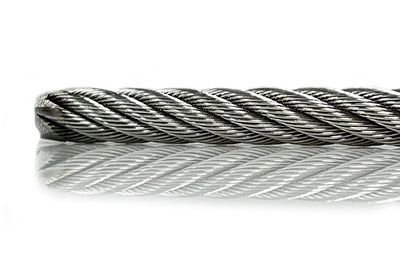
Opening paragraph: Have you ever wondered why some wire ropes are easier to handle than others? It makes a big difference. Choosing the wrong one can cause real problems for your project.
Snippet paragraph: The core difference lies in how wires and strands are shaped during manufacturing. Preformed wire rope has wires and strands pre-shaped before closing, making it more stable and coil-resistant.
Transition paragraph: I remember a time when I was just starting out in my factory, learning about wire ropes. The idea of “preforming” seemed small at first. But when I saw it in action, I understood its big impact. (Personal story placeholder: I will add a short anecdote about handling a non-preformed rope vs. a preformed one and the immediate difference in stiffness/ease of spooling.)
Preformed wire rope is a modern choice. It greatly changed how we make and use wire ropes. Most ropes made today use this method.
Preformed wire rope has individual wires and strands shaped into a helical form before the rope is laid. This process makes the rope more stable. It reduces internal stresses within the rope structure.
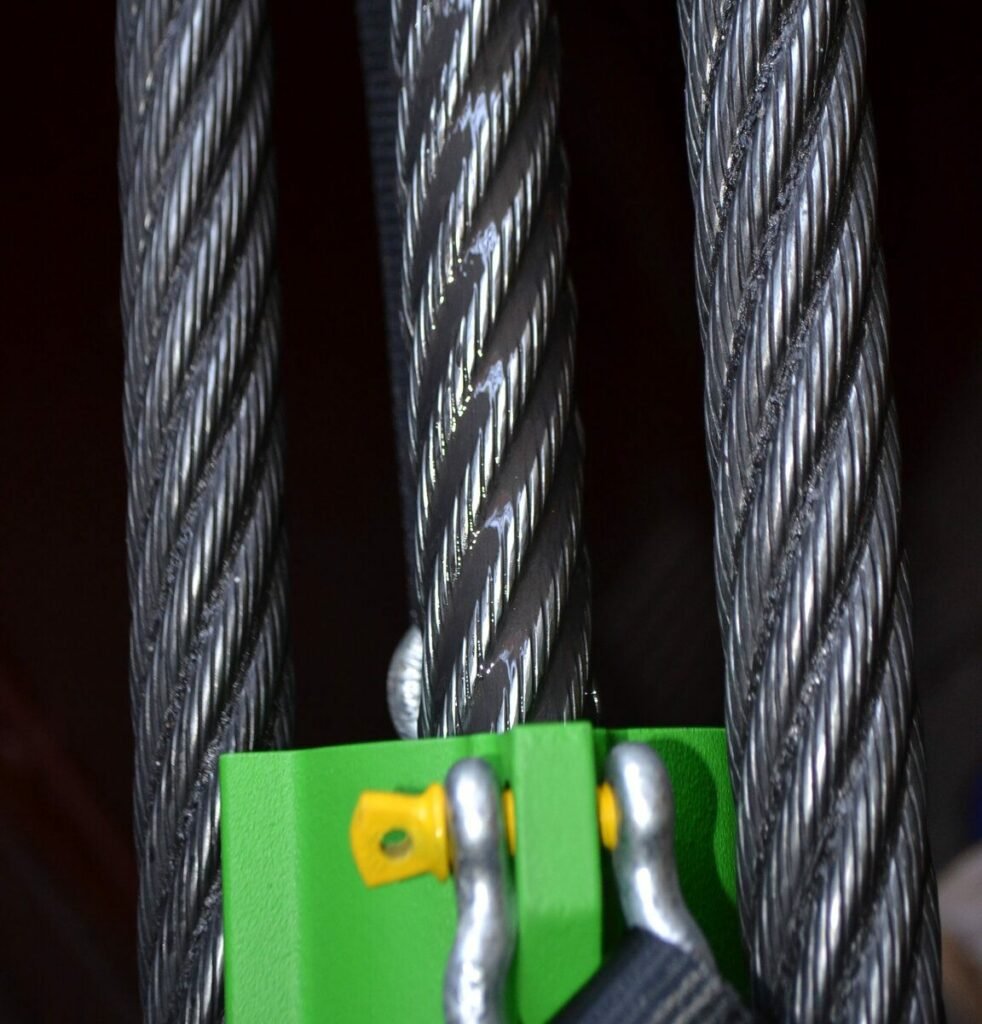
When we talk about preformed wire rope, we are looking at its birth process. Each wire and each strand is given its spiral-like shape first. Then, we assemble them into the final rope. This might sound like a small step, but it is very important.
Key Benefits of Preformed Wire Rope
This pre-shaping brings many advantages. It makes the rope much more stable. When you cut a preformed wire rope, its strands do not spring apart. This “dead” characteristic is a huge plus. It means less time is spent handling the rope and more safety.
Consider a scenario: imagine a crane needing new wire rope. If the rope is preformed, my team can install it with less effort. It uncoils smoothly from the reel. It resists kinks and loops. This saves time and reduces frustration on site. This is a common requirement for customers like Maksim, who are focused on efficient operations.
- Ease of Handling: It is easier to unreel and install. This means less work for operators.
- Resistance to Kinking: It does not form loops easily. This adds to safety.
- Reduced Internal Stress: The wires and strands fit together naturally. This makes the rope last longer.
- Longer Service Life: Less stress means less wear and tear over time.
- Better Fatigue Resistance: It handles repeated bending better. This is key for dynamic applications.
How Preforming Improves Safety and Efficiency
Safety is very important in operations. A preformed rope will not unravel easily if a wire breaks. This holds its shape even under damage. For my Aulone factory, we focus on high quality. We know safety is paramount. Our preformed ropes, like those supplied for mining or crane use, meet tough standards. They help prevent accidents. We are proud to offer certifications like BV & CE to show our commitment.
Feature | Preformed Wire Rope |
---|---|
Ease of handling | Very easy |
Kink resistance | High |
Internal stress | Low |
Spooling | Smooth |
Cutting stability | Excellent |
Non-preformed wire rope is the older way of making ropes. It was common before modern methods came along. It has its own specific features.
Non-preformed wire rope has its wires and strands laid together straight, without prior shaping. This method results in higher internal stresses. The rope will unlay or “birdcage” if not secured properly.
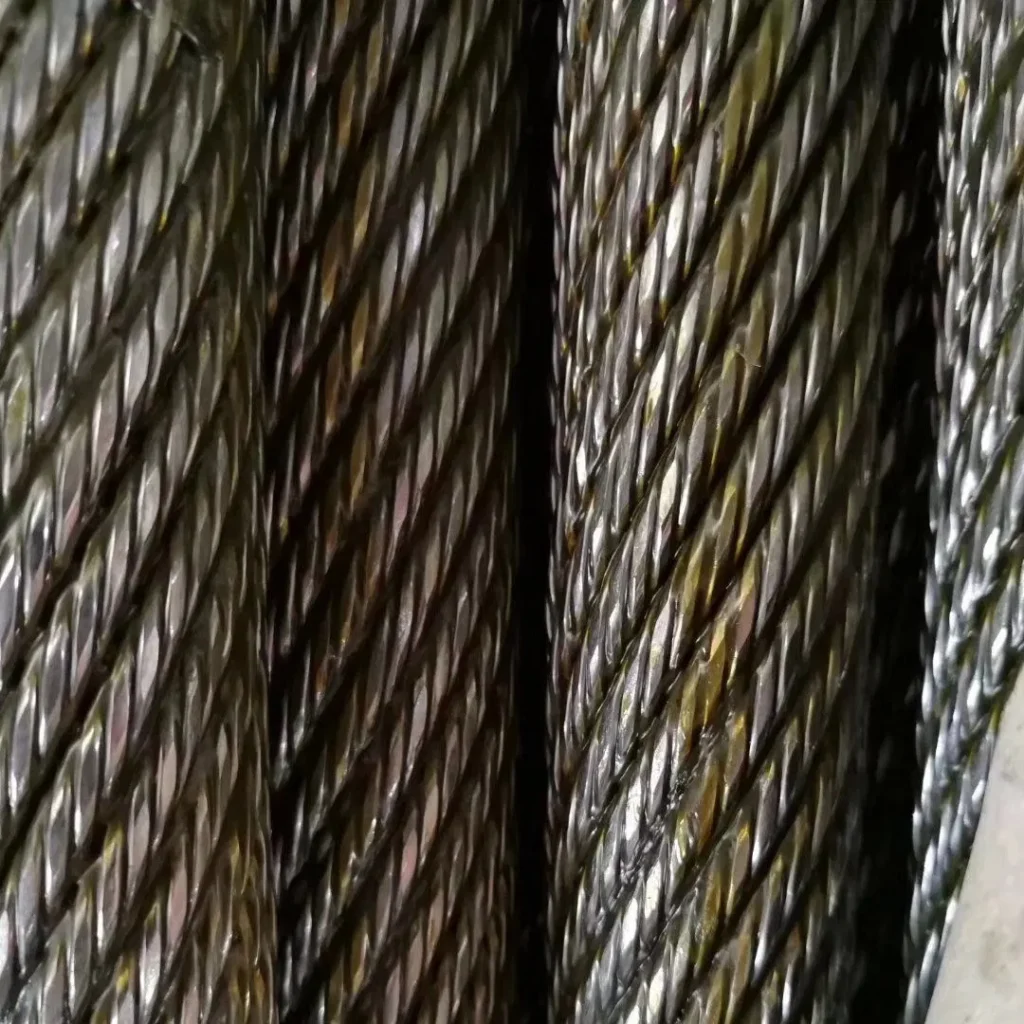
With non-preformed wire rope, we assemble it directly. The wires and strands are wound together without first curving them. This creates tension inside the rope structure. Think of it like trying to bend a straight piece of metal into a curve without any pre-bending. It wants to spring back.
Challenges with Non-Preformed Wire Rope
This internal tension causes several challenges. When you cut a non-preformed rope, the strands will quickly unlay. They “birdcage” or fan out. This makes it hard to work with. It also makes it less safe if not handled correctly. For this reason, extra care is needed when installing or cutting non-preformed ropes.
For example, when I saw non-preformed ropes, they needed special seizing at the ends. This means wrapping the ends tightly with thin wire before cutting. If you didn’t do this, the rope would unravel right before your eyes. This added steps to any job. It took more time and effort. This is why many people prefer preformed ropes now.
- Kinking Tendency: It can form kinks or loops easily. This creates safety risks.
- High Internal Stress: Wires and strands are under constant tension. This can shorten rope life.
- Difficult Handling: It is harder to unreel and work with without proper tools.
- Unravelling Risk: If not seized, it unlays easily when cut. This can be dangerous.
- Reduced Fatigue Life: The internal stresses make it wear out faster.
When are Non-Preformed Ropes Used?
Even with these challenges, non-preformed ropes still have some uses. They might be chosen for specific applications where the rope will not be subjected to much bending or movement. Sometimes, they are used in very short lengths or for fixed applications. However, their use has greatly decreased. Most modern applications require the benefits that preformed rope offers.
Feature | Non-Preformed Wire Rope |
---|---|
Ease of handling | Difficult |
Kink resistance | Low |
Internal stress | High |
Spooling | Challenging |
Cutting stability | Poor without seizing |
Preforming truly changes how wire rope behaves. It impacts everything from handling to how long it lasts. Let us look at these key differences.
Preforming greatly improves a wire rope’s handling characteristics by reducing internal stresses. It makes the rope more flexible and resistant to deformation. This leads to a longer lifespan and safer operation across various applications.
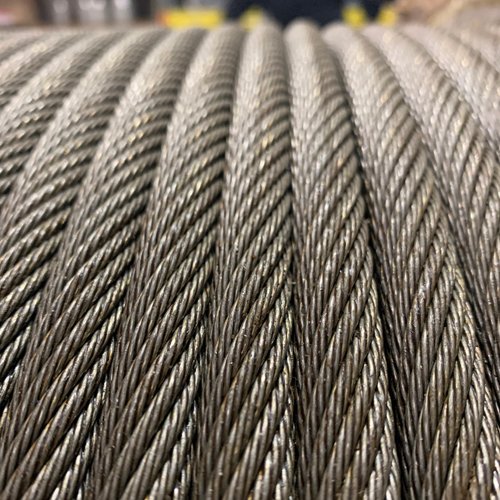
The preforming process is a significant technical advancement. It means that each strand and wire inside the rope is already in its relaxed, helical shape. When these pre-shaped components are assembled, they fit together naturally. There is no force trying to make them lay straight. This makes the entire rope structure calm and stable.
The Impact on Performance and Durability
This calmness means the rope does not fight itself from the inside. This greatly reduces internal friction and wear. For instance, when a preformed rope bends over a sheave, the strands can move and adjust with less resistance. This helps the rope last much longer in dynamic applications. My high-quality wire ropes from Aulone must meet tough standards. We understand these principles well. Our ropes are durable and perform excellently.
Consider the example of purchasing managers. They often look for high-tensile strength and high breaking load. But they also need ropes that are reliable. A rope that lasts longer means fewer replacements. This saves money in the long run. My factory ensures our products meet EN12385-4. This is a key quality sign for customers.
- Fatigue Life: Preformed ropes resist bending fatigue better. This is crucial for cranes.
- Wear Resistance: Less internal friction means less wear. The rope maintains its strength longer.
- Smoothness in Operation: Preformed ropes run smoother over drums and sheaves. This reduces wear on equipment.
- Reduced Rotation: Often, preformed ropes have better rotational stability. This is vital for lifting loads.
Comparison of Key Characteristics
Characteristic | Preformed Wire Rope | Non-Preformed Wire Rope |
---|---|---|
Internal Stress | Low | High |
Handling | Easy, flexible | Stiff, prone to kinking |
Resistance to Kinks | Excellent | Poor |
Fatigue Life | Extended | Shorter |
Stability when Cut | Holds shape | Unravels, birdcages |
Cost (Generally) | Slightly Higher (initial) | Lower (initial) |
Lifespan | Longer in most applications | Shorter in dynamic applications |
Selecting the correct wire rope is very important. It affects safety, cost, and how long your project lasts. I want to help you make the best choice.
Choose preformed wire rope for most modern applications, especially those involving movement or frequent handling, due to its superior stability and longer lifespan. Non-preformed ropes have limited, niche uses where internal stress is less critical.
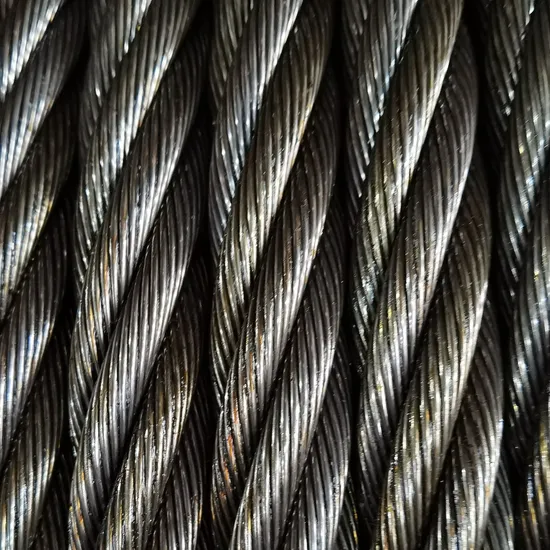
Making the right choice depends on your specific application. As an experienced supplier from Aulone in China, I have helped many customers. Understanding requirements is key. For example, a customer buying 1,000 tons of wire rope per year needs consistency. They need a product that performs every time. They also worry about pricing, quality control, and certifications.
Factors to Consider for Selection
- Application: Is the rope for static mooring, lifting, or continuous operation? For cranes, elevators, or mining, preformed is almost always the better choice. It handles continuous bending. For static overhead lines, non-preformed might still work.
- Operating Conditions: Will the rope face extreme temperatures, corrosive environments, or constant friction? Our galvanized and stainless steel options handle harsh conditions well. Plastic impregnated ropes can also offer a long service life.
- Safety Requirements: If human life or high-value equipment is involved, go for the safest option. Preformed wire ropes are inherently safer due to their stability. My factory ensures all our ropes meet strict international standards, like EN12385-4. We can provide BV, CE, RMRS, DNV, and ABS certificates. This gives our clients peace of mind.
- Budget vs. Lifespan: While non-preformed might be cheaper initially, the cost of frequent replacement or potential failure often outweighs the initial saving. Investing in quality preformed rope usually pays off in the long run. My team at Aulone is dedicated to offering high-quality solutions that are also competitively priced. We export to places like Russia, Canada, and Australia. We understand varied market needs.
If you are a purchasing manager, you need reliable products. You also need good prices. At Aulone, we have four production lines. This allows us to produce quality products efficiently. We ship to many countries. This experience helps us offer competitive pricing without sacrificing quality.
Seeking Expert Advice
It is always good to consult with experts. My team and I are always ready to help. We can look at your specific needs. Then we can recommend the best wire rope type and construction. We can even advise on the best material, like synthetic rope for marine uses or specialized assemblies. My goal is to make sure you get the right rope for your job, efficiently and safely.
When choosing wire rope, quality control is not just a buzzword. It is a promise. It ensures the rope will perform as expected.
Strict quality control and reliable certifications are essential. They guarantee that wire ropes meet performance and safety standards. Our factory, Aulone, ensures products like ours pass rigorous tests and hold global certifications.
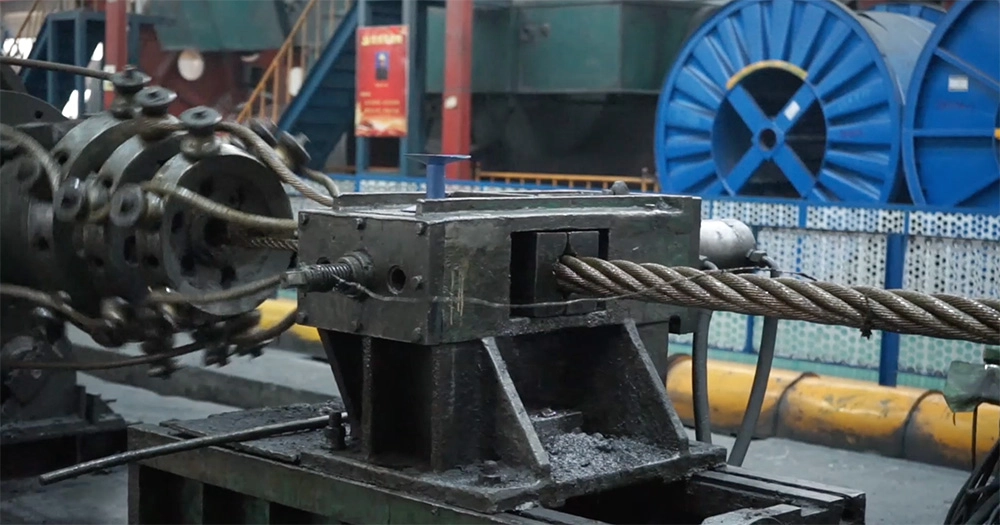
Many buyers face pain points with quality control and certifications. It can be hard to trust new suppliers. This is especially true after seeing varying quality from different sources. My factory in China, Aulone, takes quality seriously. We know our products are critical parts of our customers’ operations.
Our Commitment to Quality
First, we use only high-quality raw materials. We check every step of production. From melting the steel to forming the final rope, our team watches everything. We have four production lines. Each line follows strict checks. This results in high tensile strength and high breaking load. These features are not just numbers. They mean the rope can handle heavy loads safely.
The Role of Certifications
Certifications are proof of quality. They show that our products meet global standards. We can provide several important certificates:
- BV & CE: For general quality and conformity in Europe.
- RMRS: For marine use.
- DNV & ABS: Key for marine, oil and gas, and specific industrial uses.
For a customer who values strict quality control and certifications, my ropes are a strong choice. When I supply a cable, it comes with the promise of reliability. I have seen the challenges customers face when they cannot trust their suppliers. We want to be a partner you can trust. Our export history to countries like Russia, Saudi Arabia, and Canada shows our global reach and trust.
Conclusion
Summary for the whole post: Preformed wire rope offers superior stability and handling. It is the best choice for most uses. Non-preformed rope has limited, specific roles. Always pick based on your project needs and prioritize quality.