Ship Cranes Wire Rope
High performance steel wire rope from Aulone for ship cranes
High Performance Steel Wire Ropes For Ship Cranes
Always Keeping an Eye on Costs
When selecting the perfect steel wire rope for cranes, cost-effectiveness is just as important as technical parameters. Choosing crane ropes made by Aulone significantly reduces overall expenses, as we understand that the costs associated with a rope extend beyond mere installation.
The Aulone rope experts are here to provide you with professional advice. In case of any issues, we are available 24/7 through our network of engineers and a dedicated hotline. We ensure that your downtime is minimized and manageable.
Technological Lead with plastic coated and compacted creating high-performance steel wire ropes requires extensive technological and production expertise. Aulone’s plastic coatedtechnology involves covering the lubricated steel core with a durable synthetic coat. Meanwhile, our compacted technology utilizes a specialized process to compact the individual strands of the steel wire rope.
High-Performance Steel Wire Ropes
Aulone offers a wide range of rotation-resistant and non-rotation-resistant high-performance steel wire ropes suitable for construction cranes, including applications as boom hoist ropes, hoist ropes, trolley ropes, and draglines.
Tailored Ship Cranes Wire Rope To Suit Your Needs!
At Aulone, we specialize in manufacturing high-quality hoist ropes designed specifically for ship cranes. Our ropes are engineered to withstand the toughest maritime conditions while providing exceptional strength and reliability. With a focus on high breaking force, our products ensure safe and efficient lifting operations, making them the ideal choice for shipyards and marine applications.
Available Sizes: Ranging from 8mm up to 200mm.
Tensile Strength: 1770, 1960, 2160mpa.
Specifications on Offer: EN12385-4, GB8918, YB/T5359 and specific customer requirements.
Surface Treatments: Options including hot galvanized, ungalvanized, and stainless steel.
Special technology: Including multi-strand ropes, plastic impregnated, compacted, galvanized.
Structure:35WXK7, 15XK7, 16xK7-EPIWRC(K),39XK7,35WXK7-EPWSC, 8XK26WS-IWRC, 8XK26WS-EPIWRC, 6XK36WS-IWRC etc.
Lay types: RHLL, RHRL, LHLL, LHOL
Certifications: All our ropes come with BV and CE certifications, providing you with the assurance of quality and compliance with international standards.
Hoist Ropes
In the maritime industry, the integrity and performance of hoist ropes are critical to operational success. As ship cranes face significant loads and environmental stresses, selecting the right hoist rope is essential for safety and efficiency.
Key Features of Aulone’s Hoist Ropes
Superior Breaking Force: Engineered for optimal strength, Aulone’s hoist ropes exhibit high breaking force, allowing for the safe lifting of heavy cargo while minimizing the risk of failure. Our rigorous testing protocols ensure that every rope meets or exceeds industry standards.
Enhanced Durability: Designed specifically for maritime applications, our ropes are constructed to resist abrasion, corrosion, and environmental degradation. This durability reduces maintenance needs and prolongs the lifespan of your equipment, ultimately saving costs.
Customized Solutions: We recognize that every operational scenario is unique. Aulone offers customized hoist rope solutions that cater to specific lifting requirements, ensuring maximum efficiency and performance tailored to your applications.
Stringent Quality Assurance: At Aulone, we prioritize quality control throughout our manufacturing process. Each hoist rope undergoes extensive testing and certification to guarantee compliance with the highest safety and performance standards.
Conclusion
Investing in Aulone’s hoist ropes for your ship crane operations means prioritizing safety, efficiency, and reliability. Our commitment to engineering excellence ensures that you receive products that meet the highest expectations. Reach out to us today to discuss your requirements and receive a tailored quote that fits your operational needs.
35WXK7 & 35WXK7-EP Compacted Wire Rope
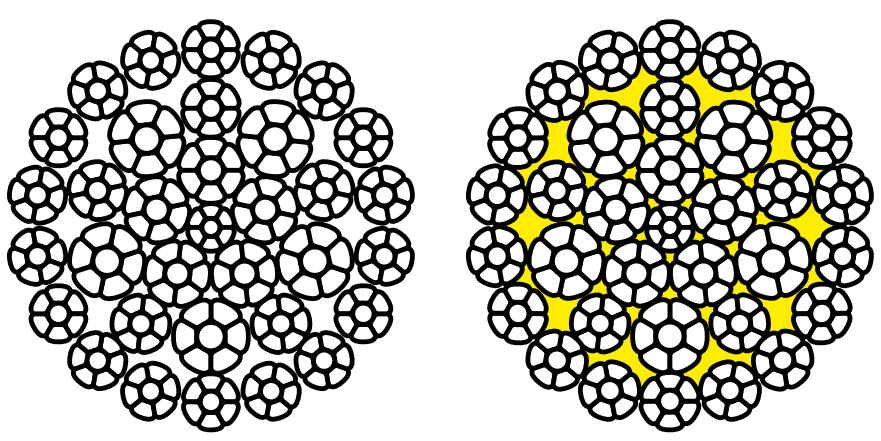
- 35WXK7 is a high performance compacted low rotational rope that combines varying multistrand rope designs to achieve excellent rotation resistance in high lift operations.
Multistrand Non-rotating Wire Ropes with Compacted Outer Strands, EN 12385-4
35WXK7 Advantage
- High tensile strength
- High abrasion resistance
- High fatigue failure resistance
- Expanded contact with bearing surface area
- Less wear of sheaves and capstans
35WXK7-EP Advantage
- High polymer filled and sealed steel reinforced plastic layer within the lubricating oil to make it longer.
- Resistance to outer strands of wire rope to squeeze;
- Non-rotation Recommended for high lifting operations
- High strength
- Reduced rope sheave wear
- Accurate diameter,recommended for multi-layer coiling
- Suitable for single part and multi-part reeving Long service life
Diameter | Approx. weight (kg/100m) | Tensile strength (MPa) | ||
(mm) | 1770 | 1960 | 2160 | |
Minimum breaking load (kN) | ||||
8 | 33 | 51 | 56 | 62 |
9 | 41 | 65 | 71 | 79 |
10 | 51 | 80 | 88 | 97 |
11 | 62 | 96 | 107 | 118 |
12 | 73 | 115 | 127 | 140 |
13 | 86 | 135 | 149 | 164 |
14 | 100 | 156 | 173 | 191 |
15 | 115 | 179 | 198 | 219 |
16 | 131 | 204 | 226 | 249 |
17 | 147 | 230 | 255 | 281 |
18 | 165 | 258 | 286 | 315 |
19 | 184 | 288 | 318 | 351 |
20 | 204 | 319 | 353 | 389 |
21 | 225 | 351 | 389 | 429 |
22 | 247 | 386 | 427 | 470 |
23 | 270 | 421 | 467 | 514 |
24 | 294 | 459 | 508 | 560 |
25 | 319 | 498 | 551 | 608 |
26 | 345 | 538 | 596 | 657 |
27 | 372 | 581 | 643 | 709 |
28 | 400 | 624 | 691 | 762 |
29 | 429 | 670 | 742 | 817 |
30 | 459 | 717 | 794 | 875 |
31 | 490 | 765 | 848 | 934 |
32 | 522 | 816 | 903 | 995 |
35 | 625 | 976 | 1080 | 1191 |
36 | 661 | 1032 | 1143 | 1260 |
39 | 776 | 1211 | 1342 | 1478 |
40 | 816 | 1274 | 1411 | 1555 |
Aulone specializes in developing and manufacturing highly compacted, high-performance steel wire ropes suitable for both hoist and auxiliary applications on ship cranes. Ensuring safe, reliable, and cost-effective lifting operations aboard ships is crucial, making the use of appropriate high-performance steel wire ropes essential. Aulone’s hoist and auxiliary ropes are engineered for exceptional longevity, customized to meet the specific requirements of each crane, thereby helping to minimize overall costs for ship crane operators.
To enhance performance, our high-performance steel wire ropes are equipped with suitable end terminations, which are standard features of our products. Furthermore, no rope leaves our production facility without undergoing comprehensive testing and inspection. We ensure timely delivery of our ropes
Auxiliary Hoist Ropes
Aulone produces highly compacted high-performance steel wire ropes for hoist and auxiliary hoist applications on ship cranes. Lifting heavy loads safely, reliably, and cost-effectively requires the use of top-quality steel wire ropes. Aulone’s ropes are known for their durability and longevity, reducing overall costs for ship crane operators.
Our ropes have proven their effectiveness on cranes from leading manufacturers such as Liebherr, Huisman, NMF, Cargotec, and Palfinger. Using plastic coated technology, which impregnates the steel core with plastic material, ensures high safety and corrosion resistance throughout the rope’s lifespan.
Aulone’s rotation-resistant ropes perform exceptionally well even under challenging conditions with larger fleet angles and complex reeving arrangements. The compaction technology further extends rope lifetime by minimizing wear.
Aulone’s ropes come with suitable end terminations and are thoroughly inspected to ensure compliance and quality before delivery, along with necessary certificates.
35WXK7 & 35WXK7-EP Compacted Wire Rope
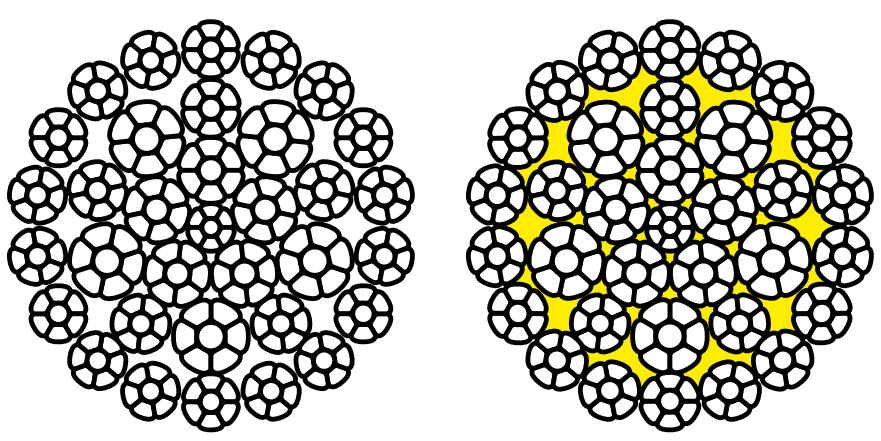
- 35WXK7 is a high performance compacted low rotational rope that combines varying multistrand rope designs to achieve excellent rotation resistance in high lift operations.
Multistrand Non-rotating Wire Ropes with Compacted Outer Strands, EN 12385-4
35WXK7 Advantage
- High tensile strength
- High abrasion resistance
- High fatigue failure resistance
- Expanded contact with bearing surface area
- Less wear of sheaves and capstans
35WXK7-EP Advantage
- High polymer filled and sealed steel reinforced plastic layer within the lubricating oil to make it longer.
- Resistance to outer strands of wire rope to squeeze;
- Non-rotation Recommended for high lifting operations
- High strength
- Reduced rope sheave wear
- Accurate diameter,recommended for multi-layer coiling
- Suitable for single part and multi-part reeving Long service life
Diameter | Approx. weight (kg/100m) | Tensile strength (MPa) | ||
(mm) | 1770 | 1960 | 2160 | |
Minimum breaking load (kN) | ||||
8 | 33 | 51 | 56 | 62 |
9 | 41 | 65 | 71 | 79 |
10 | 51 | 80 | 88 | 97 |
11 | 62 | 96 | 107 | 118 |
12 | 73 | 115 | 127 | 140 |
13 | 86 | 135 | 149 | 164 |
14 | 100 | 156 | 173 | 191 |
15 | 115 | 179 | 198 | 219 |
16 | 131 | 204 | 226 | 249 |
17 | 147 | 230 | 255 | 281 |
18 | 165 | 258 | 286 | 315 |
19 | 184 | 288 | 318 | 351 |
20 | 204 | 319 | 353 | 389 |
21 | 225 | 351 | 389 | 429 |
22 | 247 | 386 | 427 | 470 |
23 | 270 | 421 | 467 | 514 |
24 | 294 | 459 | 508 | 560 |
25 | 319 | 498 | 551 | 608 |
26 | 345 | 538 | 596 | 657 |
27 | 372 | 581 | 643 | 709 |
28 | 400 | 624 | 691 | 762 |
29 | 429 | 670 | 742 | 817 |
30 | 459 | 717 | 794 | 875 |
31 | 490 | 765 | 848 | 934 |
32 | 522 | 816 | 903 | 995 |
35 | 625 | 976 | 1080 | 1191 |
36 | 661 | 1032 | 1143 | 1260 |
39 | 776 | 1211 | 1342 | 1478 |
40 | 816 | 1274 | 1411 | 1555 |
Boom hoist and grab ropes for ship cranes
Boom hoist ropes are critical components of every crane. For this application, Aulone develops high-performance 8 and 6-strand steel wire ropes that excel in reliability, safety, and durability. These attributes are essential for the cost-effective operation of ship cranes. In addition to meeting all technical specifications, minimizing total cost of ownership is a key priority for crane operators, and as a manufacturer of crane ropes, it is a primary focus for us as well.
6XK36WS-IWRC & 6XK36WS-EPIWRC
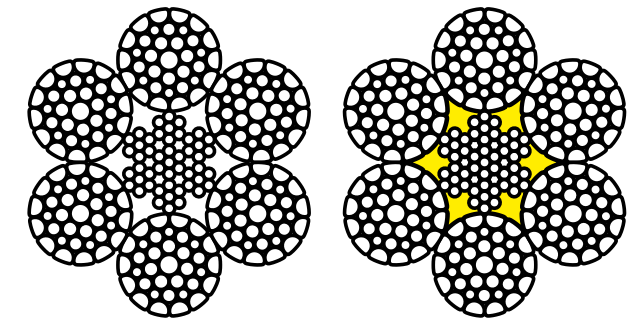
Rope type:6×K19, 6×K36
Rope Construction :6×K19S, 6×K26WS, 6×K31WS, 6×K36WS, 6×K41WSIn accordance with the EN 12385-4 standard.
Different constructions depending on the diameter.
Grade:1770mpa,1960mpa,2160mpa
Lay: sZ,zS,zZ,sS
Application: They can be used as Variable amplitude rope on mobile crane, vessel crane and grab bucket crane. And can be used as hoisting rope on container crane, floating crane, portal crane and steel factory crane etc… Also be applicable to multi-multiplying power system with smaller hoisting height, double coiling block system with matched left-hand and right-hand pairs using for deep hoisting height.
6XK36WS-IWRC Advantage
- Abrasion resistance performance.
- High breaking force.
- Fatigue resistant performance
- Improved support of outer strands in service.
- Improved ton-mile performance
6XK36WS-EPIWRC Advantage
- Abrasion resistance performance.
- High breaking force.
- Outstanding bending fatigue performance
- Improved support of outer strands in service
- Plastic inset
- Long service life
Diameter (mm) | Approx. weight (kg/100m) | Tensile strength (MPa) | ||||||||||||
1570 | 1670 | 1770 | 1870 | 1960 | 2160 | |||||||||
Minimum breaking load (kN) | ||||||||||||||
FC | WC | FC | WC | FC | WC | FC | WC | FC | WC | FC | WC | FC | WC | |
12 | 61.2 | 67.0 | 84.3 | 93.8 | 89.7 | 99.8 | 95.1 | 106 | 100 | 112 | 105 | 117 | 116 | 129 |
14 | 83.3 | 91 | 115 | 128 | 122 | 136 | 129 | 144 | 137 | 152 | 143 | 159 | 158 | 176 |
16 | 109 | 119 | 150 | 167 | 159 | 177 | 169 | 188 | 179 | 199 | 187 | 208 | 206 | 230 |
18 | 138 | 151 | 190 | 211 | 202 | 225 | 214 | 238 | 226 | 251 | 237 | 264 | 261 | 290 |
20 | 170 | 186 | 234 | 261 | 249 | 277 | 264 | 294 | 279 | 310 | 292 | 325 | 322 | 359 |
22 | 206 | 225 | 283 | 315 | 301 | 335 | 320 | 356 | 338 | 376 | 354 | 394 | 390 | 434 |
24 | 245 | 268 | 337 | 375 | 359 | 399 | 380 | 423 | 402 | 447 | 421 | 469 | 464 | 516 |
26 | 287 | 314 | 396 | 440 | 421 | 469 | 446 | 497 | 472 | 525 | 494 | 550 | 545 | 606 |
28 | 333 | 365 | 459 | 511 | 488 | 543 | 518 | 576 | 547 | 608 | 573 | 638 | 632 | 703 |
30 | 382 | 419 | 527 | 586 | 561 | 624 | 594 | 661 | 628 | 698 | 658 | 732 | 725 | 807 |
32 | 435 | 476 | 600 | 667 | 638 | 710 | 676 | 752 | 714 | 795 | 749 | 833 | 825 | 918 |
34 | 491 | 538 | 677 | 753 | 720 | 801 | 763 | 849 | 806 | 897 | 845 | 940 | 931 | 1040 |
36 | 551 | 603 | 759 | 844 | 807 | 898 | 856 | 952 | 904 | 1010 | 947 | 1050 | 1040 | 1160 |
38 | 614 | 671 | 846 | 941 | 899 | 1000 | 950 | 1060 | 1010 | 1120 | 1060 | 1170 | 1160 | 1290 |
40 | 680 | 744 | 937 | 1040 | 1000 | 1110 | 1060 | 1180 | 1120 | 1240 | 1170 | 1300 | 1290 | 1430 |
42 | 750 | 820 | 1030 | 1150 | 1100 | 1220 | 1160 | 1300 | 1230 | 1370 | 1290 | 1430 | 1420 | 1580 |
44 | 823 | 900 | 1130 | 1260 | 1210 | 1340 | 1280 | 1420 | 1350 | 1500 | 1420 | 1570 | 1560 | 1740 |
46 | 899 | 984 | 1240 | 1380 | 1320 | 1470 | 1400 | 1550 | 1480 | 1640 | 1550 | 1720 | 1700 | 1900 |
48 | 979 | 1070 | 1350 | 1500 | 1440 | 1600 | 1520 | 1690 | 1610 | 1790 | 1680 | 1870 | 1860 | 2070 |
50 | 1060 | 1160 | 1460 | 1630 | 1560 | 1730 | 1650 | 1840 | 1740 | 1940 | 1830 | 2030 | 2010 | 2240 |
52 | 1150 | 1260 | 1580 | 1760 | 1680 | 1870 | 1790 | 1990 | 1890 | 2100 | 1980 | 2200 | 2180 | 2420 |
54 | 1240 | 1360 | 1710 | 1900 | 1820 | 2020 | 1930 | 2140 | 2030 | 2260 | 2130 | 2370 | 2350 | 2610 |
56 | 1330 | 1460 | 1840 | 2040 | 1950 | 2170 | 2070 | 2300 | 2190 | 2430 | 2290 | 2550 | 2530 | 2810 |
58 | 1430 | 1560 | 1970 | 2190 | 2100 | 2330 | 2220 | 2470 | 2350 | 2610 | 2460 | 2740 | 2710 | 3020 |
60 | 1530 | 1670 | 2110 | 2350 | 2240 | 2490 | 2380 | 2640 | 2510 | 2790 | 2630 | 2930 | 2900 | 3230 |
8XK26WS-IWRC & 8XK26WS-EPIWRC
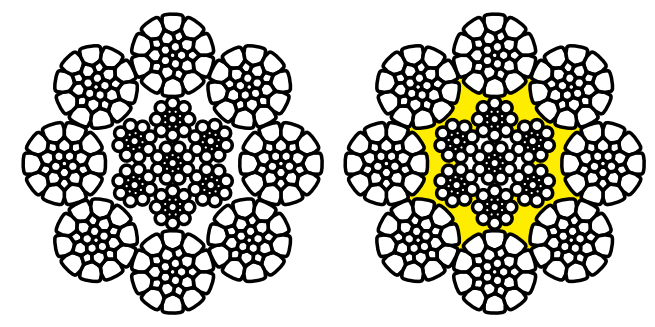
Extremely flexible rope types with up to 288 single wires (8×36) in the outer strands. Better fatigue performance and fatigue life expectancy than 6×19/6×36. Due to the larger number of outer wires these ropes tend to be more sensitive to mechanical damages.
All 8-strand constructions require proper sheave- and drum groove dimensions. Undersized and/or worn sheaves will immediately result in rope deformations, waviness, or high strands. These ropes require extra care during installation (no reverse bend spooling).
High performance compacted single layer constructed rope with 8 outer strands.
The compacted exterior wires make for a larger metal section, and increased resistance to abrasion and crushing.
Rope series :8×K19S, 8×K26WS, 8×K31WS, 8×K36WS, 8×K41WS
In accordance with the EN 12385-4 standard.
Different constructions depending on the diameter.
Core:IWRC, Independent Wire Rope Core
Grade:1770mpa,1960mpa,2160mpa
Lay: sZ,zS,zZ,sS
Application: They can be used as Variable amplitude rope on mobile crane, vessel crane and grab bucket crane. And can be used as hoisting rope on container crane, floating crane, portal crane and steel factory crane etc… Also be applicable to multi-multiplying power system with smaller hoisting height, double coiling block system with matched left-hand and right-hand pairs using for deep hoisting height.
8XK26WS-IWRC Advantage
- Abrasion resistance performance.
- High breaking force
- Outstanding bending fatigue performance
- Very stable rope construction
- improved support of outer strands in service
8XK26WS-EPIWRC Advantage
- High breaking force
- lexible eight strand construction
- High temperature lubricant
- Consistent performance
- Enhanced bend fatigue
- Superior crush resistance
- Accurate diameter tolerance
- Long life, reduced lifetime costs
- Reduced stretch
- Corrosion protected core
- Recommended for multi-layer coiling
Diameter | Approx. | Tensile strength (MPa) | ||||||||||||
1570 | 1670 | 1770 | 1870 | 1960 | 2160 | |||||||||
Minimum breaking load (kN) | ||||||||||||||
FC | WC | FC | WC | FC | WC | FC | WC | FC | WC | FC | WC | FC | WC | |
10 | 40.5 | 48.5 | 51.8 | 65.2 | 55.1 | 69.3 | 58.4 | 73.5 | 62 | 78 | 64.7 | 81.3 | 71.2 | 89.6 |
12 | 58.3 | 69.8 | 74.6 | 93.8 | 79.4 | 99.8 | 84.1 | 106 | 89 | 112 | 93.1 | 117 | 103 | 129 |
14 | 79.4 | 95.1 | 102 | 128 | 108 | 136 | 114 | 144 | 121 | 152 | 127 | 159 | 140 | 176 |
16 | 104 | 124 | 133 | 167 | 141 | 177 | 150 | 188 | 158 | 199 | 166 | 208 | 183 | 230 |
18 | 131 | 157 | 168 | 211 | 179 | 225 | 189 | 238 | 200 | 251 | 210 | 264 | 231 | 290 |
20 | 162 | 194 | 207 | 261 | 220 | 277 | 234 | 294 | 247 | 310 | 259 | 325 | 285 | 359 |
22 | 196 | 235 | 251 | 315 | 267 | 335 | 283 | 356 | 299 | 376 | 313 | 394 | 345 | 434 |
24 | 233 | 279 | 298 | 375 | 317 | 399 | 336 | 423 | 355 | 447 | 373 | 469 | 411 | 516 |
26 | 274 | 328 | 350 | 440 | 373 | 469 | 395 | 497 | 417 | 525 | 437 | 550 | 482 | 606 |
28 | 318 | 380 | 406 | 511 | 432 | 543 | 458 | 576 | 484 | 608 | 507 | 638 | 559 | 703 |
30 | 364 | 437 | 466 | 586 | 496 | 624 | 526 | 661 | 555 | 698 | 582 | 732 | 642 | 807 |
32 | 415 | 497 | 531 | 667 | 564 | 710 | 598 | 752 | 632 | 795 | 662 | 833 | 730 | 918 |
34 | 468 | 561 | 599 | 753 | 637 | 801 | 675 | 849 | 713 | 897 | 748 | 940 | 824 | 1040 |
36 | 525 | 629 | 671 | 844 | 714 | 898 | 757 | 952 | 800 | 1010 | 838 | 1050 | 924 | 1160 |
38 | 585 | 700 | 748 | 941 | 796 | 1000 | 843 | 1060 | 891 | 1120 | 934 | 1170 | 1030 | 1290 |
Your Ultimate Guide to Acquiring Ship Cranes Wire Rope
When selecting wire rope for ship cranes, choosing the right specifications ensures optimal performance, safety, and durability. This guide will walk you through the critical considerations, technical features, and best practices to make the best choice for your marine operations.
Table of contents
Chapt 1
What are the basic components of a wire rope?
Wire Rope Components and Construction
1. Wires: The smallest component of wire rope, wires are made primarily from high-carbon steel due to its strength and resistance to wear. The size and the material of the wires may vary depending on the application’s demands for strength, flexibility, or corrosion resistance. Some common materials besides steel are iron, stainless steel, and Monel (nickel-copper alloy).
2. Strands: Strands are formed by twisting together multiple wires. The number of wires in each strand can vary typically from around 7 to 49 or more. This configuration significantly impacts the rope’s total strength, flexibility, and resistance to bending fatigue. Strands can be made using different methods like single layer, filler wire, seale, or warrington, each providing specific advantages in terms of load distribution and resistance to external pressures.
3. Core: The core supports the strands and can be made from different materials:
- Fiber Core (FC): Made from natural fibers like sisal or synthetic materials such as polypropylene. Fiber cores are lighter and more flexible but less resistant to environmental damage than steel.
- Independent Wire Rope Core (IWRC): A separate wire rope within the main rope, providing added strength, durability, and resistance to crushing.
- Wire Strand Core (WSC): Similar to IWRC but typically consists of a single strand.
4. Lubrication: Lubrication is vital for maintaining the wire rope’s integrity. It reduces internal friction, protects against corrosion, and enhances fatigue resistance. The type of lubricant and the method of application can vary depending on the operational environment and the specific requirements of the rope.
5. Lay: The lay of the rope refers to the direction and the manner in which the strands are twisted around the core. There are several types of lays:
- Regular Lay: Strands are twisted in the opposite direction to the wires within the strands. This is the most common lay, providing stable, balanced characteristics.
- Lang Lay: Both strands and wires are twisted in the same direction, resulting in a rope that offers superior abrasion resistance and contact with pulleys and sheaves but can be more susceptible to untwisting and kinking.
- Alternate Lay: Alternating the direction of lays between strands for specialized applications.
6. Finish: The finish on the wires can be bright (uncoated), galvanized (coated with zinc for corrosion resistance), or stainless steel (for high corrosion resistance). The choice of finish affects the wire rope’s durability in different environments.
Properties and Applications
Flexibility vs. Strength: The construction of wire rope aims to balance flexibility and strength. Ropes with fewer, larger wires are generally stronger but less flexible, whereas ropes with more, smaller wires are more flexible but have lower breaking strength.
Fatigue Resistance: This is influenced by the wire rope’s diameter, construction, and lay type. Lang lay ropes generally have better fatigue resistance than regular lay ropes due to the way the wires align with the rope’s curve under stress.
Abrasion Resistance: Critical for ropes used over sheaves or drums. Lang lay ropes, with their parallel wire alignment, offer better resistance to external abrasion.
Corrosion Resistance: Determined by the material and finish of the wire. Galvanized and stainless steel ropes offer higher resistance compared to bright steel ropes.
Conclusion
Wire ropes are essential in numerous applications ranging from construction and mining to shipping and fishing. Understanding the components and characteristics of wire ropes is crucial for selecting the right rope for the job, ensuring safety, efficiency, and durability in operations. For further information or specific applications, consulting with wire rope manufacturers or specialized engineering texts is recommended to obtain detailed insights tailored to your specific needs and applications.
Chapt 2
What special requirements do ship cranes have for wire ropes?
Wire ropes used in ship cranes need to meet specific requirements due to the challenging conditions they face, including constant exposure to the elements, heavy loads, and the need for high levels of reliability and safety. Here are some of the special requirements for wire ropes used in ship cranes:
1. High Tensile Strength
Ship crane wire ropes must have high tensile strength to handle the heavy lifting operations typical in marine and shipping environments. These ropes are often required to lift heavy containers, equipment, or cargo, necessitating a wire rope capable of bearing significant loads without failure.
2. Corrosion Resistance
Given the marine environment, where saltwater and humidity are prevalent, wire ropes used in ship cranes must have excellent corrosion resistance. Galvanized wire ropes, which are coated with zinc, or stainless steel wire ropes are commonly used due to their ability to withstand corrosive marine environments.
3. Fatigue Resistance
The dynamic loading conditions, where loads are frequently lifted and lowered, require wire ropes that can resist fatigue. Ropes with multiple strands and wires, such as those with compacted strands or rotation-resistant designs, are preferred because they offer better resistance to the bending stresses that occur over sheaves and drums.
4. Flexibility
Flexibility is crucial for wire ropes in ship crane applications because the ropes are often subjected to tight bending radii over sheaves and drums. A more flexible rope minimizes stress and wear under these conditions, which can extend the rope’s operational life. Ropes with a higher number of smaller wires in each strand generally offer greater flexibility.
5. Rotation Resistance
Ship crane operations often require precise control of the load, which can be complicated by rope twisting and rotation. Rotation-resistant wire ropes are designed to minimize these issues, enabling more stable and controlled lifting operations. These ropes are constructed in a way that balances the outer and inner layers of strands, reducing the torque that can cause rotation.
6. Diameter and Length Consistency
Uniform diameter and length are important for the smooth operation of ship cranes. Consistency in these dimensions ensures that the rope performs reliably across the entire length of the crane, providing stable lifting and lowering without unexpected variances in performance.
7. Abrasion Resistance
Wire ropes in ship cranes must also be abrasion-resistant due to frequent contact with various surfaces and other rigging components. Enhanced outer layers or specially treated wires can be used to increase the rope’s durability against external wear.
Practical Considerations
When selecting a wire rope for ship cranes, it’s also essential to consider the manufacturer’s specifications and certifications. The ropes should meet international and maritime safety standards, such as those from the International Organization for Standardization (ISO) and other relevant maritime regulatory bodies.
By addressing these specialized requirements, wire ropes for ship cranes can ensure operational efficiency, safety, and longevity, even in the demanding conditions of maritime environments.

Chapt 3
How can I identify wear and damage in wire ropes?
Identifying wear and damage in wire ropes is critical to ensuring safe and efficient operations, especially in industries that involve heavy lifting, pulling, and stabilizing. Wire rope degradation over time is inevitable due to wear, fatigue, environmental factors, and mechanical stresses. Recognizing the early signs of wear or damage helps prevent accidents, minimize downtime, and extend the lifespan of the wire rope. Below are detailed guidelines to help identify wear and damage in wire ropes.
Types of Wear and Damage in Wire Ropes
Broken Wires
- Types of Broken Wires:
- Crown Breaks: Occur on the surface of the wire rope and are typically a result of repeated bending over sheaves, leading to fatigue.
- Valley Breaks: These are breaks that occur between strands, often caused by excessive crushing or improper loading.
- How to Identify:
- Visually inspect the rope along its entire length.
- Look for broken wires sticking out from the surface.
- Broken wires can be grouped together or distributed along the rope, which could indicate different types of stress or fatigue.
- Types of Broken Wires:
Corrosion
- External Corrosion: Caused by exposure to moisture, saltwater, or chemicals, leading to rust formation on the wire surface.
- Internal Corrosion: Occurs when moisture or contaminants penetrate into the core of the rope, leading to hidden damage.
- How to Identify:
- Look for visible signs of rust or pitting on the rope’s exterior.
- If the rope feels rough or has a reddish-brown discoloration, it may indicate corrosion.
- In severe cases, internal corrosion can reduce the rope’s diameter. Use calipers to measure the diameter at regular intervals and compare with the nominal diameter.
Abrasion
- Surface Abrasion: Caused by rubbing against other surfaces or equipment, leading to the wear of outer wires.
- How to Identify:
- Visually inspect for flat or shiny areas on the rope, which indicate contact with external surfaces.
- Check for a reduction in the diameter of individual wires, as abrasion can wear them down over time.
- Rope abrasion is often caused by misalignment or improper sheave size.
Deformation
- Types of Deformations:
- Kinks: Occur when the rope is improperly handled or unspooled, resulting in sharp bends that damage the rope structure.
- Birdcaging: A type of deformation where the strands “pop out,” causing the rope to resemble a birdcage. This occurs when the rope is subjected to sudden release of tension or overloading.
- Crushing: Happens when the rope is compressed between sheaves or improperly spooled on a drum, leading to flattened or distorted areas.
- How to Identify:
- For kinks, look for sharp bends in the rope. Kinks cannot be repaired, and the rope should be discarded.
- Birdcaging is characterized by an obvious bulging or spread of the strands, indicating severe internal damage.
- Crushing appears as a flattening or squashed section of the rope, often due to improper spooling or lack of tension during winding.
- Types of Deformations:
Core Protrusion
- Core protrusion refers to the core pushing out beyond the strands. It usually occurs when the rope is overloaded or subjected to shock loading.
- How to Identify:
- Inspect the rope for any visible displacement of the core, protruding from the center of the rope structure.
- Core protrusion is often indicative of severe internal damage, requiring the rope to be replaced.
Reduction in Rope Diameter
- Causes: Reduction in diameter can result from core failure, excessive wear, or internal strand damage.
- How to Identify:
- Use calipers to measure the rope diameter at different points along its length.
- If the diameter has reduced more than 10% of the nominal value, the rope should be discarded.
- Reduction in diameter may also indicate internal corrosion or a failing core.
Fatigue-Induced Damage
- Bending Fatigue: Repeated bending of the rope over sheaves and pulleys can lead to fatigue breaks in individual wires.
- How to Identify:
- Look for broken wires, especially at points where the rope passes over sheaves or is bent frequently.
- Fatigue breaks tend to appear at regular intervals and are often found near fittings or terminations.
- Wires broken due to fatigue often have a cup-and-cone appearance.
Inspection Techniques for Identifying Wear and Damage
Visual Inspection
- The most common and effective method for identifying wear and damage.
- Inspect the entire length of the rope systematically, looking for any irregularities, broken wires, discoloration, deformation, or reduced diameter.
- Pay particular attention to areas that interact with sheaves, drums, and terminations, as these locations are more prone to damage.
Measuring Rope Diameter
- Use calipers to measure the rope’s diameter at different points.
- Compare the measured diameter with the nominal diameter of the rope.
- A reduction in diameter of more than 10% is a sign that the rope should be discarded.
Magnetic Flux Leakage (MFL) Inspection
- A non-destructive testing method that uses magnetic fields to detect broken wires and internal corrosion.
- An MFL device can scan the rope to detect damage that may not be visible during a visual inspection.
- It is particularly useful for assessing internal damage in wire ropes with IWRC.
Ultrasonic Testing
- Ultrasonic testing is used to assess internal conditions and detect hidden flaws such as internal corrosion or breaks.
- This method involves sending ultrasonic waves through the rope and measuring the response to detect discontinuities.
Bend Test
- Bend the rope in a loop and closely examine the strands and wires. If cracks or broken wires appear, it indicates that the rope is compromised.
- The bend test can help identify broken wires that may be hidden under normal tension.
Discard Criteria for Wire Ropes
Wire ropes must be discarded when they exhibit certain levels of damage. The following are common discard criteria based on international standards such as ISO 4309:
Broken Wires
- If 6 or more broken wires are found in one rope lay length, the rope should be discarded.
- If 3 or more broken wires are found in one strand, this indicates that the strand is weakened and the rope should be replaced.
Corrosion
- Severe corrosion that affects the wire surface or reduces the rope diameter by more than 10% is grounds for discarding.
- If internal corrosion is detected, especially if it has led to a reduction in the rope’s strength, the rope must be removed from service.
Abrasion
- If the outer wires are worn down by more than one-third of their original diameter, the rope should be discarded.
- Visible flattening of wires, or areas where the rope has become significantly smoother, are also indicators for replacement.
Deformation
- Kinks: Ropes with kinks should be discarded immediately. Kinks result in a permanent deformation that cannot be corrected.
- Birdcaging: Birdcaged ropes indicate severe internal damage and must be removed from service.
- Crushing: If the rope exhibits severe crushing that affects its ability to spool properly or impacts its diameter, it should be replaced.
Reduction in Diameter
- A reduction in rope diameter of more than 10% compared to the nominal diameter indicates that the rope has likely suffered internal core damage or significant wear and must be discarded.
Fatigue Damage
- If fatigue breaks are observed along multiple points of the rope, particularly near points of bending, it is a sign that the rope has reached the end of its service life.
Best Practices for Inspecting Wire Ropes
Frequency of Inspection
- Daily Inspections: Conduct daily visual inspections, especially before starting work. This is essential for critical applications like cranes, elevators, and hoists.
- Periodic Inspections: In addition to daily checks, conduct a more thorough inspection weekly or monthly, depending on usage frequency. Use advanced methods such as MFL or ultrasonic testing during these inspections.
- Post-Incident Inspections: If the rope has been subjected to shock loading or an incident (such as slipping out of a sheave), conduct an immediate and thorough inspection.
Qualified Personnel
- Inspections should be performed by personnel who are trained in identifying wire rope damage and aware of discard criteria. They should be familiar with the specific application and operating conditions of the rope.
Documentation
- Maintain detailed records of each inspection, including the date, the findings, and any corrective actions taken.
Track the cumulative number of broken wires, signs of wear, and reductions in diameter over time. This helps in identifying patterns of deterioration and planning timely replacements.
Conclusion
The safe use of wire ropes depends on regular and thorough inspections to identify signs of wear and damage. Broken wires, corrosion, abrasion, deformation, and a reduction in diameter are all indicators that a wire rope may need to be replaced. Utilizing different inspection methods—such as visual inspections, magnetic flux leakage, ultrasonic testing, and diameter measurements—ensures that potential problems are identified before they lead to rope failure.
Adhering to established discard criteria is essential for maintaining safety in any operation involving wire ropes. Early identification and replacement of damaged ropes prevent accidents, minimize downtime, and ensure the longevity of equipment and personnel safety.
Chapt 4
What are the basic maintenance and care requirements for wire ropes?
Proper maintenance and care of wire ropes are crucial to extend their service life, ensure operational safety, and maintain optimal performance. Wire ropes are subject to constant stresses, including tension, bending, and environmental exposure, which can lead to wear, corrosion, fatigue, and even failure. A well-maintained wire rope operates more reliably, prevents potential accidents, and reduces downtime costs. Here is a comprehensive guide on the basic maintenance and care requirements for wire ropes:
1. Inspection and Monitoring
Regular inspection is the cornerstone of wire rope maintenance. Proper inspection helps identify wear, damage, and potential safety risks before they result in failure. Key points to consider include:
1.1 Frequency of Inspection
- Daily Inspections: Conduct visual inspections of wire ropes daily, especially before starting any operations involving heavy lifting or critical applications such as cranes, hoists, and elevators.
- Periodic Inspections: Comprehensive inspections should be performed periodically based on the rope’s usage and application. For highly stressed environments, weekly or monthly inspections may be required.
- Post-Incident Inspection: Whenever a wire rope has been subjected to shock loading, overload, or a sudden event, conduct an immediate inspection to determine if it is still safe to use.
1.2 Components to Inspect
- Outer Wires: Check for broken or worn wires along the entire length of the rope.
- Corrosion: Look for signs of rust, pitting, or discoloration. This is particularly important for ropes exposed to outdoor environments or saltwater.
- Deformation: Identify any birdcaging, kinking, crushing, or reduction in diameter, as these can indicate serious internal damage.
- End Fittings and Terminations: Inspect end fittings (such as thimbles, sockets, and swaged fittings) for wear, cracks, or signs of loosening.
2. Proper Lubrication
Lubrication is one of the most critical aspects of wire rope maintenance. It reduces friction between the strands and individual wires, minimizes wear, and protects against corrosion.
2.1 Importance of Lubrication
- Reducing Friction: Wire ropes undergo significant internal friction between individual wires and strands as they bend or pass over sheaves and drums. Lubrication reduces this friction, prolonging the rope’s service life.
- Corrosion Protection: A good lubricant helps protect against environmental factors, such as moisture, which can lead to corrosion.
2.2 Types of Lubricants
- Petroleum-Based Lubricants: Commonly used for general applications. These lubricants provide good protection against moisture and reduce internal friction.
- Biodegradable Lubricants: These are used in environmentally sensitive areas, such as marine environments or forestry operations, where minimizing the environmental impact is essential.
- Penetrating and Coating Lubricants:
- Penetrating Lubricants: Designed to penetrate deep into the wire rope and reach the core, providing internal lubrication and corrosion protection.
- Coating Lubricants: Form a protective layer around the exterior of the wire rope, reducing external wear and providing additional corrosion resistance.
2.3 Lubrication Methods
- Manual Lubrication: Involves applying lubricant by hand, using a brush, cloth, or spray. This method is effective for smaller ropes and situations where targeted lubrication is needed.
- Bath Immersion: Immersing the entire rope in a lubricant bath is the most effective method for ensuring complete coverage. This method is more suitable for new ropes or when full relubrication is required.
- Pressure Lubrication: A specialized pressurized lubrication system is used to force the lubricant into the wire rope, reaching the inner strands and core. This is the most effective method for deep lubrication.
3. Proper Handling and Use
The way wire ropes are handled and used plays a significant role in maintaining their integrity and extending their lifespan.
3.1 Avoiding Shock Loading
- Shock loading occurs when the rope is subjected to a sudden, forceful load. This can happen if the load is dropped or if tension is applied too quickly.
- Impact of Shock Loading: Shock loading can result in broken wires, internal damage, or deformation such as kinking or birdcaging. Care should be taken to avoid rapid or jerky movements.
3.2 Proper Spooling on Drums
- Alignment: When winding wire rope onto a drum, ensure proper alignment. Poor spooling can lead to overlapping, crushing, and accelerated wear.
- Controlled Tension: Maintain appropriate tension when spooling to avoid slack, loose wraps, or kinking. Proper tension keeps the wraps tight and prevents flattening of the rope.
3.3 Avoiding Kinks and Bends
- Uncoiling: When uncoiling a new wire rope, avoid pulling it off from the side of the reel, as this can create loops and kinks. Instead, uncoil from a turntable or straight along the ground.
- Bending Radius: Follow manufacturer recommendations regarding the minimum bending radius. Excessive bending over sheaves or hooks with a diameter smaller than recommended can cause permanent damage.
4. Storage Requirements
Proper storage is essential to prevent damage to wire ropes when not in use. Incorrect storage can lead to rust, corrosion, or damage to the structure of the rope.
4.1 Environmental Conditions
- Dry Environment: Store wire ropes in a dry, well-ventilated area to avoid moisture buildup, which can lead to corrosion.
- Avoid Direct Contact with the Ground: Ropes should be stored on wooden pallets or similar structures to keep them elevated off the ground, reducing the risk of moisture absorption.
- Avoid Direct Sunlight and Chemicals: Exposure to direct sunlight for long periods can degrade the lubricant, while chemical exposure can cause corrosion.
4.2 Coil and Reel Storage
- Coiling: When storing smaller wire ropes, coil them neatly and avoid tight coils that could introduce kinks or stress.
- Reels: Larger ropes should be stored on reels, with the ends securely fastened to prevent unwinding. Rotate reels periodically to avoid flat spots or deformation.
5. Protecting Against Corrosion
Corrosion is a major concern for wire ropes, particularly those used outdoors or in marine environments. Proper maintenance is key to minimizing corrosion.
5.1 Use of Protective Coatings
- Galvanized Wire Ropes: For outdoor or marine applications, using galvanized wire ropes provides an extra layer of corrosion protection through zinc coating.
- Plastic or Polymer Coating: Plastic-coated wire ropes can offer superior corrosion resistance, particularly for applications involving saltwater or exposure to harsh chemicals.
5.2 Inspection for Corrosion
- Regular Checks: Regularly inspect wire ropes for signs of rust or discoloration. Corrosion often starts on the exterior wires and gradually affects the core.
- Preventive Measures: Applying a protective lubricant regularly is one of the best preventive measures to protect against corrosion.
6. Repair and Replacement Protocols
While proper maintenance can extend the life of wire ropes, there are limits to how much wear and damage can be tolerated before they become unsafe.
6.1 Criteria for Wire Rope Replacement
- Broken Wires: If six or more wires are broken within one rope lay, or if three or more wires are broken within a single strand, the rope should be replaced.
- Reduction in Diameter: A reduction in diameter of more than 10% from the original diameter indicates severe internal damage and the rope should be discarded.
- Severe Corrosion: If visible signs of rust, pitting, or other forms of corrosion are present, especially near terminations, the rope should be replaced.
6.2 Prohibited Repairs
- No Attempted Repairs: Wire ropes with significant wear, kinks, birdcaging, or broken wires should never be repaired. Repairs can compromise the strength of the rope and lead to accidents. Damaged ropes must be replaced with new, certified wire ropes.
7. Training and Best Practices for Maintenance
Proper maintenance of wire ropes involves not just having the right knowledge but also ensuring that operators are well-trained in best practices for handling, inspecting, and caring for wire ropes.
7.1 Training Personnel
- Knowledge of Rope Types: Personnel should be familiar with the specific wire ropes in use, their limitations, and their appropriate applications.
- Inspection Techniques: Train workers on proper inspection techniques, discard criteria, and the use of appropriate inspection tools like calipers, magnetic flux devices, and ultrasonic testers.
7.2 Documentation of Maintenance
- Inspection Records: Maintain detailed records of all inspections, including dates, findings, and any maintenance performed.
- Tracking Rope Life: Document the number of hours or load cycles a wire rope has experienced. This information can help establish a replacement schedule and identify ropes that may be nearing the end of their useful life.
Conclusion
Wire ropes are subjected to significant stresses and wear during their service life, making regular maintenance and care essential for safe and efficient operations. Proper inspection, lubrication, handling, storage, and protection from corrosion are fundamental to extending the lifespan of wire ropes and ensuring they operate safely.
The key aspects of maintaining wire ropes include:
- Frequent and Thorough Inspections: Identify damage early to prevent failures.
- Adequate Lubrication: Maintain lubrication to reduce internal wear and corrosion.
- Proper Handling and Storage: Store ropes correctly to prevent damage and degradation.
- Training and Best Practices: Ensure personnel understand how to properly care for and handle wire ropes.
By following these maintenance and care practices, you can maximize the performance of wire ropes, minimize downtime, and create a safer working environment for your operations.
Chapt 5
How can I extend the lifespan of a wire rope?
Extending the lifespan of a wire rope requires a combination of proper usage, regular maintenance, and adherence to best practices for handling, storing, and operating. Wire ropes face a range of stresses in use—tension, bending, abrasion, and exposure to environmental elements—which can degrade their performance over time. Following specific guidelines helps ensure wire ropes provide maximum performance for as long as possible. Here are the most effective ways to extend the lifespan of a wire rope:
1. Proper Handling and Installation
The way a wire rope is handled and installed has a significant impact on its lifespan. Incorrect handling can introduce kinks, deformation, and early fatigue, compromising the rope’s structural integrity.
1.1 Avoid Kinks and Bends
- Unspooling Properly: When unspooling a new wire rope, never pull the rope from the side of the reel. Instead, place the reel on a turntable and pull the rope straight off or roll it off the spool.
- Correct Handling: Avoid creating loops or twisting the rope in ways that could form kinks. Kinks introduce weak points, permanently deforming the rope, which can lead to premature failure.
1.2 Follow Manufacturer’s Installation Recommendations
- Proper Alignment: During installation, ensure the rope is properly aligned with sheaves and drums. Misalignment can lead to abrasion, flattening, and crushing, reducing the rope’s service life.
- Correct Drum Spooling: Ensure that wire ropes are wound onto drums with appropriate tension. Loose winding can lead to crushing and birdcaging as subsequent layers are applied.
1.3 Appropriate Tensioning
- Controlled Tension: Apply the correct amount of tension when installing the rope. Over-tensioning can lead to overstress and internal damage, while under-tensioning can cause kinks or uneven spooling.
2. Proper Lubrication
Lubrication is essential to reduce friction between the strands, minimize wear, and prevent corrosion. Proper lubrication significantly extends the lifespan of wire ropes.
2.1 Benefits of Lubrication
- Reduce Internal Friction: Internal friction occurs between the individual wires and strands, especially when the rope bends over sheaves or pulleys. Proper lubrication minimizes this internal friction, which extends the rope’s fatigue life.
- Corrosion Prevention: Lubricant protects the rope from moisture and other corrosive elements, preventing rust and pitting that could weaken the wire rope.
2.2 Lubrication Techniques
- Regular Lubrication: Apply lubricant periodically during the rope’s use, based on the manufacturer’s recommendations. The frequency depends on the operating conditions, such as load, speed, and environmental factors.
- Penetrative Lubricants: Use penetrating lubricants that reach the core of the rope, providing complete coverage to protect both the external and internal components. Regularly inspect the rope and add lubrication if the original lubricant appears to be wearing off.
3. Regular Inspections and Preventive Maintenance
Regular inspections are key to identifying damage early and taking corrective action before the rope fails. Preventive maintenance practices can effectively prolong the wire rope’s service life.
3.1 Frequent Visual Inspections
- Daily Checks: Perform a visual inspection of the entire length of the wire rope before each use. Look for signs of wear, broken wires, kinks, crushing, and any other visible damage.
- Periodic In-Depth Inspections: Depending on the intensity of use, conduct thorough inspections weekly or monthly. Use specialized inspection techniques such as Magnetic Flux Leakage (MFL) testing or ultrasonic testing to assess internal integrity.
3.2 Detect and Address Early Signs of Wear
- Replace Damaged Sections: If a localized section of the rope shows damage (e.g., broken wires), consider shortening the rope or splicing in a new section if applicable. If damage is extensive, replace the entire rope.
- Proper Documentation: Record inspection details, including any signs of damage, broken wires, or reduction in diameter. Documenting inspections helps track the rope’s condition over time and determine when replacement is needed.
4. Minimize Abrasion and Mechanical Wear
Abrasion and wear are common factors that reduce the lifespan of wire ropes, especially when they are subjected to rough surfaces, sharp edges, or improper use.
4.1 Use Appropriate Sheave and Drum Sizes
- Matching Groove Size: Ensure that the sheave or drum grooves match the diameter of the wire rope. Grooves that are too small can lead to excessive wear, while oversized grooves can cause the rope to flatten.
- Sheave and Drum Condition: Inspect sheaves and drums for wear or damage that could harm the wire rope. A worn groove may introduce excessive friction and abrasion, shortening the rope’s life.
4.2 Minimize Contact with Rough Surfaces
- Avoid Dragging: Never drag wire ropes across the ground or abrasive surfaces, as this can damage the outer wires and reduce the rope’s strength.
- Protection Against Abrasive Contact: Use protective sheaths or liners on surfaces where the rope is in contact with rough or sharp edges. This helps prevent abrasion and minimizes damage.
5. Avoid Shock Loading and Overloading
Shock loading and overloading are two of the most common causes of premature wire rope failure. It is crucial to understand and avoid these damaging forces.
5.1 Understanding Shock Loads
- Gradual Tensioning: Avoid sudden jerks or rapid application of force to the wire rope, as shock loading creates peak stress levels that can lead to wire fractures and internal core damage.
- Use Proper Lifting Techniques: Always use controlled and gradual tensioning when starting to lift a load. This practice will minimize the risk of shock loading and extend the rope’s lifespan.
5.2 Stay Within Working Load Limit (WLL)
- Know the WLL: The Working Load Limit (WLL) is the maximum load that a wire rope can safely handle. Never exceed the WLL, as overloading can cause permanent damage to the rope and reduce its fatigue life.
- Consider Safety Factors: Use an appropriate safety factor when determining the rope’s load capacity, based on the application type. For personnel lifting, use a higher safety factor to reduce risk.
6. Proper Storage Practices
Storing wire ropes correctly prevents environmental damage such as corrosion and deformation, which can reduce the rope’s strength and performance.
6.1 Store in a Dry and Well-Ventilated Environment
- Protection from Moisture: Moisture is the main cause of corrosion in wire ropes. Store ropes in a dry, well-ventilated area to minimize exposure to moisture.
- Off the Ground: Store ropes elevated off the ground, preferably on wooden pallets or racks. Keeping the ropes away from direct contact with the ground prevents moisture accumulation and rust.
6.2 Avoid Prolonged Exposure to Sunlight
- Shield from UV Radiation: UV radiation from direct sunlight can degrade the rope’s protective lubricant and cause synthetic fibers (in hybrid ropes) to weaken. Store ropes in a shaded or covered area to protect them from UV exposure.
7. Training and Education
Proper handling, maintenance, and inspection require adequate knowledge and training. Ensuring that personnel are trained in best practices helps in extending the lifespan of wire ropes.
7.1 Train Personnel in Proper Handling Techniques
- Educate on Damage Causes: Training personnel on the causes of wire rope damage and how to avoid them is key to preventing unnecessary wear. Employees should understand how to prevent kinks, avoid shock loading, and properly tension wire ropes.
- Inspection Training: Train personnel to conduct thorough visual inspections and identify common signs of wear, such as broken wires, deformation, corrosion, and crushing. The ability to identify problems early will extend the life of the rope and prevent accidents.
8. Use the Right Type of Wire Rope for the Job
Selecting the correct type of wire rope for the specific application can significantly improve its service life. Different applications require different types of wire rope constructions, materials, and coatings.
8.1 Match Construction to Application
- Non-Rotating Ropes for Lifting: For crane hoisting applications, use non-rotating ropes such as 35WxK7 to minimize load rotation. Choosing the wrong type of wire rope can result in premature wear and increased risk of accidents.
- Abrasion-Resistant Ropes: In applications where the rope is exposed to abrasion, such as in mining or dragging, use ropes with fewer but thicker outer wires (e.g., 6×19 construction) to improve abrasion resistance.
8.2 Consider Environmental Factors
- Corrosion-Resistant Ropes: For marine environments, where corrosion is a major concern, use galvanized or stainless steel wire ropes. Specialty coatings, such as plastic jacketing, also help protect against harsh environmental conditions.
- Heat-Resistant Ropes: In applications involving high temperatures, select wire ropes made from materials that can withstand heat without degrading.
9. Use Proper End Fittings and Attachments
The correct use of end fittings and terminations can influence the performance and lifespan of wire ropes. Improperly fitted or damaged terminations can lead to stress concentrations and early failure.
9.1 Correct Termination Methods
- Use Suitable End Fittings: Ensure that end fittings such as thimbles, sockets, clips, and wedge sockets are suitable for the type of rope being used and are installed correctly.
- Avoid Improper Installation: Incorrectly installed terminations can result in reduced strength and increased stress at the termination point. Follow the manufacturer’s guidelines for installation to ensure proper performance.
9.2 Inspect End Fittings Regularly
- Check for Wear and Corrosion: Regularly inspect end fittings for signs of wear, corrosion, and cracks. End fittings are often subjected to high stresses, and any defects could lead to failure.
Conclusion
Extending the lifespan of a wire rope requires a combination of proper handling, regular lubrication, frequent inspection, correct storage, and avoidance of damaging practices like shock loading and overloading. By following these best practices, you can minimize the risk of wire rope failure, reduce downtime, and ensure the safe and efficient use of your wire rope.
Key takeaways include:
- Proper Handling: Avoid kinks and improper unspooling, and ensure correct alignment during installation.
- Lubrication: Regularly lubricate the rope to reduce friction and prevent corrosion.
- Regular Inspections: Identify early signs of wear, deformation, or broken wires through consistent inspection.
- Appropriate Usage: Use the correct type of wire rope, follow load limits, and avoid shock loading.
- Storage Practices: Store ropes in dry, shaded areas to protect against moisture and UV damage.
Implementing these strategies will not only extend the service life of the wire rope but also enhance safety, efficiency, and cost-effectiveness in your operations.
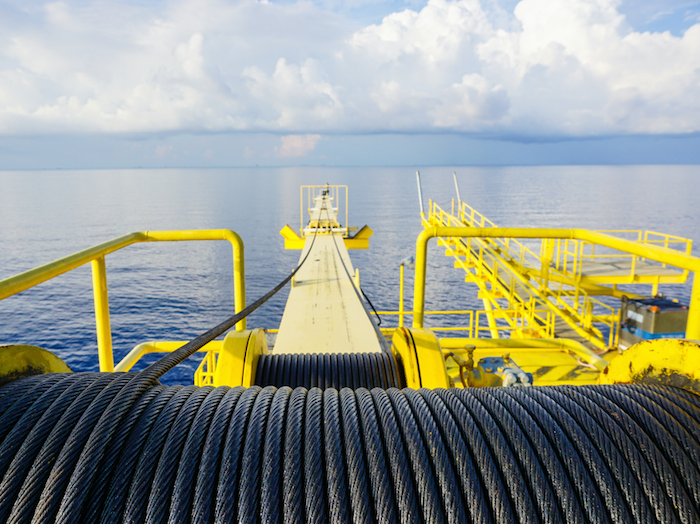
Get the catalogue
Leave a request and we will send you the catalogue with Aulone steel wire ropes by e-mail
86-15573139663
86-15363044363