The Ultimate Guide to Steel Wire Ropes: A Comprehensive Buyer’s Perspective
Steel wire ropes are indispensable components across various industries, from construction and mining to elevators, bridges, and marine applications. A thorough understanding of their internal structure, specifications, and key features like lay direction and breaking force is crucial for selecting the right product. This guide aims to equip buyers with the knowledge needed to make informed decisions.
Anatomy of Steel Wire Ropes
Understanding the internal components of steel wire ropes is the foundation for selecting the right product.
Wires
Definition: Individual steel threads twisted together to form strands.
Material: High-carbon steel for tensile strength and wear resistance.
Surface Finishes:
Bright (Uncoated): Economical and suitable for non-corrosive environments.
Galvanized: Zinc-coated for corrosion resistance in marine or outdoor applications.
Strands
Definition: Groups of wires twisted together in specific patterns.
Function: Provide strength, flexibility, and resistance to wear.
Core
Fiber Core (FC): Offers greater flexibility and cushioning but is less resistant to crushing.
Independent Wire Rope Core (IWRC): Made of steel, providing higher strength and resistance to crushing, suitable for heavy-duty applications.
Wire Strand Core (WSC)
Lubrication
Reduces internal friction and prevents corrosion, extending rope lifespan.
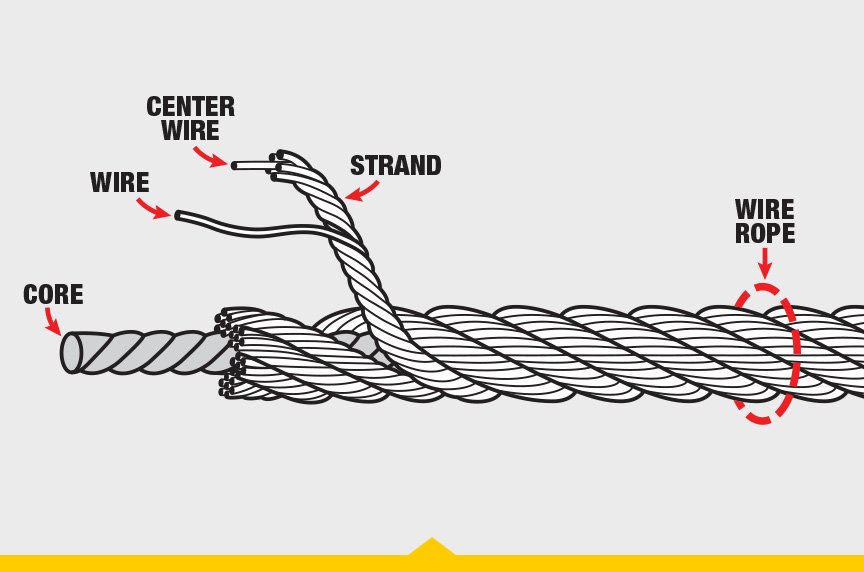
Wire Rope Construction
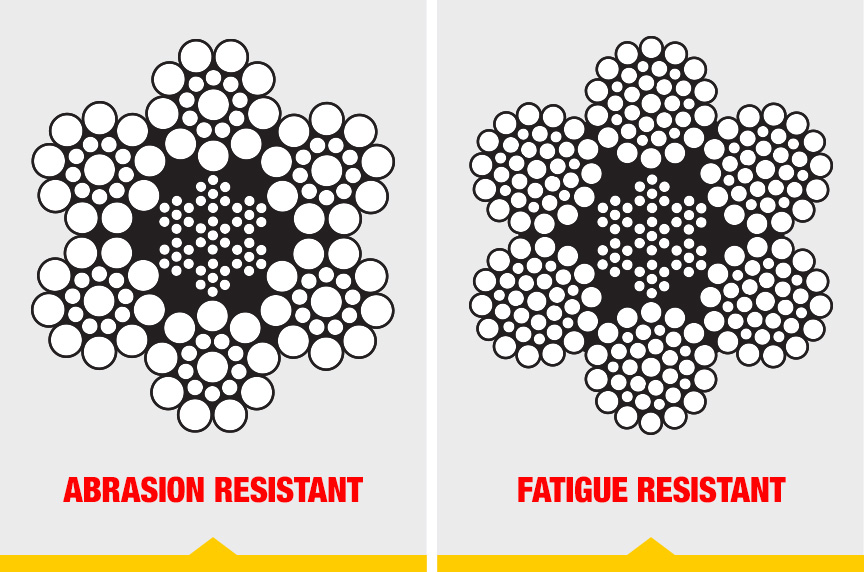
The following terms help to define the construction and properties of wire rope:
- Length
- Size
- Preformed or Non-Preformed
- Direction and Type of Lay
- Finish of Wires
- Grade of Rope
- Type of Core
Length
The total number of feet (cut to size) when wrapped around the spool and delivered.
Size
This is the specified nominal diameter of the wire rope and can be specified in inches or millimeters.
Strand Patterns
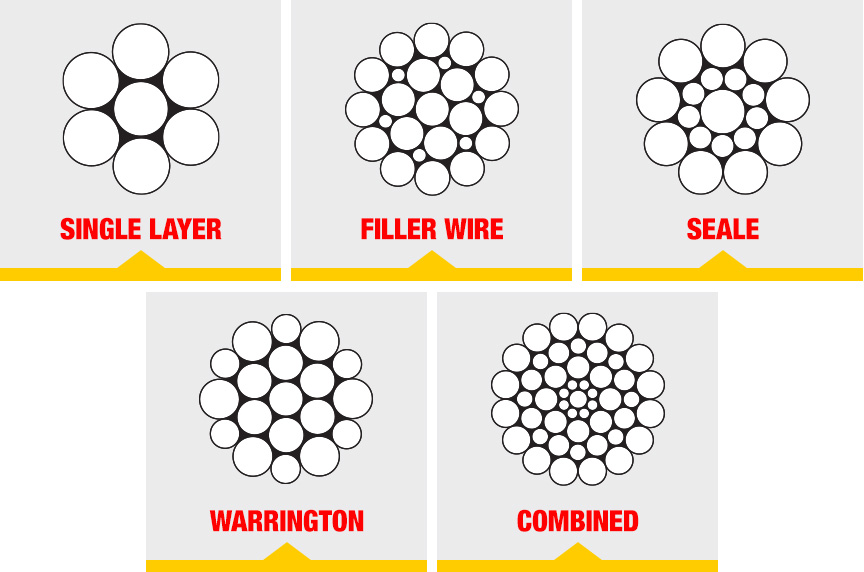
The number of layers of wires, the number of wires per layer, and the size of the wires per layer all affect the strand pattern type. Wire rope can be constructed using one of the following patterns, or can be constructed using two or more of the patterns below.
- Single Layer – The most common example is a 7 wire strand with a single-wire center and six wires of the same diameter around it.
- Filler Wire – Two layers of uniform-size wire around a center with the inner layer having half the number of wires as the outer layer. Small filler wires, equal to the number in the inner layer, are laid in valleys of the inner wire.
- Seale – Two layers of wires around a center with the same number of wires in each layer. All wires in each layer are the same diameter. The large outer wires rest in the valleys between the smaller inner wires.
- Warrington – Two layers of wires around a center with one diameter of wire in the inner layer, and two diameters of wire alternating large and small in the outer later. The larger outer-layer wires rest in the valleys, and the smaller ones on the crowns of the inner layer.
- Combination – A combination strand is constructed using any combination of two or more of the patterns listed above.
Preformed or Non-Preformed
On a preformed wire rope, the strands and wires are formed during the manufacturing process to the helical shape that they will take in a finished wire rope.
Preformed rope can be advantageous in certain applications where it needs to spool more uniformly on a drum, needs greater flexibility, or requires more fatigue-resistance when bending.
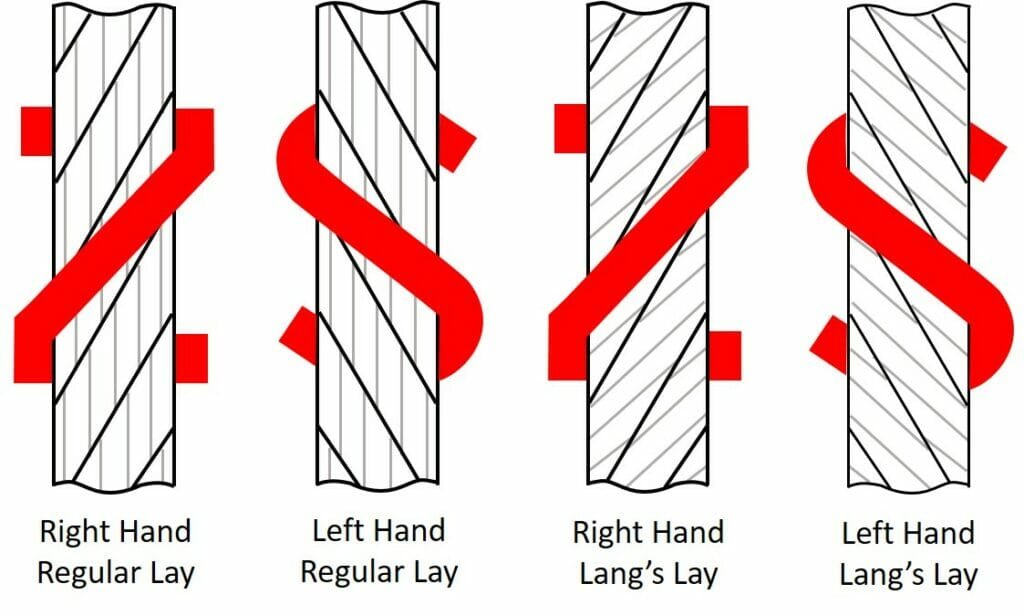
Direction and Type of Lay
The lay direction refers to how the strands and wires are twisted during manufacturing. This significantly impacts the rope’s performance and handling.
Right-Hand Regular Lay (RHRL)
Strands are twisted to the right, while wires within the strands are twisted to the left.
Right-Hand Lang Lay (RHLL)
Strands and wires are both twisted to the right.
Left-Hand Lang Lay (LHLL)
Strands and wires are twisted to the left.
Left-Hand Ordinary Lay (LHOL)
Strands are twisted to the left, and wires within the strands are twisted to the right.
Finish of Wires
Zinc coated (galvanized), zinc/aluminum alloy coated (mischmetal), stainless steel, or unfinished steel (“bright”).
Grade of Rope
The grade of a steel wire rope indicates the tensile strength of the material used in the wires. Higher grades mean stronger wires, enabling the rope to handle greater loads while maintaining the same diameter. Understanding grades is essential for selecting the right rope for your application.
The plow steel strength curve forms the basis for calculating the strength of most steel rope wires.
Common Grades of Steel Wire Rope
1570 N/mm² (1570 MPa)
Characteristics:
Standard grade with moderate strength and durability.
Suitable for general-purpose applications.
1770 N/mm² (1770 MPa)
Characteristics:
High strength for more demanding applications.
Commonly used in construction and material handling.
1960 N/mm² (1960 MPa)
Characteristics:
Extra-high strength with greater load capacity.
Balances strength and flexibility.
2160 N/mm² (2160 MPa)
Characteristics:
Ultra-high strength for extreme loads and demanding environments.
Reduced diameter ropes with high breaking loads.
Type of Core
Wire rope cores are designated as:
- Fiber Core (FC)
- Independent Wire Rope Core (IWRC)
- Wire Strand Core (WSC)
A fiber core can be made of natural or synthetic polypropylene fibers. Fiber cores offer greater elasticity than a steel core but are more susceptible to crushing and not recommended for high heat environments.
A steel core can be an independent wire rope or an individual strand. Steel cores are best suited for applications where a fiber core may not provide adequate support, or in an operating environment where temperatures could exceed 180° F.
Based on what we’ve learned above, this wire rope description would provide the user with the following information:
1″ 6 x 25 FW EIP RRL IWRC
- Diameter = 1″
- Number of Strands = 6
- Number of Wires Per Strand = 25
- Strand Pattern = Filler wire
- Grade = Extra Improved Plow Steel
- Direction and Lay = Right Regular Lay
- Core Type = Independent Wire Rope Core
Minimum Breaking Force (MBF)
- Definition: The maximum load the rope can bear before failing.
- Importance: Ensures safety in operation by meeting or exceeding required load capacity.
Applications Across Industries
Steel wire ropes serve a wide range of industrial applications. Buyers must match the rope’s specifications to the demands of the operation.
Crane industry
Steel wire ropes are indispensable in cranes, hoists, and other lifting equipment.
- Applications:
- Hoisting loads.
- Adjusting crane jibs (luffing).
- Horizontal movement (trolleying).
- Key Considerations:
- High breaking strength for heavy loads.
- Rotation resistance, especially for hoisting applications.
- Durability for multi-layer spooling on drums.
Mining
Mining operations subject ropes to extreme conditions, requiring enhanced durability and performance.
- Applications:
- Draglines for material excavation.
- Hoisting ore and personnel.
- Winches in underground operations.
- Key Considerations:
- Abrasion resistance for high-wear environments.
- Corrosion resistance for wet and humid conditions.
- Fatigue resistance for repeated bending cycles.
Elevators
Steel wire ropes play a vital role in passenger and freight elevator systems.
- Applications:
- Passenger elevators in commercial and residential buildings.
- Industrial lifts for heavy materials.
- Key Considerations:
- Consistent diameter for smooth traction.
Bridges and Structural Engineering
Steel wire ropes are essential for load-bearing and stabilization in structural projects.
- Applications:
- Suspension bridges.
- Stay cables in high-rise buildings.
- Guy wires for stabilization.
- Key Considerations:
- Minimal elongation to maintain structural integrity.
- Long-term corrosion resistance.
- Aesthetic finishes for visible installations.
Marine and Offshore
Marine environments demand ropes resistant to saltwater corrosion and dynamic loads.
- Applications:
- Mooring and towing ships.
- Cranes on vessels.
- Offshore oil and gas rigs.
- Key Considerations:
- Superior corrosion resistance.
- High flexibility for dynamic loads.
- Enhanced durability through plastic coatings.
Specifications Buyers Should Prioritize
Structure
Wire rope structure refers to the arrangement of wires, strands, and the core within the rope. The choice of structure depends on the specific application, load requirements, flexibility, and environmental conditions. Here’s a detailed guide to help you select the right wire rope structure.
Rope Diameter
Ensure compatibility with equipment such as pulleys, sheaves, or drums.
Surface Finish
- Bright: Suitable for indoor applications or controlled environments.
- Galvanized: Provides corrosion resistance for outdoor and marine use.
- Galvanized type: Zn95Al5 , A, AB, B
Lay Type Selection
- Regular Lay (RHRL, LHOL): Ideal for general-purpose use with reduced rotation.
- Lang Lay (RHLL, LHLL): Preferred for abrasion resistance and flexibility in specialized applications.
Breaking Force and Safety Factor
Always select ropes with an MBF that comfortably exceeds operational requirements.
Tensile Strength
Higher grades (1960 or 2160) are ideal for heavy-duty applications.
Lower grades (1570 or 1770) suffice for light to medium loads.
Length
Accurate length is essential for effective and safe operation.
Key Considerations:
Application:
Lifting: Ensure enough rope for the full lifting height plus extra for anchoring.
Towing/Mooring: Account for dynamic loads like wave action or terrain variations.
Stretch and Elongation:
Include a margin for initial and long-term rope stretch under load.
Safety Margin:
Add extra length to allow for adjustments during operation.
Tips:
- Use precise measuring tools like calibrated wheels.
- Verify length based on equipment specifications.
Termination
Terminations secure the ends of a wire rope for load attachment.
Common Methods:
Sockets:
Types: Open, closed, swaged, or poured.
Use: Heavy-duty applications like cranes or bridges.
Strength: High; ideal for permanent connections.
Wire Rope Clips:
Use: Temporary terminations, guy wires, or emergency repairs.
Limitations: Requires regular inspection and tightening.
Eye Splicing:
Types: Hand or mechanical.
Use: Marine ropes, elevators, or flexible applications.
Advantage: Retains more strength than clips.
Swaging (Pressed Sleeves):
Use: Fixed-length industrial or lifting applications.
Advantage: Permanent and secure.
Thimbles:
Use: Protects loops from wear and maintains shape.
Common for lifting slings or towing.
Maintenance and Longevity
To maximize the lifespan of steel wire ropes, regular maintenance is crucial:
- Inspection
- Look for broken wires, corrosion, or diameter reduction.
- Examine terminations for signs of wear or fatigue.
- Lubrication
- Apply lubrication periodically to reduce friction and prevent rust.
- Replacement Guidelines
- Retire ropes showing excessive wear, broken wires exceeding allowable limits, or significant deformation.
Partnering with the Right Supplier
Choosing a reputable supplier ensures:
- Certified products compliant with standards like EN 12385.
- Rigorous quality testing, including breaking force and fatigue resistance.
- Tailored solutions for specific industrial needs.
Conclusion
Understanding the internal structure, lay directions, and technical specifications of steel wire ropes is vital for buyers in any industry. By matching the rope’s features to the operational requirements, you can ensure safety, efficiency, and durability.
For expert advice and tailored recommendations, consult a trusted supplier to meet your specific needs.
Ask For A Quick Quote
Fill out a quick form to get a personalized quote tailored to your specific needs.