A non-rotating wire rope is a type of wire rope designed to prevent or minimize rotation when it is under load. This is achieved through a specialized construction that counters the tendency of the rope to twist or rotate, a common issue in standard wire ropes under tension.
Key Features:
Construction: Non-rotating wire ropes typically have a combination of multiple layers of strands wound in different directions. The construction often involves a combination of wires with opposing twist directions, such as a double layer (where one layer twists in one direction, and the other layer twists in the opposite direction) or a strand-on-strand design. This ensures that when the rope is loaded, the forces are balanced, and the rope doesn’t rotate.
This article will continue the discussion on non-rotating wire rope from the following aspects.
Outline
To determine if your wire rope is rotation-resistant, you need to look at several factors related to its construction and design. Rotation-resistant ropes are specifically engineered to minimize or prevent twisting under load, which is particularly important in applications like cranes, hoisting systems, and drilling rigs where rope stability is critical.
Here’s how you can confirm whether your wire rope is rotation-resistant:
1. Check the Rope Construction
Rotation-resistant wire ropes are designed with special features that prevent twisting when tensioned. The key features to look for in the construction include:
- Opposing Twist Directions:
Non-rotating or rotation-resistant ropes typically feature layers of strands twisted in opposing directions. This means that the strands or layers of wire inside the rope are arranged so that the forces applied to the rope cancel each other out, preventing rotation. Examples of such constructions include:- Strand-on-strand construction: One layer of strands twists in one direction, while the next layer twists in the opposite direction.
- Cross-lay construction: The strands are laid in an alternating pattern, crossing each other, which helps resist rotation.
2. Identify the Rope Type and Code
Many manufacturers use specific construction types and codes to identify rotation-resistant wire ropes. When looking at your wire rope, check if the rope is labeled or listed with a construction code. Here are some common rotation-resistant rope types:
- 35WXK7, 19XK7, or 35WXK19: These are specifically designed to be rotation-resistant.
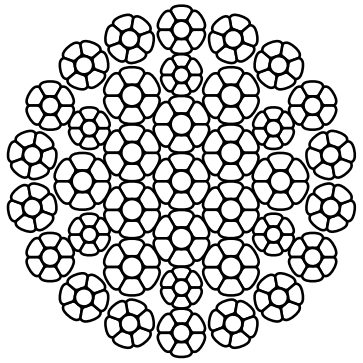
35WXK7
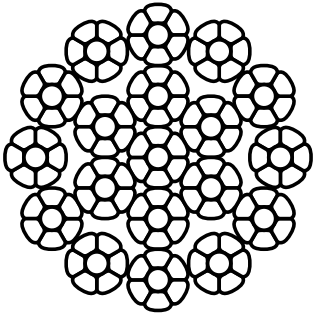
19XK7
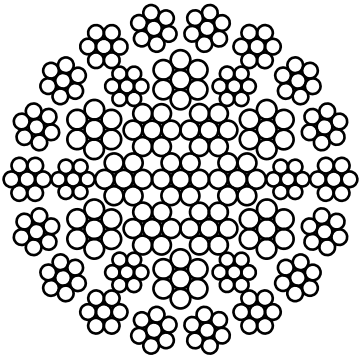
35WX7
3. Check Manufacturer Documentation
The manufacturer’s specifications are often the best way to confirm whether the rope is rotation-resistant. Look at the technical datasheet, product catalog, or user manual for the following terms:
- “Rotation-Resistant”
- “Non-Rotating”
- “Anti-Rotation”
If your rope is labeled with any of these terms, it is likely designed to prevent twisting.
4. Perform a Rotation Test
You can test the rope’s ability to resist rotation by performing a simple manual or dynamic test:
-
Lift a Load and Observe:
If the rope is rotation-resistant, it will not twist when a load is applied. When lifting, check to see if the rope twists or rotates around its axis. If it does, it is not rotation-resistant. -
Manual Rotation Test:
You can manually rotate the rope and apply tension to see how it behaves. For this test, rotate the rope under load (or simulate load by applying force to the rope) and see if it twists. A non-rotating rope should not rotate easily and should return to its original position after being manually rotated.
5. Rope Markings or Labels
Many reputable manufacturers will mark their rotation-resistant ropes with labels that clearly indicate their purpose. You might see markings such as:
- “Rotation-Resistant”
- “Non-Rotating”
- “Anti-Twist”
These markings are typically found on the rope itself, in the form of a printed label or engraved tag. If you see such markings, it’s a strong indication that the rope is designed to prevent twisting.
6. Consult with the Manufacturer
If you’re still unsure, the best course of action is to contact the manufacturer directly. Provide them with the rope’s specifications or part number, and they will be able to confirm whether the rope is designed to be rotation-resistant. Manufacturers often provide detailed explanations of rope construction and performance characteristics.
Summary of Steps to Identify a Rotation-Resistant Rope:
- Examine the Construction: Look for opposing twists in the strands, and check if the rope has a steel core (IWRC).
- Check the Rope Type and Code: Look for ropes with designations like 35WXK7, 35WXK19, which are specifically designed to be rotation-resistant.
- Review Manufacturer Documentation: Consult the rope’s technical data sheet or product catalog for terms like “Rotation-Resistant” or “Non-Rotating”.
- Perform a Rotation Test: Lift a load and check for twisting. Alternatively, apply manual rotation and see if the rope resists twisting under tension.
- Look for Markings: Check if the rope is labeled with terms such as “Rotation-Resistant” or “Anti-Twist”.
- Consult with the Manufacturer: If you’re still uncertain, contact the manufacturer for confirmation.
By following these steps, you can accurately determine whether your wire rope is rotation-resistant and ensure that it’s appropriate for your intended application. If you need more guidance or clarification, feel free to ask!
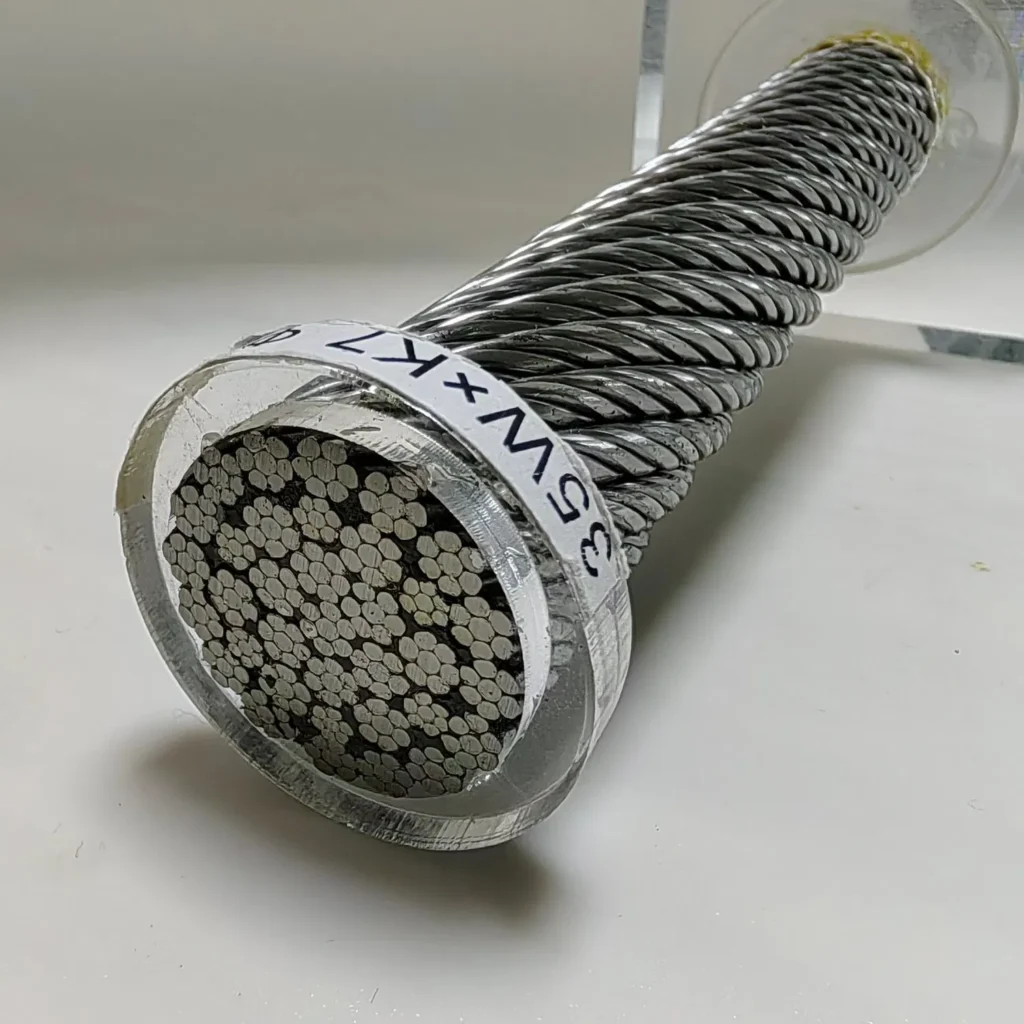
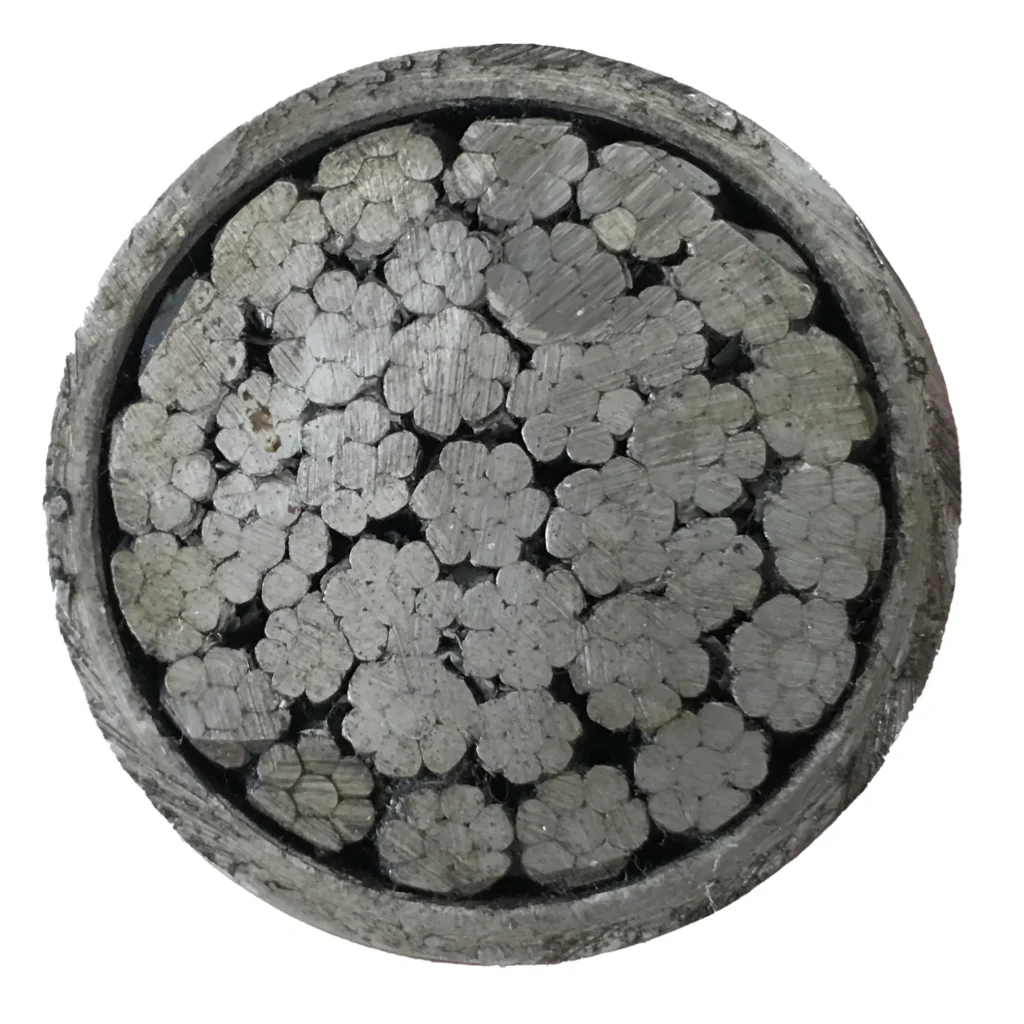
What is the difference between preformed and non-preformed wire rope?
The difference between preformed and non-preformed wire ropes lies primarily in their construction process and behavior under load. Both types are widely used in various industries, including construction, marine, and mining, but they have different mechanical properties, durability, and performance characteristics.
1. Preformed Wire Rope
Preformed wire rope refers to a rope in which the strands are formed into their helical shape before they are laid together to form the final rope. This means that the strands have already been given a specific twist and shape, which helps them maintain their shape and prevent deformation during use.
Key Characteristics of Preformed Wire Rope:
- Strands are pre-formed: The strands are twisted or formed into their final shape before being combined to form the rope. This gives the rope a more consistent structure.
- Better Stability: Preforming the strands ensures that they will not untwist or lose their shape during use. This makes the rope more stable under load, reducing the chance of kinks or deformations.
- Higher Fatigue Resistance: Because the strands maintain their shape, preformed wire ropes are generally more resistant to fatigue and wear, making them more durable over time.
- Less Stretching: Preformed wire ropes tend to exhibit less elongation and stretch compared to non-preformed ropes, leading to more predictable performance under load.
- Applications: These ropes are often used in cranes, elevators, hoisting systems, marine applications, and other heavy-duty operations where stability and durability are crucial.
Advantages of Preformed Wire Rope:
- Longer lifespan due to reduced strand distortion.
- Improved handling as the rope maintains its form and doesn’t untwist easily.
- Higher load-bearing capacity due to better strand structure integrity.
- Reduced maintenance as preformed ropes are less likely to develop wear patterns such as strand displacement.
2. Non-Preformed Wire Rope
Non-preformed wire rope is made from strands that are not preformed before being laid into the rope. The strands are twisted into the rope in their initial, unformed state and are then twisted into the rope’s final shape.
Key Characteristics of Non-Preformed Wire Rope:
- Strands are not pre-formed: In non-preformed ropes, the strands are laid out straight and twisted into the rope, meaning the strands retain a higher degree of flexibility when compared to preformed ropes.
- More Flexible: Non-preformed ropes are more flexible initially, which can make them easier to handle during installation or spooling. However, this flexibility can cause the strands to shift or deform under high load, especially if the rope is not maintained properly.
- More Susceptible to Deformation: Since the strands are not pre-formed, non-preformed ropes are more likely to experience strand distortion or deformation over time, which can reduce the rope’s lifespan.
- Higher Initial Stretch: Non-preformed wire ropes tend to stretch more initially than preformed ropes. This can lead to less precise control during lifting or hoisting tasks.
- Applications: These ropes are typically used in general-purpose lifting or situations where flexibility is needed, but they may not be suitable for highly demanding applications like cranes or winches.
Advantages of Non-Preformed Wire Rope:
- Initial Flexibility: Easier to install, handle, and spool due to increased flexibility.
- Lower cost: Non-preformed ropes can be cheaper to produce, making them a more cost-effective choice for some applications.
- Better for short-term, light-duty applications where the rope won’t experience heavy, continuous loads.
3. Comparison Between Preformed and Non-Preformed Wire Rope
Characteristic | Preformed Wire Rope | Non-Preformed Wire Rope |
---|---|---|
Strand Construction | Strands are pre-formed before being laid into the rope | Strands are twisted directly into the rope without pre-forming |
Shape Stability | Maintains its shape under load, less prone to deformation | Strands can shift or deform under load over time |
Flexibility | Less flexible, more stable under load | More flexible, easier to handle initially |
Load-bearing Capacity | Higher due to better strand integrity | Lower, as strands may deform under heavy loads |
Fatigue Resistance | Higher resistance to wear and fatigue | Lower resistance, more prone to wear and damage |
Elongation/Stretch | Less initial stretch, more predictable performance | More initial stretch, can be less predictable |
Applications | Heavy-duty applications (cranes, hoists, marine) | Light-duty or general-purpose lifting applications |
4. Which One to Choose?
The choice between preformed and non-preformed wire rope depends on the specific application and requirements:
- Choose Preformed Wire Rope when:
- You need higher durability and fatigue resistance.
- The rope will be used in high-load or critical applications (e.g., cranes, elevators, marine operations).
- You want to minimize maintenance and ensure stable performance under load.
- Choose Non-Preformed Wire Rope when:
- The application involves lower loads or temporary use.
- You need a more flexible rope that is easier to handle and install.
- Cost-effectiveness is a priority and the rope won’t be subjected to extreme wear or heavy loads.
Conclusion:
- Preformed wire ropes are ideal for heavy-duty, high-load applications due to their stability, resistance to deformation, and longer lifespan.
- Non-preformed wire ropes are more suitable for general-purpose, lighter applications where flexibility is more important than long-term durability.
By understanding these differences, you can select the right wire rope for your specific needs, ensuring safety, performance, and cost-efficiency.
How do you keep wire rope from twisting?
Keeping wire rope from twisting is essential in applications where rope stability and smooth operation are crucial, such as cranes, winches, hoisting systems, or even marine operations. Twisting can lead to damage, wear, and reduced lifespan of the rope, and may compromise safety. Here are several strategies to prevent wire rope from twisting:
1. Use Rotation-Resistant or Non-Rotating Wire Rope
The most effective way to prevent twisting is to use rotation-resistant or non-rotating wire rope. These ropes are specifically designed to counteract twisting forces.
- How it works: Rotation-resistant ropes have a special construction where the strands are twisted in opposite directions to cancel out the forces that would otherwise cause the rope to twist under load.
- Example: Common types include 35WXK7, 35WXK19, or ropes with IWRC (Independent Wire Rope Core), which are less prone to twisting.
Using a non-rotating rope is one of the most direct ways to prevent issues with rope twisting.
2. Install a Rotating Drum or Sheave System
Using a rotating drum or sheave system can help prevent twisting by guiding the rope in a controlled manner.
- How it works: A rotating drum or sheave evenly distributes the tension on the rope, ensuring that the rope is guided smoothly during movement. This helps to prevent kinks or unwanted rotation.
- Key features:
- Multiple grooves: Drums with multiple grooves allow the rope to remain in the correct position and prevents tangling or twisting.
- Proper alignment: Ensure the rope is correctly aligned with the drum or sheave to avoid twisting as it moves.
3. Use an Anti-Twist Device
In some systems, an anti-twist device or rotation limiter can be installed to reduce the likelihood of twisting.
- How it works: Anti-twist devices work by preventing the rope from rotating when tension is applied. These devices usually consist of a mechanism that locks the rope’s rotation in place, allowing it to move linearly but not twist.
- Examples:
- Rotation-reducing swivels or anti-twist pulleys are used in applications such as cranes or hoists.
- Swivel connectors can be used to allow the rope to move freely in one direction while preventing rotation in the other.
4. Proper Installation and Handling
Proper installation and handling of the wire rope during setup and operation can prevent twists from forming in the first place.
- Correct spool alignment: When spooling the wire rope onto a winch or reel, ensure that the rope is wound in the correct direction. Spooling in the opposite direction can lead to twisting as the rope is unwound during use.
- Proper pay-out method: When paying out the rope, ensure that it is done in a way that doesn’t induce twisting. If the rope is under tension, it is more likely to twist.
- Avoid overloading: Overloading the rope can lead to deformation and cause twisting or kinking. Always follow the manufacturer’s recommended load limits for the rope.
5. Use a Luffing Mechanism or Tensioning System
In some applications, particularly with cranes or hoists, a luffing mechanism or tensioning system can help prevent rope twisting.
- How it works: These systems adjust the angle or tension on the rope as it is lifted or lowered, ensuring that the rope does not twist or tangle as it moves. A properly tensioned rope is less likely to twist under load.
- Example: In crane systems, the use of a tensioning device on the load line helps to reduce the chance of rotation by keeping the rope aligned and taut.
6. Routine Maintenance and Inspection
Regular maintenance and inspection can help identify and prevent rope twisting before it becomes an issue.
- Inspect for damage: Regularly check the rope for signs of wear, such as broken wires, flattened strands, or corrosion, which could contribute to twisting or reduced strength.
- Lubrication: Some types of wire rope, especially those used in harsh environments, benefit from regular lubrication to reduce friction between the strands, which can prevent premature wear and twisting.
7. Avoid Sharp Bends or Angles
Sharp bends or angles in the rope can induce stress and twisting, especially when the rope is in motion. Ensure that the rope is not subjected to tight bends, which can create friction and increase the likelihood of twisting.
- Use proper sheaves and pulleys: Make sure that pulleys and sheaves are designed with a sufficient radius to prevent the rope from bending too sharply. This reduces the risk of rope deformation and twisting.
8. Use a Multi-Layer Rope System (in Specific Applications)
For winching or lifting operations, using a multi-layer rope system can prevent twisting. By managing the layers of the rope, the forces are distributed more evenly, which helps to avoid twisting.
- How it works: This method involves using a rope that is laid across multiple layers on the drum or reel, allowing the load to be shared evenly across the rope without excessive strain on any one layer.
Summary of Methods to Prevent Wire Rope Twisting:
Method | Description |
---|---|
Rotation-Resistant Wire Rope | Use ropes designed with opposing twists in strands (e.g., 35WXK7, 35WXK19) or with an IWRC core to prevent twisting under load. |
Rotating Drum/Sheave System | Use rotating drums or sheaves to guide the rope and distribute tension evenly, reducing twisting. |
Anti-Twist Devices | Install swivels or anti-twist pulleys to limit rope rotation and keep it aligned. |
Proper Installation and Handling | Ensure correct spooling, correct pay-out method, and avoid overloading the rope. |
Luffing Mechanism/Tensioning System | Use systems that adjust tension or angle to prevent twisting, particularly in hoists or cranes. |
Routine Maintenance | Regularly inspect for damage and lubricate the rope to reduce friction and wear, which can lead to twisting. |
Avoid Sharp Bends or Angles | Ensure the rope passes through pulleys and sheaves with a sufficient radius to avoid sharp bends, which can lead to twisting. |
Multi-Layer Rope System | Use a system that distributes load evenly across multiple layers, especially in winching or lifting operations. |
By incorporating these methods into your wire rope usage and maintenance practices, you can significantly reduce the risk of twisting and increase the lifespan and efficiency of your rope in demanding applications.