Swaged Wire Rope
Aulone swaged wire rope is an excellent choice for forestry and logging applications
High-Performance Wire Ropes and Sling Solutions
Aulone swaged wire ropes are designed to meet the rigorous demands of the forestry and logging industry. Known for their superior strength, flexibility, and durability, these ropes are ideal for various heavy-duty applications in challenging environments.
Mian Structure
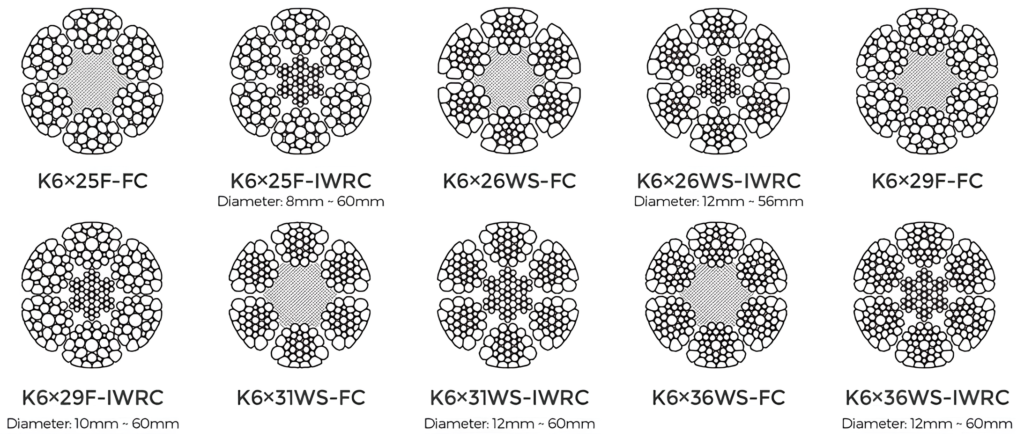
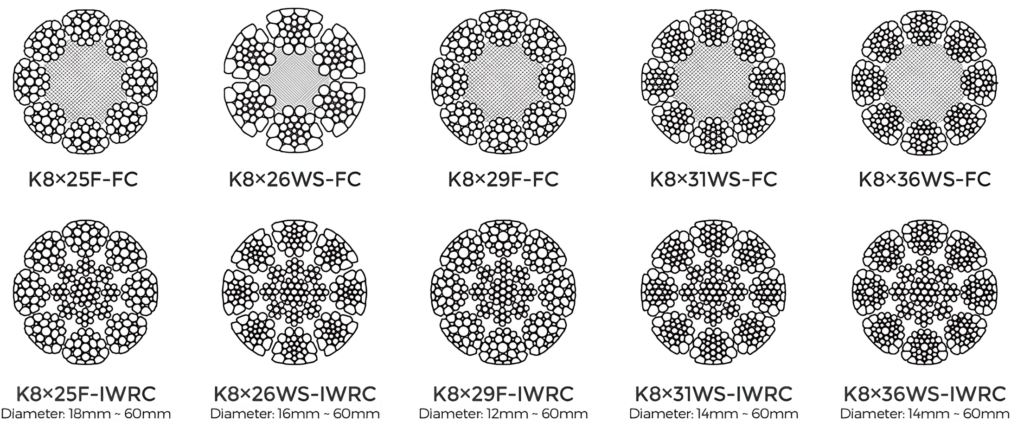
Special wire ropes for your application;
Proven strand design and versatile adaptability;
Long service life;
Fiber core, constant quality;
Low elastic and permanent elongation·Low maintenance costs;
100 % rope quality, high quality assurance;
Fair cost-benefit ratio;
Highly qualified and experienced personnel;
Competent advice;
Reliable service;
Worldwide sales network.
This rope provides higher strength than standard ropes of same diameter while offering greater resistance to drum crushing, scrubbing and similar wear. We utilize a rotary swaging process to produce a compacted crosssection with minium voids and greater surface area on outer wires.
Product Description : Swaged wire rope is manufactured by compacting standard wire rope until the diameter is reduced. The result is a wire rope with greater strength in comparison to standard wire ropes of the same diameter. This denser product can withstand more abuse than standard wire ropes making it popular in the logging industry.
Advantage of Swaged Rope
1) Cutting force is higher compared to the same rope diameter, have a long life.
2) Since the outer shape of the rope is rectangular and extend the life Inclusive of the drum reduces the frictional force.
Diameter | Approx. | Tensile strength (MPa) | |||
1570 | 1770 | 1960 | 2160 | ||
Minimum breaking load (kN) | |||||
10 | 49.0 | 64.4 | 72.6 | 80.4 | 88.6 |
12 | 70.6 | 92.7 | 104 | 116 | 128 |
14 | 96.0 | 126 | 142 | 158 | 174 |
16 | 125 | 165 | 186 | 206 | 227 |
18 | 159 | 209 | 235 | 260 | 287 |
20 | 196 | 257 | 290 | 321 | 354 |
22 | 237 | 312 | 351 | 389 | 429 |
24 | 282 | 371 | 418 | 463 | 510 |
26 | 331 | 435 | 491 | 543 | 599 |
28 | 384 | 505 | 569 | 630 | 694 |
30 | 441 | 579 | 653 | 723 | 797 |
32 | 502 | 659 | 743 | 823 | 907 |
34 | 566 | 744 | 839 | 929 | 1020 |
36 | 635 | 834 | 941 | 1040 | —— |
38 | 708 | 930 | 1050 | 1160 | —— |
40 | 784 | 1030 | 1160 | 1290 | —— |
42 | 864 | 1140 | 1280 | 1420 | —— |
44 | 949 | 1250 | 1400 | 1560 | —— |
46 | 1040 | 1360 | 1540 | 1700 | —— |
Your Ultimate Guide to Acquiring Swaged Wire Rope
When looking to acquire compacted strand wire rope, there are several factors to consider to ensure you get a product that meets your specific needs and standards. Here’s a comprehensive guide to help you navigate the selection process:
Table of contents
Chapt 1
What is Swaged Wire Rope
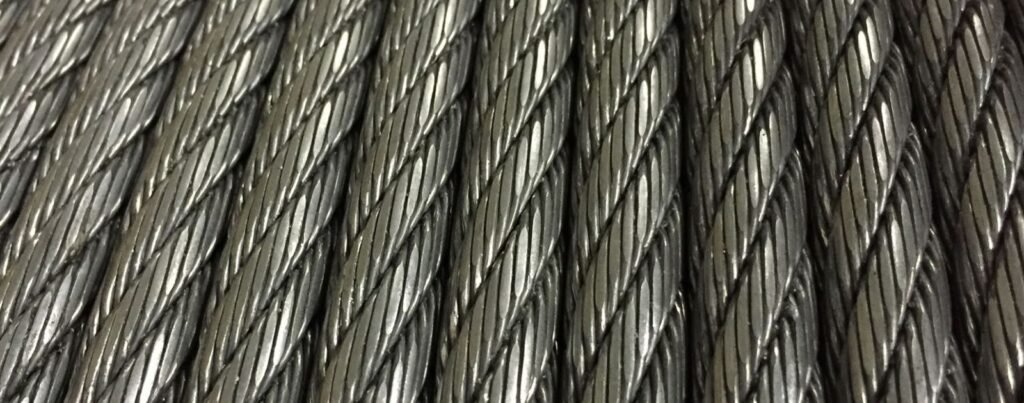
Swaged wire rope is a type of wire rope that has undergone a swaging process to achieve a denser and more compact structure. Swaging involves passing the wire rope through a series of dies that compress and shape the rope, reducing its diameter and increasing its tensile strength.
Understanding Swaged Wire Rope Construction
Swaged wire rope construction is a vital aspect of its design, directly affecting its performance, strength, and suitability for various applications. Let’s dive into the specifics of swaged wire rope construction to help you make an informed choice.
Basic Components of Swaged Wire Rope
Wires: The smallest components, made of steel or other materials. Wires form strands.
Strands: Groups of wires twisted together. The configuration of wires in a strand determines the rope’s characteristics.
Core: The central part around which strands are laid. It can be fiber or steel, providing the foundation for the wire rope.
Common Swaged Wire Rope Constructions
6×19 Construction
Configuration: 6 strands, each containing 19 wires.
Characteristics: Balances flexibility and strength. Suitable for general lifting applications.
Swaging Impact: Increases tensile strength and abrasion resistance, making it robust for various uses.
8×19 Construction
Configuration: 8 strands, each containing 19 wires.
Characteristics: Offers higher flexibility compared to 6-strand ropes, with better resistance to crushing.
Swaging Impact: Improved strength and longevity, suitable for applications requiring frequent bending.
Conclusion
Understanding the construction of swaged wire rope is crucial for selecting the right type for your specific application. By considering the wire, strand, and core configurations, you can ensure optimal performance, safety, and longevity. For expert advice and high-quality swaged wire ropes, reach out to Aulone, where we prioritize rigorous quality control and certification to meet your industrial needs.
Chapt 2
Advantege of Swaged Wire Rope
Swaged wire rope offers several advantages that make it an ideal choice for demanding applications. Here are the key benefits:
Increased Strength
- Tensile Strength: The swaging process compresses the wire rope, aligning the individual wires and strands more tightly together. This increases the rope’s tensile strength, allowing it to withstand greater forces without breaking.
- Load-Bearing Capacity: Because of its increased tensile strength, swaged wire rope can handle heavier loads, making it ideal for high-stress applications such as lifting and rigging.
Enhanced Durability
- Wear Resistance: The compact structure of swaged wire rope enhances its resistance to wear and tear. This makes it more suitable for applications where the rope is subject to constant friction and abrasion.
- Abrasion Resistance: The denser structure also makes the rope more resistant to external damage from rough surfaces, extending its operational life.
Reduced Diameter
- Space Efficiency: By reducing the overall diameter of the wire rope, swaging allows for the use of smaller and lighter components in machinery and structures. This is particularly beneficial in applications with limited space or weight restrictions.
- Improved Handling: The reduced diameter makes the rope easier to handle, install, and manipulate in various applications.
Smooth Surface
- Reduced Friction: A smoother surface results in less friction when the rope runs over pulleys and sheaves, reducing wear on both the rope and the equipment.
- Easier Inspection and Maintenance: A smooth surface makes it easier to inspect the rope for wear and damage, facilitating timely maintenance and ensuring safety.
Improved Flexibility
- Ease of Use: Despite being stronger and more compact, swaged wire rope retains good flexibility. This makes it easier to work with, especially in applications requiring frequent movement or adjustments.
- Adaptability: The flexibility of swaged wire rope allows it to be used in a variety of configurations and setups, adapting to the needs of different applications.
Consistency in Performance
- Uniform Dimensions: The swaging process ensures that the rope has uniform dimensions along its entire length, providing consistent performance and reliability.
- Predictable Behavior: Consistent dimensions and structure mean that the rope behaves predictably under load, enhancing safety and efficiency in its use.
Higher Load Capacity
- Safety Margins: The higher load capacity of swaged wire rope provides greater safety margins in critical applications, reducing the risk of overloading and failure.
- Versatility: This increased capacity makes the rope versatile, suitable for a wider range of tasks and applications.
Cost-Effective
- Longer Lifespan: Although swaged wire rope may have a higher initial cost, its extended lifespan reduces the frequency of replacements, leading to long-term cost savings.
- Lower Maintenance Costs: The enhanced durability and wear resistance of the rope lower maintenance requirements and associated costs.
Conclusion
Swaged wire rope is a versatile and robust solution for a wide range of industrial applications. Its increased strength, enhanced durability, reduced diameter, smooth surface, improved flexibility, consistent performance, higher load capacity, and cost-effectiveness make it a preferred choice in industries such as construction, marine, mining, and logging. These advantages ensure that swaged wire rope meets the demanding requirements of these applications, providing reliability and safety.
Chapt 3
Swaged Wire Rope Production Procedure
Swaged wire ropes are known for their enhanced strength, flexibility, and abrasion resistance, making them suitable for demanding applications. Here’s a detailed overview of the production procedure for swaged wire ropes:
1. Selection of Raw Materials
Wire Selection:
- Material: High-quality steel wires are chosen based on the specific requirements, such as galvanized steel or stainless steel.
- Diameter and Grade: Wires are selected for their appropriate diameter and grade to meet the desired strength and flexibility specifications.
Core Selection:
- Fiber Core (FC): Provides flexibility and cushioning.
- Independent Wire Rope Core (IWRC): Offers higher strength and resistance to crushing.
2. Wire Drawing
Process:
- Drawing Dies: Steel rods are drawn through a series of progressively smaller dies to achieve the desired wire diameter.
- Annealing: The wires are heat-treated to relieve internal stresses and enhance ductility.
3. Stranding
Strand Formation:
- Stranding Machines: Multiple wires are twisted together to form individual strands.
- Lay Direction: The strands are twisted in a specific direction (right or left lay) to ensure consistency in the final product.
Strand Configuration:
- Common Constructions: Includes configurations such as 6×19, 6×36, or 6×26, where each strand contains a specific number of wires.
4. Rope Closing
Core Insertion:
- Core Placement: The chosen core (FC or IWRC) is placed at the center.
- Strand Twisting: The strands are twisted around the core to form the wire rope.
Compaction:
- Preliminary Compaction: In some cases, the rope undergoes a preliminary compaction process to partially reduce its diameter.
5. Swaging
Swaging Process:
- Swaging Machine: The wire rope is passed through a swaging machine equipped with a series of dies.
- Compression: The machine compresses the rope, reducing its diameter and increasing its density.
- Multiple Passes: The rope may pass through several sets of dies to achieve the final desired diameter and compactness.
Benefits:
- Increased Strength: The compression process increases the rope’s breaking strength.
- Abrasion Resistance: The smooth, compact surface reduces wear.
- Flexibility: Maintains necessary flexibility while enhancing durability.
6. Final Processing
Cutting and Length Measurement:
- Precision Cutting: The rope is cut to the required lengths with precision.
- Length Verification: Ensures each segment meets the specified measurements.
End Termination:
- Fittings: End fittings such as sockets, thimbles, or loops are attached if required by the application.
- Swaging of Fittings: Fittings may also undergo a swaging process to secure them firmly to the rope.
Lubrication:
- Coating: The rope is coated with a lubricant to reduce friction and prevent corrosion.
- Application: Lubricants are applied uniformly to ensure complete coverage.
7. Quality Control and Testing
Inspection:
- Visual Inspection: Checks for surface defects, uniformity, and correct construction.
- Dimensional Checks: Verifies diameter, length, and consistency.
Mechanical Testing:
- Tensile Testing: Measures breaking strength to ensure it meets specifications.
- Flexibility Testing: Assesses the rope’s ability to bend without damage.
- Fatigue Testing: Evaluates the rope’s endurance under cyclic loading.
Certification:
- Compliance: Ensures the rope meets industry standards and customer specifications.
- Documentation: Provides certification and test reports as required.
8. Packaging and Delivery
Packaging:
- Protection: Ropes are coiled and packaged to prevent damage during transport.
- Labelling: Each package is labeled with relevant information, including length, diameter, construction, and batch number.
Shipping:
- Transport: Arrangements are made for safe transportation to the customer or end user.
Summary
The production of swaged wire rope involves careful selection of raw materials, precise manufacturing processes, and rigorous quality control to ensure a high-performance product. Each step, from wire drawing to final packaging, is critical in producing a wire rope that meets the demanding requirements of various industrial applications.
Chapt 4
Application of Swaged Wire Rope
Forestry and Logging
The swaged wire rope is a popular choice in the forestry and logging industry due to its excellent balance of strength, flexibility, and durability. Here’s an in-depth look at its applications and benefits in this field:
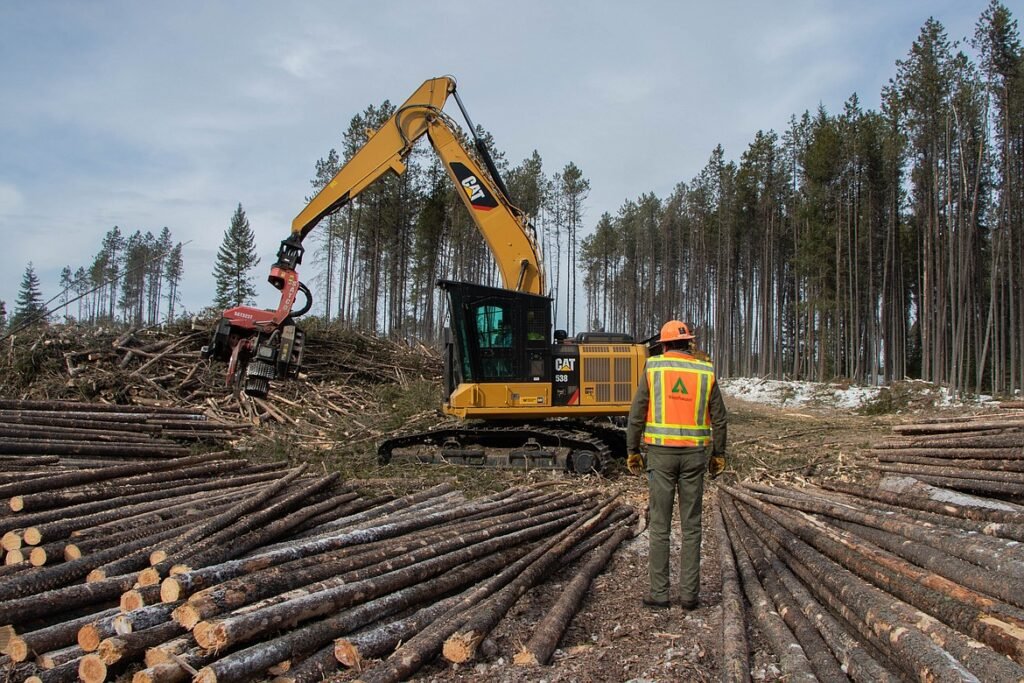
Applications in Forestry and Logging
Skidding:
- Purpose: Dragging felled trees from the cutting site to a landing area where they can be processed and loaded onto transport vehicles.
- Advantages: Aulone 6×26 swaged wire rope’s high strength and abrasion resistance ensure it can withstand the harsh conditions and heavy loads involved in skidding operations.
Yarding:
- Purpose: Transporting logs from the felling site to a central collection point using cable yarding systems.
- Advantages: The rope’s flexibility allows it to navigate through dense forest environments, while its strength ensures safe and efficient transport of large logs.
Winching:
- Purpose: Pulling logs or forestry equipment up steep inclines or across difficult terrain.
- Advantages: The swaged wire rope’s increased breaking strength and compact structure provide the reliability needed for winching applications, ensuring logs and equipment can be moved without rope failure.
Chokers:
- Purpose: Attaching to logs to secure them for dragging or lifting.
- Advantages: Aulone 6×26 construction offers the durability and strength needed to create effective chokers that can handle the stress of lifting and moving heavy logs.
Aulone swaged wire rope is an excellent choice for forestry and logging applications due to its superior strength, flexibility, and abrasion resistance. Its construction and the swaging process make it ideal for the demanding tasks of skidding, yarding, winching, and creating chokers. By ensuring proper maintenance and regular inspections, you can maximize the performance and lifespan of the wire rope, ensuring safe and efficient logging operations.
Chapt 5
Selecting the Right Swaged Wire Rope
Choosing the right swaged wire rope for your application is critical to safety, efficiency, and longevity. This guide will help you choose the right swaged wire rope.
1. Determine Your Application Requirements
Load Capacity:
Determine the maximum load the rope will need to handle.
Determine the safety factor you need. This can range from 5:1 to 10:1, depending on your application.
Flexibility:
Determine the flexibility you need based on the equipment and operation. Wire core ropes are less flexible but stronger, while fiber core ropes are more flexible but may be weaker.
Environmental Conditions:
Consider the working environment, including exposure to moisture, chemicals, extreme temperatures, and abrasion. This will determine the material and coating you need.
2. Understand Swaged Wire Rope Specifications
Diameter and Construction:
Choose the right diameter based on your load requirements and equipment specifications.
Choose the right construction (e.g., 6×19, 6×36) based on the flexibility and strength you need.
Material and Coating:
Common materials include galvanized steel for corrosion resistance and stainless steel for high corrosion and chemical resistance.
Consider coatings that provide additional protection, such as plastic or zinc.
Core Types:
Fiber Core (FC): Provides flexibility and cushioning. Good for applications where you bend the rope a lot.
Independent Wire Rope Core (IWRC): Provides more strength and resistance to crushing. Good for heavy-duty applications.
3. Evaluate Performance Characteristics
Breaking Strength:
Make sure the rope’s breaking strength is greater than the maximum load you will put on it, including your safety factor.
Abrasion Resistance:
Swaged ropes have good abrasion resistance because they are compact. Choose a rope that can handle the abrasion in your application.
Fatigue Resistance:
Consider the rope’s fatigue resistance, especially if you will bend and load it repeatedly.
4. Certification and Quality Standards
Industry Standards:
Make sure the rope meets the relevant industry standards, such as ISO, or EN. This ensures the rope meets the minimum safety and performance requirements.
Supplier Quality Assurance:
Choose a supplier that has good quality control, including regular testing and certification of their products.
5. Customization Options
Custom Solutions:
Many suppliers can customize the rope to meet your specific needs, such as:
Custom diameters and lengths.
Special coatings or materials.
Specific constructions or core types.
Consultation:
Work with suppliers to get the right wire rope for your needs. Give them as much information as possible about your application to get the best recommendations.
Conclusion
Choosing the right swaged wire rope involves understanding your application requirements, evaluating performance characteristics, and making sure the product meets industry standards and certifications. By considering these factors and working with a reputable supplier, you can get a wire rope solution that is safe, efficient, and long-lasting.
Chapt 6
Quality Assurance for Swaged Wire Rope
Ensuring the quality of swaged wire rope is crucial for safety, performance, and longevity in demanding applications. Here is a comprehensive overview of the quality assurance processes for swaged wire rope production:
1. Raw Material Inspection
Wire Material:
- Chemical Composition: Verify that the steel used meets the required chemical composition for strength and corrosion resistance.
- Mechanical Properties: Check tensile strength, ductility, and toughness to ensure the wire meets the desired specifications.
Core Material:
- Type and Quality: Ensure the selected core (fiber or independent wire rope core) meets the required standards for flexibility and strength.
- 2. Wire Drawing Quality Control
Die Inspection:
- Precision: Ensure drawing dies are within tolerance to produce wires of uniform diameter.
- Surface Finish: Verify that dies are free from defects to prevent surface imperfections on wires.
Wire Testing:
- Diameter Consistency: Regularly measure wire diameters to maintain consistency.
- Surface Quality: Inspect for surface defects such as scratches, pits, or corrosion.
- 3. Stranding Process Control
Strand Formation:
- Tension Control: Maintain consistent tension during stranding to avoid variations in strand diameter.
- Lay Length: Ensure the lay length (pitch) of the strands is consistent with design specifications.
Strand Testing:
- Visual Inspection: Check for uniformity and absence of kinks or twists.
- Diameter Verification: Measure strand diameters to ensure they meet specifications.
4. Rope Closing and Compaction Quality Checks
Core Placement:
- Alignment: Ensure the core is centered and strands are evenly distributed around it.
Compaction Process:
- Preliminary Checks: Conduct preliminary inspections to ensure the rope is correctly aligned before swaging.
- Swaging Machine Calibration: Regularly calibrate the swaging machine to maintain consistent compression.
- 5. Swaging Quality Assurance
Swaging Process Control:
- Die Condition: Inspect swaging dies regularly for wear and replace as needed.
- Compression Uniformity: Ensure the rope passes uniformly through all dies to achieve consistent compaction.
Post-Swaging Inspection:
- Diameter Measurement: Verify that the final diameter is within specified tolerances.
- Surface Inspection: Check for smoothness and absence of surface defects.
6. Final Processing Quality Control
Cutting and Length Measurement:
- Precision Cutting: Ensure cuts are clean and lengths are accurate.
- Dimensional Verification: Confirm that all lengths match customer specifications.
End Termination:
- Attachment Quality: Inspect fittings and terminations for secure attachment and proper swaging.
- Load Testing: Conduct load tests on terminations to verify their strength and reliability.
Lubrication:
- Application Consistency: Ensure lubricant is evenly applied and penetrates the rope structure.
7. Mechanical Testing and Certification
Tensile Testing:
- Breaking Load: Perform tensile tests to confirm the rope’s breaking load meets or exceeds specifications.
- Elongation: Measure elongation to ensure it falls within acceptable ranges.
Fatigue Testing:
- Cyclic Loading: Test ropes under repeated loading cycles to evaluate their fatigue resistance.
Bend Testing:
- Flexibility: Assess the rope’s ability to bend without breaking or kinking.
Abrasion Testing:
- Wear Resistance: Simulate abrasive conditions to test the rope’s durability under friction and wear.
- 8. Documentation and Compliance
Quality Records:
- Batch Records: Maintain detailed records of each production batch, including material certifications and test results.
- Traceability: Ensure all components and processes are traceable to their source.
Certification:
- Industry Standards: Verify compliance with relevant industry standards such as EN etc.
- Customer Specifications: Ensure all customer-specific requirements are met and documented.
- 9. Packaging and Final Inspection
Packaging:
- Protection: Use appropriate packaging materials to protect the rope during transport and storage.
- Labeling: Clearly label each package with relevant information, including product specifications and batch numbers.
Final Inspection:
- Visual Check: Conduct a final visual inspection to confirm the rope is free from defects.
- Dimensional Check: Verify that all dimensions are accurate and within specified tolerances.
Summary
Quality assurance for swaged wire rope involves a comprehensive series of inspections, tests, and controls throughout the production process. From raw material selection to final packaging, each step is critical to ensuring the rope’s performance, safety, and reliability in its intended applications. By adhering to stringent quality assurance procedures, Aulone can deliver high-quality swaged wire ropes that meet the demanding requirements of various industries.
Get the catalogue
Leave a request and we will send you the catalogue with Aulone steel wire ropes by e-mail
86-15573139663
86-15363044363