assisting you throughout the entire process.
80m is acceptable.
It's based on order size and customization requirements. Generally speaking, it is 30 days,However, we strive to fulfill orders as quickly as possible while maintaining our quality standards. For specific timelines, please reach out directly to our sales team.
Please provide wire rope structure, diameter, lay types, galvanized or ungalvanized, tensile strength, min breaking force, length of a roll, termination condition.
Want to buy wire rope & sling?
We’re happy to assist you in finding the ideal rope for your application
86-15573139663
86-15363044363
Want to buy wire rope & sling?
We’re happy to assist you in finding the ideal rope for your application
86-15573139663
86-15363044363