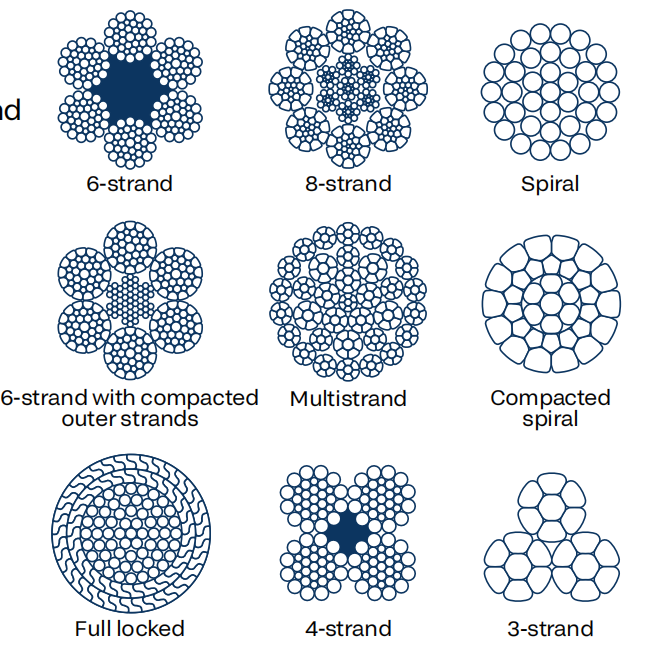
Are you struggling to find the right wire rope for your mining operations? Are broken ropes costing you time and money? Choosing the wrong type can lead to big problems.
Mining wire ropes come in various types, including hoist ropes, drag ropes, and shovel ropes. They differ in construction, strength, and durability, designed for specific mining tasks.
I know how frustrating it is when equipment fails. I once saw a small mistake create a huge delay. Let’s make sure that doesn’t happen to you.
What are hoist ropes? How do they lift heavy loads safely?
Mining operations often require lifting very heavy items. This is where hoist ropes truly shine. They are a core part of many mining machines.
Hoist ropes are designed to lift and lower material in mine shafts or open pits. They are built for extreme strength and fatigue resistance, ensuring safe and efficient lifting.
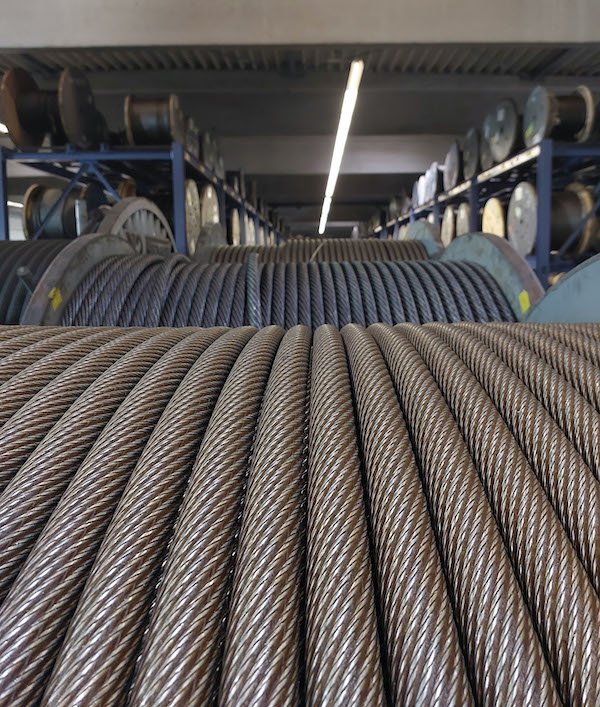
When we talk about hoist ropes, we are discussing the backbone of many lifting systems. They need to handle incredible tension and repeated stress.
How are hoist ropes constructed?
Hoist ropes usually feature a specific construction to maximize their lifting power and lifespan.
- Core Type: Often use a steel core for added strength.
- Strand Count: Typically 6 or 8 strands.
- Lay Direction: Usually use regular lay, but lang lay can offer more flexibility.
- Lubrication: Well-lubricated to reduce internal friction.
Let me explain the details. The core of the rope, whether fiber or steel, provides critical support. A steel core, in particular, adds significant strength and prevents crushing. Then, we have the strands. These are individual wires twisted together. The more strands, often the more flexible the rope.
What stress do hoist ropes endure?
These ropes work hard. They face constant pulling, bending, and abrasive forces.
- Tension: High loads cause immense tension.
- Bending Fatigue: Ropes bend over sheaves and drums.
- Abrasion: Contact with equipment and materials causes wear.
- Corrosion: Moisture and chemicals can degrade the rope.
I always explain to my clients that understanding these stresses is key. For example, consistent bending over small sheaves can cause premature failure, even for a high-quality rope. This is why following equipment specifications is so important.
Why is inspection key for hoist ropes?
Regular inspection of hoist ropes is not just a recommendation; it’s a must. Safety depends on it.
Inspection Point | What to Look For | Why it Matters |
---|---|---|
Broken Wires | Visible broken strands | Reduces strength, can lead to sudden failure |
Abrasion | Worn outer wires, reduced diameter | Weakens the rope, indicates excessive wear |
Corrosion | Rust, pitting, discoloration | Damages wire integrity, reduces lifespan |
Deformation | Kinks, core protrusion, birdcaging | Indicates structural damage, unsafe operation |
Lubrication Loss | Dry, gritty surface | Increases internal friction, speeds up wear |
Through years of helping factories, I’ve seen firsthand how vigilance here saves lives and money. Early detection of problems means you can replace a rope before it fails catastrophically.
What are drag ropes? How do they pull and move material?
Drag ropes are unsung heroes in open-pit mining. They are constantly pulling and enduring tough conditions.
Drag ropes are specifically designed for dragline excavators and similar pulling systems. They are built to withstand severe abrasion, shock loads, and continuous dragging forces across rough terrain.
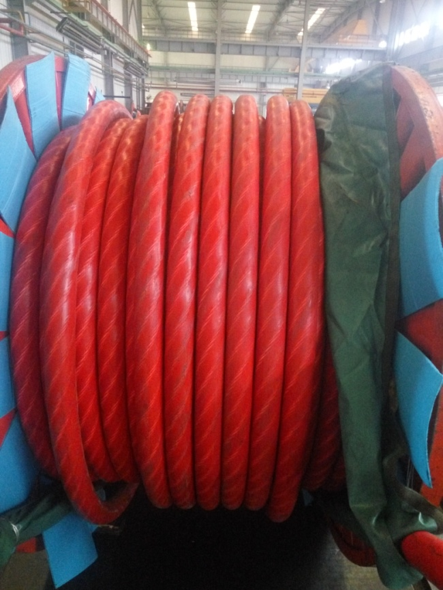
When I talk to clients about drag ropes, I emphasize their toughness. These ropes are not just lifting; they are experiencing significant friction with the ground and immense shock when the bucket digs into rock.
What makes drag ropes unique?
Their construction is built for extreme wear and tear. They are different from ropes that only lift.
- Larger Wire Diameter: Often use thicker wires for greater abrasion resistance.
- Specialized Lay: Can use specific lay types to manage rotational forces.
- High Strength Grade: Made from steel with very high tensile strength.
- Robust Lubrication: Contains heavy-duty lubricant to protect against dirt and moisture.
From my factory’s perspective, manufacturing drag ropes requires precision to ensure each wire contributes to the overall strength and durability needed for these demanding applications.
What are common challenges for drag ropes?
They face a unique set of challenges that need careful consideration.
- Severe Abrasion: Constantly dragged through abrasive materials like rock and dirt.
- High Shock Loads: Experience sudden jolts when the bucket hits hard material.
- Fatigue: Repetitive bending and pulling cycles cause material fatigue.
- Corrosion: Exposed to weather and sometimes corrosive ground conditions.
I’ve advised many purchasing managers from mining giants on how to handle these challenges. It often comes down to choosing a rope specifically engineered for these conditions, not just a general-purpose one. Quality upfront saves a lot down the line.
What are shovel ropes? How do they handle heavy digging?
Shovel ropes are vital for the large electric shovels used in mining. They share some characteristics with hoist ropes but have their own demands.
Shovel ropes are used on electric shovels to raise and lower the dipper and crowd the boom. They are designed for high strength, excellent flexibility, and resistance to impact and abrasion.
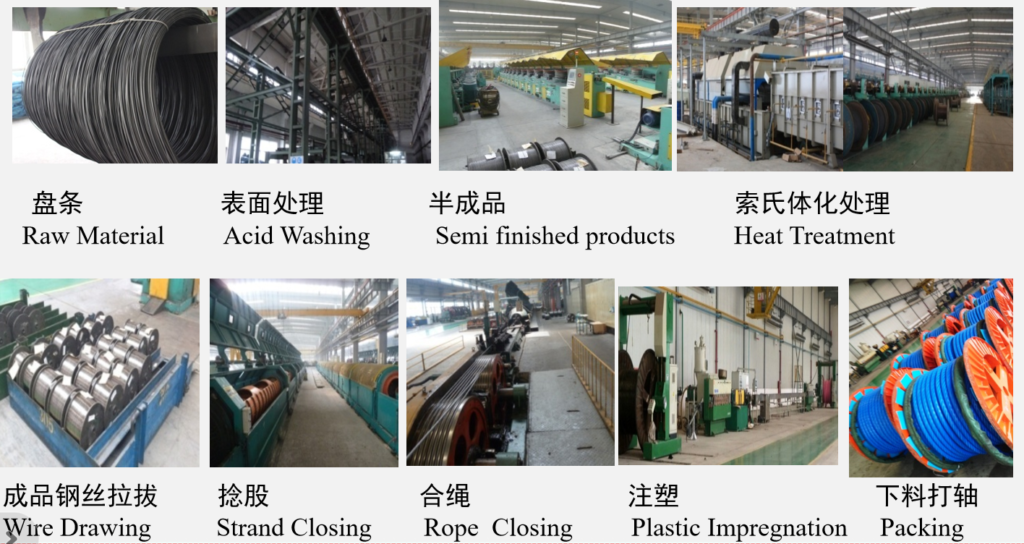
When I discuss shovel ropes, I think about the dynamic forces they experience. It’s not just lifting; it’s about digging into earth, dealing with sudden resistance, and continuous movement.
How do shovel ropes perform under pressure?
These ropes endure tremendous stress as they operate. Their performance is critical for continuous mining.
- Flexibility: Must bend around multiple sheaves and drums.
- Impact Resistance: Need to withstand sudden jerks and impacts.
- Abrasion: Constantly exposed to dirt and debris.
- High Breaking Load: Must handle the weight of the dipper and excavated material.
Our company, Aulone, focuses on ensuring these ropes can handle the extreme conditions. We ensure our ropes meet high standards like EN12385-4.
What features improve shovel rope lifespan?
Specific features in shovel rope design help them last longer in harsh environments.
- Plastic Impregnated Cores: Improve stability and prevent internal corrosion.
- Galvanized Wires: Offer superior corrosion protection.
- Special Lubricants: Reduce friction and protect against external elements.
- Compacted Strands: Increase metallic area, improving strength and resistance to crushing.
I always recommend these features to my clients, especially those with harsh operating conditions. Plastic impregnation, for example, really makes a difference in preventing premature rope failure from internal corrosion.
Conclusion
Understanding the unique demands of hoist, drag, and shovel ropes is crucial for safe and efficient mining. Choosing the right high-quality rope, like those we offer at Aulone, ensures operational longevity and safety.