Wire Rope Clips
Wire rope clips, also known as wire rope clamps or cable clamps, are essential fittings used to secure the ends of wire rope or cable when forming a loop or an eye. They provide a mechanical means of fastening that is both secure and adjustable. Here’s a detailed overview of wire rope clips:
Introduction: Wire rope clips are commonly used in various industries such as construction, marine, agriculture, and transportation. They are designed to create a reliable connection point or termination in wire rope assemblies, allowing for the formation of loops, splices, or ends that can be easily attached to hooks, rings, or other fittings.
Types of Wire Rope Clips:
Drop-Forged Wire Rope Clips: These are precision-engineered and often used in heavy-duty applications where maximum strength and reliability are required. They are forged from high-quality steel, providing superior durability and load-bearing capacity.
Malleable Wire Rope Clips: Made from malleable iron, these clips are more economical and suitable for general-purpose applications. They offer good strength and durability but are typically used in lighter load conditions compared to drop-forged clips.
Stainless Steel Wire Rope Clips: These clips are corrosion-resistant and suitable for applications where exposure to moisture, chemicals, or outdoor environments is common. They provide excellent durability and longevity, making them ideal for marine and offshore industries.
Components of Wire Rope Clips:
Saddle: The saddle is the curved part of the clip that holds the rope in place. It typically has a smooth surface to minimize wear on the rope.
U-Bolt: The U-bolt secures the wire rope by clamping it against the saddle. It passes through the holes in the saddle and is tightened using nuts to create a firm grip.
Nuts: Nuts are used to secure the U-bolt in place. They are tightened to the recommended torque specifications to ensure a secure and safe connection.
Installation and Usage:
Proper Alignment: Ensure that the U-bolt is correctly aligned with the saddle and that the wire rope lays neatly in the saddle before tightening.
Torque Requirements: Follow manufacturer recommendations for tightening torque to ensure the clip grips the rope securely without causing damage.
Number of Clips: Use the correct number of clips based on the diameter of the wire rope and the application. Generally, three clips are recommended for making an eye termination (two on the live end and one on the dead end).
Regular Inspection: Inspect wire rope clips periodically for signs of wear, corrosion, or loosening. Replace any clips that show signs of damage to maintain safety and reliability.
Applications:
Lifting and Rigging: Securing wire rope slings, lifting cables, and rigging assemblies.
Marine and Offshore: Mooring lines, anchor cables, and other marine applications where corrosion resistance is crucial.
Agriculture: Fencing, animal enclosures, and general farm use.
Construction: Hoisting and securing loads on construction sites.
Benefits:
Versatility: Suitable for various wire rope sizes and configurations.
Reliability: Provides a secure and adjustable termination point for wire rope assemblies.
Cost-Effective: Available in different materials and designs to suit different budgets and applications.
Wire rope clips are indispensable components in securing and terminating wire ropes, offering a practical and reliable solution for creating loops and attachments in various industrial and commercial settings.
US type drop forged wire rope clip
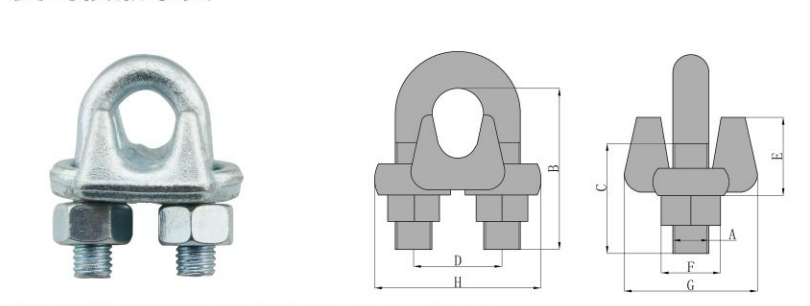
Feature:
Feature:
- Standard: US Standard
- Material Body: 45# Carbon Steel, U bolt- Q235 Carbon Steel
- Technology: Drop Forged
- Surface Finish: Self Color, Zinc Plated, Hot Dip Galvanized, Dacromet, Powder Coated
- Application: Fixed Wire Rope
Parameters
Size (in) | Diemensions (in) | Weight 100pcs (lbs) | |||||||
A | B | C | D | E | F | G | H | ||
1/8 | 0.22 | 0.72 | 0.44 | 0.47 | 0.37 | 0.38 | 0.81 | 0.99 | 6 |
3/16 | 0.25 | 0.97 | 0.56 | 0.59 | 0.50 | 0.44 | 0.94 | 1.18 | 10 |
1/4 | 0.31 | 1.03 | 0.50 | 0.75 | 0.66 | 0.56 | 1.19 | 1.43 | 19 |
5/16 | 0.38 | 1.38 | 0.75 | 0.88 | 0.73 | 0.69 | 1.31 | 1.66 | 28 |
3/8 | 0.44 | 1.50 | 0.75 | 1.00 | 0.91 | 0.75 | 1.63 | 1.94 | 48 |
7/16 | 0.50 | 1.88 | 1.00 | 1.19 | 1.13 | 0.88 | 1.91 | 2.28 | 78 |
1/2 | 0.50 | 1.88 | 1.00 | 1.19 | 1.13 | 0.88 | 1.91 | 2.28 | 80 |
9/16 | 0.56 | 2.25 | 1.25 | 1.31 | 1.34 | 0.94 | 2.06 | 2.50 | 109 |
5/8 | 0.56 | 2.25 | 1.25 | 1.31 | 1.34 | 0.94 | 2.06 | 2.50 | 110 |
3/4 | 0.62 | 2.75 | 1.44 | 1.5 | 1.39 | 1.06 | 2.25 | 2.84 | 142 |
7/8 | 0.75 | 3.12 | 1.62 | 1.75 | 1.58 | 1.25 | 2.44 | 3.16 | 212 |
1 | 0.75 | 3.50 | 1.81 | 1.88 | 1.77 | 1.25 | 2.63 | 3.47 | 252 |
1 1/8 | 0.75 | 3.88 | 2.00 | 2.00 | 1.91 | 1.25 | 2.81 | 3.59 | 283 |
1 1/4 | 0.88 | 4.44 | 2.22 | 2.34 | 2.17 | 1.44 | 3.13 | 4.13 | 438 |
1 3/8 | 0.88 | 4.44 | 2.22 | 2.34 | 2.31 | 1.44 | 3.13 | 4.19 | 442 |
1 1/2 | 0.88 | 4.94 | 2.38 | 2.59 | 2.44 | 1.44 | 3.41 | 4.44 | 544 |
1 5/8 | 1.00 | 5.31 | 2.62 | 2.75 | 2.66 | 1.63 | 3.63 | 4.75 | 704 |
1 3/4 | 1.13 | 5.75 | 2.75 | 3.06 | 2.92 | 1.81 | 3.81 | 5.24 | 934 |
2 | 1.25 | 6.44 | 3.00 | 3.38 | 3.03 | 2.00 | 4.44 | 5.88 | 1300 |
2 1/4 | 1.25 | 7.13 | 3.19 | 3.88 | 3.19 | 2.00 | 4.56 | 6.38 | 1600 |
2 1/2 | 1.25 | 7.69 | 3.44 | 4.13 | 3.69 | 2.00 | 4.69 | 6.63 | 1900 |
2 3/4 | 1.25 | 8.31 | 3.56 | 4.38 | 4.88 | 2.00 | 5.00 | 6.88 | 2300 |
3 | 1.50 | 9.19 | 3.88 | 4.75 | 4.44 | 2.38 | 5.31 | 7.61 | 3100 |
3 1/2 | 1.50 | 10.75 | 4.50 | 5.50 | 6.00 | 2.38 | 6.19 | 8.38 | 4000 |
US type malleable wire rope clip
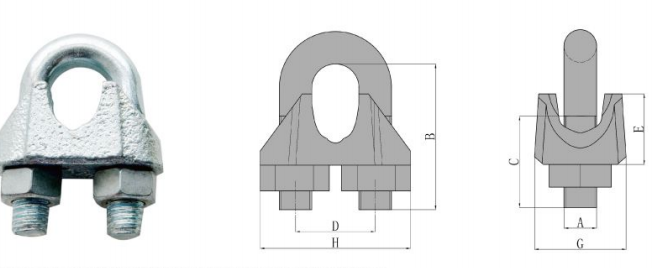
Feature:
- Product: US Type Galv Malleable Wire Rope Clips
- Place of origin: Shandong,China
- Brand Name: Sail Rigging
- Model Number: US Type
- Material: Malleable Iron
- Surface: Spraying Paint , Spraying Plastics, Galvanized
- Technology: Casting
- Size: From 1/8″ to 1 1/2″
- Packing: Gunny Bag + Pallet
- Certification: ISO, SGS,CE
- Using for: Fixing Wire Rope
Parameters
Size (in) | Diemensions (in) | Weight 100 pcs (lbs) | ||||||
A | B | C | D | E | G | H | ||
1/8 | 1/4 | 13/16 | 1/2 | 1/2 | 7/16 | 1/2 | 15/16 | 4.30 |
3/16 | 1/4 | 31/32 | 5/8 | 9/16 | 1/2 | 9/16 | 1 1/16 | 6.80 |
1/4 | 5/16 | 1 7/32 | 7/8 | 11/16 | 5/8 | 11/16 | 1 3/8 | 14.50 |
5/16 | 5/16 | 1 7/32 | 7/8 | 11/16 | 11/16 | 11/16 | 1 3/8 | 15.00 |
3/8 | 3/8 | 1 5/8 | 1 | 7/8 | 13/16 | 7/8 | 1 5/8 | 21.50 |
7/16 | 3/8 | 1 5/8 | 1 | 7/8 | 13/16 | 15/16 | 1 5/8 | 24.00 |
1/2 | 7/16 | 2 | 1 1/4 | 1 | 1 1/16 | 1 | 1 7/8 | 37.00 |
9/16 | 1/2 | 2 5/16 | 1 15/32 | 1 3/16 | 1 3/16 | 1 1/8 | 2 3/16 | 55.00 |
5/8 | 1/2 | 2 5/16 | 1 15/32 | 1 3/16 | 1 5/16 | 1 1/8 | 2 3/16 | 59.00 |
3/4 | 9/16 | 2 9/16 | 1 3/4 | 1 11/32 | 1 1/2 | 1 1/4 | 2 7/16 | 84.00 |
7/8 | 5/8 | 3 1/16 | 1 13/16 | 1 5/8 | 1 3/4 | 1 3/4 | 2 7/8 | 128.00 |
1 | 5/8 | 3 3/8 | 2 1/16 | 1 3/4 | 1 15/16 | 2 | 3 | 150.00 |
1 1/8 | 3/4 | 3 7/8 | 2 3/16 | 2 1/16 | 2 3/16 | 2 1/8 | 3 7/16 | 243.00 |
1 1/4 | 3/4 | 3 7/8 | 2 3/16 | 2 1/16 | 2 3/8 | 2 1/2 | 3 7/16 | 262.00 |
1 3/8 | 7/8 | 4 1/2 | 2 | 2 9/16 | 2 7/8 | 3 1/8 | 4 3/16 | 456.00 |
1 1/2 | 7/8 | 4 1/2 | 2 | 2 9/16 | 3 | 3 1/4 | 4 1/4 | 512.00 |
DIN741 malleable wire rope clip
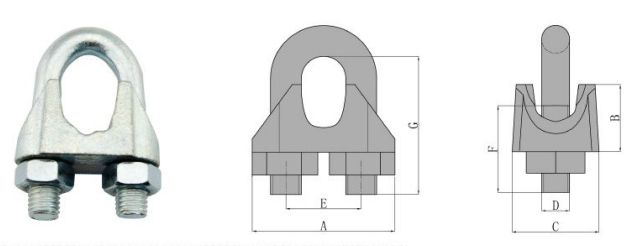
Feature:
- Standard: DIN Standard
- Material Body: Body-Malleable Steel, U bolt- Q235 Carbon Steel
- Technology: Casting
- Surface Finish: Zinc Plated
- Application: Fixed Wire Rope
Parameters
Size (mm) | Diemensions (mm) | Weight 100pcs (kg) | ||||||
A | B | C | D | E | F | G | ||
3 | 21 | 10 | 10 | 4 | 9 | 12 | 16.6 | 1.4 |
5 | 23 | 10 | 11 | 5 | 11 | 13 | 19.65 | 1.5 |
6.5 | 26 | 11 | 12 | 5 | 13 | 15 | 23.65 | 2.1 |
8 | 30 | 15 | 14 | 6 | 16 | 19 | 28.85 | 4.1 |
10 | 34 | 17 | 18 | 8 | 19 | 22 | 35 | 6.8 |
11 | 36 | 18 | 19 | 8 | 20 | 22 | 37 | 7.2 |
13 | 40 | 21 | 23 | 10 | 24 | 30 | 46.24 | 13 |
14 | 44 | 22 | 23 | 10 | 25 | 30 | 48.24 | 13.5 |
16 | 50 | 26 | 26 | 12 | 29 | 33 | 52.5 | 21 |
19 | 54 | 30 | 29 | 12 | 32 | 38 | 64.5 | 28 |
22 | 61 | 34 | 33 | 14 | 37 | 44 | 72.5 | 40 |
26 | 65 | 37 | 35 | 14 | 41 | 45 | 82.5 | 44 |
30 | 74 | 43 | 37 | 16 | 48 | 50 | 95.6 | 66 |
34 | 80 | 50 | 42 | 16 | 52 | 55 | 105.6 | 85 |
40 | 88 | 55 | 45 | 16 | 58 | 60 | 125.6 | 104 |
DIN741 malleable wire rope clip
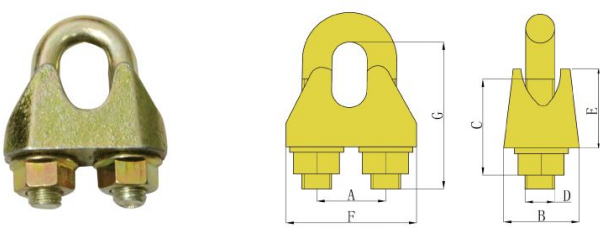
Feature:
- Product: Din1142 Wire Rope Clip
- Place of origin: Shandong,China
- Brand Name: Sail Rigging
- Model Number: DIN1142
- Material: Body-Malleable Steel, U Bolt- Q235 Carbon Steel
- Surface: Spraying Paint , Spraying Plastics, Galvanized
- Technology: Casting
- Size: From 5mm to 40 mm
- Packing: Gunny Bag + Pallet
- Certification: ISO, SGS,CE
- Using for: Fixing Wire Rope
Parameters
Size (mm) | Dimensions(mm) | Weight 100pcs (kg) | ||||||
A | B | C | D | E | F | G | ||
5 | 12 | 13 | 14 | 5 | 13 | 25 | 20 | 2 |
6.5 | 14 | 16 | 17 | 6 | 14 | 30 | 26 | 4 |
8 | 18 | 20 | 20 | 8 | 18 | 39 | 33 | 8.2 |
10 | 20 | 20 | 24 | 8 | 21 | 40 | 38 | 9.2 |
13 | 24 | 28 | 29 | 12 | 29 | 55 | 52 | 27.5 |
16 | 34 | 32 | 35 | 14 | 35 | 64 | 62 | 43 |
19 | 37 | 33 | 36 | 14 | 40 | 68 | 69 | 49 |
22 | 41 | 34 | 40 | 16 | 44 | 74 | 80 | 68 |
26 | 46 | 38 | 50 | 20 | 51 | 84 | 91 | 117 |
30 | 54 | 41 | 55 | 20 | 59 | 95 | 107 | 140 |
34 | 60 | 45 | 60 | 22 | 67 | 105 | 119 | 213 |
40 | 68 | 49 | 65 | 24 | 77 | 117 | 135 | 268 |
Italian type wire rope clip
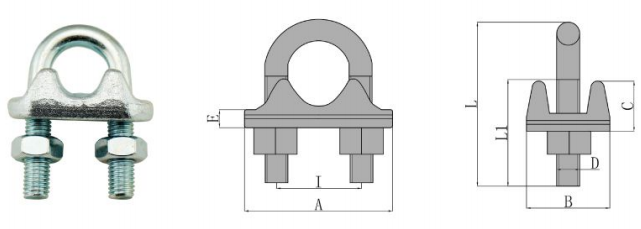
Feature:
- Product: Italian Type Wire Rope Clips
- Place of origin: Shandong,China
- Brand Name: Sail Rigging
- Model Number: Italian Type
- Material: Q235 Carbon Steel
- Surface: Spraying Paint , Spraying Plastics, Galvanized
- Technology: Casting
- Size: From 3-4 to 45
- Packing: Gunny Bag + Pallet
- Certification: ISO, SGS,CE
- Using for: Fixing Wire Rope
Parameters
Size (mm) | Dimensions(mm) | Weight (kg) | |||||||
A | B | C | D | E | I | L | L1 | ||
3-4 | 21.00 | 14.00 | 9.00 | 4.00 | 4.50 | 9.00 | 20.00 | 11.00 | 0.01 |
5 | 25.00 | 17.00 | 10.00 | 5.00 | 4.50 | 11.00 | 24.00 | 12.00 | 0.02 |
6 | 30.00 | 19.00 | 11.00 | 6.00 | 5.00 | 14.00 | 33.00 | 18.00 | 0.03 |
8 | 34.00 | 20.00 | 12.00 | 6.00 | 5.00 | 16.00 | 35.00 | 18.00 | 0.04 |
10 | 38.00 | 22.00 | 14.00 | 8.00 | 6.00 | 18.50 | 44.00 | 22.00 | 0.07 |
11 | 41.00 | 24.00 | 14.30 | 8.00 | 7.00 | 22.00 | 44.00 | 22.00 | 0.08 |
12 | 45.00 | 25.00 | 16.00 | 10.00 | 7.00 | 24.00 | 55.00 | 33.00 | 0.12 |
14 | 46.00 | 27.00 | 17.00 | 10.00 | 7.50 | 24.00 | 55.00 | 33.00 | 0.14 |
16 | 53.00 | 31.00 | 18.00 | 10.00 | 8.00 | 30.00 | 65.00 | 33.00 | 0.18 |
18 | 59.00 | 33.00 | 20.00 | 12.00 | 8.00 | 30.00 | 78.00 | 38.00 | 0.26 |
20 | 60.00 | 34.00 | 22.00 | 12.00 | 8.00 | 34.00 | 78.00 | 38.00 | 0.29 |
22 | 66.00 | 35.00 | 23.00 | 12.00 | 8.00 | 36.00 | 81.00 | 45.00 | 0.30 |
24-25 | 70.00 | 40.00 | 24.00 | 12.00 | 9.00 | 39.00 | 86.00 | 45.00 | 0.38 |
26 | 72.00 | 40.00 | 26.50 | 14.00 | 12.00 | 42.00 | 95.00 | 50.00 | – |
28 | 80.00 | 43.00 | 30.00 | 14.00 | 12.00 | 43.00 | 110.00 | 55.00 | 0.56 |
30 | 80.00 | 44.00 | 33.00 | 14.00 | 10.00 | 47.00 | 110.00 | 50.00 | 0.706 |
32 | 92.00 | 45.00 | 34.00 | 16.00 | 14.00 | 49.00 | 115.00 | 60.00 | 0.91 |
34 | 90.00 | 48.00 | 37.00 | 16.00 | 11.00 | 53.00 | 120.00 | 55.00 | – |
38 | 95.00 | 51.00 | 39.00 | 16.00 | 16.00 | 57.00 | 130.00 | 63.00 | 1.03 |
40 | 100.00 | 55.00 | 40.00 | 16.00 | 14.00 | 59.00 | 140.00 | 60.00 | – |
45 | 116.00 | 60.00 | 47.00 | 16.00 | 17.00 | 70.00 | 158.00 | 83.00 | 1.45 |
Commercial heavy duty wire rope clip
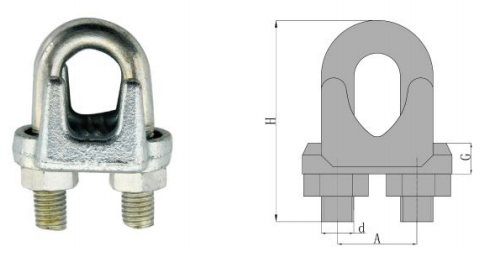
Feature:
- Product: Commercial Type Wire Rope Clips
- Place of origin: Shandong,China
- Brand Name: Sail Rigging
- Standard:Chinese Type
- Material: Body- Malleable Steel, U Bolt- Q235 Carbon Steel
- Surface: Spraying Paint , Spraying Plastics, Galvanized
- Technology: Casting
- Size: From 6 to 32
- Packing: Gunny Bag + Pallet
- Certification: ISO, SGS,CE
- Using for: Fixing Wire Rope
Parameters
Size(mm) | Dimensions(mm) | Weight (kg) | ||
d | A | H | ||
6 | m6 | 13 | 31 | 0.038 |
8 | m8 | 17 | 41 | 0.075 |
10 | m10 | 21 | 51 | 0.130 |
12 | m12 | 25 | 62 | 0.200 |
15 | m15 | 29 | 70 | 0.320 |
18 | m16 | 35 | 87 | 0.420 |
20 | m16 | 37 | 92 | 0.490 |
22 | m20 | 43 | 108 | 0.720 |
25 | m25 | 46 | 113 | 0.980 |
28 | m22 | 51.5 | 127 | 1.460 |
32 | m22 | 55.5 | 136 | 1.650 |
Malleable wire rope clip type A
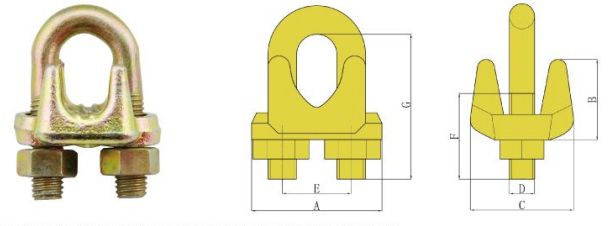
Feature:
- Product: Malleable Wire Rope Clips Type A
- Place of origin: Shandong,China
- Brand Name: Sail Rigging
- Model Number: A Type
- Material: Body -Malleable Steel, U Bolt- Q235 Carbon Steel
- Surface: Spraying Paint , Spraying Plastics, Galvanized
- Technology: Casting
- Size: From 6mm to 50 mm
- Packing: Gunny bag + Pallet
- Certification: ISO, SGS,CE
- Using for: Lifting with wire rope
Parameters
Size (mm) | Dimensions(mm) | Weight (kg) | ||||||
A | B | C | D | E | F | G | ||
6 | 23 | 14 | 17 | 5 | 12 | 14 | 24 | 0.023 |
8 | 28 | 17 | 21 | 6 | 15 | 16 | 30 | 0.038 |
10 | 38 | 21 | 28 | 8 | 19 | 20 | 37 | 0.085 |
12 | 45 | 27 | 34 | 10 | 24 | 25 | 47 | 0.165 |
15 | 52 | 32 | 40 | 12 | 29 | 30 | 56 | 0.26 |
20 | 62 | 38 | 47 | 14 | 36 | 36 | 70 | 0.44 |
22 | 69 | 43 | 52 | 16 | 40 | 39 | 77 | 0.6 |
25 | 76 | 50 | 56 | 18 | 43 | 44 | 85 | 0.85 |
28 | 85 | 57 | 62 | 20 | 48 | 48 | 95 | 1.12 |
32 | 93 | 61 | 67 | 22 | 55 | 51 | 108 | 1.52 |
40 | 111 | 73 | 81 | 24 | 64 | 62 | 120 | 2.4 |
45 | 123 | 86 | 88 | 27 | 72 | 70 | 137 | 3.5 |
50 | 135 | 95 | 95 | 30 | 80 | 88 | 154 | 4.7 |
US type fist grip clip
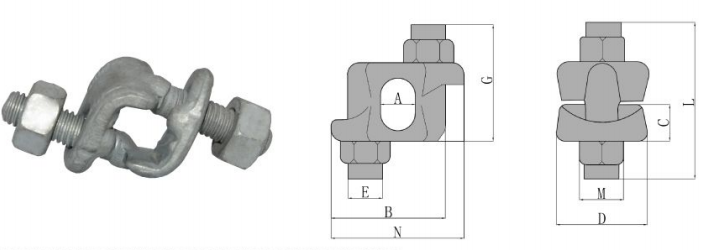
Feature:
- Product: US Type Fist Grip Clips
- Place of origin: Shandong,China
- Brand Name: Sail Rigging
- Model Number: US Type
- Material: 45#
- Surface: Spraying Paint , Spraying Plastics, Galvanized, Hot Dip Galvanized
- Technology: Forging
- Size: From 3/16″ to 1 1/2″
- Packing: Gunny bag + Pallet
- Certification: ISO, SGS,CE
- Using for: Connecting Wire Rope
Parameters
Size (in) | Dimensions(in) | Weight 100pcs (lbs) | ||||||||
A | B | C | D | E | G | Approx L | M | N | ||
3/16-1/4 | 0.25 | 1.25 | 0.34 | 0.94 | 0.38 | 1.28 | 1.36 | 0.69 | 1.47 | 18 |
5/16 | 0.31 | 1.34 | 0.44 | 1.06 | 0.38 | 1.47 | 1.94 | 0.69 | 1.56 | 28 |
3/8 | 0.38 | 1.59 | 0.50 | 1.06 | 0.44 | 1.81 | 2.38 | 0.75 | 1.88 | 40 |
7/16-1/2 | 0.50 | 1.88 | 0.56 | 1.25 | 0.50 | 2.19 | 2.75 | 0.88 | 2.19 | 70 |
9/16-5/8 | 0.63 | 2.28 | 0.69 | 1.50 | 0.63 | 2.69 | 3.50 | 1.06 | 2.63 | 100 |
3/4 | 0.75 | 2.69 | 0.88 | 1.81 | 0.75 | 2.94 | 3.75 | 1.25 | 3.06 | 175 |
7/8 | 0.88 | 2.97 | 0.97 | 2.13 | 0.75 | 3.31 | 4.13 | 1.25 | 3.14 | 225 |
1 | 1.00 | 3.06 | 1.19 | 2.25 | 0.75 | 3.72 | 4.63 | 1.25 | 3.53 | 300 |
1-1/8 | 1.13 | 3.44 | 1.28 | 2.38 | 0.88 | 4.19 | 5.25 | 1.44 | 3.91 | 400 |
1-1/4 | 1.25 | 3.56 | 1.34 | 2.50 | 0.88 | 4.25 | 5.25 | 1.44 | 4.03 | 400 |
1-3/8-1-1/2 | 1.50 | 4.13 | 1.56 | 3.00 | 1.00 | 5.56 | 7.00 | 1.63 | 4.66 | 700 |
Your Ultimate Guide to Acquiring Wire Rope Clips
When it comes to securing wire ropes in construction, rigging, and industrial applications, wire rope clips are essential. Selecting the right type of wire rope clip for your needs is crucial to ensure safety and effectiveness. This guide will walk you through everything you need to know about acquiring wire rope clips.
Table of contents
Chapt 1
What Are Wire Rope Clips
Wire rope clips, also known as wire rope clamps, are mechanical devices used to secure the loose end of a wire rope back to the standing part of the rope, forming a loop or thimble. This loop can then be attached to various hardware, such as hooks, shackles, or other components, providing a secure connection point.
Key Components of Wire Rope Clips
U-Bolt: The U-shaped bolt that forms the primary structure of the clip. The wire rope is placed inside the curve of this U-bolt.
Saddle: The saddle is the part of the clip that sits on the wire rope when the nuts on the U-bolt are tightened. It helps to clamp the wire rope securely.
Nuts: These are threaded onto the U-bolt, securing the saddle in place and providing the necessary pressure to hold the rope firmly.
Types of Wire Rope Clips
Drop Forged Clips: Made from drop-forged steel, these clips are extremely strong and durable, suitable for heavy-duty applications. They are commonly used in industries where the wire rope is under significant stress.
Malleable Iron Clips: These clips are made from malleable iron, which is less strong than drop-forged steel but more flexible. They are typically used in lighter-duty applications where the load is not as extreme.
Fist Grip Clips: Featuring a design where the saddle has two nuts on each side of the U-bolt, fist grip clips offer a more secure hold, making them suitable for high-tension applications.
Uses of Wire Rope Clips
Wire rope clips are widely used in various industries for several purposes:
Creating Loops: The primary use of a wire rope clip is to form a loop at the end of a wire rope, which can then be attached to a hook, shackle, or another device.
Splicing: In some cases, wire rope clips are used to create a splice, connecting two lengths of wire rope together.
Securing Loads: Wire rope clips are also used to secure loads by clamping the rope around an object, ensuring that it doesn’t slip or move.
Common Applications
Wire rope clips are essential in:
- Construction: Securing scaffolding, lifting materials, and other structural applications.
- Marine: Securing ropes in docks, ships, and other maritime environments.
- Industrial Rigging: Creating secure connections for hoisting and pulling operations.
- Theatrical Rigging: Securing lighting and set pieces in theaters.
Conclusion
Wire rope clips are simple yet critical components that play a vital role in securing wire ropes in a variety of applications. By understanding their types, uses, and installation requirements, you can ensure that your wire rope systems are both safe and effective.
Chapt 2
What are the differences between different types of wire rope clips?
Wire rope clips come in various types, each designed to meet specific requirements depending on the application, load capacity, and environmental conditions. The key differences between these types of wire rope clips are mainly in their material, manufacturing process, strength, and intended use. Here’s a breakdown of the primary differences:
1. Drop Forged Wire Rope Clips
Material and Manufacturing:
- Made from drop-forged steel, which involves hammering a heated metal blank into the desired shape. This process increases the material’s density and strength.
Strength and Durability:
- Extremely strong and durable, making them suitable for heavy-duty applications where high load capacity is critical.
Applications:
- Commonly used in critical applications such as lifting, rigging, and heavy industrial operations. They are often used where safety is paramount, such as in construction, shipping, and mining.
Cost:
- Generally more expensive than other types of clips due to their strength and the cost of the forging process.
2. Malleable Wire Rope Clips
Material and Manufacturing:
- Made from malleable iron, which is a type of cast iron that has been treated to make it more flexible and less brittle.
Strength and Durability:
- Less strong than drop-forged clips, but they offer more flexibility. They are typically used in lighter-duty applications.
Applications:
- Suitable for non-critical applications where the load is lighter, such as in agricultural settings, fencing, and general-purpose rigging.
Cost:
- More cost-effective than drop-forged clips, making them a good choice for budget-conscious projects where high strength is not required.
3. Fist Grip Clips
Material and Manufacturing:
- Typically made from drop-forged steel, similar to traditional drop-forged clips, but with a different design.
Strength and Durability:
- Designed with a saddle that has nuts on both sides of the U-bolt, which provides a more even distribution of clamping force and greater security.
Applications:
- Used in high-tension applications where a very secure hold is needed. Common in situations where the wire rope is subjected to dynamic loads or where slippage must be avoided at all costs.
Cost:
- Generally more expensive than traditional drop-forged clips due to their specialized design and enhanced security features.
4. DIN741 Wire Rope Clips
Material and Manufacturing:
- Made according to the DIN 741 standard, typically using malleable iron or steel. The design is standardized, particularly in European applications.
Strength and Durability:
- The strength and durability can vary depending on whether they are made from malleable iron or steel, with steel variants being stronger.
Applications:
- Commonly used in Europe for a variety of applications, including general rigging, securing loads, and forming wire rope loops. The standardization makes them a reliable choice in applications where adherence to specific regulations is required.
Cost:
- Typically mid-range in cost, depending on the material used.
5. Commercial Heavy Duty Wire Rope Clips
Material and Manufacturing:
- Made from durable materials like steel, but not necessarily drop-forged. They are designed for higher load capacities than standard malleable clips.
Strength and Durability:
- Stronger than malleable iron clips but may not match the strength of drop-forged clips.
Applications:
- Used in commercial applications where higher loads are involved but where extreme heavy-duty performance is not needed, such as in large-scale construction projects or industrial settings.
Cost:
- Priced between malleable iron clips and drop-forged clips, offering a balance between strength and cost.
6. Italian Type Wire Rope Clips
Material and Manufacturing:
- Typically made from malleable iron or steel, with a design specific to Italian manufacturing standards.
Strength and Durability:
- The design may offer different strength characteristics compared to DIN or US types, but this depends on the specific use case and material.
Applications:
- Used in applications where regional standards or design preferences dictate the use of this particular type. Common in various industrial and marine applications.
Cost:
- Cost varies depending on material and market availability.
Summary
- Drop Forged Clips: Best for heavy-duty applications requiring maximum strength.
- Malleable Clips: Suitable for lighter loads, more flexible, and cost-effective.
- Fist Grip Clips: Offer extra security for high-tension or dynamic load applications.
- DIN741 Clips: Standardized in Europe, used in a variety of applications, with material strength varying.
- Commercial Heavy Duty Clips: A middle-ground option for higher loads but not as strong as drop-forged clips.
- Italian Type Clips: Region-specific, with varying strength depending on material and design.
Choosing the right type of wire rope clip depends on the specific needs of your project, including the required load capacity, application environment, and budget.
Chapt 3
How to choose the right size of a wire rope clip?
Choosing the right size of a wire rope clip is crucial to ensuring the safety and effectiveness of your wire rope assembly. The size of the wire rope clip must match the diameter of the wire rope you are using. Here’s a step-by-step guide on how to select the correct size:
1. Determine the Diameter of the Wire Rope
The first and most important step is to know the exact diameter of the wire rope you are working with. This is usually measured in millimeters (mm) or inches.
- Measurement Tools: Use a caliper or a micrometer to accurately measure the diameter of the wire rope. Make sure to measure the rope at its widest point.
2. Match the Clip Size to the Rope Diameter
Wire rope clips are sized to correspond directly to the diameter of the wire rope. The size of the clip is typically listed in the product description, and it should be the same as the diameter of your wire rope.
- Example: If you have a wire rope with a diameter of 10mm (3/8 inch), you should use a 10mm (3/8 inch) wire rope clip.
3. Consider the Manufacturer’s Recommendations
Each manufacturer may provide specific guidelines on the appropriate clip size for different wire rope diameters. It is always best to follow these recommendations to ensure the clip performs as expected.
4. Check the Number of Clips Required
The number of clips required for a secure connection depends on the diameter of the wire rope. Larger diameters typically require more clips. Manufacturers often provide tables that specify the recommended number of clips for different wire rope sizes.
- Example: For a 3/8 inch wire rope, you might need three clips to ensure a secure connection, while a 1/2 inch rope might require four clips.
5. Ensure Proper Spacing Between Clips
The spacing between wire rope clips is also important for ensuring a secure grip. The general rule is to space the clips at a distance equal to six times the diameter of the wire rope.
- Example: For a 1/2 inch rope, space the clips 3 inches apart.
6. Consider Load Requirements
If your application involves high loads or safety-critical situations, ensure that both the wire rope and the clip are rated to handle the load. In such cases, opting for a higher quality, such as drop-forged wire rope clips, might be necessary.
7. Consult Standards and Regulations
In some industries, there may be specific standards or regulations that dictate the size and type of wire rope clips you should use. Be sure to consult any relevant guidelines, such as OSHA standards, particularly for lifting and rigging operations.
8. Regular Inspection and Maintenance
Once installed, regularly inspect the clips to ensure they are still secure and properly sized. Clips that are too large or too small can fail under load, leading to potential safety hazards.
Conclusion
To choose the right size of a wire rope clip:
- Accurately measure the diameter of the wire rope.
- Select a clip that matches this diameter.
- Follow the manufacturer’s guidelines for clip size and the number of clips required.
- Ensure proper spacing and installation according to industry standards.
By carefully selecting the correct size of wire rope clips, you can ensure a safe and secure connection in your wire rope assemblies.
Chapt 4
What is the correct way to install a wire rope clip?
Installing a wire rope clip correctly is crucial to ensure a secure and reliable connection in your wire rope assembly. Improper installation can lead to slippage or failure, which can be dangerous, especially in lifting or load-bearing applications. Here’s a step-by-step guide to installing a wire rope clip correctly:
1. Gather Necessary Tools and Equipment
- Wire Rope Clips: Ensure you have the correct size and type for your wire rope.
- Wrench or Torque Wrench: A torque wrench is preferred to apply the correct amount of torque to the nuts.
- Wire Rope: The rope to which the clip will be attached.
- Thimble (Optional): Used to protect the eye of the wire rope from abrasion.
2. Prepare the Wire Rope
- Form a Loop: Take the end of the wire rope and loop it back onto the standing part of the rope. If using a thimble, place it inside the loop before proceeding.
3. Position the First Clip
- Saddle on the Live End: The most important rule in wire rope clip installation is to always place the saddle of the clip on the live end of the wire rope (the load-bearing part). The U-bolt should be on the dead end (the shorter end that is not under load).
- Mnemonic: “Never saddle a dead horse” helps remember this rule.
- Placement: Position the first clip as close to the thimble or the end of the loop as possible, but leave enough space to allow for the installation of additional clips.
4. Tighten the Nuts
- Initial Tightening: Using a wrench, tighten the nuts evenly on both sides of the U-bolt until the wire rope is snugly held by the clip.
- Torque Wrench (if available): If you have a torque wrench, tighten the nuts to the recommended torque specified by the manufacturer. This is crucial to ensure the clip holds securely without damaging the rope.
5. Position and Install Additional Clips
- Spacing: Install additional wire rope clips along the rope, spacing them evenly. The standard recommendation is to space them about 6 rope diameters apart.
- Example: For a 1/2 inch wire rope, space the clips about 3 inches apart.
- Number of Clips: The number of clips required depends on the diameter of the rope. For example, a 1/2 inch rope typically requires three clips, while a 1-inch rope may need five.
- Install Each Clip: For each additional clip, follow the same procedure: saddle on the live end, tighten the nuts evenly, and ensure proper spacing.
6. Final Tightening
- Retighten All Clips: After all clips are in place, go back and retighten all the nuts. This helps to compensate for any settling that may have occurred during the initial tightening.
- Check Torque: If using a torque wrench, check that all nuts are tightened to the correct torque.
7. Inspection
- Check Installation: Inspect the installation to ensure that all clips are properly spaced, oriented correctly (saddle on live end), and securely tightened.
- Test the Assembly: If possible, test the assembly under load to ensure that the wire rope is secure and that there is no slippage.
8. Regular Maintenance
- Periodic Retightening: Over time, the nuts on the clips may loosen slightly due to the tension and load. Regularly check and retighten the nuts as necessary.
- Inspect for Wear: Periodically inspect the wire rope and clips for signs of wear, corrosion, or deformation.
Summary
- Form a loop in the wire rope and place a thimble inside the loop (if used).
- Place the first wire rope clip with the saddle on the live end and the U-bolt on the dead end.
- Tighten the nuts evenly, ensuring the clip is secure.
- Install additional clips evenly spaced along the rope, ensuring proper orientation.
- Retighten all clips and check that they are secure.
- Regularly inspect and maintain the clips to ensure ongoing safety.
By following these steps, you can ensure that your wire rope clips are installed correctly, providing a secure and reliable connection for your wire rope assembly.
Chapt 5
How often should wire rope clips be inspected for safety?
The frequency of wire rope clip inspections is crucial to maintaining safety and ensuring the longevity of your wire rope assembly. The exact frequency can depend on the specific application, the environment in which the clips are used, and the load they are bearing. However, here are general guidelines for inspecting wire rope clips:
1. Initial Inspection
- Post-Installation Inspection: After the initial installation, it’s important to inspect the wire rope clips to ensure they are properly installed, the nuts are tightened to the correct torque, and the assembly is secure.
- First Re-Tightening: It is recommended to check and retighten the nuts after the first few uses. This helps to account for any settling or slight loosening that may occur once the wire rope comes under load.
2. Regular Inspection Intervals
General Use: For general use in non-critical applications, wire rope clips should be inspected at least every 3 to 6 months. This includes checking for proper torque on the nuts, signs of wear, corrosion, and any deformation of the clip or wire rope.
Heavy-Duty Applications: In heavy-duty or safety-critical applications, such as lifting or load-bearing operations, inspections should be more frequent, typically every 1 to 3 months. This ensures that any potential issues are identified and addressed before they can lead to failure.
High-Risk Environments: In harsh environments (e.g., marine, chemical exposure, extreme weather), inspections should occur monthly or even weekly, depending on the severity of the conditions. These environments can accelerate corrosion and wear, making more frequent inspections necessary.
3. Before and After Critical Operations
- Pre-Operation Inspection: Always inspect the wire rope clips before any critical operation, such as lifting a heavy load, to ensure that everything is in proper condition.
- Post-Operation Inspection: After completing a critical operation, inspect the clips to check for any signs of damage or loosening caused by the load.
4. After Significant Events
After Heavy Loads or Shock Loads: If the wire rope assembly has been subjected to an unusually heavy load or a shock load, inspect the wire rope clips immediately afterward. These events can cause unexpected stress on the clips, potentially leading to slippage or damage.
After Environmental Exposure: If the wire rope clips have been exposed to harsh environmental conditions, such as saltwater immersion, chemical spills, or extreme temperatures, inspect them immediately after exposure to assess any damage or corrosion.
5. Annual Comprehensive Inspection
- Detailed Annual Inspection: At least once a year, conduct a thorough inspection of all wire rope clips as part of a broader inspection of your wire rope assemblies. This should include disassembly (if feasible) to closely examine each component for wear, corrosion, cracks, or any other signs of degradation.
6. Documentation
- Record Inspections: Keep a log of all inspections, including the date, findings, and any maintenance or adjustments made. This record helps track the condition of the wire rope clips over time and ensures that inspections are not missed.
Summary
- Post-Installation: Inspect after initial installation and retighten after first few uses.
- Regular Intervals: Inspect every 3 to 6 months for general use, more frequently (1 to 3 months) for heavy-duty or high-risk applications.
- Before/After Critical Operations: Inspect before and after critical tasks or after significant loads.
- After Significant Events: Immediate inspection after exposure to heavy loads or harsh conditions.
- Annual Inspection: Conduct a comprehensive inspection at least once a year.
- Document Inspections: Maintain records of all inspections for safety and maintenance tracking.
Following these guidelines will help ensure the ongoing safety and reliability of your wire rope assemblies and the wire rope clips used within them.
Chapt 6
Can wire rope clips be reused, or should they be replaced after each use?
Wire rope clips can sometimes be reused, but whether they should be reused or replaced after each use depends on several factors, including the application, the condition of the clips, and safety considerations. Here’s a detailed look at the factors that determine whether wire rope clips should be reused or replaced:
1. Application Type
Critical Applications (e.g., lifting, load-bearing, safety-related tasks): In safety-critical applications, such as lifting operations or where failure could result in injury or significant damage, it is generally recommended to replace wire rope clips after each use. This ensures maximum safety and reliability, as even slight wear or deformation can compromise the clip’s effectiveness.
Non-Critical Applications (e.g., temporary structures, non-load-bearing connections): For less critical applications where the wire rope clip is not subjected to heavy loads or where failure would not result in serious consequences, reuse may be acceptable, provided the clip is still in good condition.
2. Condition of the Wire Rope Clips
Inspection: Before reusing a wire rope clip, it must be thoroughly inspected for any signs of wear, deformation, corrosion, or damage. Key areas to check include:
- The threads on the U-bolt and nuts, ensuring they are not stripped or damaged.
- The saddle, ensuring it has not deformed or developed cracks.
- The overall integrity of the clip, including the U-bolt, nuts, and saddle.
Signs of Wear or Damage: If any wear, deformation, or damage is detected, the clip should be replaced immediately. Even minor damage can lead to failure under load.
3. Environmental Considerations
Harsh Environments (e.g., marine, corrosive, extreme temperatures): In environments that are harsh or corrosive, wire rope clips are more likely to suffer from corrosion or degradation, which can weaken them. In such cases, it is safer to replace clips after use, especially if they have been exposed to saltwater, chemicals, or extreme temperatures.
Mild Environments: In less harsh environments where the clip is less likely to suffer from corrosion or wear, reuse may be more acceptable, provided the clip remains in good condition.
4. Manufacturer’s Recommendations
- Check Manufacturer Guidelines: Always refer to the manufacturer’s guidelines regarding the reuse of wire rope clips. Some manufacturers may recommend against reuse, particularly for clips used in critical applications, while others may provide specific criteria for determining if a clip is still safe to use.
5. Load History
High-Load or Shock-Load Applications: If the wire rope clip has been used in high-load or shock-load applications, it should be replaced rather than reused. Such conditions can cause stress or fatigue in the clip, even if no visible damage is present.
Light or Moderate Loads: If the clip has only been used in light or moderate loads and passes a thorough inspection, it may be possible to reuse it.
6. Cost vs. Safety
- Safety Priority: In any situation where safety is a concern, it is generally better to err on the side of caution and replace the wire rope clips. The cost of replacing clips is often minimal compared to the potential risks associated with reusing a compromised clip.
Conclusion
- Critical/Safety Applications: Replace wire rope clips after each use.
- Non-Critical Applications: Clips may be reused if they pass a thorough inspection and show no signs of wear, damage, or corrosion.
- Environmental Exposure: Replace clips exposed to harsh conditions or corrosive environments after each use.
- Manufacturer’s Guidelines: Always follow the manufacturer’s recommendations for reuse.
- High-Load History: Replace clips used in high-load or shock-load situations.
In summary, while wire rope clips can sometimes be reused, it is crucial to carefully consider the specific circumstances and conduct a thorough inspection before deciding to reuse a clip. Prioritizing safety is always the best approach, especially in critical applications.
Chapt 7
What should I do if a wire rope clip fails during operation?
If a wire rope clip fails during operation, it is critical to take immediate action to ensure safety and prevent further damage or injury. Here are the steps you should follow:
1. Stop the Operation Immediately
- Cease All Activity: If you notice a wire rope clip has failed or if you suspect a failure (e.g., slippage of the wire rope, unusual sounds, or visible damage), stop the operation immediately. This is crucial to prevent any further damage or potential injuries.
- Secure the Area: Make sure the area is secure, especially if the wire rope is holding a load. Clear the area of any personnel to avoid the risk of injury.
2. Assess the Situation
- Check the Load: If the wire rope was supporting a load, assess the stability of the load. Ensure that it is not at risk of falling or causing additional hazards.
- Inspect the Wire Rope: Visually inspect the wire rope and the failed clip to determine the extent of the damage. Look for fraying, kinks, or other damage to the wire rope itself, as well as any deformation or breakage in the clip.
3. Report the Incident
- Notify Supervisors: Immediately report the incident to your supervisor or the person responsible for safety on-site. Provide details of what happened, including any visible damage and the condition of the wire rope and clip.
- Document the Failure: Take photos or make notes about the failure, including the position of the clip, the type of clip, and any environmental factors that might have contributed to the failure. This documentation can be useful for later analysis and improving safety protocols.
4. Remove the Load (if safe)
- Carefully Lower the Load: If it is safe to do so, carefully lower the load using an alternative method, such as another wire rope or lifting device. Avoid putting any additional stress on the compromised wire rope or clip.
- Do Not Reuse the Damaged Clip: Remove the failed clip and any other clips in the assembly, as they may also have been compromised. Replace them with new, properly rated clips.
5. Inspect the Entire Assembly
- Thorough Inspection: Conduct a thorough inspection of the entire wire rope assembly, including all clips, the wire rope itself, and any other hardware involved. Check for any additional signs of wear, damage, or potential failure.
- Replace Damaged Components: Replace any components that show signs of wear or damage. Do not reuse any parts that have been compromised.
6. Investigate the Cause of Failure
- Analyze the Incident: Investigate the cause of the wire rope clip failure. Consider factors such as improper installation (e.g., incorrect torque, wrong orientation), overloading, environmental factors (e.g., corrosion, extreme temperatures), or the use of incorrect or substandard equipment.
- Review Installation Practices: Ensure that wire rope clips were installed correctly according to manufacturer guidelines, with the saddle on the live end and the nuts tightened to the proper torque.
- Check Load Limits: Verify that the wire rope and clips were not overloaded beyond their rated capacity.
7. Implement Corrective Actions
- Training: If the failure was due to improper installation or usage, provide additional training to personnel on the correct procedures for installing and inspecting wire rope clips.
- Update Procedures: Review and update safety procedures, installation guidelines, and inspection protocols to prevent future failures.
- Upgrade Equipment: If the failure was due to substandard or inappropriate equipment, consider upgrading to higher-quality clips or using alternative securement methods.
8. Resume Operations Safely
- Final Inspection: Before resuming operations, perform a final inspection to ensure that all replacements have been installed correctly and that the assembly is safe to use.
- Gradual Resumption: Gradually resume operations, carefully monitoring the assembly for any signs of issues.
Conclusion
A wire rope clip failure during operation is a serious incident that requires immediate action. By stopping the operation, securing the area, assessing the situation, and conducting a thorough investigation, you can mitigate risks and prevent future failures. Always prioritize safety and ensure that all equipment is used within its rated capacity and installed correctly.
Get the catalogue
Leave a request and we will send you the catalogue with Aulone rigging hardware by e-mail
86-15573139663
86-15363044363