Spiral Strand Cables
Choose a manufacturer known for producing high-quality spiral strand cables with a proven track record.
High-Performance Wire Ropes and Sling Solutions
Our spiral strand ropes, reinforced with innovative materials and construction techniques, offer unmatched durability, high performance, and safety for demanding static applications. They are an ideal choice for projects requiring robust, long-lasting tension elements.
Main Structure

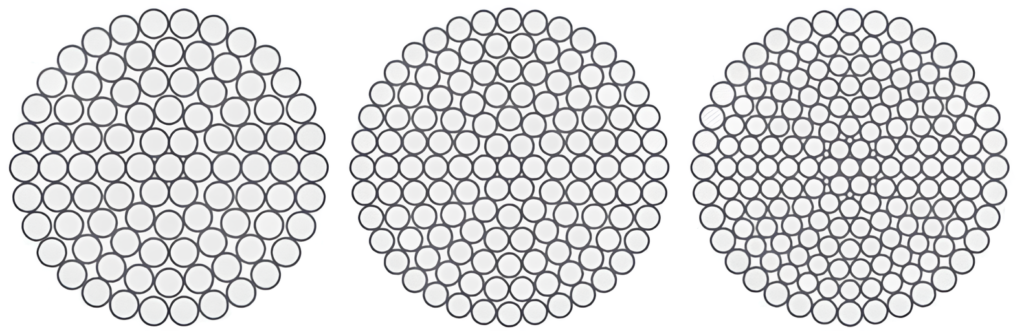
A spiral strand is a composite of multiple layers of helically twisted steel wires. Layers are spun in opposite directions providing constructional and torque stability. The use of high strength steel wires makes it a good candidate as tension member in static applications. Our proprietary Aulone blocking compound fills the cable on the inside, reducing the impact of steel-steel contact, and adding an additional barrier against corrosion.
Features
High aixal stiffness
Excellence Corrosion-resistant duo to Galfan( composed of 95% Zinc and 5% aluminum)
High breaking force because of high strength wires
Good clamping capabilities
Torque balanced due to cross laying
High fatigue resistance
Multiple layers
Parallel contact core
Increased fatigue resistance
Reduces contact stress
Excellent corrosion resistance
Galfan
Galvanized
Rope Type | Typical Construction | Rope Diameter (mm) | |
Wire Rope | Strand | ||
Single-strand wire rope | 1×7 | (1+6) | 6~16 |
1×19 | (1+6+12) | 10~30 | |
1×37 | (1+6+12+18) | 14~42 | |
1×61 | (1+6+12+18+24) | 20~54 | |
1×91 | (1+6+12+18+24+30) | 30~66 | |
1×127~1×631 | — | 50~160 |
Your Ultimate Guide to Acquiring Spiral Strand Cables
When it comes to acquiring spiral strand cables, understanding their features, applications, and factors to consider before purchase is crucial. Spiral strand cables are widely used in structures like suspension bridges, cable-stayed bridges, and other engineering projects that demand high strength and flexibility. Here’s a comprehensive guide to help you navigate your options.
Table of contents
Chapt 1
What is Spiral Strand Cables

Spiral strand cables, a specialized form of wire rope, are integral to numerous structural, mechanical, and marine applications due to their superior mechanical properties. These cables are designed to offer a combination of high tensile strength, excellent flexibility, and resistance to fatigue, making them ideal for situations where cables are subjected to high dynamic loads or require high durability.
Historical Background
The development of wire ropes dates back to the 19th century, with spiral strand cables evolving as a result of technological advancements in metal drawing and fabrication. Originally, these cables were developed to meet the demands of mining and maritime applications, but their use has expanded significantly over the decades.
Design and Structure
Core: The core can be composed of either a fiber material, which provides elasticity and reduces weight, or a smaller wire rope that enhances the structural strength and stability of the overall cable.
Wires and Strands: Around the core, multiple layers of wires are helically wound. Each wire is typically made from high-carbon steel, although other materials like stainless steel or aluminum can be used for specific needs. The wires are usually galvanized or coated to resist corrosion.
Lay Configuration: The wires can be laid in various configurations, with common types being regular lay and lang lay, each offering different benefits in terms of wear and flexibility.
Material Selection
The choice of material for the wires is crucial. High-carbon steel is preferred for its tensile strength and durability, while stainless steel offers better corrosion resistance, important for marine environments.
Chapt 2
Advantage of Spiral Strand Cables
Spiral strand cables, a specific type of wire rope, offer several distinct advantages that make them suitable for a wide range of applications, particularly where strength and flexibility are paramount. Here are some of the key benefits of using spiral strand cables:
High Strength-to-Weight Ratio
Efficiency: Spiral strand cables provide a high strength-to-weight ratio, allowing them to support large loads while being lighter than equivalent strength cables made from other materials. This makes them ideal for applications where weight is a critical factor, such as in suspension bridges or cranes.
Flexibility
Adaptability: The construction of spiral strand cables allows them to be very flexible without sacrificing strength. This flexibility is essential for applications that require cables to bend or loop, such as in lifting applications or architectural structures.
Durability and Longevity
Resilience: These cables are highly durable and resistant to fatigue, which is the weakening of material caused by repeatedly applied loads. They are designed to endure the rigors of heavy use and harsh conditions, resulting in a longer lifespan.
Corrosion Resistance
Material Options: Spiral strand cables can be made from galvanized steel or stainless steel, both of which offer excellent resistance to corrosion. This makes them suitable for marine environments and other settings where exposure to corrosive elements is a concern.
Minimal Stretch
Stability: While all wire ropes exhibit some degree of stretch under load, spiral strand cables are engineered to minimize stretch. This characteristic is crucial in applications where elongation could be problematic, such as structural supports in buildings or bridge
Uniform Stress Distribution
Load Handling: The spiral construction helps in distributing stress evenly across the entire length and cross-section of the cable. This uniform distribution of forces contributes to the cable’s overall strength and durability.
Aesthetic Appeal
Visual Quality: Spiral strand cables have a smooth and uniform appearance, making them aesthetically pleasing. This is a beneficial characteristic for architectural applications where appearance is as important as functionality.
Customizability Versatility: Manufacturers can customize spiral strand cables to meet specific requirements, including varying the core type, the material of the strands, and the configuration. This adaptability allows engineers and designers to specify cables that precisely match the needs of their projects.
Ease of Handling and Installation
Practicality: Despite their strength, spiral strand cables are relatively easy to handle and install because of their flexibility and the fact that they are less prone to kinking than other types of wire rope.
These advantages make spiral strand cables a preferred choice for many engineering, construction, and architectural projects, providing a reliable combination of strength, durability, and flexibility.
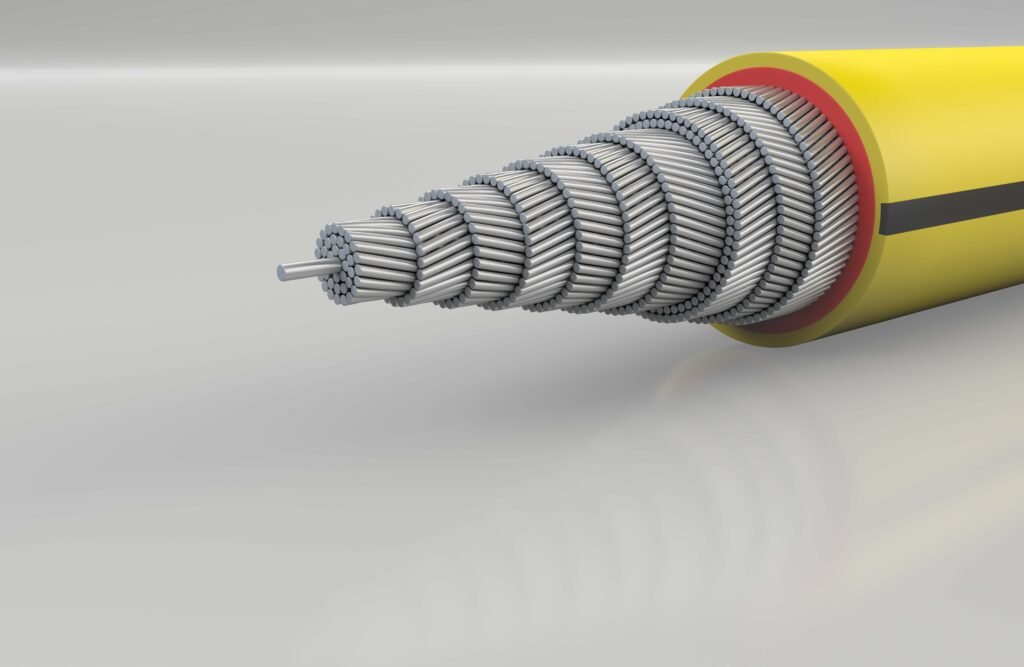
Chapt 3
Spiral Strand Cables Production Procedure
The production of spiral strand cables involves a detailed and precise process to ensure the final product meets high standards of strength, flexibility, and durability. Here’s a step-by-step outline of the production procedure:
1. Raw Material Selection
- Wire Rods: High-quality wire rods, typically made from carbon steel, galvanized steel, or stainless steel, are selected. The choice depends on the required properties of the final product, such as tensile strength and corrosion resistance.
2. Wire Drawing
- Reduction: The wire rods are drawn through a series of dies to reduce their diameter to the desired size. This process involves multiple stages to gradually achieve the required wire gauge.
- Annealing: Between drawing stages, the wires may undergo annealing, a heat treatment process that relieves internal stresses and improves ductility.
3. Surface Treatment
- Cleaning: The drawn wires are cleaned to remove any surface contaminants, such as oxides or lubricants, from the drawing process.
- Galvanizing: For galvanized spiral strands, the cleaned wires are coated with a layer of zinc to enhance corrosion resistance. This can be done through hot-dip galvanizing or electro-galvanizing.
4. Stranding
- Core Formation: The production of spiral strand cables begins with forming the core strand. Several wires are twisted together in a helical pattern to form the core.
- Layering: Additional layers of wires are helically wound around the core. The number of layers and the number of wires per layer depend on the desired diameter and strength of the final cable.
- Tension Control: During the stranding process, precise tension control is essential to ensure uniform winding and prevent kinks or inconsistencies.
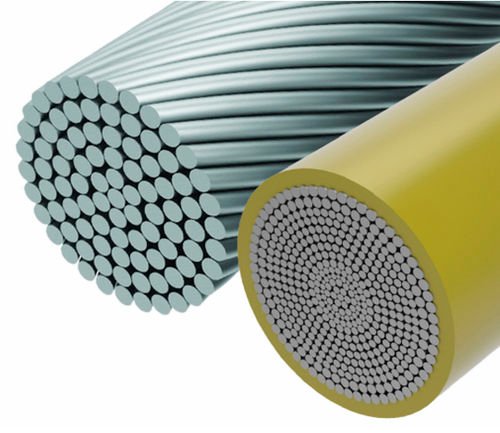
5. Compaction (Optional)
- Compacting: In some cases, the stranded cable is compacted to reduce its diameter and increase its density. This is achieved by passing the cable through a series of compacting dies or rollers.
- Benefits: Compaction improves the cable’s tensile strength and reduces elongation, making it more suitable for high-stress applications.
6. Heat Treatment
- Stress Relieving: The stranded cable may undergo heat treatment to relieve internal stresses and improve its mechanical properties. This process ensures the cable retains its shape and strength during use.
7. Quality Control and Testing
- Dimensional Checks: The cable is inspected to ensure it meets the specified dimensions and tolerances.
- Tensile Testing: Samples of the cable are tested for tensile strength, elongation, and breaking load to verify they meet the required specifications.
- Nondestructive Testing: Techniques such as magnetic particle inspection or ultrasonic testing may be used to detect internal flaws or defects.
8. Coating and Finishing
- Lubrication: Some spiral strand cables are lubricated to reduce friction and wear during use. The lubricant also provides additional corrosion protection.
- Protective Coatings: Additional protective coatings, such as polyethylene or PVC, may be applied for specific applications requiring enhanced environmental resistance.
9. Spooling and Packaging
- Spooling: The finished cables are wound onto spools or reels for easy handling and transportation.
- Packaging: The spooled cables are packaged to protect them from damage during shipping and storage. Packaging may include protective wrapping, wooden crates, or steel drums.
10. Final Inspection and Certification
- Inspection: A final inspection is conducted to ensure the cables meet all quality standards and specifications.
- Certification: The cables are certified according to relevant industry standards and customer requirements. Certification documents may include test reports and compliance certificates.
Summary
The production of spiral strand cables involves careful selection of materials, precise manufacturing processes, and rigorous quality control to ensure the final product meets the required specifications for strength, flexibility, and durability. This comprehensive approach ensures that spiral strand cables are suitable for a wide range of demanding applications across various industries.
Chapt 4
Application of Spiral Strand Cables
Spiral strand cables, also known as spiral ropes or spiral strands, have a variety of applications across different industries due to their unique construction and properties. Here are some key applications:
Structural Engineering and Construction
- Bridges: Spiral strand cables are commonly used in suspension bridges, cable-stayed bridges, and pedestrian bridges due to their high tensile strength and flexibility.
- Buildings: They are used for architectural support, tension structures, and in some cases, for seismic retrofitting.
- Masts and Towers: Spiral strands provide stability and support for radio, TV, and communication towers.
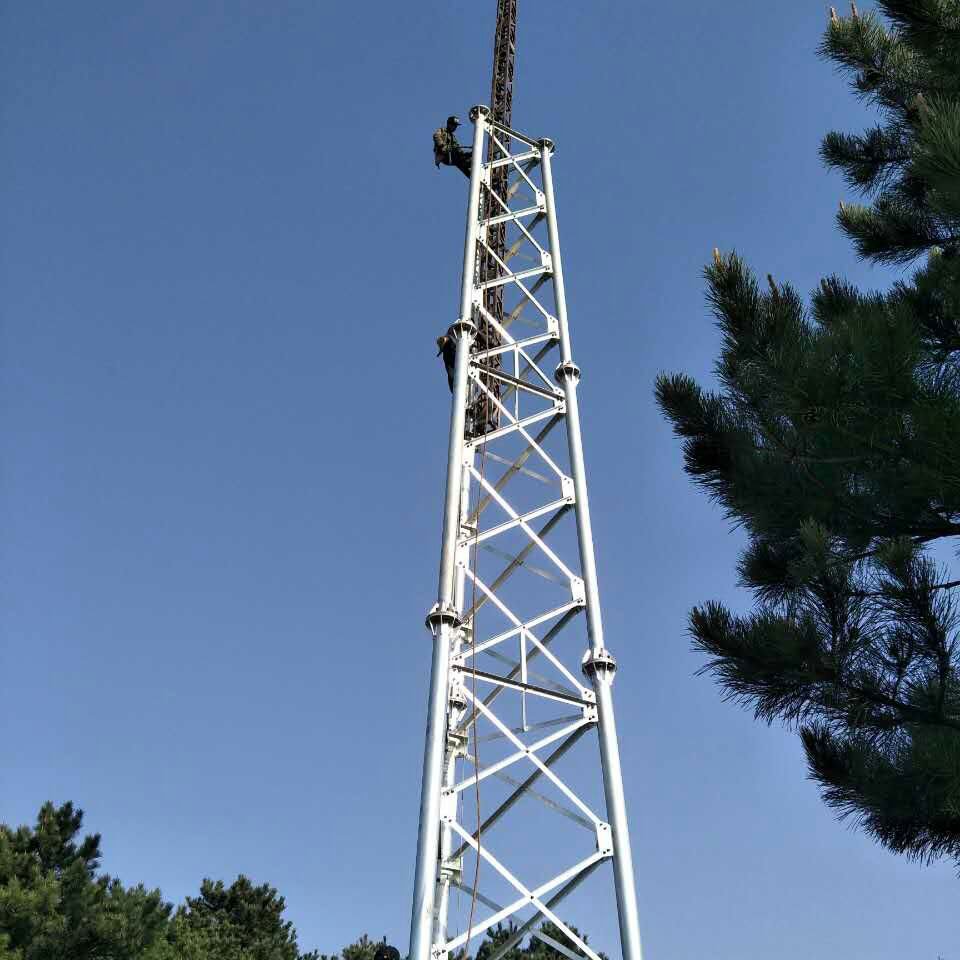
Marine and Offshore
- Mooring Lines: Used to secure ships and floating structures to piers, buoys, or the seabed.
- Rigging: Essential in sailing ships and yachts for standing rigging, which includes the ropes or wires that hold up the mast.
- Anchoring Systems: Used in anchoring offshore platforms and floating wind turbines.

Mining
Applied in shaft hoisting systems, draglines, and other mining equipment for lifting and pulling heavy loads.
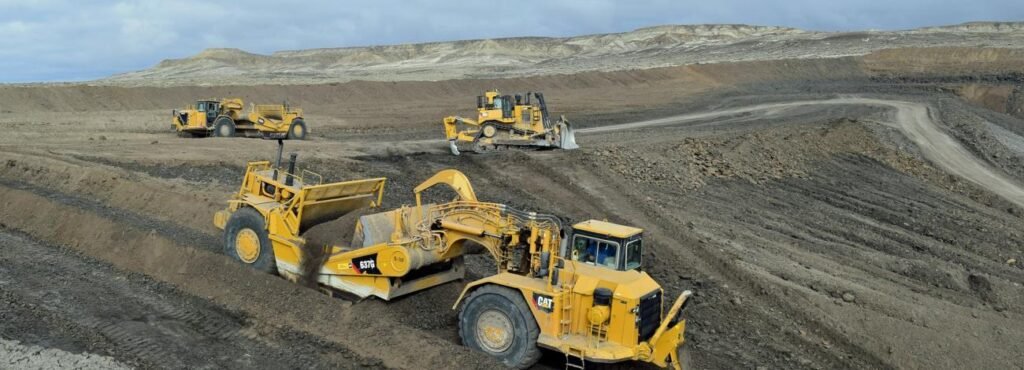
Entertainment and Sports
- Adventure Parks: Used in zip lines and adventure park structures for safety and reliability.
- Theater Rigging: Employed in theaters and stages for hanging and moving set pieces and lighting rigs.

Spiral strand cables’ versatility and robust characteristics make them indispensable across numerous industries, ensuring structural integrity, safety, and operational efficiency in a wide range of applications.
Chapt 5
How To Choose Right Spiral Strand Cables ?
1. Identify Application Requirements
- Load Capacity: Determine the maximum load the cable will need to support, considering both static (constant) and dynamic (variable) loads.
- Environmental Conditions: Assess the environmental conditions the cable will be exposed to, such as temperature, humidity, and corrosive elements (saltwater, chemicals).
- Flexibility and Bend Radius: Understand the required flexibility and the minimum bend radius based on the installation constraints and operational movements.
2. Material Selection
- Galvanized Steel: Suitable for general-purpose applications with moderate corrosion resistance.
- Stainless Steel: Ideal for applications requiring high corrosion resistance, such as marine or chemical environments.
- Carbon Steel: Used for applications where high strength is needed but corrosion resistance is not a primary concern.
3. Cable Construction
- Diameter: Select the appropriate cable diameter based on the load requirements. Larger diameters generally offer higher load capacities.
- Stranding Pattern: The construction of the cable (number of strands and layers) affects its flexibility and strength.
4. Coating and Protection
- Galvanization: Provides basic corrosion resistance and is suitable for outdoor use.
- Polyethylene (PE) or PVC Coating: Offers additional protection against environmental factors and wear.
- Lubrication: Reduces friction and wear in dynamic applications.
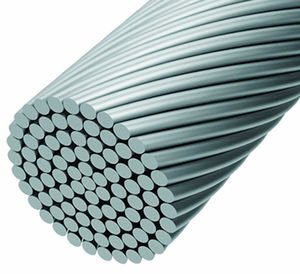
5. Compliance with Standards
- Industry Standards: Ensure the cables meet relevant standards, such as EN (European Norms).
- Certifications: Look for cables that come with certifications confirming compliance with these standards.
6. Manufacturer and Quality Assurance
- Reputable Manufacturer: Choose a reputable manufacturer known for producing high-quality spiral strand cables.
- Quality Control: Ensure the manufacturer follows strict quality control procedures, including testing for tensile strength, elongation, and breaking load.
7. Application-Specific Considerations
- Bridges and Structural Applications: Require high strength, stiffness, and corrosion resistance.
- Marine and Offshore: Need excellent corrosion resistance and flexibility.
- Cranes and Lifting Equipment: Require high tensile strength and flexibility.
- Transmission Lines: Need a balance between strength, flexibility, and corrosion resistance.
8. Cost Considerations
- Budget: Consider the overall cost, including initial purchase, installation, and maintenance.
- Longevity: Investing in higher-quality, more durable cables can reduce long-term costs by minimizing maintenance and replacements.
9. Consultation and Expert Advice
- Consult with Experts: Seek advice from engineers or experts who specialize in spiral strand cables to ensure you select the most suitable cable for your application.
- Technical Support: Choose a supplier that offers strong technical support and after-sales service.
Summary
To choose the right spiral strand cables, thoroughly assess your application requirements, select appropriate materials and construction, ensure compliance with standards, and consider cost-effectiveness. Consulting with experts and choosing a reputable manufacturer can further ensure that you make an informed decision and select a cable that will perform reliably in your specific application.
Chapt 5
Quality Assurance For Spiral Strand Cables
Ensuring the quality of spiral strand cables involves a comprehensive approach to quality assurance (QA) throughout the manufacturing process. Here are the key steps and considerations for maintaining high standards:
1. Raw Material Inspection
- Material Certification: Verify that the raw materials, such as wire rods, meet the required specifications and standards (e.g., ASTM, ISO).
- Chemical Composition: Perform chemical analysis to ensure the material has the correct alloy composition for the desired mechanical properties.
- Mechanical Properties: Test the raw materials for tensile strength, yield strength, elongation, and other relevant mechanical properties.
2. Manufacturing Process Control
Wire Drawing: Monitor the wire drawing process to ensure consistent reduction in diameter and maintain mechanical properties.
- Die Inspection: Regularly inspect and maintain drawing dies to prevent surface defects and ensure uniform wire quality.
- Annealing: Control the annealing process to achieve the desired ductility and relieve internal stresses.
Surface Treatment: Ensure proper cleaning and coating (e.g., galvanizing) of the wires to enhance corrosion resistance.
- Cleaning: Use effective cleaning methods to remove oxides and contaminants from the wire surface.
- Coating Thickness: Measure the thickness of galvanization or other coatings to ensure adequate protection.
3. Stranding Process Control
- Stranding Tension: Maintain consistent tension during the stranding process to prevent kinks and ensure uniform strand formation.
- Helical Winding: Monitor the helical winding process to ensure correct alignment and uniformity of the strands.
4. In-Process Quality Checks
- Dimensional Checks: Measure the diameter and other dimensions of the stranded cable at various stages to ensure compliance with specifications.
- Surface Inspection: Visually inspect the cable for surface defects, such as cracks, pits, or scratches
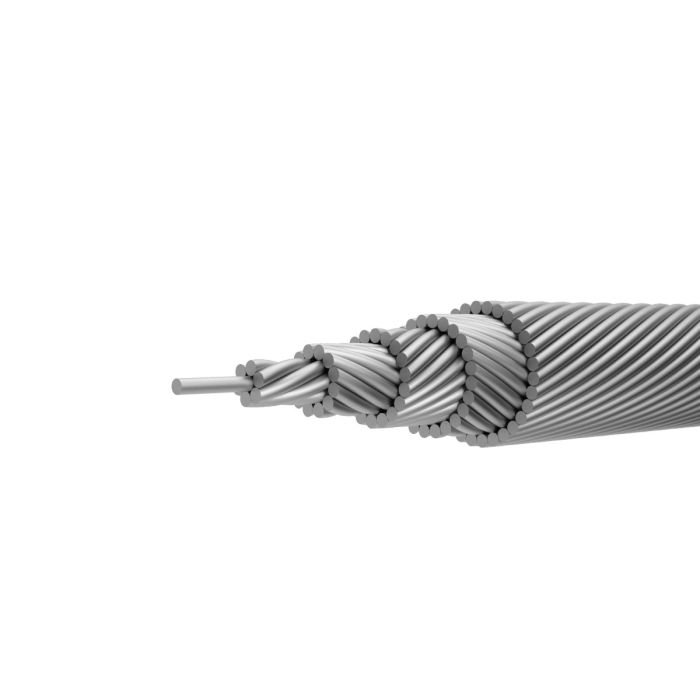
5. Final Quality Testing
- Tensile Testing: Conduct tensile tests on samples of the finished cable to verify its tensile strength, elongation, and breaking load.
- Fatigue Testing: Perform fatigue tests to assess the cable’s durability under cyclic loading conditions.
- Nondestructive Testing (NDT): Use NDT methods such as ultrasonic testing or magnetic particle inspection to detect internal defects without damaging the cable.
- Corrosion Testing: Evaluate the cable’s resistance to corrosion through salt spray tests or immersion tests in corrosive environments.
6. Certification and Compliance
- Industry Standards: Ensure the cables meet industry standards and certifications (e.g., ASTM, ISO, EN).
- Documentation: Maintain detailed records of all tests, inspections, and certifications for traceability and quality control.
7. Packaging and Handling
- Proper Packaging: Package the cables to protect them from damage during transportation and storage.
- Spooling: Wind the cables onto spools or reels to prevent tangling and bending.
- Protective Wrapping: Use protective wrapping materials to shield the cables from moisture, dust, and physical damage.
8. Continuous Improvement
- Feedback Loop: Collect feedback from customers and end-users to identify areas for improvement.
- Process Optimization: Continuously review and optimize manufacturing processes to enhance quality and efficiency.
- Training and Development: Provide regular training for employees on quality assurance practices and updates to industry standards.
9. Supplier Quality Management
- Supplier Audits: Conduct regular audits of suppliers to ensure they meet quality standards and provide high-quality raw materials.
- Supplier Development: Work with suppliers to improve their quality control processes and ensure consistent material quality.
Summary
Quality assurance for spiral strand cables involves rigorous inspection and testing at every stage of the manufacturing process, from raw material selection to final packaging. By adhering to industry standards, maintaining detailed records, and continuously improving processes, manufacturers can ensure the production of high-quality, reliable spiral strand cables.
Get the catalogue
Leave a request and we will send you the catalogue with Aulone steel wire ropes by e-mail
86-15573139663
86-15363044363