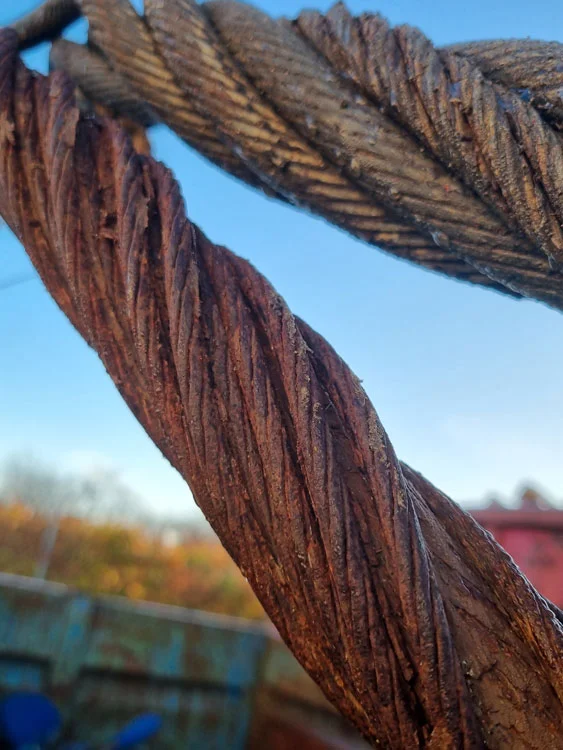
You fear rust on your wire ropes. It harms performance and safety. Galvanized wire rope sounds like a solution. But does it truly prevent rust?
Galvanized wire rope can rust, but its zinc coating significantly delays the corrosion process compared to uncoated steel, especially in mild conditions.
I’ve been in the wire rope industry for years. I know the challenges you face. I’ve seen countless projects where understanding material properties makes all the difference. Let me share what I’ve learned about galvanized wire rope.
How does galvanized wire rope resist rust?
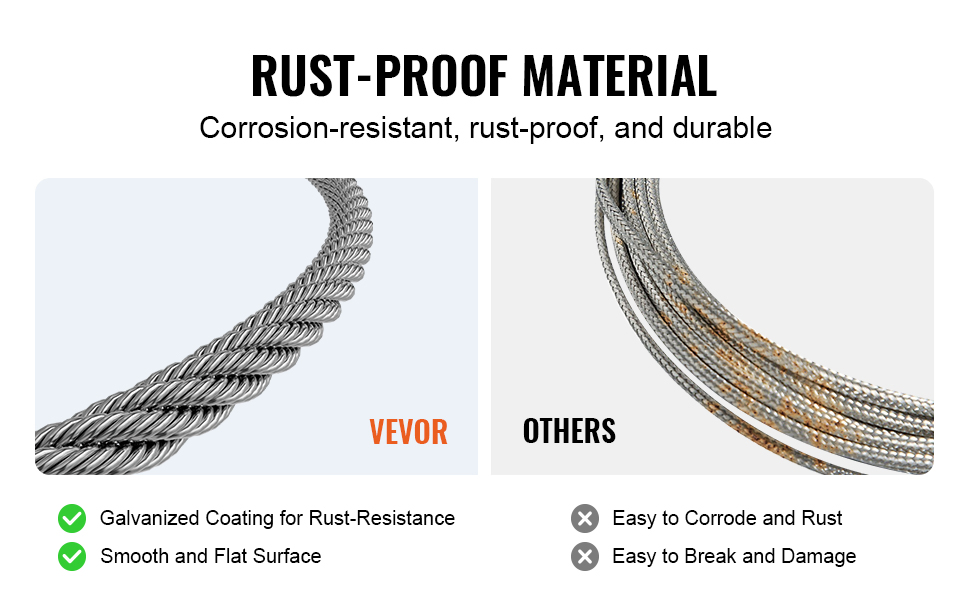
Galvanized wire rope resists rust using a protective zinc layer. This layer acts in two key ways. It creates a barrier. It also provides cathodic protection.
Galvanized wire rope resists rust primarily through a sacrificial zinc coating that serves as a protective barrier and offers cathodic protection, corroding before the underlying steel.
Let’s dive deeper into how this process works. I want you to understand the science behind it. This knowledge helps you make better choices for your projects.
Dive Deeper: The Science Behind Zinc Protection
The zinc coating on galvanized wire rope works hard. First, it forms a physical barrier. This barrier keeps moisture and oxygen away. Rust needs moisture and oxygen to form. Without them, rust cannot start.
Second, zinc protects the steel sacrificially. This means zinc corrodes first. It gives itself up to protect the steel. Zinc is more reactive than steel. So, in the presence of an electrolyte like water, zinc will oxidize instead of iron. This is called cathodic protection. Even if the zinc coating is scratched, it still protects the steel nearby.
Sometimes, you might see white spots on galvanized surfaces. This is white rust. White rust is zinc corrosion. It’s a sign the zinc is working. It’s protecting the steel underneath.
Consider this table for different galvanization types:
Type of Galvanization | Description | Thickness of Coating (microns) |
---|---|---|
Hot-dip Galvanizing | Immersion in molten zinc | 65-100+ |
Electro-galvanizing | Electro-deposition of zinc | 5-25 |
Zinc Plating (Mechanical) | Application of zinc powder and glass beads | 15-50 |
Hot-dip galvanizing gives a thick, durable coat. This means longer protection. Electro-galvanizing is thinner. It’s often used for cosmetic purposes.
The Factors Affecting Rust on Galvanized Wire Rope
Many things impact how long galvanized wire rope lasts. The first is the environment. Saltwater environments are very corrosive. High humidity areas also speed up corrosion. Pollution in the air can also cause rust. Acids and chemicals in the air can damage the zinc.
The thickness of the zinc coating matters. A thicker coating lasts longer. This is because there is more zinc to sacrifice. Quality of the galvanization also counts. A uniform, properly bonded coating performs best. Badly applied coatings can have weak spots. These spots might rust faster.
Usage conditions are also important. Constant friction and abrasion can wear away the zinc. This exposes the steel. Once the steel is bare, rust can begin. Proper maintenance can extend the life. Regular cleaning removes harmful substances. Applying appropriate lubricants can protect the coating. We make sure our products, like the ones from Aulone, meet high standards. We offer plastic impregnated ropes. This offers extra protection.
What are the benefits of galvanized wire rope?
Galvanized wire rope offers clear advantages. Its main benefit is rust resistance. This makes it suitable for many environments. It extends the product’s lifespan.
The main benefits of galvanized wire rope include enhanced corrosion resistance, extended service life, reduced maintenance needs, and a lower overall cost when considering longevity.
Let me explain why these benefits are so important for your operations. I work with clients globally. I understand the need for reliable, long-lasting products.
Dive Deeper: Real-World Advantages
The enhanced corrosion resistance means your ropes last longer. You replace them less often. This saves you money. Think about cranes or mining equipment. These machines work in tough conditions. A rope that resists rust performs better. It also makes operations safer. A strong rope is a safe rope.
For example, in marine environments, rust is a huge problem. Standard steel ropes corrode quickly. Galvanized marine wire rope significantly reduces this issue. It handles the saltwater exposure much better. This means less downtime for repairs. It means more productive time for your vessels or port operations.
I’ve seen purchasing managers from large corporations. They need reliable products. They often buy large quantities. They look for solutions that reduce long-term costs. Galvanized wire rope is exactly that. It’s an investment that pays off. It minimizes replacement frequency. It lowers labor costs for maintenance.
Here are some scenarios where galvanized wire rope shines:
Scenario | Benefit |
---|---|
Marine Industry | Resists saltwater corrosion, reduces replacement |
Construction | Handles outdoor exposure, maintains strength |
Mining | Withstands harsh environmental conditions |
General Lifting | Extends life in humid or outdoor settings |
We ensure our galvanized wire ropes meet strict standards. We comply with EN12385-4. We can provide BV & CE, RMRS, DNV, ABS certificates. This proves our commitment to quality. My factory has four production lines. We export to Singapore, Indonesia, Vietnam, Saudi Arabia, UAE, Russia, Australia, Canada, and other countries. The quality we provide helps my clients succeed.
When should you choose galvanized wire rope?
You should choose galvanized wire rope when rust is a concern. It is ideal for outdoor use. It is perfect for corrosive environments. Consider it for long-term projects.
You should choose galvanized wire rope when operating in environments prone to corrosion, such as outdoor, marine, or industrial settings, or when seeking extended service life and reduced maintenance.
This choice is critical for cost-effectiveness and safety. Based on my experience, selecting the right rope is key for any project.
Dive Deeper: Making the Right Choice for Your Project
Choosing galvanized wire rope is smart for several reasons. First, it’s about durability. If your rope will be exposed to rain, humidity, or fluctuating temperatures, galvanization is a must. Standard steel will rust quickly. This leads to weakened ropes and safety hazards.
Second, consider the return on investment. While a galvanized rope might have a slightly higher upfront cost, its extended lifespan means you save money in the long run. You won’t need to replace it as often. This cuts down on material costs. It also reduces labor costs for replacement. This is especially true for buyers of wire ropes and slings. They often manage large inventories.
For example, a mining company needs ropes that can withstand harsh underground conditions. Moisture, chemicals, and constant use are common. Standard ropes corrode quickly. Galvanized mining wire rope performs much better. This means less downtime for maintenance. It means more ore extracted.
Here are key decision points for choosing galvanized:
- Exposure to elements: Is the rope outdoors? Will it get wet?
- Corrosive agents: Is it near saltwater, chemicals, or pollution?
- Desired lifespan: Do you need it to last many years without frequent replacement?
- Maintenance budget: Do you want to minimize ongoing maintenance and inspection costs related to rust?
At Aulone, we offer high-tensile strength. Our ropes have high breaking loads. They are high quality. We can customize logos. We are focused on providing solutions that meet your specific needs. My goal is to make sure you get the best rope for your job every time.
Conclusion
Galvanized wire rope significantly delays rust. It does so with a zinc coating. This coating extends rope life. It also saves money. It is a smart choice for many tough environments.